Brass H62: Structure and Properties
Brass H62 is a widely utilized copper alloy primarily composed of copper (Cu) and zinc (Zn), with a nominal composition of 62% copper and 38% zinc. Known for its excellent mechanical properties, corrosion resistance, and aesthetic appearance, H62 brass is commonly used in a variety of applications, ranging from plumbing and electrical components to decorative items. This article delves into the metallurgical structure, physical and chemical properties, mechanical behavior, and various applications of H62 brass, alongside a discussion of its processing techniques, historical background, and comparative analysis with other copper-zinc alloys.
Chemical Composition
The chemical composition of Brass H62 is characterized by a high copper content, with zinc as the principal alloying element. The typical composition is approximately 61.5% to 63.5% copper and the remainder zinc. Trace elements such as lead (Pb), iron (Fe), and silicon (Si) may be present in minute quantities, affecting the alloy's properties slightly. The composition of H62 is regulated by standards such as GB/T 5231 in China, which ensures consistency in its application.
Metallurgical Structure
H62 brass exhibits a dual-phase microstructure comprising α (alpha) and β (beta) phases. The α-phase is a solid solution of zinc in copper and is predominant in the alloy. It provides ductility and corrosion resistance. The β-phase, which is a more complex intermetallic phase, emerges as zinc content increases. In H62 brass, the β-phase is present in smaller quantities and contributes to the alloy's hardness and strength. The distribution and morphology of these phases are influenced by the cooling rate during solidification and subsequent heat treatment processes.
Crystallographic Structure
The α-phase of H62 brass has a face-centered cubic (FCC) structure, which is typical of copper and its alloys. This structure allows for a high degree of slip and deformation, leading to good ductility. The β-phase, in contrast, has a body-centered cubic (BCC) structure, which is less ductile but contributes to the alloy's overall strength. The crystallographic orientation and grain size of these phases play a crucial role in determining the mechanical properties of the alloy.
Mechanical Properties
H62 brass is known for its excellent mechanical properties, which include a good balance between strength and ductility. The alloy has a typical tensile strength ranging from 300 to 400 MPa, with an elongation at break of about 40% to 60%. These properties can be tailored through various heat treatment processes, such as annealing, which can soften the alloy and improve its workability. The hardness of H62 brass, typically measured on the Brinell scale, can vary depending on the phase distribution and the degree of cold working it has undergone.
Thermal Properties
The thermal properties of H62 brass are characterized by its high thermal conductivity, which is a hallmark of copper-based alloys. The thermal conductivity of H62 brass is approximately 120 W/m·K, making it suitable for applications where heat dissipation is critical, such as in heat exchangers and radiators. The alloy also has a moderate coefficient of thermal expansion, which needs to be considered in applications involving temperature variations to prevent thermal stress and deformation.
Electrical Properties
H62 brass has good electrical conductivity, although it is lower than that of pure copper. The electrical conductivity of H62 brass is typically around 28% IACS (International Annealed Copper Standard), which is sufficient for many electrical and electronic applications, such as connectors and terminals. The presence of zinc, while lowering the conductivity compared to pure copper, also improves the alloy's mechanical strength, making it a better choice for components that require both electrical and mechanical performance.
Corrosion Resistance
The corrosion resistance of H62 brass is one of its most valued properties. The alloy exhibits good resistance to atmospheric corrosion, seawater corrosion, and various other environments. The α-phase is particularly resistant to corrosion, while the β-phase is slightly less so. The alloy's resistance to dezincification, a form of corrosion where zinc is selectively leached out of the alloy, is adequate for most applications, although it may require additional protective measures in highly aggressive environments.
Formability and Machinability
H62 brass is highly formable and can be easily worked into various shapes through processes such as rolling, drawing, and extrusion. Its ductility allows for deep drawing and other complex forming operations without cracking. The machinability of H62 brass is also good, making it suitable for high-speed machining operations. The alloy can be easily drilled, milled, and turned, with good surface finish quality and tool life.
Heat Treatment
Heat treatment plays a significant role in adjusting the mechanical properties of H62 brass. Annealing is commonly used to soften the alloy and relieve internal stresses caused by cold working. The annealing temperature for H62 brass is typically in the range of 450°C to 600°C. Quenching after hot working or annealing can lead to the formation of a finer grain structure, improving the alloy's mechanical properties. The choice of heat treatment parameters depends on the desired balance between strength and ductility.
Applications
H62 brass is used in a wide range of applications due to its excellent combination of properties. In the plumbing industry, it is used for valves, fittings, and connectors due to its corrosion resistance and formability. In the electrical industry, it is used for terminals, connectors, and other components where both mechanical strength and electrical conductivity are required. H62 brass is also used in the manufacture of musical instruments, decorative items, and various household products, owing to its attractive appearance and ease of fabrication.
