Dry Run in CNC Machining
A dry run in CNC (Computer Numerical Control) machining is a preliminary process where the machine runs a program without any material or with the cutting tool raised to avoid actual contact with the material. This process is critical in verifying the accuracy of the program and ensuring that the machine will operate as expected when the final production begins. It is an essential step in the CNC machining process, aimed at preventing errors that could result in damage to the machine, the workpiece, or the tooling.
Overview of CNC Machining
CNC machining is a manufacturing process in which pre-programmed computer software dictates the movement of factory tools and machinery. The process can control a range of complex machinery, from grinders and lathes to mills and routers. With CNC machining, three-dimensional cutting tasks can be accomplished in a single set of prompts.
Importance of Dry Runs
A dry run is one of the key preparatory steps in CNC machining. It serves multiple purposes:
-
Verification of the Program: Dry runs help in verifying the G-code and ensuring that the machine will execute the program correctly without any errors.
-
Avoidance of Collisions: By simulating the machining process without material, dry runs help detect potential collisions between the tool, workpiece, or machine components, thereby preventing costly damages.
-
Toolpath Validation: The dry run allows operators to verify that the tool paths are correct, ensuring that the tool moves in the intended trajectory.
-
Cycle Time Estimation: It provides an estimate of the actual machining time, which is crucial for planning and scheduling in a production environment.
Procedure of Conducting a Dry Run
The procedure for conducting a dry run varies depending on the machine and software, but generally involves the following steps:
-
Loading the Program: The G-code program is loaded into the CNC machine's controller.
-
Setting Up the Machine: The machine is set up with the appropriate tooling and fixtures, but without any workpiece material. Alternatively, the tool may be positioned above the workpiece to avoid actual cutting.
-
Running the Program: The program is run at a reduced feed rate or with the tool positioned away from the material to simulate the machining process.
-
Monitoring the Run: Operators carefully monitor the machine to identify any errors in the program, unexpected movements, or potential collisions.
-
Adjustments: Based on the observations during the dry run, adjustments may be made to the program or machine setup to correct any issues.
Common Errors Detected by Dry Runs
Dry runs are particularly effective at identifying common errors in CNC machining, including:
-
Incorrect Tool Paths: Misprogrammed tool paths that could result in the tool cutting the wrong area or colliding with the fixture.
-
Wrong Tool Selection: Errors in tool selection, where the wrong tool is used for a particular operation, can be detected.
-
Feed and Speed Errors: Incorrect feed rates or spindle speeds that could result in suboptimal machining or tool damage.
-
Coordinate System Errors: Mistakes in the machine's coordinate system that could lead to the workpiece being machined in the wrong location.
Software and Simulation Tools for Dry Runs
Advanced CNC machining software often includes simulation tools that can perform a virtual dry run before the actual machine run. These simulations provide a visual representation of the tool paths and machine movements, allowing operators to detect errors without physically running the machine.
Role of Operators in Dry Runs
While software simulations are increasingly sophisticated, the role of the operator in conducting a dry run remains critical. Experienced operators can identify subtle issues that may not be apparent in a simulation, such as unusual machine vibrations or sounds that indicate a potential problem.
Challenges and Limitations
Despite its benefits, the dry run process is not without challenges:
-
Time-Consuming: Dry runs can be time-consuming, particularly for complex parts with long machining cycles.
-
Not Foolproof: While effective, dry runs cannot detect all potential issues, particularly those related to material properties or tool wear.
-
Requires Expertise: Conducting a dry run effectively requires a skilled operator who understands both the machine and the program.
Conclusion
In conclusion, a dry run in CNC machining is an essential step in ensuring the success of the machining process. By simulating the operation without material, operators can detect and correct errors before actual production begins, thereby reducing the risk of damage to the machine, tooling, or workpiece. While the process can be time-consuming, its benefits in terms of preventing costly mistakes make it an invaluable part of CNC machining.
Reprint Statement: If there are no special instructions, all articles on this site are original. Please indicate the source for reprinting:https://www.cncmachiningptj.com/,thanks!
3, 4 and 5-axis precision CNC machining services for aluminum machining, beryllium, carbon steel, magnesium, titanium machining, Inconel, platinum, superalloy, acetal, polycarbonate, fiberglass, graphite and wood. Capable of machining parts up to 98 in. turning dia. and +/-0.001 in. straightness tolerance. Processes include milling, turning, drilling, boring, threading, tapping, forming, knurling, counterboring, countersinking, reaming and laser cutting. Secondary services such as assembly, centerless grinding, heat treating, plating and welding. Prototype and low to high volume production offered with maximum 50,000 units. Suitable for fluid power, pneumatics, hydraulics and valve applications. Serves the aerospace, aircraft, military, medical and defense industries.PTJ will strategize with you to provide the most cost-effective services to help you reach your target,Welcome to Contact us ( sales@pintejin.com ) directly for your new project.
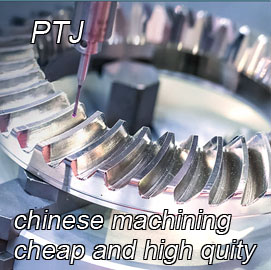
- 5 Axis Machining
- Cnc Milling
- Cnc Turning
- Machining Industries
- Machining Process
- Surface Treatment
- Metal Machining
- Plastic Machining
- Powder Metallurgy Mold
- Die Casting
- Parts Gallery
- Auto Metal Parts
- Machinery Parts
- LED Heatsink
- Building Parts
- Mobile Parts
- Medical Parts
- Electronic Parts
- Tailored Machining
- Bicycle Parts
- Aluminum Machining
- Titanium Machining
- Stainless Steel Machining
- Copper Machining
- Brass Machining
- Super Alloy Machining
- Peek Machining
- UHMW Machining
- Unilate Machining
- PA6 Machining
- PPS Machining
- Teflon Machining
- Inconel Machining
- Tool Steel Machining
- More Material