How to Manufacture Aluminum Art Parts
Aluminum has become a prominent material in the field of art manufacturing due to its favorable properties such as lightweight, corrosion resistance, and malleability. The process of creating aluminum art parts involves various techniques and methods, from initial design concepts to the final production stages. This article aims to provide an in-depth exploration of the manufacturing process for aluminum art parts, covering design considerations, materials, techniques, and finishing options.
1. Understanding Aluminum as a Material
1.1 Properties of Aluminum
Aluminum is a versatile metal with several beneficial properties that make it suitable for artistic applications. Key properties include:
- Lightweight: Aluminum is significantly lighter than other metals, making it easier to handle and manipulate.
- Corrosion Resistance: Due to its natural oxide layer, aluminum resists corrosion, enhancing the durability of art pieces.
- Malleability and Ductility: These properties allow for complex shapes and designs, facilitating creativity in art manufacturing.
- Thermal and Electrical Conductivity: While not always critical in art, these properties can enhance certain artistic applications, such as light installations.
1.2 Types of Aluminum Alloys
Different aluminum alloys possess unique characteristics that can influence the manufacturing process. Common alloys used in art manufacturing include:
- Aluminum 6061: Known for its good mechanical properties and weldability, this alloy is frequently used in structural applications.
- Aluminum 5052: Recognized for its excellent corrosion resistance and formability, this alloy is suitable for artistic applications requiring intricate shapes.
- Aluminum 7075: Although heavier than other alloys, it offers exceptional strength, making it suitable for large sculptures.
2. Design Considerations
2.1 Concept Development
The design phase is crucial in the manufacturing process of aluminum art parts. Artists must consider various factors, including the intended message, audience, and functionality of the artwork.
- Sketching and Prototyping: Initial sketches can help visualize the concept. Prototyping may involve creating small-scale models to test design ideas before full-scale production.
- Computer-Aided Design (CAD): Modern artists often use CAD software to create precise digital models, allowing for intricate designs and modifications.
2.2 Technical Specifications
Understanding the technical specifications is vital to ensure the successful manufacturing of art parts. Key specifications include:
- Dimensions: Accurate measurements are essential for the fit and functionality of the art piece.
- Weight Considerations: Lightweight designs can enhance the feasibility of installation and transportation.
- Joint and Connection Types: Artists should determine how different parts will be connected, whether through welding, rivets, or adhesive bonding.
3. Manufacturing Techniques
3.1 Cutting Techniques
The first step in manufacturing aluminum art parts often involves cutting the material to the desired shape and size. Common cutting methods include:
- Laser Cutting: This technique offers high precision and the ability to cut complex shapes. It uses a focused laser beam to melt or vaporize the material.
- Water Jet Cutting: Utilizing high-pressure water mixed with abrasives, this method can cut thick aluminum plates without introducing heat-affected zones.
- CNC Milling: Computer Numerical Control (CNC) milling machines can create intricate designs by removing material from a solid block of aluminum.
3.2 Forming Techniques
Once the aluminum has been cut, forming techniques shape the material into the desired form. Common forming methods include:
- Bending: This technique involves deforming the aluminum along a straight axis, allowing for the creation of angles and curves.
- Spinning: Metal spinning is a process where a flat disc of aluminum is rotated at high speeds and formed into a shape using tools.
- Hydroforming: This process uses high-pressure fluids to shape aluminum into complex forms, often resulting in seamless structures.
3.3 Joining Techniques
Joining techniques are essential for assembling multiple components into a single art piece. Methods include:
- Welding: Various welding techniques, such as TIG (Tungsten Inert Gas) and MIG (Metal Inert Gas), can be used to join aluminum parts.
- Riveting: This mechanical fastening method involves inserting a metal pin through pre-drilled holes and securing it to create a strong connection.
- Adhesive Bonding: Specialized adhesives designed for metal bonding can create strong, permanent connections without altering the aluminum’s surface.
4. Surface Finishing
Surface finishing plays a crucial role in enhancing the aesthetic appeal and durability of aluminum art parts. Common finishing techniques include:
4.1 Anodizing
Anodizing is an electrochemical process that thickens the natural oxide layer on aluminum, providing enhanced corrosion resistance and the ability to dye the surface for color effects. This method can produce various textures and colors, making it popular in artistic applications.
4.2 Powder Coating
Powder coating involves applying a dry powder to the surface of the aluminum, which is then cured under heat to form a durable finish. This method allows for a wide range of colors and finishes while providing excellent protection against wear and corrosion.