Comparative Analysis with Other Brasses
Compared to other brass alloys, H62 offers a good balance between cost and performance. For instance, while H70 brass, with a higher copper content, offers better corrosion resistance and electrical conductivity, H62 is more economical and has sufficient properties for many applications. Conversely, alloys with higher zinc content, such as H59, may offer better machinability but at the cost of reduced corrosion resistance. The choice of brass alloy depends on the specific requirements of the application, with H62 being a versatile option for general-purpose use.
Historical Context and Development
The use of brass dates back thousands of years, with early civilizations recognizing the beneficial properties of copper-zinc alloys. H62 brass, as it is known today, was developed in response to the need for an alloy that offered a good combination of strength, corrosion resistance, and formability at a reasonable cost. The development of modern metallurgical techniques has allowed for the precise control of the composition and microstructure of H62 brass, leading to its widespread use in various industries.
Processing Techniques
The manufacturing process of H62 brass typically involves melting and casting the raw materials, followed by hot and cold working processes such as rolling, extrusion, and drawing. The alloy may also undergo various finishing processes, such as annealing, quenching, and surface treatment, to achieve the desired mechanical properties and surface quality. The processing techniques used can significantly influence the final properties of the alloy, making it essential to optimize the manufacturing parameters for each specific application.
Environmental and Health Considerations
Like other copper alloys, H62 brass is considered to be environmentally friendly due to its recyclability. The alloy can be easily recycled without significant loss of its properties, making it a sustainable choice for various applications. However, care must be taken during the manufacturing and machining processes to minimize the release of zinc and other potentially harmful elements into the environment. Additionally, appropriate protective measures should be in place to prevent exposure to fine metal dust during machining operations.
Future Developments
Ongoing research in the field of metallurgy continues to explore ways to improve the properties of H62 brass, such as enhancing its corrosion resistance, mechanical strength, and formability. Advances in additive manufacturing and powder metallurgy techniques may also offer new opportunities for the use of H62 brass in complex and high-performance applications. The development of new surface treatments and coatings could further extend the range of environments in which H62 brass can be used.
Conclusion
Brass H62 is a versatile and widely used copper-zinc alloy, known for its excellent combination of mechanical properties, corrosion resistance, and formability. Its dual-phase microstructure, consisting of α and β phases, plays a crucial role in determining its behavior under various conditions. H62 brass is used in a broad range of industries, from plumbing and electrical components to decorative and artistic applications. The alloy's historical significance, coupled with ongoing research and development, ensures its continued relevance in modern manufacturing and engineering.
Reprint Statement: If there are no special instructions, all articles on this site are original. Please indicate the source for reprinting:https://www.cncmachiningptj.com/,thanks!
PTJ® provides a full range of Custom Precision cnc machining china services.ISO 9001:2015 &AS-9100 certified. 3, 4 and 5-axis rapid precision CNC machining services including milling, turning to customer specifications,Capable of metal & plastic machined parts with +/-0.005 mm tolerance.Secondary services include CNC and conventional grinding, drilling,die casting,sheet metal and stamping.Providing prototypes, full production runs, technical support and full inspection.Serves the automotive, aerospace, mold&fixture,led lighting,medical,bicycle, and consumer electronics industries. On-time delivery.Tell us a little about your project's budget and expected delivery time. We will strategize with you to provide the most cost-effective services to help you reach your target,Welcome to Contact us ( sales@pintejin.com ) directly for your new project.
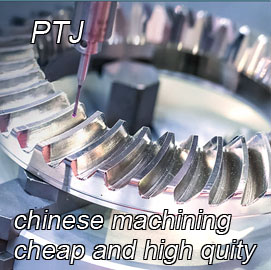
- 5 Axis Machining
- Cnc Milling
- Cnc Turning
- Machining Industries
- Machining Process
- Surface Treatment
- Metal Machining
- Plastic Machining
- Powder Metallurgy Mold
- Die Casting
- Parts Gallery
- Auto Metal Parts
- Machinery Parts
- LED Heatsink
- Building Parts
- Mobile Parts
- Medical Parts
- Electronic Parts
- Tailored Machining
- Bicycle Parts
- Aluminum Machining
- Titanium Machining
- Stainless Steel Machining
- Copper Machining
- Brass Machining
- Super Alloy Machining
- Peek Machining
- UHMW Machining
- Unilate Machining
- PA6 Machining
- PPS Machining
- Teflon Machining
- Inconel Machining
- Tool Steel Machining
- More Material