What is G96 In CNC
G96 is a G-code command used in CNC (Computer Numerical Control) machining, specifically for lathe operations. G-codes are a fundamental aspect of CNC programming, where they act as commands that control various machine functions. G96 is known as the "constant surface speed" command and plays a crucial role in optimizing cutting conditions during the machining process.
In this article, we will explore the concept of G96, its role in CNC programming, its applications, and the technical intricacies associated with it. We will also discuss the broader context of G-codes, CNC machining, and how G96 interacts with other commands to produce efficient and precise machining operations.
Overview of CNC Machining
CNC machining is a manufacturing process that involves the use of computers to control machine tools. The origins of CNC can be traced back to the 1940s and 1950s when numerical control (NC) technology was first developed. Early CNC systems used punched tape to control the movements of machine tools, which evolved into the more advanced, computer-controlled systems we use today.
Importance of G-Codes
G-codes, or preparatory codes, are essential in CNC programming as they define the specific operations that the machine must perform. These codes control everything from the movement of the machine's axes to the speed of the cutting tool, coolant flow, and other essential functions. G-codes are standardized across the industry, though some variations exist depending on the machine manufacturer.
The Function of G96 in CNC Programming
Definition of G96
G96 is a G-code command used to maintain a constant surface speed (CSS) during machining operations, primarily in turning operations on a lathe. Surface speed refers to the speed at which the cutting tool engages with the material being machined. In many cases, this speed needs to be consistent to ensure optimal cutting conditions, tool life, and surface finish.
How G96 Works
When G96 is activated in a CNC program, the machine's spindle speed automatically adjusts to maintain a constant surface speed as the diameter of the workpiece changes. This is particularly useful in turning operations, where the workpiece is rotated and the cutting tool moves along its surface. As the tool moves closer to or farther from the center of the workpiece, the spindle speed changes to maintain the desired surface speed.
For example, when the cutting tool is working on a larger diameter, the spindle speed decreases to maintain the constant surface speed. Conversely, when the tool moves to a smaller diameter, the spindle speed increases.
Applications of G96 in Machining
Turning Operations
G96 is predominantly used in turning operations on a lathe, where it ensures that the cutting conditions remain optimal throughout the machining process. By maintaining a constant surface speed, G96 helps prevent issues such as excessive tool wear, poor surface finish, and inefficient machining.
Impact on Tool Life
One of the significant benefits of using G96 is its positive impact on tool life. Consistent surface speed reduces the thermal and mechanical stress on the cutting tool, leading to longer tool life and fewer tool changes. This, in turn, reduces downtime and increases productivity.
Surface Finish Quality
Maintaining a constant surface speed is crucial for achieving a high-quality surface finish. Inconsistent speeds can lead to variations in the material removal rate, resulting in an uneven surface finish. G96 ensures that the cutting tool removes material at a consistent rate, producing a smooth and even surface.
Technical Aspects of G96
Programming Syntax
In a typical CNC program, G96 is followed by an "S" code, which specifies the desired surface speed in units of meters per minute (m/min) or feet per minute (ft/min). The command might look something like this:
G96 S150
In this example, the machine is instructed to maintain a constant surface speed of 150 m/min.
Interactions with Other G-Codes
G96 often works in conjunction with other G-codes, such as G97, which is used to cancel the constant surface speed mode and revert to a constant spindle speed mode. For instance, when machining a workpiece, the programmer might use G96 for the roughing pass to maintain optimal cutting conditions, then switch to G97 for finishing operations where a specific spindle speed is required.
G96 S150 ... G97 S1000
This example shows a transition from a constant surface speed of 150 m/min to a fixed spindle speed of 1000 RPM.
Machine Control Parameters
When using G96, it is crucial to set the appropriate control parameters on the CNC machine, such as the maximum spindle speed limit (often defined by the G50 command). Without setting a spindle speed limit, the machine might attempt to reach unsafe speeds as it tries to maintain the constant surface speed, particularly when machining small diameters.
This command limits the spindle speed to a maximum of 2000 RPM, ensuring safe operation while using G96.
Advantages and Disadvantages of G96
Advantages
- Improved Tool Life: By maintaining a constant surface speed, G96 reduces thermal and mechanical stress on the cutting tool, extending its life.
- Better Surface Finish: Consistent cutting conditions lead to a higher-quality surface finish, reducing the need for additional finishing operations.
- Increased Efficiency: G96 allows for faster material removal rates in roughing operations while maintaining optimal cutting conditions.
Disadvantages
- Complex Programming: Using G96 requires careful planning and understanding of the machining process, which can complicate the programming task.
- Machine Wear: Frequent changes in spindle speed can lead to increased wear on the machine's spindle drive system.
- Safety Concerns: Without proper spindle speed limits, G96 can cause the machine to reach dangerously high speeds, posing a safety risk.
Practical Considerations for Using G96
Material Considerations
Different materials require different surface speeds to achieve optimal machining results. When using G96, it is essential to choose a surface speed that matches the material being machined. For example, softer materials like aluminum might require a higher surface speed than harder materials like steel.
