When Was Rapid Prototyping Invented
Rapid prototyping (RP) refers to a group of techniques used to quickly fabricate a scale model of a physical part or assembly using three-dimensional computer-aided design (CAD) data. This revolutionary technology emerged in the late 20th century and has since transformed industries such as manufacturing, engineering, healthcare, and education.
Early Concepts and Origins
The concept of rapid prototyping is deeply rooted in the broader evolution of manufacturing and production technologies. The earliest forms of prototyping can be traced back to the early 20th century when industrial designers and engineers began exploring ways to streamline the design-to-production process.
-
Predecessors to RP
- Model Making: Before the advent of rapid prototyping, physical models were painstakingly crafted by hand or through traditional machining processes. This was time-consuming, expensive, and often prone to inaccuracies.
- Automated Processes: The desire to automate and accelerate these processes led to the development of technologies like numerically controlled (NC) machining, which laid the groundwork for more advanced techniques.
-
The Birth of CAD (1960s-1970s)
- CAD Development: The introduction of computer-aided design (CAD) systems in the 1960s revolutionized the way designs were conceptualized and communicated. Early CAD systems allowed for the creation of precise digital models, paving the way for subsequent advancements in manufacturing.
- Integration with CAM: The coupling of CAD with computer-aided manufacturing (CAM) enabled more efficient translation of designs into physical objects, further narrowing the gap between conceptualization and production.
The Advent of Rapid Prototyping (1980s)
The 1980s marked the true beginning of rapid prototyping as we know it today. During this decade, several key technologies were developed that allowed for the rapid and automated creation of physical models from digital designs.
-
Stereolithography (SLA)
- Introduction of SLA: In 1983, Dr. Chuck Hull invented stereolithography, a process that uses ultraviolet (UV) lasers to solidify layers of photopolymer resin, building up a three-dimensional object layer by layer. This was the first commercialized rapid prototyping technology, and Hull later co-founded 3D Systems, a company that would become a pioneer in the field.
- Impact: SLA allowed for the creation of complex geometries with high accuracy, something that was not possible with traditional methods. It was a game-changer for industries such as automotive, aerospace, and medical device manufacturing.
-
Selective Laser Sintering (SLS)
- Development of SLS: In the mid-1980s, Carl Deckard at the University of Texas developed selective laser sintering (SLS), a process that uses a laser to fuse powdered materials (such as nylon, metals, or ceramics) into solid objects. Unlike SLA, SLS did not require support structures, making it suitable for more complex and intricate designs.
- Commercialization: Deckard’s work led to the founding of DTM Corporation, which commercialized SLS technology. SLS quickly became popular due to its ability to produce functional prototypes and end-use parts.
-
Fused Deposition Modeling (FDM)
- Invention of FDM: In 1988, Scott Crump invented fused deposition modeling (FDM), a process in which a thermoplastic filament is extruded through a heated nozzle, layer by layer, to build up a part. Crump co-founded Stratasys, another major player in the rapid prototyping industry.
- Accessibility: FDM technology was more affordable and user-friendly compared to SLA and SLS, making it accessible to a broader range of industries and hobbyists. It has since become one of the most widely used 3D printing technologies.
Evolution and Expansion (1990s-2000s)
As rapid prototyping technologies matured, they became more sophisticated, versatile, and widely adopted across various industries.
-
Diversification of Materials
- Introduction of New Materials: The 1990s and 2000s saw the introduction of a wide variety of materials that could be used in rapid prototyping, including metals, ceramics, and bio-compatible polymers. This diversification allowed for the production of prototypes and final parts with specific material properties tailored to their intended applications.
- Functional Prototyping: The ability to prototype with a range of materials enabled the creation of functional prototypes that could be tested under real-world conditions, leading to more reliable and optimized designs.
-
Advances in Software
- Improvement in CAD/CAM: As CAD and CAM software evolved, they became more powerful and user-friendly, with enhanced capabilities for handling complex geometries, simulating performance, and optimizing designs for rapid prototyping.
- Integration with Simulation: The integration of simulation tools with rapid prototyping allowed designers to predict the performance of prototypes before they were physically produced, reducing the need for multiple iterations and speeding up the development process.
-
Proliferation of RP Technologies
- Emergence of New Techniques: Beyond SLA, SLS, and FDM, other rapid prototyping techniques emerged during this period, such as Laminated Object Manufacturing (LOM), Digital Light Processing (DLP), and Electron Beam Melting (EBM). Each of these techniques offered unique advantages in terms of speed, precision, and material compatibility.