4.3 Painting and Plating
Artists may choose traditional painting techniques or metal plating to achieve specific visual effects. Painting allows for creativity and customization, while plating can provide a luxurious finish.
5. Quality Control
Quality control is an essential aspect of the manufacturing process to ensure that the final art pieces meet the required specifications and standards. Methods of quality control include:
- Dimensional Inspection: Measuring the final product against the original design to ensure accuracy.
- Visual Inspection: Checking for surface defects, such as scratches or inconsistencies in finish.
- Functional Testing: Ensuring that the artwork functions as intended, especially for kinetic or interactive pieces.
6. Installation and Maintenance
Once manufactured, the installation of aluminum art parts must be carefully planned to ensure the longevity and stability of the artwork. Considerations include:
6.1 Site Assessment
Artists should assess the installation site for factors such as environmental conditions, accessibility, and potential interactions with the public.
6.2 Mounting Techniques
The choice of mounting techniques depends on the weight and design of the artwork. Common methods include:
- Bolted Connections: Securing art pieces with bolts to ensure stability.
- Welded Frames: Creating a supportive frame that the artwork can be welded or attached to.
- Suspended Systems: For hanging pieces, artists may use cables or rods to create an illusion of floating.
6.3 Maintenance Practices
Regular maintenance ensures the longevity of aluminum art pieces. Maintenance practices may include:
- Cleaning: Periodic cleaning to remove dirt and debris, especially for outdoor installations.
- Inspection: Routine checks for structural integrity and any signs of wear or damage.
- Refinishing: Applying new finishes or protective coatings as needed.
7. Case Studies and Applications
7.1 Architectural Art
Aluminum is often used in architectural art installations due to its lightweight properties and versatility. Examples include large-scale sculptures integrated into building designs or public art installations in urban spaces.
7.2 Kinetic Art
Artists creating kinetic art can leverage aluminum's lightweight nature to design moving sculptures. The material’s strength allows for intricate mechanisms that enhance the artwork's visual appeal.
7.3 Functional Art
Aluminum art can also serve functional purposes, such as furniture or lighting designs, combining aesthetics with usability. Artists must balance form and function in these applications.
Conclusion
Manufacturing aluminum art parts is a multifaceted process that requires careful consideration of materials, design, and techniques. By understanding the properties of aluminum and employing various manufacturing methods, artists can create innovative and durable art pieces. As the field of art manufacturing continues to evolve, advancements in technology and materials will further enhance the possibilities for artistic expression in aluminum.
3, 4 and 5-axis precision CNC machining services for aluminum machining, beryllium, carbon steel, magnesium, titanium machining, Inconel, platinum, superalloy, acetal, polycarbonate, fiberglass, graphite and wood. Capable of machining parts up to 98 in. turning dia. and +/-0.001 in. straightness tolerance. Processes include milling, turning, drilling, boring, threading, tapping, forming, knurling, counterboring, countersinking, reaming and laser cutting. Secondary services such as assembly, centerless grinding, heat treating, plating and welding. Prototype and low to high volume production offered with maximum 50,000 units. Suitable for fluid power, pneumatics, hydraulics and valve applications. Serves the aerospace, aircraft, military, medical and defense industries.PTJ will strategize with you to provide the most cost-effective services to help you reach your target,Welcome to Contact us ( sales@pintejin.com ) directly for your new project.
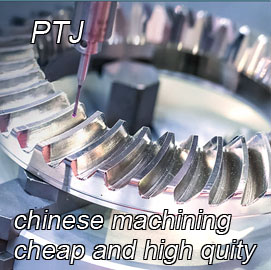
- 5 Axis Machining
- Cnc Milling
- Cnc Turning
- Machining Industries
- Machining Process
- Surface Treatment
- Metal Machining
- Plastic Machining
- Powder Metallurgy Mold
- Die Casting
- Parts Gallery
- Auto Metal Parts
- Machinery Parts
- LED Heatsink
- Building Parts
- Mobile Parts
- Medical Parts
- Electronic Parts
- Tailored Machining
- Bicycle Parts
- Aluminum Machining
- Titanium Machining
- Stainless Steel Machining
- Copper Machining
- Brass Machining
- Super Alloy Machining
- Peek Machining
- UHMW Machining
- Unilate Machining
- PA6 Machining
- PPS Machining
- Teflon Machining
- Inconel Machining
- Tool Steel Machining
- More Material