How to Extrude Aluminium Profiles
Aluminum extrusion is a process used to transform aluminum alloy into objects with a definitive cross-sectional profile for a wide range of uses. This versatile process allows for the creation of complex designs with high precision, making extruded aluminum profiles a critical component in industries such as construction, automotive, aerospace, electronics, and more. In this comprehensive guide, we will explore the various aspects of aluminum extrusion, from the materials used to the technical details of the process, its applications, benefits, and challenges.
1. Introduction to Aluminum Extrusion
Aluminum extrusion is a manufacturing process that involves forcing aluminum alloy through a die to create products with specific cross-sectional profiles. This process takes advantage of aluminum's malleability, allowing it to be formed into intricate and complex shapes without sacrificing strength and other key properties.
1.1 History of Aluminum Extrusion
The process of extrusion was first developed in the early 19th century for soft metals like lead and tin. However, it wasn't until the 20th century that aluminum began to be extruded. The development of aluminum alloys with higher strength-to-weight ratios and the need for lightweight, corrosion-resistant materials in industries like aerospace and automotive led to the rapid adoption of aluminum extrusion technology.
1.2 Overview of the Extrusion Process
The basic principle of extrusion involves pushing a preheated billet of aluminum alloy through a steel die with the desired cross-sectional shape. The extruded material emerges from the die as a long, continuous profile, which is then cooled, stretched, and cut to the desired length.
1.3 Aluminum Alloys Used in Extrusion
Aluminum alloys are classified into various series based on their chemical composition. Each series has its own unique properties, making it suitable for specific applications. The most commonly extruded aluminum alloys are from the 6000 series, which include:
- 6061: Known for its strength, weldability, and corrosion resistance, 6061 is widely used in structural applications.
- 6063: This alloy offers excellent formability and is often used for architectural applications, such as window frames and door frames.
- 6082: Offering a higher strength-to-weight ratio than 6061, 6082 is used in high-stress applications like bridges and cranes.
Other series, such as the 7000 series (e.g., 7075), are used for high-strength applications, while the 1000 series is nearly pure aluminum, offering excellent corrosion resistance but lower strength.
2. The Aluminum Extrusion Process: Step by Step
The aluminum extrusion process consists of several stages, each critical for producing high-quality profiles. These steps include:
2.1 Billet Preparation
The extrusion process begins with the preparation of the aluminum billet. The billet is a cylindrical block of aluminum alloy that serves as the raw material for extrusion. Billets are typically heated to a temperature between 375°C and 500°C (700°F to 930°F), depending on the alloy, to make the aluminum more malleable and easier to extrude.
2.2 Extrusion Press and Die
The extrusion press is a large hydraulic machine that applies pressure to the billet, forcing it through a die. The die is a steel plate with an opening in the shape of the desired cross-sectional profile. Dies can be made for simple shapes, like rods and tubes, or complex shapes with multiple cavities.
- Solid Die: Used for extruding solid shapes like rods and beams.
- Hollow Die: Contains pins or mandrels to create hollow sections, such as tubes.
- Semi-Hollow Die: Used for shapes that are nearly hollow but not entirely.
2.3 The Extrusion Process
Once the billet is heated and loaded into the extrusion press, the process begins:
-
Extrusion: The press forces the billet through the die, and the aluminum emerges from the die in the shape of the die's opening. The extrusion process can be either direct or indirect:
- Direct Extrusion: The most common method, where the billet is pushed through the die by a ram.
- Indirect Extrusion: The die moves towards the billet while the billet remains stationary. This method reduces friction and requires less force.
-
Cooling: The extruded profile is immediately cooled after exiting the die. This is usually done with air or water quenching, depending on the alloy and the desired mechanical properties.
-
Stretching: After cooling, the profile is stretched to straighten it and relieve any internal stresses that may have developed during extrusion.
-
Cutting: The profile is cut to the desired length, typically using a saw.
2.4 Heat Treatment
Certain aluminum alloys require heat treatment to achieve their full strength potential. This can involve aging or tempering processes, where the extruded profile is heated to specific temperatures for controlled durations to enhance mechanical properties such as strength, hardness, and corrosion resistance.
2.5 Finishing
Once the extrusion process is complete, the aluminum profiles may undergo additional finishing processes to improve their appearance or enhance their properties. Common finishing techniques include:
- Anodizing: A process that increases corrosion resistance and allows for color treatments.
- Powder Coating: A finishing technique where powdered paint is applied and then heated to form a durable, protective coating.
- Mechanical Finishing: Processes such as polishing, sanding, or brushing to achieve the desired surface texture.
3. Types of Extruded Aluminum Profiles
Extruded aluminum profiles are classified based on their cross-sectional shape. The most common types include:
3.1 Solid Profiles
Solid profiles have no hollow cavities and are simple in shape. Examples include rods, bars, and beams. These profiles are used in structural applications where strength is important, such as in frames and supports.
3.2 Hollow Profiles
Hollow profiles have one or more internal voids, such as tubes or pipes. These profiles offer excellent strength-to-weight ratios and are commonly used in applications like piping systems, structural frameworks, and automotive parts.
3.3 Semi-Hollow Profiles
Semi-hollow profiles are similar to hollow profiles but contain a partially enclosed void. These profiles are typically used in applications where a balance of strength and formability is required.
