Rapid Prototyping: An Advantageous Methodology
Rapid Prototyping (RP) is a group of techniques used to quickly fabricate a physical part or assembly using three-dimensional computer-aided design (CAD) data. It generally refers to a variety of manufacturing processes that produce prototypes, often without the need for complex tooling or molds. Over the years, rapid prototyping has emerged as a crucial tool in product development cycles due to its ability to shorten lead times, reduce costs, and enhance innovation.
While traditional manufacturing methods may require weeks or even months to produce a prototype, rapid prototyping can deliver functional models within days, or even hours in some cases. This methodology is employed across various industries, from automotive and aerospace to consumer electronics and healthcare.
Historical Background
The concept of rapid prototyping began gaining prominence in the late 20th century, with the development of technologies like 3D printing (additive manufacturing), CNC machining, and laser cutting. Early rapid prototyping methods were primarily used for form and fit testing, allowing designers to validate physical aspects of their designs before committing to expensive production methods.
In the 1980s and 1990s, the emergence of 3D printing technologies like Stereolithography (SLA) and Selective Laser Sintering (SLS) marked a revolution in rapid prototyping. These methods allowed for the creation of complex geometries directly from CAD models without the need for traditional machining or mold-making. Since then, rapid prototyping techniques have evolved considerably, with modern methods offering greater precision, speed, and material diversity.
Key Techniques in Rapid Prototyping
Additive Manufacturing
Additive Manufacturing (AM) is one of the most well-known and widely used methods of rapid prototyping. Commonly referred to as 3D printing, AM involves the layer-by-layer addition of material to create a physical object. Various techniques fall under this category, including:
- Stereolithography (SLA): Uses a UV laser to cure liquid resin into hardened plastic in a layer-by-layer process.
- Fused Deposition Modeling (FDM): Involves the extrusion of thermoplastic materials to create parts layer by layer.
- Selective Laser Sintering (SLS): Uses a laser to sinter powdered material, fusing particles together to form solid objects.
The advantages of additive manufacturing include the ability to create highly complex geometries, customize designs with ease, and reduce material waste. However, AM processes can sometimes be limited by material properties, surface finish quality, and longer build times for large parts.
Subtractive Manufacturing
Subtractive Manufacturing (SM), as the name suggests, involves the removal of material to create a part. CNC (Computer Numerical Control) machining is a primary example of subtractive rapid prototyping. In this method, a block of material—metal, plastic, or other substrates—is cut, drilled, or milled to shape the final part.
CNC machining offers high precision and can work with a wide range of materials, including metals, plastics, and composites. While it may require more setup time compared to additive methods, CNC machining is often faster for creating prototypes out of materials that are difficult or expensive to 3D print.
Hybrid Manufacturing
Hybrid manufacturing combines both additive and subtractive techniques to create prototypes. For example, a part may be partially printed using an additive method and then finished through CNC machining to achieve tighter tolerances or a better surface finish. This combination allows for greater flexibility in design and manufacturing, making it an appealing choice for industries requiring high precision and complexity.
Casting and Molding
Though casting and molding are typically associated with mass production, some variations of these processes are used for rapid prototyping. Techniques like vacuum casting and silicone molding can produce small batches of parts quickly and affordably. These methods are especially advantageous when creating prototypes for testing in real-world environments or when requiring a certain material property that additive or subtractive methods cannot provide.
Advantages of Rapid Prototyping
Speed and Efficiency
The most significant advantage of rapid prototyping is the ability to dramatically reduce the time required to create a physical part from a design concept. Traditional manufacturing methods often require expensive and time-consuming mold-making or machining processes, whereas RP techniques can bypass these steps entirely.
By using rapid prototyping, companies can iterate on their designs much faster, leading to shorter product development cycles. The ability to create a prototype in a matter of hours or days allows for faster testing, modification, and refinement of ideas.
Cost Reduction
In traditional manufacturing, creating prototypes can be expensive due to the need for specialized tooling, molds, and skilled labor. Rapid prototyping techniques, particularly additive manufacturing, reduce these costs by eliminating the need for molds and using less material. Furthermore, since RP allows for iterative testing and refinement, companies can identify design flaws early, reducing the chances of costly errors during the final production stage.
For startups and small businesses, the cost benefits of rapid prototyping are especially significant, as it allows them to develop products and bring them to market without the need for substantial upfront capital investment.
Flexibility and Customization
One of the key advantages of rapid prototyping is the flexibility it offers in terms of design. Traditional manufacturing methods often impose restrictions on geometry, making it challenging or impossible to produce certain shapes or structures. Rapid prototyping, particularly additive manufacturing, allows for the creation of complex geometries and intricate details that would be difficult to achieve with traditional methods.
Additionally, rapid prototyping enables greater customization, allowing designers to modify and adjust designs quickly and efficiently. This flexibility is especially important in industries such as healthcare, where custom implants or prosthetics may need to be designed for individual patients.
Risk Mitigation
By allowing for the rapid creation of physical models, rapid prototyping helps to mitigate risks in the product development process. Companies can quickly test the form, fit, and function of a prototype and identify potential design flaws before committing to full-scale production. This not only reduces the risk of costly errors but also allows for better-informed decision-making during the design process.
In addition, rapid prototyping enables more thorough testing of a design in real-world conditions. Engineers can evaluate how a prototype performs under various stresses and conditions, helping them to make more informed decisions about material selection, design modifications, and manufacturing processes.
Better Communication and Collaboration
Rapid prototyping enhances communication and collaboration among designers, engineers, and stakeholders. Physical models provide a tangible representation of a design, making it easier for team members to visualize and understand the product. This can lead to more effective collaboration, as team members can more easily identify potential issues and suggest improvements.
