Ways To Improve The Accuracy Of Shaft Gear Hobbing
Ways To Improve The Accuracy Of Shaft Gear Hobbing
Through the analysis of the machining accuracy of the shaft gear hobbing, the factors affecting the machining accuracy of the hobbing are found out, so as to improve the quality of the hobbing processing. A heavy-duty automobile gearbox professional production plant, the shaft gear is the most important machine in the gearbox, and the unevenness of the machining accuracy indirectly affects the overall quality of the gearbox. At present, the machining method of the machining gear teeth used by the factory is the hobbing and shaving method. To create high-precision gears by rolling and shaving, it is necessary to show the best level of rolling and shaving. |
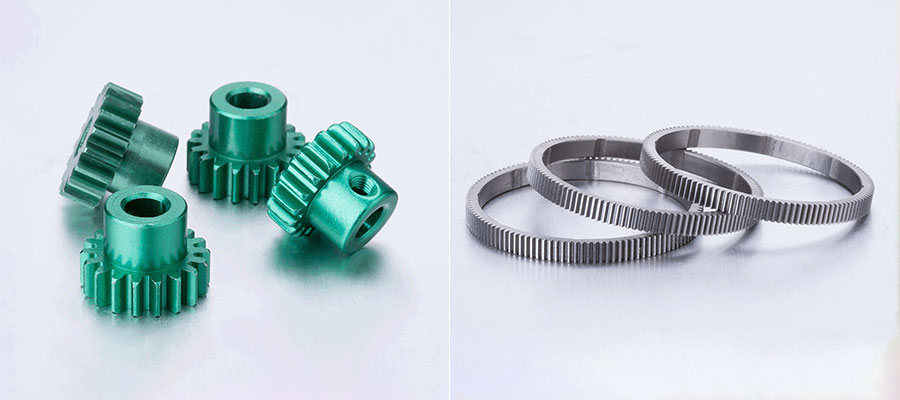
The shaving accuracy is very fluent on the saddle hobbing accuracy, so some deviations in the hobbing must be strictly controlled to create a high quality gear. Hobbing is a commonly used gear machining method. On the hobbing machine with high precision, a fine hob is used to machine the gear teeth with 4-5 precision. On the popular level hobbing machine, with the precision precision hob, only 8 precision teeth can be machined. The accuracy of the gear shaft gear toothing is 8-7-7, and if the gear machining method uses the two core holes and the end face as the positioning reference, the deviation of the hobbing is explained, and the machining accuracy is improved. The way is very important.
1 hobbing machining accuracy analysis
The accuracy of the shaft teeth is related to the motion accuracy, the stability accuracy, and the contact accuracy. The hobbing machining top uses the length of the common normal line and the ring diameter to jump to the movement precision, and uses the control of the tooth profile deviation and the base section error to achieve the stability of the event, and the contact accuracy is controlled by the deviation of the tooth. Under the face of several deviations in the hobbing process, the reasons for the deviation are explained:
1.1 ring gear radial runout deviation (ie geometric pain)
The ring gear radial runout is that the axe is in the range of the gear one turn, the probe is in the tooth groove or on the gear teeth, and the double-sided contact with the middle of the tooth height, the maximum change amount of the probe relative to the axis of the tooth. It is also the partial pain of the gear tooth ring relative to the core line of the shaft.
This kind of pain is caused by the fact that the two core holes of the whole machine are not coincident with the core device of the reverse rotation of the table or the error is too large. Or because the top and top holes are badly formed, the contact surface is not well contacted to form a partial pain, so the ring diameter jump should be handled from the above edge.
1.2 Common normal length deviation (ie active pain)
Hobbing is the processing of gears by means of the exhibition method. The gear transmission chain from the tool to the tooth blank is connected to the accuracy of the movement according to the inevitable transmission ratio. However, these transmission chains are composed of a series of relay elements.
