What is Batch Manufacturing Record
A Batch Manufacturing Record (BMR) is a critical document used in the pharmaceutical, biotechnology, and food manufacturing industries. It serves as a comprehensive record of the manufacturing process for a specific batch of product, ensuring compliance with regulatory standards and facilitating traceability and quality assurance. The BMR is essential for maintaining consistent product quality, adhering to Good Manufacturing Practices (GMP), and providing detailed documentation for inspection by regulatory authorities.
Definition and Purpose
The BMR is a detailed document that outlines the entire manufacturing process for a batch of a product, including the quantities of raw materials used, the equipment employed, the steps of the production process, and the environmental conditions under which the product was manufactured. Its primary purposes include:
-
Quality Control: The BMR provides a framework for quality assurance, ensuring that every step of the manufacturing process is performed according to established protocols. This helps to minimize variations in product quality.
-
Regulatory Compliance: Regulatory bodies such as the Food and Drug Administration (FDA) and the European Medicines Agency (EMA) require detailed documentation of manufacturing processes. The BMR serves as a legal record that demonstrates compliance with applicable regulations.
-
Traceability: In the event of a product recall or quality issue, the BMR enables manufacturers to trace back through the manufacturing process to identify any potential sources of contamination or error.
-
Training and Reference: The BMR serves as a reference document for training new employees and for ongoing training of existing staff. It provides standardized procedures that can be followed to ensure consistency.
Components of a Batch Manufacturing Record
A typical BMR will include the following components:
-
Product Information: This section includes the name, description, and identification number of the product being manufactured.
-
Batch Information: Details such as the batch number, production date, expiration date, and the quantity produced are recorded here.
-
Raw Materials: A comprehensive list of all raw materials used in the production of the batch, including specifications, lot numbers, and quantities.
-
Equipment: The BMR lists all equipment used during the manufacturing process, including identification numbers and maintenance records.
-
Manufacturing Process: A step-by-step description of the manufacturing process, including any specific procedures, parameters, and controls. This section may include information on mixing, heating, cooling, and other processing steps.
-
Environmental Conditions: Details about the manufacturing environment, such as temperature, humidity, and cleanliness levels, which are crucial for certain products.
-
Quality Control Tests: Information on any quality control tests performed during or after the manufacturing process, along with the results.
-
Signatures: The BMR should be signed by relevant personnel, including the operators, quality control inspectors, and supervisors, to verify that the batch was produced according to the documented procedures.
Importance in Different Industries
The BMR is particularly important in industries where product safety and efficacy are critical. In the pharmaceutical industry, for example, the BMR ensures that drugs are manufactured under strict quality controls, reducing the risk of contamination and ensuring that products meet regulatory standards. In the food industry, a BMR helps to ensure that food products are safe for consumption, following best practices for hygiene and quality.
Challenges and Best Practices
Implementing an effective BMR system can pose challenges, including the need for thorough training of personnel, the complexity of manufacturing processes, and the evolving nature of regulatory requirements. Best practices for developing and maintaining a BMR include:
- Standardization: Develop standardized templates for BMRs that can be adapted for different products while ensuring consistency across documentation.
- Automation: Utilize electronic batch record systems to streamline data collection and enhance accuracy, while also facilitating real-time monitoring and reporting.
- Regular Review: Establish a process for regular review and updating of BMRs to ensure they remain current with changes in manufacturing processes, regulations, and industry standards.
- Training: Provide ongoing training for personnel involved in the manufacturing process to ensure that they understand the importance of the BMR and how to complete it accurately.
Conclusion
The Batch Manufacturing Record is an indispensable tool in ensuring the safety, quality, and compliance of products in the pharmaceutical, biotechnology, and food manufacturing industries. By documenting every aspect of the manufacturing process, the BMR not only serves regulatory requirements but also supports continuous improvement and operational excellence within manufacturing organizations. As industries continue to evolve, the role of the BMR will remain critical in fostering trust between manufacturers and consumers, safeguarding public health, and ensuring product integrity.
Reprint Statement: If there are no special instructions, all articles on this site are original. Please indicate the source for reprinting:https://www.cncmachiningptj.com/,thanks!
PTJ® provides a full range of Custom Precision cnc machining china services.ISO 9001:2015 &AS-9100 certified. 3, 4 and 5-axis rapid precision CNC machining services including milling, turning to customer specifications,Capable of metal & plastic machined parts with +/-0.005 mm tolerance.Secondary services include CNC and conventional grinding, drilling,die casting,sheet metal and stamping.Providing prototypes, full production runs, technical support and full inspection.Serves the automotive, aerospace, mold&fixture,led lighting,medical,bicycle, and consumer electronics industries. On-time delivery.Tell us a little about your project's budget and expected delivery time. We will strategize with you to provide the most cost-effective services to help you reach your target,Welcome to Contact us ( sales@pintejin.com ) directly for your new project.
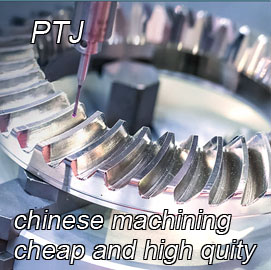
- 5 Axis Machining
- Cnc Milling
- Cnc Turning
- Machining Industries
- Machining Process
- Surface Treatment
- Metal Machining
- Plastic Machining
- Powder Metallurgy Mold
- Die Casting
- Parts Gallery
- Auto Metal Parts
- Machinery Parts
- LED Heatsink
- Building Parts
- Mobile Parts
- Medical Parts
- Electronic Parts
- Tailored Machining
- Bicycle Parts
- Aluminum Machining
- Titanium Machining
- Stainless Steel Machining
- Copper Machining
- Brass Machining
- Super Alloy Machining
- Peek Machining
- UHMW Machining
- Unilate Machining
- PA6 Machining
- PPS Machining
- Teflon Machining
- Inconel Machining
- Tool Steel Machining
- More Material