Electroplating vs. Electroforming
Electroplating and electroforming are both electrochemical processes used to deposit metal onto a substrate. While they share some similarities, including the underlying principle of electrodeposition, their applications, techniques, and outcomes differ significantly. This article explores the definitions, processes, applications, advantages, and disadvantages of electroplating and electroforming, providing a comprehensive overview of these two important manufacturing techniques.
Definitions
Electroplating is the process of depositing a layer of metal onto a surface by passing an electric current through a solution containing metal ions. This technique is widely used for various purposes, including corrosion protection, aesthetic enhancement, and wear resistance.
Electroforming, on the other hand, is the process of creating a metal object by depositing metal onto a conductive substrate or mandrel, which is later removed to leave behind a hollow or solid metal part. Electroforming is often employed in applications requiring precise dimensions and intricate details, such as in the manufacturing of molds, medical devices, and electronic components.
Process
Electroplating
The electroplating process involves several key steps:
-
Preparation of the Substrate: The surface of the object to be electroplated is cleaned to remove any contaminants that could hinder adhesion. This can involve mechanical cleaning, chemical cleaning, or a combination of both.
-
Electrolyte Solution: The substrate is immersed in an electrolyte solution containing metal salts (e.g., gold, silver, nickel) and additives that enhance the plating process.
-
Electrodeposition: An electric current is applied, causing metal ions from the electrolyte to migrate towards the cathode (the substrate), where they are reduced and deposited as a solid layer.
-
Post-Treatment: After plating, the object may undergo additional processes such as rinsing, drying, and polishing to achieve the desired finish.
Electroforming
Electroforming involves a more complex series of steps:
-
Mandrel Creation: A mandrel, which can be made from various materials (often non-conductive), is created in the desired shape of the final product. The mandrel must be designed with precision to ensure the electroformed part meets required specifications.
-
Conductive Coating: The mandrel is coated with a conductive layer, typically using techniques such as sputtering or painting with conductive paint, to allow for the deposition of metal during the electroforming process.
-
Electrolyte Bath: Similar to electroplating, the mandrel is immersed in an electrolyte solution containing metal ions.
-
Electrodeposition: An electric current is passed through the solution, depositing metal onto the mandrel. This process continues until the desired thickness of the metal layer is achieved.
-
Mandrel Removal: After the desired thickness is reached, the mandrel is carefully removed, leaving behind a hollow or solid metal part.
Applications
Electroplating Applications
Electroplating is used in a variety of industries, including:
- Jewelry: Enhancing the appearance of jewelry by applying precious metals for aesthetic purposes.
- Automotive: Providing corrosion resistance to components such as bumpers, trim, and connectors.
- Electronics: Creating conductive pathways and improving solderability on circuit boards.
- Industrial Equipment: Protecting tools and machinery from wear and corrosion.
Electroforming Applications
Electroforming is utilized in specialized applications, including:
- Molds and Dies: Producing highly accurate molds for casting and injection molding processes.
- Medical Devices: Manufacturing intricate components for medical instruments and implants.
- Art and Sculpture: Creating detailed sculptures and artistic objects with fine features.
- Electronic Components: Fabricating precise parts for connectors, antennas, and other electronic devices.
Advantages and Disadvantages
Advantages of Electroplating
- Cost-Effectiveness: Generally, electroplating is less expensive than electroforming due to the lower material costs and shorter production times.
- Versatility: Electroplating can be applied to a wide range of substrates and is suitable for various metal types.
- Improved Surface Properties: Enhances surface characteristics such as corrosion resistance, conductivity, and aesthetic appeal.
Disadvantages of Electroplating
- Thickness Limitations: The layers deposited are typically thinner compared to electroformed parts, which may not be suitable for all applications.
- Adhesion Issues: If the substrate surface is not adequately prepared, poor adhesion of the plating layer can occur, leading to flaking or peeling.
Advantages of Electroforming
- Precision and Detail: Electroforming allows for the production of highly intricate and detailed parts that may be difficult to achieve through traditional machining.
- Thickness Control: The thickness of the deposited metal layer can be precisely controlled, allowing for the creation of parts with specific dimensional requirements.
Disadvantages of Electroforming
- Higher Costs: The process can be more expensive than electroplating due to the need for a mandrel and longer production times.
- Complexity: The setup and process are generally more complex, requiring specialized knowledge and equipment.
Conclusion
In summary, electroplating and electroforming are both valuable electrochemical techniques used for metal deposition, each with its own unique advantages and applications. While electroplating is commonly used for enhancing the surface properties of various objects, electroforming is favored for its ability to create precise and intricate metal components. Understanding the differences between these two processes is essential for selecting the appropriate technique for specific manufacturing needs, ensuring optimal performance and cost-effectiveness in the production of metal parts.
Reprint Statement: If there are no special instructions, all articles on this site are original. Please indicate the source for reprinting:https://www.cncmachiningptj.com/,thanks!
PTJ® provides a full range of Custom Precision cnc machining china services.ISO 9001:2015 &AS-9100 certified. 3, 4 and 5-axis rapid precision CNC machining services including milling, turning to customer specifications,Capable of metal & plastic machined parts with +/-0.005 mm tolerance.Secondary services include CNC and conventional grinding, drilling,die casting,sheet metal and stamping.Providing prototypes, full production runs, technical support and full inspection.Serves the automotive, aerospace, mold&fixture,led lighting,medical,bicycle, and consumer electronics industries. On-time delivery.Tell us a little about your project's budget and expected delivery time. We will strategize with you to provide the most cost-effective services to help you reach your target,Welcome to Contact us ( sales@pintejin.com ) directly for your new project.
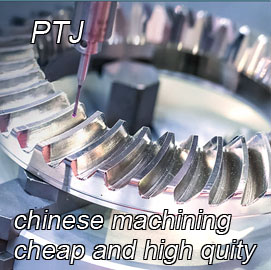
- 5 Axis Machining
- Cnc Milling
- Cnc Turning
- Machining Industries
- Machining Process
- Surface Treatment
- Metal Machining
- Plastic Machining
- Powder Metallurgy Mold
- Die Casting
- Parts Gallery
- Auto Metal Parts
- Machinery Parts
- LED Heatsink
- Building Parts
- Mobile Parts
- Medical Parts
- Electronic Parts
- Tailored Machining
- Bicycle Parts
- Aluminum Machining
- Titanium Machining
- Stainless Steel Machining
- Copper Machining
- Brass Machining
- Super Alloy Machining
- Peek Machining
- UHMW Machining
- Unilate Machining
- PA6 Machining
- PPS Machining
- Teflon Machining
- Inconel Machining
- Tool Steel Machining
- More Material