How To Scallop Board Edge with CNC Router
Scalloping board edges is a woodworking technique that adds aesthetic appeal and structural detail to wooden boards. The use of CNC routers for scalloping has become increasingly popular due to the precision and repeatability they offer. This article explores the process of scalloping board edges using a CNC router, providing a detailed overview of the tools, techniques, and considerations involved.
History of Scalloping in Woodworking
Scalloping, a decorative edge treatment, has been used in woodworking for centuries. Early woodworkers employed hand tools such as chisels, gouges, and planes to create scalloped edges. These manual techniques required a high level of skill and were often used in fine furniture and cabinetry.
Evolution of Scalloping Techniques
With the advent of power tools in the 20th century, the process of scalloping became more accessible. Routers and specialized bits allowed woodworkers to create scalloped edges more efficiently. However, it was the introduction of CNC (Computer Numerical Control) technology that revolutionized the practice, enabling precise and consistent scalloping on an industrial scale.
Understanding CNC Routers
What is a CNC Router?
A CNC router is a computer-controlled cutting machine used in woodworking, metalworking, and other industries. It operates by following programmed instructions to carve, cut, or shape materials. CNC routers are capable of performing complex tasks with high precision, making them ideal for detailed work such as scalloping.
Components of a CNC Router
- Spindle: The rotating part of the CNC router that holds the cutting tool. The spindle's speed and power are critical factors in determining the quality of the cut.
- Cutting Tools: CNC routers use various cutting tools, including end mills, ball nose bits, and specialized scalloping bits. The choice of tool depends on the desired scallop profile and material.
- Control System: The control system interprets the design files and converts them into machine movements. This system includes the CNC software, which allows users to create and modify designs.
Types of CNC Routers
CNC routers come in various sizes and configurations, from small desktop models to large industrial machines. The choice of router depends on the scale of the project and the type of materials being used.
Materials Suitable for Scalloping
Types of Wood
- Hardwoods: Hardwoods such as oak, maple, and cherry are commonly used for scalloping due to their strength and fine grain. They provide a smooth finish and are less prone to chipping.
- Softwoods: Softwoods like pine and cedar are also used, especially for decorative purposes. However, they may require more careful handling to avoid tear-out.
- Engineered Wood: Plywood, MDF, and other engineered wood products can be scalloped, though they may produce more dust and require different cutting speeds.
Non-Wood Materials
CNC routers can also scallop materials such as plastics, composites, and even metals. The process and tools used will vary depending on the material's properties.
Designing Scalloped Edges
Scallop Profiles and Styles
Scallop profiles can range from simple rounded curves to intricate patterns. Common styles include:
- Convex Scallops: Outward-curving scallops that create a rounded edge.
- Concave Scallops: Inward-curving scallops that produce a hollowed effect.
- Wave Patterns: A series of connected scallops that create a flowing, wave-like appearance.
Software for Design
Several software programs are available for designing scalloped edges, including:
- CAD (Computer-Aided Design) Software: Programs like AutoCAD and SolidWorks allow users to create precise 2D and 3D models of the scalloped edge.
- CAM (Computer-Aided Manufacturing) Software: CAM software, such as VCarve and Fusion 360, converts the CAD design into toolpaths that the CNC router can follow.
Creating Toolpaths for Scalloping
Toolpaths are the routes the CNC router's cutting tool will follow to create the scallop. These are carefully planned to ensure smooth transitions and prevent damage to the material.
Preparing for Scalloping
Material Preparation
Before scalloping, the material must be properly prepared. This includes:
- Surfacing: Ensuring the board's surface is flat and even.
- Securing: Clamping the material securely to prevent movement during cutting.
- Measuring and Marking: Accurate measurements and markings are essential for aligning the scallop design with the board.
Tool Selection and Setup
Choosing the right tool is crucial for achieving the desired scallop effect. Factors to consider include:
- Tool Diameter: The size of the tool affects the depth and width of the scallop.
- Flute Design: The number and shape of flutes (cutting edges) impact the quality of the cut.
- Tool Material: Carbide-tipped tools are preferred for their durability and precision.
CNC Router Setup
Setting up the CNC router involves:
- Mounting the Tool: Securely attaching the cutting tool to the spindle.
- Setting the Zero Point: Establishing the starting point for the toolpath.
- Configuring the Speed and Feed Rates: Adjusting the spindle speed and feed rate based on the material and tool.
The Scalloping Process
Step-by-Step Guide to Scalloping
- Load the Design File: Import the scallop design into the CNC software.
- Simulate the Toolpath: Run a simulation to verify the toolpath and make any necessary adjustments.
- Start the CNC Router: Begin the scalloping process, monitoring the machine for any issues.
- Inspect the Scallop: After cutting, inspect the scalloped edge for smoothness and consistency.
- Final Adjustments: Make any required adjustments or refinements to the scallop.
Troubleshooting Common Issues
Common issues in scalloping with a CNC router include:
- Tear-Out: This occurs when the wood fibers tear rather than cut cleanly, often due to incorrect feed rates or dull tools.