In addition, prototypes can be used to gather feedback from customers and other stakeholders, enabling companies to make design adjustments based on user input. This iterative feedback loop helps to ensure that the final product meets customer expectations and performs as intended.
Innovation and Creativity
Rapid prototyping encourages innovation by providing designers and engineers with the tools to quickly experiment with new ideas and concepts. The ability to create physical prototypes in a short amount of time allows for greater experimentation and exploration of design possibilities.
In traditional manufacturing, the cost and time associated with creating prototypes can stifle creativity, as designers may be hesitant to explore unconventional or risky ideas. Rapid prototyping removes these barriers, empowering designers to push the boundaries of what is possible.
Realistic Prototyping for Functional Testing
Beyond just visual models, many rapid prototyping methods allow for the creation of functional prototypes that can be tested in real-world conditions. For example, materials used in processes like SLS and CNC machining often closely resemble the final product materials, allowing for mechanical, thermal, and stress testing.
Functional testing provides essential insights into how a product will behave in its intended environment. Designers can simulate real-world applications and identify any potential design flaws, durability concerns, or performance issues, enabling them to fine-tune the product before moving to mass production.
Scalability
Rapid prototyping is not only beneficial during the early design stages but can also be used for small-batch production. Many RP methods, particularly additive manufacturing, are highly scalable, enabling companies to produce a limited number of parts or products without investing in expensive tooling. This makes rapid prototyping a viable option for low-volume production runs, pilot projects, and market testing.
For example, a company may use RP to produce a small batch of products for beta testing with customers. Feedback from this testing phase can then be used to make further improvements to the design before committing to large-scale production.
Challenges and Limitations of Rapid Prototyping
Material Constraints
While rapid prototyping techniques have advanced significantly, there are still limitations when it comes to material selection. Many additive manufacturing processes, for example, are limited to specific types of plastics, resins, or metals. The mechanical properties of these materials may not always match the requirements of the final product, limiting their suitability for certain applications.
Moreover, some rapid prototyping methods may not be able to replicate the surface finish, durability, or strength of the final product material. This can be a concern when functional testing is needed, as the prototype may not behave exactly as the final product would.
Accuracy and Tolerances
Although rapid prototyping methods can produce highly detailed models, they may not always achieve the same level of precision as traditional manufacturing methods. For applications requiring extremely tight tolerances, such as in aerospace or medical devices, RP techniques may need to be supplemented with additional processes like CNC machining or polishing.
Build Size and Resolution
Many rapid prototyping methods are limited in terms of build size and resolution. Additive manufacturing processes, for example, may have restrictions on the maximum size of a part that can be printed, and larger parts may need to be printed in sections and assembled later. Additionally, the resolution of the final prototype can vary depending on the method used, with some processes producing parts with visible layer lines or surface roughness.
Time Constraints for Complex Geometries
While rapid prototyping can reduce lead times significantly, the time required to produce a prototype can vary depending on the complexity of the design and the method used. For example, highly intricate geometries with fine details may take longer to produce, particularly in additive manufacturing processes that build parts layer by layer. In such cases, alternative methods like CNC machining or casting may be faster, depending on the design requirements.
Cost Considerations for Specialized Materials
Although rapid prototyping is often more cost-effective than traditional methods, certain materials used in additive manufacturing, such as high-performance metals or specialty polymers, can still be expensive. The cost of producing a prototype may increase significantly if specialized materials are required for functional testing or if the design involves complex geometries that require longer build times.
Reprint Statement: If there are no special instructions, all articles on this site are original. Please indicate the source for reprinting:https://www.cncmachiningptj.com/,thanks!
3, 4 and 5-axis precision CNC machining services for aluminum machining, beryllium, carbon steel, magnesium, titanium machining, Inconel, platinum, superalloy, acetal, polycarbonate, fiberglass, graphite and wood. Capable of machining parts up to 98 in. turning dia. and +/-0.001 in. straightness tolerance. Processes include milling, turning, drilling, boring, threading, tapping, forming, knurling, counterboring, countersinking, reaming and laser cutting. Secondary services such as assembly, centerless grinding, heat treating, plating and welding. Prototype and low to high volume production offered with maximum 50,000 units. Suitable for fluid power, pneumatics, hydraulics and valve applications. Serves the aerospace, aircraft, military, medical and defense industries.PTJ will strategize with you to provide the most cost-effective services to help you reach your target,Welcome to Contact us ( sales@pintejin.com ) directly for your new project.
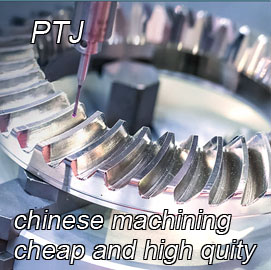
- 5 Axis Machining
- Cnc Milling
- Cnc Turning
- Machining Industries
- Machining Process
- Surface Treatment
- Metal Machining
- Plastic Machining
- Powder Metallurgy Mold
- Die Casting
- Parts Gallery
- Auto Metal Parts
- Machinery Parts
- LED Heatsink
- Building Parts
- Mobile Parts
- Medical Parts
- Electronic Parts
- Tailored Machining
- Bicycle Parts
- Aluminum Machining
- Titanium Machining
- Stainless Steel Machining
- Copper Machining
- Brass Machining
- Super Alloy Machining
- Peek Machining
- UHMW Machining
- Unilate Machining
- PA6 Machining
- PPS Machining
- Teflon Machining
- Inconel Machining
- Tool Steel Machining
- More Material