Electricity Consumption of CNC Machines
Computer Numerical Control (CNC) machines are vital in modern manufacturing, offering precision, efficiency, and the ability to produce complex parts with high repeatability. These machines are utilized across various industries, including aerospace, automotive, electronics, and metalworking. Given their widespread use, understanding the electricity consumption of CNC machines is essential for cost management, environmental sustainability, and energy efficiency. This article provides a detailed analysis of the electricity consumption of CNC machines, examining factors such as machine types, operational parameters, energy-saving practices, and more.
Overview of CNC Machines
CNC machines are automated tools that control machining processes through programmed commands. Unlike manual machines, which require direct human intervention, CNC machines operate autonomously based on coded instructions. These instructions guide the machine's movements, spindle speed, feed rate, and other parameters to produce precise parts from raw materials.
Types of CNC Machines
CNC machines come in various forms, each designed for specific applications. The most common types include:
- CNC Milling Machines: Used for cutting and shaping materials by removing material from a workpiece with a rotating cutter.
- CNC Lathes: Used for shaping materials by rotating the workpiece against a stationary cutting tool.
- CNC Routers: Used for cutting and shaping wood, plastic, and other soft materials.
- CNC Plasma Cutters: Used for cutting metal sheets with a plasma torch.
- CNC Laser Cutters: Used for cutting materials with a focused laser beam.
- CNC Electric Discharge Machines (EDM): Used for machining hard metals by eroding material using electrical discharges.
Importance of Energy Consumption in CNC Operations
The electricity consumption of CNC machines is a critical factor in the overall operational costs of manufacturing facilities. Understanding and managing this consumption is essential for several reasons:
- Cost Efficiency: Electricity is a significant operating expense in manufacturing. Reducing energy consumption can lead to substantial cost savings.
- Environmental Impact: Lowering electricity usage reduces the carbon footprint of manufacturing operations, contributing to environmental sustainability.
- Regulatory Compliance: Many regions have regulations and incentives aimed at reducing industrial energy consumption. Efficient CNC operations can help companies comply with these regulations.
Factors Affecting Electricity Consumption in CNC Machines
The type and size of a CNC machine significantly influence its electricity consumption. Larger machines with more powerful motors typically consume more electricity. For example, a CNC milling machine with a high-power spindle motor will use more electricity than a smaller, less powerful machine.
- Spindle Motor Power: The spindle motor's power rating, usually measured in kilowatts (kW), directly affects energy consumption. High-power motors consume more electricity, especially during heavy-duty operations.
- Axis Motors: CNC machines have multiple axes (typically three to five), each powered by a motor. The number of axes and the power rating of these motors contribute to overall electricity usage.
- Machine Size: Larger machines require more energy to move components and maintain stability, increasing electricity consumption.
Operational Parameters
The way a CNC machine is operated also impacts its electricity consumption. Key operational parameters include:
- Spindle Speed: Higher spindle speeds require more power, increasing electricity usage. However, optimizing spindle speed for specific tasks can improve efficiency.
- Feed Rate: The speed at which the cutting tool moves through the material affects energy consumption. Higher feed rates can increase power demand but may reduce overall machining time.
- Cutting Depth: Deeper cuts require more power, leading to higher electricity consumption. Optimizing cutting depth can reduce energy usage while maintaining productivity.
- Tool Path: Efficient tool paths reduce unnecessary movements, lowering electricity consumption.
Usage Patterns
The frequency and duration of CNC machine operation also determine electricity consumption. Continuous operation at high power levels consumes more electricity than intermittent or low-power usage.
- Duty Cycle: The duty cycle refers to the proportion of time a machine is actively cutting versus idle. Machines with high duty cycles consume more electricity.
- Idle Time: CNC machines consume electricity even when idle. Reducing idle time through efficient scheduling and programming can lower overall energy usage.
- Load Variability: Machines operating under varying loads may experience fluctuations in electricity consumption. Consistent loading helps in managing energy usage more effectively.
Machine Age and Condition
Older CNC machines may consume more electricity due to less efficient motors, worn components, or outdated control systems. Regular maintenance and timely upgrades can mitigate these effects.
- Maintenance Practices: Proper maintenance, including lubrication, alignment, and calibration, ensures that CNC machines operate efficiently, reducing electricity consumption.
- Upgrades: Retrofitting older machines with energy-efficient components or advanced control systems can significantly lower electricity usage.
Energy Efficiency Measures
Implementing energy-efficient practices and technologies can reduce the electricity consumption of CNC machines.
- Variable Frequency Drives (VFDs): VFDs control motor speed and torque, reducing energy consumption during low-load operations.
- Energy-Efficient Motors: Upgrading to high-efficiency motors reduces electricity consumption without compromising performance.
- Software Optimization: Advanced CNC software can optimize tool paths, feed rates, and other parameters to minimize energy usage.
- Energy Management Systems: These systems monitor and manage electricity consumption, allowing operators to identify inefficiencies and implement corrective measures.
Case Studies of CNC Electricity Consumption
Several case studies illustrate the electricity consumption of CNC machines in different industrial settings.
- Aerospace Manufacturing: CNC machines in the aerospace industry often operate at high power levels due to the precision required and the hardness of materials used. These machines consume significant electricity, but energy-efficient practices can reduce costs.
- Automotive Manufacturing: In the automotive sector, CNC machines are used for machining engine components, body parts, and other critical elements. Optimizing operational parameters can lead to substantial energy savings.
- Metalworking Industry: CNC machines in metalworking facilities vary in size and power, leading to different levels of electricity consumption. Case studies show that implementing energy-efficient technologies can reduce energy usage by up to 30%.
