How Cnc Machining Impacts Manufacturing
Computer Numerical Control (CNC) machining represents a significant advancement in the field of manufacturing, enabling enhanced precision, efficiency, and versatility in the production of complex components. This technology utilizes computer systems to control machine tools, which allows for the automation of manufacturing processes. As industries increasingly adopt CNC machining, its impact on manufacturing is profound, influencing everything from design to production, quality control, and overall productivity.
Definition and Overview of CNC Machining
CNC machining refers to the process of using computer-controlled machines to perform various manufacturing tasks, including drilling, milling, turning, and grinding. Unlike traditional manual machining, where operators directly control the tools, CNC machines follow pre-programmed instructions to execute precise movements. This is achieved through a combination of hardware and software, where the design of a component is converted into a series of commands that dictate the movements of the machining tools.
Historical Context
The origins of CNC machining can be traced back to the 1940s and 1950s when numerical control (NC) systems were developed to automate the machining process. The introduction of computers in the 1960s revolutionized this technology, leading to the emergence of CNC machines that could execute more complex tasks with higher accuracy. Over the decades, CNC machining has evolved alongside advancements in computer technology and materials science, becoming an integral part of modern manufacturing practices.
Enhanced Precision and Accuracy
One of the most significant impacts of CNC machining on manufacturing is its ability to produce components with exceptional precision and accuracy. Traditional machining methods are often subject to human error, whereas CNC machines are governed by algorithms that ensure consistent results. This level of precision is crucial in industries such as aerospace, automotive, and medical device manufacturing, where even minute deviations can result in catastrophic failures.
CNC machining systems can achieve tolerances as tight as ±0.001 inches, allowing for the production of intricate parts that meet stringent industry standards. This precision reduces the need for extensive post-processing and inspection, thereby streamlining the production process and minimizing costs.
Increased Efficiency and Productivity
CNC machining significantly enhances manufacturing efficiency by automating repetitive tasks that would otherwise require manual intervention. CNC machines can operate continuously, running multiple shifts with minimal downtime. This capability enables manufacturers to produce large volumes of parts in a shorter timeframe, thus increasing overall productivity.
Additionally, CNC machining allows for the rapid prototyping of components. Manufacturers can quickly create and test prototypes, facilitating faster design iterations and reducing the time to market for new products. The ability to switch between different production runs with relative ease also contributes to greater operational flexibility, allowing manufacturers to respond swiftly to changing market demands.
Versatility in Manufacturing
CNC machining is versatile and can be applied to a wide range of materials, including metals, plastics, wood, and composites. This adaptability makes it suitable for various industries, from aerospace and automotive to electronics and consumer goods. CNC machines can execute multiple processes, such as milling, turning, and laser cutting, on a single platform, reducing the need for multiple specialized machines.
The capability to work with diverse materials enables manufacturers to innovate and create complex geometries that may not be achievable through traditional methods. This versatility also extends to custom manufacturing, where CNC machining can produce one-off parts tailored to specific customer requirements.
Quality Control and Consistency
Quality control is a critical aspect of manufacturing, and CNC machining enhances this process by ensuring consistent quality across production runs. The use of computer software allows for precise monitoring and adjustment of machining parameters, resulting in uniformity in finished products. Additionally, CNC machines often incorporate advanced sensors and feedback systems that provide real-time data on machining performance, facilitating immediate corrections if deviations from desired specifications occur.
The consistency achieved through CNC machining contributes to reducing scrap rates and rework, further improving the efficiency and cost-effectiveness of manufacturing operations. As a result, manufacturers can maintain higher levels of quality assurance, leading to increased customer satisfaction and brand loyalty.
Challenges and Limitations
Despite its numerous advantages, CNC machining is not without challenges. The initial investment in CNC machinery and software can be substantial, making it a significant barrier for small and medium-sized enterprises (SMEs). Furthermore, the complexity of CNC systems requires skilled operators and programmers, necessitating ongoing training and development to maintain proficiency in the technology.
Another limitation is the potential for over-reliance on automation, which may lead to reduced manual skills among operators. While CNC machines excel at executing programmed tasks, they may not always adapt well to unforeseen issues that arise during the manufacturing process. Therefore, a balanced approach that combines automation with human expertise is essential for optimal outcomes.
Conclusion
CNC machining has profoundly transformed the landscape of manufacturing, offering unparalleled precision, efficiency, and versatility. As industries continue to evolve and adopt advanced manufacturing technologies, the importance of CNC machining will only grow. Its ability to produce high-quality components at scale positions it as a cornerstone of modern manufacturing practices. While challenges remain, the benefits of CNC machining far outweigh its limitations, making it a vital tool in the pursuit of innovation and excellence in manufacturing. As technology advances further, CNC machining will likely continue to drive improvements in productivity, quality, and efficiency, shaping the future of manufacturing across various sectors.
Reprint Statement: If there are no special instructions, all articles on this site are original. Please indicate the source for reprinting:https://www.cncmachiningptj.com/,thanks!
PTJ® provides a full range of Custom Precision cnc machining china services.ISO 9001:2015 &AS-9100 certified. 3, 4 and 5-axis rapid precision CNC machining services including milling, turning to customer specifications,Capable of metal & plastic machined parts with +/-0.005 mm tolerance.Secondary services include CNC and conventional grinding, drilling,die casting,sheet metal and stamping.Providing prototypes, full production runs, technical support and full inspection.Serves the automotive, aerospace, mold&fixture,led lighting,medical,bicycle, and consumer electronics industries. On-time delivery.Tell us a little about your project's budget and expected delivery time. We will strategize with you to provide the most cost-effective services to help you reach your target,Welcome to Contact us ( sales@pintejin.com ) directly for your new project.
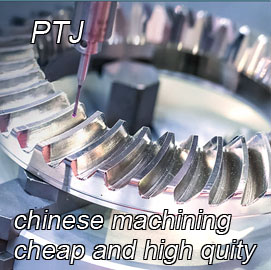
- 5 Axis Machining
- Cnc Milling
- Cnc Turning
- Machining Industries
- Machining Process
- Surface Treatment
- Metal Machining
- Plastic Machining
- Powder Metallurgy Mold
- Die Casting
- Parts Gallery
- Auto Metal Parts
- Machinery Parts
- LED Heatsink
- Building Parts
- Mobile Parts
- Medical Parts
- Electronic Parts
- Tailored Machining
- Bicycle Parts
- Aluminum Machining
- Titanium Machining
- Stainless Steel Machining
- Copper Machining
- Brass Machining
- Super Alloy Machining
- Peek Machining
- UHMW Machining
- Unilate Machining
- PA6 Machining
- PPS Machining
- Teflon Machining
- Inconel Machining
- Tool Steel Machining
- More Material