- Inconsistent Scallops: Variations in scallop size or shape can result from improper toolpath planning or machine calibration.
- Burn Marks: Excessive heat from the cutting tool can cause burn marks on the wood, usually due to high spindle speed or slow feed rate.
Advanced Techniques in Scalloping
Multi-Axis Scalloping
Some CNC routers offer multi-axis capabilities, allowing for more complex scallop designs that include varying depths and angles.
Combining Scalloping with Other Techniques
Scalloping can be combined with other decorative techniques, such as inlay work or engraving, to create intricate designs.
Custom Tooling for Unique Scallops
Custom-designed tools can be created to produce unique scallop profiles that are not possible with standard bits.
Finishing Scalloped Edges
Sanding and Smoothing
After scalloping, the edges may require sanding to remove any tool marks or rough spots. This can be done manually or with specialized sanding tools.
Applying Finish
The finish applied to scalloped edges depends on the desired look and the type of wood used. Common finishes include:
- Stain: Enhances the wood grain and adds color.
- Varnish: Provides a protective, glossy finish.
- Oil: Penetrates the wood, giving it a natural look and feel.
Protecting the Scalloped Edge
To protect scalloped edges from damage, consider adding a protective coating or using edge banding.
Safety Considerations
Personal Protective Equipment (PPE)
When using a CNC router, it is essential to wear appropriate PPE, including safety glasses, hearing protection, and dust masks.
Machine Safety
Ensure that the CNC router is properly maintained and that all safety guards are in place. Regularly check for loose components and ensure the emergency stop button is functioning.
Safe Handling of Materials
Handle materials carefully to avoid injury from splinters or sharp edges, and use proper lifting techniques when dealing with heavy boards.
Case Studies and Examples
Industrial Applications
Scalloping is widely used in the production of high-end furniture, cabinetry, and architectural details. Examples include the creation of ornate moldings and decorative panels.
DIY Projects
Many hobbyists use CNC routers for scalloping in DIY projects, such as creating custom picture frames, shelves, and furniture.
Artistic Applications
Artists and designers use CNC routers to create intricate scalloped patterns in wood and other materials, often incorporating these designs into sculptures and installations.
Future Trends in Scalloping with CNC Routers
Advances in CNC Technology
As CNC technology continues to evolve, new features such as AI-driven design tools and improved multi-axis capabilities are likely to enhance the scalloping process.
Sustainable Woodworking Practices
The trend toward sustainability in woodworking includes the use of eco-friendly materials and practices. CNC routers can contribute to this by reducing material waste and increasing efficiency.
Integration with Digital Fabrication
The integration of CNC routers with other digital fabrication tools, such as 3D printers and laser cutters, offers new possibilities for complex and innovative designs.
Conclusion
Scalloping board edges with a CNC router is a versatile and precise method for adding decorative detail to woodworking projects. From the initial design to the finishing touches, each step of the process requires careful planning and execution. As technology advances, the possibilities for scalloping with CNC routers continue to expand, offering woodworkers new ways to express their creativity and craftsmanship.
Reprint Statement: If there are no special instructions, all articles on this site are original. Please indicate the source for reprinting:https://www.cncmachiningptj.com/,thanks!
3, 4 and 5-axis precision CNC machining services for aluminum machining, beryllium, carbon steel, magnesium, titanium machining, Inconel, platinum, superalloy, acetal, polycarbonate, fiberglass, graphite and wood. Capable of machining parts up to 98 in. turning dia. and +/-0.001 in. straightness tolerance. Processes include milling, turning, drilling, boring, threading, tapping, forming, knurling, counterboring, countersinking, reaming and laser cutting. Secondary services such as assembly, centerless grinding, heat treating, plating and welding. Prototype and low to high volume production offered with maximum 50,000 units. Suitable for fluid power, pneumatics, hydraulics and valve applications. Serves the aerospace, aircraft, military, medical and defense industries.PTJ will strategize with you to provide the most cost-effective services to help you reach your target,Welcome to Contact us ( sales@pintejin.com ) directly for your new project.
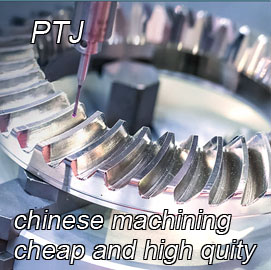
- 5 Axis Machining
- Cnc Milling
- Cnc Turning
- Machining Industries
- Machining Process
- Surface Treatment
- Metal Machining
- Plastic Machining
- Powder Metallurgy Mold
- Die Casting
- Parts Gallery
- Auto Metal Parts
- Machinery Parts
- LED Heatsink
- Building Parts
- Mobile Parts
- Medical Parts
- Electronic Parts
- Tailored Machining
- Bicycle Parts
- Aluminum Machining
- Titanium Machining
- Stainless Steel Machining
- Copper Machining
- Brass Machining
- Super Alloy Machining
- Peek Machining
- UHMW Machining
- Unilate Machining
- PA6 Machining
- PPS Machining
- Teflon Machining
- Inconel Machining
- Tool Steel Machining
- More Material