Energy-Saving Initiatives
Some manufacturers have successfully implemented energy-saving initiatives to reduce the electricity consumption of CNC machines.
- Retrofitting with VFDs: A metalworking company retrofitted its CNC machines with VFDs, resulting in a 20% reduction in electricity consumption.
- Optimizing Tool Paths: An automotive parts manufacturer optimized tool paths using advanced software, reducing machining time and energy usage by 15%.
- Upgrading to Energy-Efficient Motors: An aerospace manufacturer replaced older motors with energy-efficient models, cutting electricity consumption by 25%.
Environmental and Economic Impacts
Reducing the electricity consumption of CNC machines contributes to lowering the carbon footprint of manufacturing operations. By consuming less energy, facilities can reduce their greenhouse gas emissions, contributing to global efforts to combat climate change.
- Energy Source Considerations: The environmental impact of electricity consumption also depends on the energy source. For example, electricity from renewable sources has a lower carbon footprint than that from fossil fuels. Manufacturers can further reduce their carbon footprint by sourcing electricity from renewable providers.
Cost Savings
Energy-efficient CNC operations lead to significant cost savings. Lower electricity consumption reduces operational expenses, allowing manufacturers to allocate resources to other areas of their business.
- Return on Investment (ROI): The initial investment in energy-efficient technologies, such as VFDs or energy-efficient motors, often pays off quickly through reduced electricity costs. Manufacturers can calculate ROI to assess the financial benefits of such investments.
Regulatory Compliance and Incentives
Many regions have regulations aimed at reducing industrial energy consumption. Compliance with these regulations is essential for avoiding penalties and taking advantage of incentives.
- Energy Efficiency Standards: Some countries have established energy efficiency standards for industrial equipment, including CNC machines. Manufacturers must ensure that their machines meet these standards to avoid fines and qualify for incentives.
- Incentive Programs: Governments and utility companies may offer incentives, such as tax credits or rebates, for implementing energy-efficient technologies. Manufacturers can leverage these programs to offset the costs of upgrading their CNC machines.
Future Trends in CNC Energy Efficiency
The future of CNC machine energy efficiency lies in continued technological advancements. Emerging technologies have the potential to significantly reduce electricity consumption in CNC operations.
- Smart CNC Machines: The integration of artificial intelligence (AI) and the Internet of Things (IoT) in CNC machines can optimize energy consumption by adjusting operational parameters in real-time based on sensor data.
- Advanced Materials: The development of lighter, stronger materials for CNC machine components can reduce the energy required for machining, further lowering electricity consumption.
- Energy Harvesting: Research is ongoing into energy harvesting technologies that could capture and reuse energy generated during CNC operations, reducing overall electricity usage.
Industry Best Practices
As awareness of energy efficiency grows, industry best practices are evolving to include more energy-conscious CNC operations.
- Energy Audits: Regular energy audits help manufacturers identify areas where CNC machines consume excessive electricity, enabling targeted improvements.
- Operator Training: Training CNC machine operators on energy-efficient practices can lead to significant reductions in electricity consumption.
- Sustainable Manufacturing Initiatives: Many manufacturers are adopting broader sustainable manufacturing initiatives that include energy-efficient CNC operations as a key component.
Conclusion
The electricity consumption of CNC machines is a critical aspect of modern manufacturing that impacts both operational costs and environmental sustainability. By understanding the factors that influence energy usage, implementing energy-efficient technologies, and adopting best practices, manufacturers can significantly reduce their electricity consumption. This not only leads to cost savings but also contributes to global efforts to reduce greenhouse gas emissions and combat climate change. As technology continues to advance, the future holds even greater potential for improving the energy efficiency of CNC machines, making them an integral part of sustainable manufacturing.
Reprint Statement: If there are no special instructions, all articles on this site are original. Please indicate the source for reprinting:https://www.cncmachiningptj.com/,thanks!
3, 4 and 5-axis precision CNC machining services for aluminum machining, beryllium, carbon steel, magnesium, titanium machining, Inconel, platinum, superalloy, acetal, polycarbonate, fiberglass, graphite and wood. Capable of machining parts up to 98 in. turning dia. and +/-0.001 in. straightness tolerance. Processes include milling, turning, drilling, boring, threading, tapping, forming, knurling, counterboring, countersinking, reaming and laser cutting. Secondary services such as assembly, centerless grinding, heat treating, plating and welding. Prototype and low to high volume production offered with maximum 50,000 units. Suitable for fluid power, pneumatics, hydraulics and valve applications. Serves the aerospace, aircraft, military, medical and defense industries.PTJ will strategize with you to provide the most cost-effective services to help you reach your target,Welcome to Contact us ( sales@pintejin.com ) directly for your new project.
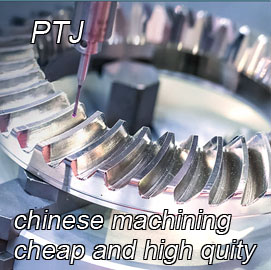
- 5 Axis Machining
- Cnc Milling
- Cnc Turning
- Machining Industries
- Machining Process
- Surface Treatment
- Metal Machining
- Plastic Machining
- Powder Metallurgy Mold
- Die Casting
- Parts Gallery
- Auto Metal Parts
- Machinery Parts
- LED Heatsink
- Building Parts
- Mobile Parts
- Medical Parts
- Electronic Parts
- Tailored Machining
- Bicycle Parts
- Aluminum Machining
- Titanium Machining
- Stainless Steel Machining
- Copper Machining
- Brass Machining
- Super Alloy Machining
- Peek Machining
- UHMW Machining
- Unilate Machining
- PA6 Machining
- PPS Machining
- Teflon Machining
- Inconel Machining
- Tool Steel Machining
- More Material