4. Design Considerations for Extruded Aluminum Profiles
Designing extruded aluminum profiles requires careful consideration of several factors, including material properties, structural requirements, and manufacturing constraints. Key design considerations include:
4.1 Wall Thickness
Uniform wall thickness is important for maintaining strength and reducing the risk of warping or cracking during the extrusion process. Thicker walls provide greater strength but increase the weight of the profile, while thinner walls offer weight savings but may reduce strength.
4.2 Tolerances
Aluminum extrusion offers excellent dimensional accuracy, but certain tolerances must be considered based on the complexity of the profile and the intended application. Tight tolerances increase the cost of extrusion, so it's important to balance precision with cost-effectiveness.
4.3 Draft Angle
Draft angles help facilitate the extrusion process by allowing the aluminum to flow smoothly through the die. Profiles with steep angles may experience flow issues, while profiles with shallow angles may require higher extrusion forces.
4.4 Radius and Corners
Sharp corners can cause stress concentrations and may be difficult to extrude. Designers typically incorporate radii at corners to distribute stress more evenly and improve the overall strength of the profile.
5. Applications of Extruded Aluminum Profiles
Extruded aluminum profiles are used across a wide range of industries due to their versatility, strength, and lightweight properties. Common applications include:
5.1 Construction and Architecture
Aluminum profiles are widely used in construction and architectural applications, including window and door frames, curtain walls, roofing systems, and structural components. Their corrosion resistance and ease of fabrication make them ideal for outdoor and structural applications.
5.2 Automotive and Transportation
In the automotive and transportation industries, aluminum profiles are used to reduce vehicle weight, improve fuel efficiency, and enhance crash performance. Extruded components can be found in everything from body panels and frames to engine components and heat exchangers.
5.3 Aerospace
The aerospace industry relies on extruded aluminum profiles for lightweight, high-strength components that can withstand extreme environmental conditions. Applications include fuselage frames, wing structures, and interior components.
5.4 Electronics and Electrical
Aluminum's excellent thermal conductivity makes it a popular choice for heat sinks and cooling systems in electronics. Extruded profiles are also used in electrical enclosures, lighting fixtures, and conductive components.
5.5 Renewable Energy
The renewable energy sector uses extruded aluminum profiles in solar panel frames, wind turbine components, and energy storage systems. Aluminum's lightweight and corrosion-resistant properties make it ideal for outdoor energy applications.
6. Benefits of Aluminum Extrusion
Aluminum extrusion offers several key advantages that make it a preferred manufacturing method for many industries:
6.1 Lightweight
Aluminum has a high strength-to-weight ratio, making it an ideal material for applications where weight reduction is critical, such as in transportation and aerospace.
6.2 Corrosion Resistance
Aluminum naturally forms a protective oxide layer that resists corrosion, making it suitable for outdoor and marine environments.
6.3 Versatility
The extrusion process allows for the creation of complex, custom-designed profiles that can meet a wide range of structural and aesthetic requirements.
6.4 Recyclability
Aluminum is 100% recyclable without loss of quality, making it an environmentally friendly choice for industries focused on sustainability.
6.5 Cost-Effectiveness
Compared to other metals, aluminum is relatively inexpensive, and the extrusion process is efficient, resulting in lower production costs for high-volume manufacturing.
Reprint Statement: If there are no special instructions, all articles on this site are original. Please indicate the source for reprinting:https://www.cncmachiningptj.com/,thanks!
3, 4 and 5-axis precision CNC machining services for aluminum machining, beryllium, carbon steel, magnesium, titanium machining, Inconel, platinum, superalloy, acetal, polycarbonate, fiberglass, graphite and wood. Capable of machining parts up to 98 in. turning dia. and +/-0.001 in. straightness tolerance. Processes include milling, turning, drilling, boring, threading, tapping, forming, knurling, counterboring, countersinking, reaming and laser cutting. Secondary services such as assembly, centerless grinding, heat treating, plating and welding. Prototype and low to high volume production offered with maximum 50,000 units. Suitable for fluid power, pneumatics, hydraulics and valve applications. Serves the aerospace, aircraft, military, medical and defense industries.PTJ will strategize with you to provide the most cost-effective services to help you reach your target,Welcome to Contact us ( sales@pintejin.com ) directly for your new project.
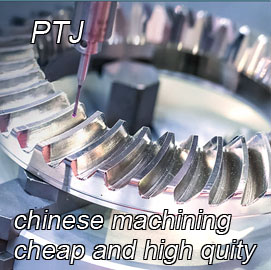
- 5 Axis Machining
- Cnc Milling
- Cnc Turning
- Machining Industries
- Machining Process
- Surface Treatment
- Metal Machining
- Plastic Machining
- Powder Metallurgy Mold
- Die Casting
- Parts Gallery
- Auto Metal Parts
- Machinery Parts
- LED Heatsink
- Building Parts
- Mobile Parts
- Medical Parts
- Electronic Parts
- Tailored Machining
- Bicycle Parts
- Aluminum Machining
- Titanium Machining
- Stainless Steel Machining
- Copper Machining
- Brass Machining
- Super Alloy Machining
- Peek Machining
- UHMW Machining
- Unilate Machining
- PA6 Machining
- PPS Machining
- Teflon Machining
- Inconel Machining
- Tool Steel Machining
- More Material