How to Make a 20 Sided Die Resin Cast
A 20-sided die, commonly referred to as a d20, is a fundamental tool in tabletop role-playing games (RPGs) like Dungeons & Dragons. The die, a platonic solid known as an icosahedron, has 20 equilateral triangular faces, with each face displaying a number from 1 to 20. Resin casting has become a popular method for producing custom dice, allowing enthusiasts to create unique and personalized gaming tools.
Overview of the Process
The process of making a 20-sided die involves several key steps:
- Design and Prototyping: Creating a 3D model of the die, either by hand-sculpting or using 3D printing technology.
- Mold-Making: Crafting a silicone mold that will be used to cast the resin die.
- Resin Casting: Pouring and curing the resin in the mold.
- Demolding and Cleaning: Removing the die from the mold and cleaning any excess material.
- Sanding and Polishing: Refining the surface of the die to achieve a smooth finish.
- Number Painting and Sealing: Enhancing the die's appearance by painting the numbers and applying a protective coating.
Each of these steps requires specific materials and tools, as well as careful attention to detail.
Design and Prototyping
3D Modeling
The first step in creating a 20-sided die is to design the die itself. This can be done using a variety of methods, but 3D modeling software is commonly used due to its precision and versatility.
Software Options
Several 3D modeling programs are suitable for designing a d20, including:
- Blender: A free and open-source 3D creation suite that is widely used for modeling, rendering, and animation.
- Autodesk Fusion 360: A powerful CAD software that offers advanced modeling and simulation tools.
- Tinkercad: A user-friendly, web-based CAD tool that is ideal for beginners.
Designing the Icosahedron
In the software, start by creating an icosahedron, which is the geometric shape of the die. The icosahedron consists of 20 equilateral triangles, and each vertex must meet the others at the correct angles to ensure symmetry. Many 3D modeling programs have built-in tools or plugins that allow for the quick generation of platonic solids, including the icosahedron.
Number Placement
Once the basic shape is created, the next step is to add the numbers to each face of the die. The placement of the numbers is critical to ensure that the die is fair and balanced. Typically, the numbers are arranged so that opposite faces add up to 21 (e.g., 1 opposite 20, 2 opposite 19, etc.).
To do this:
- Select each face of the icosahedron.
- Use the text tool to add numbers to the center of each face.
- Adjust the size and position of the numbers to ensure they are centered and legible.
Prototyping
After the 3D model is complete, you can create a physical prototype. This can be done using a 3D printer or by hand-carving a master from a solid material like clay or wax. The prototype will serve as the master model for creating the mold.
3D Printing the Master
If you choose to use a 3D printer, select a printer capable of producing high-resolution models to ensure the die's faces are smooth and the numbers are clearly defined. Resin-based printers, such as those using stereolithography (SLA) or digital light processing (DLP), are particularly well-suited for this task due to their precision.
After printing, the master model may require post-processing, such as sanding or curing, to prepare it for mold-making.
Mold-Making
Materials for Mold-Making
Silicone rubber is the preferred material for making molds, as it captures fine details and is flexible, making it easy to demold the resin cast. Several types of silicone are available, including:
- Tin-cure silicone: A cost-effective option with good durability.
- Platinum-cure silicone: A more expensive option with higher durability and better tear resistance.
Other materials needed include:
- Mold box: A container to hold the silicone while it cures.
- Mold release agent: A substance that prevents the silicone from sticking to the master model or the mold box.
Mold-Making Process
-
Prepare the Master Model: Clean the master model and apply a mold release agent to ensure it does not stick to the silicone.
-
Construct the Mold Box: The mold box should be slightly larger than the master model, allowing enough space for the silicone to fully encapsulate the model. The box can be made from materials like Lego bricks, foam board, or even disposable plastic containers.
-
Position the Master Model: Secure the master model in the mold box, ensuring it is centered and suspended slightly above the bottom to allow for a uniform silicone layer.
-
Mix and Pour the Silicone: Mix the silicone rubber according to the manufacturer’s instructions, ensuring thorough mixing to avoid uncured spots. Slowly pour the silicone into the mold box, starting from one corner and allowing it to flow over the model to minimize air bubbles.
-
Curing: Allow the silicone to cure for the recommended time, which can vary from a few hours to a full day depending on the type of silicone used.
-
Demolding: Once cured, carefully remove the mold from the box and then extract the master model from the silicone. The mold should now have a cavity in the shape of the 20-sided die, ready for casting.
Resin Casting
Materials for Resin Casting
Resin casting involves the use of liquid resin that hardens into a solid form. There are various types of resins, but the most common for dice casting are epoxy resin and polyurethane resin.
- Epoxy resin: Known for its clarity and strength, it is widely used in crafts and jewelry making.
- Polyurethane resin: Offers faster curing times but may yellow over time, which is a consideration for clear or light-colored dice.
Other materials needed include:
- Resin dyes or pigments: Used to add color to the resin.
- Mixing cups and stir sticks: For mixing the resin and hardener.
- Disposable gloves and protective equipment: To protect the skin from resin, which can be irritating.
Casting Process
-
Prepare the Mold: Apply a mold release agent to the silicone mold to ensure the resin cast can be easily removed once cured.
-
Mix the Resin: Measure and mix the resin and hardener according to the manufacturer’s instructions. Accurate measurement is crucial to ensure proper curing. Add any dyes, pigments, or inclusions at this stage, and stir thoroughly to achieve an even color distribution.
