Specifications and Standards For Aluminum Alloys Anodizing
Anodizing is an electrochemical process that enhances the natural oxide layer on the surface of aluminum and its alloys, producing a durable, corrosion-resistant, and aesthetically appealing finish. This process not only improves the material's resistance to wear and corrosion but also allows for the application of vibrant colors and various finishes that are widely used in a multitude of industries. Anodizing is a critical process in manufacturing, especially for applications where aluminum alloys are required to maintain high performance and aesthetic standards over extended periods.
Importance in Aluminum Alloys
Aluminum alloys are known for their lightweight, high strength-to-weight ratio, and excellent corrosion resistance, making them suitable for a wide range of applications, from aerospace components to architectural elements. However, aluminum's surface properties can be further enhanced through anodizing, which significantly improves its durability, wear resistance, and ability to retain finishes. Anodizing not only increases the surface hardness of aluminum alloys but also improves their aesthetic appeal by allowing for various dyeing and finishing options.
Applications of Anodized Aluminum
Anodized aluminum alloys are used in a broad array of applications across multiple industries. In the aerospace industry, anodized aluminum provides essential protection against corrosion while maintaining the lightweight characteristics necessary for flight. In architecture, anodized aluminum is favored for its aesthetic versatility and resistance to environmental factors. Consumer electronics, automotive, marine, and defense sectors also rely heavily on anodized aluminum for components that require both strength and durability with an attractive finish.
Basics of Anodizing Aluminum
Anodizing is a controlled electrochemical process that thickens the naturally occurring oxide layer on the surface of aluminum. The process involves immersing the aluminum in an electrolyte bath, typically sulfuric acid, and applying a direct current across the material. The aluminum acts as the anode, hence the term "anodizing," and oxygen ions are released from the electrolyte, reacting with the aluminum surface to form aluminum oxide. This oxide layer is much thicker than the natural oxide layer, providing enhanced protective properties.
Electrochemical Principles
The anodizing process is based on the principles of electrolysis, where the aluminum workpiece acts as the anode in an electrochemical cell. The application of an electric current drives the oxidation of the aluminum surface, converting it into a porous aluminum oxide layer. The thickness and properties of the anodic layer can be controlled by adjusting the voltage, electrolyte concentration, temperature, and processing time. The porous nature of the anodized layer allows for dyeing, while subsequent sealing treatments close the pores, locking in the color and enhancing the corrosion resistance.
Types of Anodizing Processes
Several anodizing processes are tailored to different performance requirements and aesthetic outcomes:
- Sulfuric Acid Anodizing: The most common anodizing process, it provides a balance of hardness, thickness, and colorability, making it versatile for many applications.
- Chromic Acid Anodizing: Known for producing thinner and more flexible coatings, it is often used in aerospace applications where fatigue resistance is crucial.
- Hard Anodizing: This process produces a much thicker and harder oxide layer, ideal for applications requiring superior wear resistance and corrosion protection.
- Other Types: These include phosphoric acid anodizing, which is used as a pre-treatment for adhesive bonding, and boric-sulfuric anodizing, a more environmentally friendly alternative to chromic acid anodizing.
Benefits of Anodizing
Anodizing aluminum alloys offers several benefits, including:
- Enhanced Corrosion Resistance: The anodic layer acts as a barrier against environmental elements, significantly improving the material's longevity.
- Improved Surface Hardness: Hard anodizing, in particular, greatly increases the surface hardness of aluminum, making it more resistant to abrasion and wear.
- Aesthetic Flexibility: The porous nature of the anodic layer allows for the absorption of dyes, enabling a wide range of colors and finishes.
- Thermal Stability: Anodized coatings can withstand high temperatures, making them suitable for components exposed to extreme environments.
- Electrical Insulation: The anodic oxide layer is a good electrical insulator, which is beneficial for certain electronic applications.
Aluminum Alloys Suitable for Anodizing
Aluminum alloys are categorized based on their primary alloying elements, such as magnesium, silicon, copper, and zinc, each imparting different properties to the material. These alloys are classified into two main groups: wrought alloys and cast alloys. The response of these alloys to anodizing varies significantly, with some being more suitable than others for producing high-quality anodized finishes.
Anodizing Response of Various Alloys
The composition of an aluminum alloy greatly influences its anodizing response. Alloys with high silicon or copper content, for example, may produce a darker, less aesthetically pleasing finish, while those with higher purity levels or magnesium content typically anodize to a bright, clear finish. The choice of alloy must be carefully considered based on the desired properties of the anodized layer, such as thickness, hardness, and color.
Common Alloys Used in Anodizing
- 6061 Aluminum: A versatile alloy with good mechanical properties and excellent anodizing response, commonly used in structural applications.
- 5052 Aluminum: Known for its excellent corrosion resistance, this alloy is frequently anodized for marine applications.
- 7075 Aluminum: A high-strength alloy often used in aerospace applications, it can be anodized to enhance its surface properties despite its higher copper content.
- 1100 Aluminum: A commercially pure aluminum with excellent anodizing characteristics, ideal for decorative applications.
Influence of Alloy Composition on Anodizing Quality
The presence of alloying elements such as silicon, copper, and zinc can affect the uniformity, color, and corrosion resistance of the anodic coating. Silicon, for example, can lead to a darker and less consistent finish, while copper can increase the risk of pitting during anodizing. Therefore, understanding the composition of the alloy is crucial for achieving the desired anodized outcome.
Reprint Statement: If there are no special instructions, all articles on this site are original. Please indicate the source for reprinting:https://www.cncmachiningptj.com/,thanks!
3, 4 and 5-axis precision CNC machining services for aluminum machining, beryllium, carbon steel, magnesium, titanium machining, Inconel, platinum, superalloy, acetal, polycarbonate, fiberglass, graphite and wood. Capable of machining parts up to 98 in. turning dia. and +/-0.001 in. straightness tolerance. Processes include milling, turning, drilling, boring, threading, tapping, forming, knurling, counterboring, countersinking, reaming and laser cutting. Secondary services such as assembly, centerless grinding, heat treating, plating and welding. Prototype and low to high volume production offered with maximum 50,000 units. Suitable for fluid power, pneumatics, hydraulics and valve applications. Serves the aerospace, aircraft, military, medical and defense industries.PTJ will strategize with you to provide the most cost-effective services to help you reach your target,Welcome to Contact us ( sales@pintejin.com ) directly for your new project.
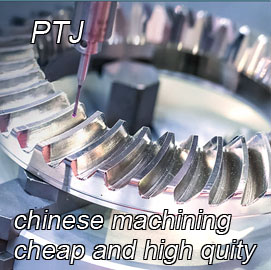
- 5 Axis Machining
- Cnc Milling
- Cnc Turning
- Machining Industries
- Machining Process
- Surface Treatment
- Metal Machining
- Plastic Machining
- Powder Metallurgy Mold
- Die Casting
- Parts Gallery
- Auto Metal Parts
- Machinery Parts
- LED Heatsink
- Building Parts
- Mobile Parts
- Medical Parts
- Electronic Parts
- Tailored Machining
- Bicycle Parts
- Aluminum Machining
- Titanium Machining
- Stainless Steel Machining
- Copper Machining
- Brass Machining
- Super Alloy Machining
- Peek Machining
- UHMW Machining
- Unilate Machining
- PA6 Machining
- PPS Machining
- Teflon Machining
- Inconel Machining
- Tool Steel Machining
- More Material