Their construction and disassembly deviations must be concentrated in the transmission process to the end of the transmission chain, the relative activity of the unacceptable, affecting the machining accuracy of the teeth. The change of the length of the common normal line is the maximum deviation of the reaction gear teeth. If this is the second time, if the hobbing machine is not convinced, the hobbing machine will be formed by the circular guide rail wear, the indexing worm wheel and the table.
The circular guide rail is formed by the bifurcated shaft. In addition, when the tooth surface of the split tooth suspension has a severe bump or a hanging wheel, the bite is too loose or too tight, which may affect the change of the common normal line.
1.3 Tooth shape deviation analysis
The tooth profile deviation is the normal distance between the two cubbly (involute) profiles of the axe in the tooth-shaped department, including the actual tooth profile. In the actual processing process, it is impossible to obtain a completely accurate involute tooth shape, and always has various types of deviations, thereby affecting the stability of the transmission. The base circle of the gear is a specific parameter that determines the involute tooth shape. If the base circle is deviated during the hobbing process, the tooth condition will also be biased.
The base circle radius R=the knife movement rate/the table reversal rotation angle rate xcosao (ao is the original tooth angle of the hob), the involute tooth shape in the hobbing process is secondary to the hob and the tooth blank By connecting the teeth of the inevitable speed ratio, it can be seen that if the tooth profile deviation is determined by the hob tooth profile deviation, the hob sharpening quality is not good and the tooth profile deviation is easy to appear.
At the same time, the radial runout and axial turbulence (ie, device deviation) that occurs in the hob in the device also have an effect on the tooth profile deviation. Common tooth shape deviations are not wrong, the tooth angle deviation (the tip is fattened or thickened), and the cycle deviation occurs.
Through the analysis of the machining accuracy of the shaft gear hobbing, the factors affecting the machining accuracy of the hobbing are found out, so as to improve the quality of the hobbing processing.
A heavy-duty automobile gearbox professional production plant, the shaft gear is the most important machine in the gearbox, and the unevenness of the machining accuracy indirectly affects the overall quality of the gearbox. At present, the machining method of the gear teeth used by the factory is the hobbing and shaving method.
Link to this article: Ways To Improve The Accuracy Of Shaft Gear Hobbing
Reprint Statement: If there are no special instructions, all articles on this site are original. Please indicate the source for reprinting:https://www.cncmachiningptj.com/,thanks!
PTJ® provides a full range of Custom Precision cnc machining china services.ISO 9001:2015 &AS-9100 certified. 3, 4 and 5-axis rapid precision CNC machining services including milling, turning to customer specifications,Capable of metal & plastic machined parts with +/-0.005 mm tolerance.Secondary services include CNC and conventional grinding, drilling,die casting,sheet metal and stamping.Providing prototypes, full production runs, technical support and full inspection.Serves the automotive, aerospace, mold&fixture,led lighting,medical,bicycle, and consumer electronics industries. On-time delivery.Tell us a little about your project’s budget and expected delivery time. We will strategize with you to provide the most cost-effective services to help you reach your target,Welcome to Contact us ( sales@pintejin.com ) directly for your new project.
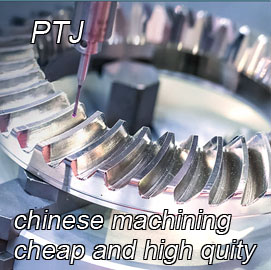
- 5 Axis Machining
- Cnc Milling
- Cnc Turning
- Machining Industries
- Machining Process
- Surface Treatment
- Metal Machining
- Plastic Machining
- Powder Metallurgy Mold
- Die Casting
- Parts Gallery
- Auto Metal Parts
- Machinery Parts
- LED Heatsink
- Building Parts
- Mobile Parts
- Medical Parts
- Electronic Parts
- Tailored Machining
- Bicycle Parts
- Aluminum Machining
- Titanium Machining
- Stainless Steel Machining
- Copper Machining
- Brass Machining
- Super Alloy Machining
- Peek Machining
- UHMW Machining
- Unilate Machining
- PA6 Machining
- PPS Machining
- Teflon Machining
- Inconel Machining
- Tool Steel Machining
- More Material