-
Pouring the Resin: Slowly pour the resin into the mold, filling it completely. Pouring slowly reduces the risk of air bubbles forming. For added control, consider using a syringe to inject the resin into the mold.
-
Pressure Casting (Optional): To remove air bubbles and ensure a clear cast, you can place the filled mold in a pressure pot. The pressure forces any trapped air out of the resin, resulting in a clearer, smoother die.
-
Curing: Allow the resin to cure according to the manufacturer’s instructions. Curing times can vary, with some resins taking as little as a few hours, while others may require up to 24 hours.
-
Demolding: Once the resin is fully cured, carefully remove the die from the mold. Inspect the cast for any defects, such as air bubbles or incomplete filling, which may require re-casting.
Demolding and Cleaning
After demolding, the cast resin die may have excess material, known as flash, around the edges. This excess resin is a result of small amounts of resin seeping between the two halves of the mold.
Cleaning the Die
-
Trimming: Use a sharp hobby knife or small scissors to carefully trim away any excess resin. Take care not to damage the die’s edges or faces.
-
Inspecting: Check the die for any imperfections that might affect its balance or aesthetics. If necessary, minor defects can be filled with additional resin or sanded down.
Sanding and Polishing
Sanding and polishing are critical steps in achieving a smooth, professional finish on the die. This process involves gradually refining the surface of the die, removing any rough spots, and creating a glossy finish.
Sanding
-
Wet Sanding: Start with a coarse grit sandpaper (e.g., 400 grit) and work your way up to finer grits (e.g., 1000, 2000, and 3000 grit). Wet sanding is recommended, as it reduces the dust produced and provides a smoother finish.
-
Sanding Process: Hold the die securely and gently sand each face in a circular motion. Be sure to evenly sand all surfaces to maintain the die’s balance. Rinse the die and change to finer grit sandpaper as you progress.
Polishing
-
Polishing Compound: Apply a small amount of plastic polishing compound to a soft cloth or buffing wheel. Gently polish the die in circular motions until a smooth, glossy finish is achieved.
-
Final Inspection: After polishing, inspect the die for any remaining imperfections. If necessary, repeat the sanding and polishing process until the desired finish is achieved.
Number Painting and Sealing
The final steps involve painting the numbers on the die and applying a protective sealant to ensure durability.
Number Painting
-
Choosing Paint: Acrylic paint is commonly used for number painting due to its ease of use and wide range of colors.
-
Applying Paint: Using a fine-tipped brush or a paint pen, carefully apply paint to the numbers. Avoid overloading the brush with paint to prevent it from spilling over onto the die's faces.
-
Cleaning Up: If paint does spill over, use a damp cloth or cotton swab to gently wipe away any excess before it dries.
Sealing the Die
-
Sealant Options: To protect the die and the painted numbers, apply a clear sealant. Options include spray varnishes or brush-on sealants like polyurethane or epoxy.
-
Application: Apply the sealant in thin, even coats, allowing each coat to dry fully before applying the next. This will protect the die from wear and ensure the paint remains intact during use.
Conclusion
Creating a 20-sided die using resin casting is a detailed process that requires precision, patience, and creativity. From designing and prototyping to casting, sanding, and finishing, each step is essential to producing a high-quality die that is both functional and aesthetically pleasing. By following this guide, hobbyists and artisans can craft personalized dice that enhance their tabletop gaming experience and showcase their craftsmanship.
Reprint Statement: If there are no special instructions, all articles on this site are original. Please indicate the source for reprinting:https://www.cncmachiningptj.com/,thanks!
3, 4 and 5-axis precision CNC machining services for aluminum machining, beryllium, carbon steel, magnesium, titanium machining, Inconel, platinum, superalloy, acetal, polycarbonate, fiberglass, graphite and wood. Capable of machining parts up to 98 in. turning dia. and +/-0.001 in. straightness tolerance. Processes include milling, turning, drilling, boring, threading, tapping, forming, knurling, counterboring, countersinking, reaming and laser cutting. Secondary services such as assembly, centerless grinding, heat treating, plating and welding. Prototype and low to high volume production offered with maximum 50,000 units. Suitable for fluid power, pneumatics, hydraulics and valve applications. Serves the aerospace, aircraft, military, medical and defense industries.PTJ will strategize with you to provide the most cost-effective services to help you reach your target,Welcome to Contact us ( sales@pintejin.com ) directly for your new project.
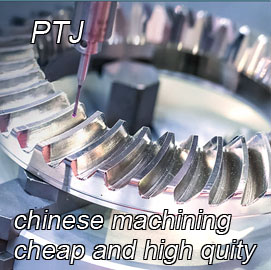
- 5 Axis Machining
- Cnc Milling
- Cnc Turning
- Machining Industries
- Machining Process
- Surface Treatment
- Metal Machining
- Plastic Machining
- Powder Metallurgy Mold
- Die Casting
- Parts Gallery
- Auto Metal Parts
- Machinery Parts
- LED Heatsink
- Building Parts
- Mobile Parts
- Medical Parts
- Electronic Parts
- Tailored Machining
- Bicycle Parts
- Aluminum Machining
- Titanium Machining
- Stainless Steel Machining
- Copper Machining
- Brass Machining
- Super Alloy Machining
- Peek Machining
- UHMW Machining
- Unilate Machining
- PA6 Machining
- PPS Machining
- Teflon Machining
- Inconel Machining
- Tool Steel Machining
- More Material