- Adoption Across Industries: Rapid prototyping expanded beyond its initial applications in automotive and aerospace into sectors such as consumer electronics, healthcare (particularly in the production of custom implants and prosthetics), and even art and fashion.
The Rise of Additive Manufacturing (2010s-Present)
By the 2010s, rapid prototyping had evolved into what is now commonly referred to as additive manufacturing (AM), encompassing not just prototyping but also the production of end-use parts.
-
Additive Manufacturing Revolution
- Transition to Production: The distinction between prototyping and production began to blur as additive manufacturing technologies improved in terms of speed, cost, and material capabilities. Industries started using AM for the production of small-batch and customized parts, especially in high-value sectors such as aerospace and healthcare.
- Customization and Personalization: The ability to create custom, one-of-a-kind products became a major selling point of additive manufacturing. This was particularly evident in the medical field, where patient-specific implants, prosthetics, and dental appliances could be produced with unmatched precision.
-
Globalization and Democratization
- Rise of 3D Printing: The widespread availability of affordable 3D printers brought rapid prototyping into homes, schools, and small businesses. The maker movement, fueled by open-source hardware and software, democratized access to rapid prototyping tools, fostering innovation at all levels of society.
- Educational Impact: Rapid prototyping became an integral part of STEM (Science, Technology, Engineering, and Mathematics) education, providing students with hands-on experience in design and manufacturing.
-
Challenges and Future Directions
- Scalability: While additive manufacturing has made significant strides, challenges remain in scaling up the technology for mass production, particularly in terms of speed, consistency, and cost.
- Sustainability: As with any manufacturing technology, there are environmental concerns associated with rapid prototyping, particularly in terms of material waste and energy consumption. Ongoing research is focused on developing more sustainable materials and processes.
- Innovation and Integration: The future of rapid prototyping lies in its continued integration with other advanced manufacturing technologies, such as robotics, artificial intelligence, and the Internet of Things (IoT). These synergies are expected to lead to even more efficient, flexible, and intelligent manufacturing systems.
Conclusion
Rapid prototyping has come a long way since its inception in the 1980s. What began as a novel way to quickly produce physical models has evolved into a cornerstone of modern manufacturing and design. As the technology continues to advance, it promises to further revolutionize the way we create, test, and produce everything from everyday objects to complex, high-performance systems.
Reprint Statement: If there are no special instructions, all articles on this site are original. Please indicate the source for reprinting:https://www.cncmachiningptj.com/,thanks!
3, 4 and 5-axis precision CNC machining services for aluminum machining, beryllium, carbon steel, magnesium, titanium machining, Inconel, platinum, superalloy, acetal, polycarbonate, fiberglass, graphite and wood. Capable of machining parts up to 98 in. turning dia. and +/-0.001 in. straightness tolerance. Processes include milling, turning, drilling, boring, threading, tapping, forming, knurling, counterboring, countersinking, reaming and laser cutting. Secondary services such as assembly, centerless grinding, heat treating, plating and welding. Prototype and low to high volume production offered with maximum 50,000 units. Suitable for fluid power, pneumatics, hydraulics and valve applications. Serves the aerospace, aircraft, military, medical and defense industries.Cnc machining china shop will strategize with you to provide the most cost-effective services to help you reach your target,Welcome to Contact us ( sales@pintejin.com ) directly for your new project.
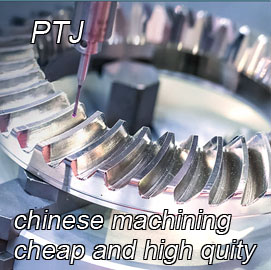
- 5 Axis Machining
- Cnc Milling
- Cnc Turning
- Machining Industries
- Machining Process
- Surface Treatment
- Metal Machining
- Plastic Machining
- Powder Metallurgy Mold
- Die Casting
- Parts Gallery
- Auto Metal Parts
- Machinery Parts
- LED Heatsink
- Building Parts
- Mobile Parts
- Medical Parts
- Electronic Parts
- Tailored Machining
- Bicycle Parts
- Aluminum Machining
- Titanium Machining
- Stainless Steel Machining
- Copper Machining
- Brass Machining
- Super Alloy Machining
- Peek Machining
- UHMW Machining
- Unilate Machining
- PA6 Machining
- PPS Machining
- Teflon Machining
- Inconel Machining
- Tool Steel Machining
- More Material