Tool Geometry
The geometry of the cutting tool also plays a role in determining the appropriate surface speed. Tools with sharper cutting edges might perform better at higher surface speeds, while more robust tools might require lower speeds to prevent excessive wear.
Workpiece Geometry
The shape and size of the workpiece also influence the effectiveness of G96. For workpieces with varying diameters, G96 is particularly useful in maintaining consistent cutting conditions across different sections of the part.
G96 in Advanced CNC Applications
Multi-Axis Machining
In multi-axis CNC machining, G96 can be used in conjunction with other advanced G-codes to control cutting conditions across complex geometries. This requires sophisticated programming and a deep understanding of the machine's capabilities.
Adaptive Machining
Adaptive machining techniques, which involve real-time adjustments to cutting conditions based on feedback from sensors and other monitoring systems, can benefit from the use of G96. By maintaining a constant surface speed, G96 can help optimize the machining process, even as conditions change during the operation.
Automation and Industry 4.0
In the context of Industry 4.0, where automation and data integration are key, G96 can be integrated into automated machining processes to enhance efficiency and precision. By using real-time data to adjust cutting conditions, CNC machines can achieve higher levels of productivity and quality.
Common Mistakes and Troubleshooting
Incorrect Spindle Speed Limits
One of the most common mistakes when using G96 is failing to set an appropriate spindle speed limit. This can result in the machine attempting to reach unsafe speeds, leading to potential damage or accidents.
Inconsistent Material Properties
If the material being machined has inconsistent properties, such as varying hardness or surface defects, G96 might not perform as expected. In such cases, additional adjustments to the machining parameters may be necessary.
Tool Wear and Breakage
Excessive tool wear or breakage can occur if the surface speed is set too high for the material and tool combination. Regular monitoring and maintenance of tools are essential to prevent such issues.
Case Studies and Real-World Examples
Automotive Industry
In the automotive industry, G96 is commonly used in the machining of engine components, where consistent surface speed is critical for achieving high-quality finishes and maintaining tight tolerances. For example, when machining crankshafts, G96 ensures that the cutting tool maintains optimal engagement with the material, resulting in a precise and smooth finish.
Aerospace Industry
The aerospace industry also relies heavily on G96, particularly in the machining of turbine blades and other critical components. These parts often have complex geometries and require high levels of precision. By using G96, manufacturers can achieve the necessary surface finishes and dimensional accuracy while minimizing tool wear and maximizing efficiency.
Conclusion
G96 is a powerful and versatile G-code command in CNC programming, particularly in lathe operations. By maintaining a constant surface speed, it enhances tool life, improves surface finish quality, and increases overall machining efficiency. However, its effective use requires careful planning, appropriate machine settings, and a deep understanding of the machining process.
As CNC technology continues to evolve, the role of G96 in optimizing machining operations is likely to grow, particularly in advanced manufacturing applications where precision and efficiency are paramount. Whether in the automotive, aerospace, or general manufacturing industries, G96 remains a critical tool for achieving high-quality results in CNC machining.
Reprint Statement: If there are no special instructions, all articles on this site are original. Please indicate the source for reprinting:https://www.cncmachiningptj.com/,thanks!
3, 4 and 5-axis precision CNC machining services for aluminum machining, beryllium, carbon steel, magnesium, titanium machining, Inconel, platinum, superalloy, acetal, polycarbonate, fiberglass, graphite and wood. Capable of machining parts up to 98 in. turning dia. and +/-0.001 in. straightness tolerance. Processes include milling, turning, drilling, boring, threading, tapping, forming, knurling, counterboring, countersinking, reaming and laser cutting. Secondary services such as assembly, centerless grinding, heat treating, plating and welding. Prototype and low to high volume production offered with maximum 50,000 units. Suitable for fluid power, pneumatics, hydraulics and valve applications. Serves the aerospace, aircraft, military, medical and defense industries.PTJ will strategize with you to provide the most cost-effective services to help you reach your target,Welcome to Contact us ( sales@pintejin.com ) directly for your new project.
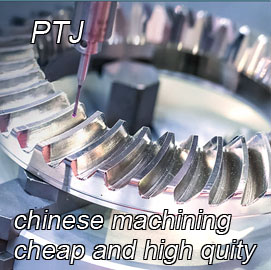
- 5 Axis Machining
- Cnc Milling
- Cnc Turning
- Machining Industries
- Machining Process
- Surface Treatment
- Metal Machining
- Plastic Machining
- Powder Metallurgy Mold
- Die Casting
- Parts Gallery
- Auto Metal Parts
- Machinery Parts
- LED Heatsink
- Building Parts
- Mobile Parts
- Medical Parts
- Electronic Parts
- Tailored Machining
- Bicycle Parts
- Aluminum Machining
- Titanium Machining
- Stainless Steel Machining
- Copper Machining
- Brass Machining
- Super Alloy Machining
- Peek Machining
- UHMW Machining
- Unilate Machining
- PA6 Machining
- PPS Machining
- Teflon Machining
- Inconel Machining
- Tool Steel Machining
- More Material