How to Deep Drawn Brass Products
Deep drawing is a pivotal metal forming process widely employed in the manufacturing of complex, hollow metal parts from sheet metal blanks. Brass, an alloy of copper and zinc, is particularly favored for deep drawing due to its excellent combination of strength, corrosion resistance, and workability. The process involves stretching the metal sheet into a desired shape through the application of mechanical force, usually by a punch and die system, making it an ideal method for producing a variety of intricate brass components. This article explores the intricate process of deep drawing brass, detailing its history, the material properties of brass, the equipment used, and the challenges encountered during the process, as well as discussing quality control measures and applications.
History of Deep Drawing in Metalworking
The art of metal forming dates back millennia, with early methods including simple hammering and forging techniques. As civilizations advanced, so did the complexity of metal forming processes. The technique of deep drawing began to take shape during the Industrial Revolution, with the advent of more sophisticated machinery and the need for mass production. Early deep drawing was primarily done with softer metals like lead and copper. However, as brass became more available and its properties were better understood, it became a material of choice for a wide range of applications, including the manufacture of ammunition casings during the late 19th and early 20th centuries. This period saw significant advancements in the precision and efficiency of deep drawing techniques, laying the groundwork for modern methods.
Material Properties of Brass Relevant to Deep Drawing
Brass is a versatile alloy, known for its ease of fabrication, excellent corrosion resistance, and good mechanical properties, which make it ideal for deep drawing. The composition of brass can vary, typically containing 60-70% copper and 30-40% zinc, with small amounts of other elements such as lead or tin added to improve machinability and corrosion resistance. The ductility and malleability of brass allow it to undergo significant deformation without cracking, essential characteristics for successful deep drawing. Furthermore, the alloy's thermal conductivity helps dissipate the heat generated during the drawing process, reducing the risk of defects.
Different types of brass alloys can be used in deep drawing, with each type offering unique properties. For example, Cartridge Brass (C26000) is widely used in deep drawing due to its excellent ductility and strength, making it ideal for producing deep-drawn parts with complex geometries.
Deep Drawing Process Overview
Deep drawing is a metal forming process in which a flat sheet of metal is progressively shaped into a three-dimensional part through a series of steps. The process typically begins with a blank, a flat piece of metal cut from a larger sheet. The blank is placed over a die cavity and held in place by a blank holder while a punch forces the metal into the die cavity, causing it to deform and take on the shape of the cavity.
The deep drawing process is distinguished from shallow drawing by the depth of the drawn part. In deep drawing, the depth of the drawn part exceeds its diameter, requiring multiple drawing stages, known as redrawing, to achieve the final depth without causing the material to fail. The process can produce a wide variety of shapes, including cylindrical, box-shaped, and more complex geometries, depending on the design of the die and punch.
Equipment and Tools Used in Deep Drawing
The equipment used in deep drawing is crucial to the success of the process. The primary machinery involved is the deep drawing press, which provides the necessary force to deform the metal. Presses can be mechanical or hydraulic, with hydraulic presses offering better control over the drawing process, making them ideal for deep drawing applications.
Dies and punches are the core tools used in deep drawing. The die is a hollow cavity that determines the shape of the final part, while the punch is a solid tool that pushes the metal into the die. Dies can be made from various materials, including tool steel and carbide, chosen for their hardness and wear resistance. The design of the die and punch is critical, as it must account for factors such as material thickness, draw depth, and the desired shape of the final part.
Lubrication plays a vital role in the deep drawing process, reducing friction between the metal and the tools, preventing tearing and wrinkling, and helping to achieve a smooth surface finish on the final product. The choice of lubricant depends on the material being drawn and the specific requirements of the process.
Stages in the Deep Drawing Process
-
Blanking: The first step in the deep drawing process is blanking, where the metal sheet is cut into the desired shape and size. The quality of the blank is crucial, as any defects or irregularities can lead to problems during the drawing process.
-
Drawing: In this stage, the blank is placed over the die and held in place by the blank holder. The punch then pushes the blank into the die cavity, causing the metal to flow and take on the shape of the cavity. The drawing stage may involve several passes, with the part being progressively drawn deeper into the die with each pass.
-
Redrawing: For parts that require a significant depth, redrawing may be necessary. Redrawing involves repeating the drawing process, with the part being placed into a second die and drawn deeper. This process may be repeated several times to achieve the final depth.
-
Trimming and Finishing: After the deep drawing process is complete, excess material may need to be trimmed from the part. This is typically done using a trimming die, which cuts away the excess material. The part may also undergo additional finishing processes, such as polishing or heat treatment, to improve its surface finish and mechanical properties.
Challenges in Deep Drawing Brass
Deep drawing brass presents several challenges, primarily related to the material's properties and the complexity of the process. Common issues include:
-
Wrinkling: Occurs when the material is compressed too much during the drawing process, causing it to fold and wrinkle. Proper control of the blank holder force and lubrication can help prevent wrinkling.
-
Tearing: Results from excessive tensile stress on the material, leading to cracks or tears. Material selection, lubrication, and careful control of the drawing process parameters are essential to avoid tearing.
-
Springback: After the drawing process, the material may partially return to its original shape due to its elastic properties. Springback can be minimized by optimizing the die and punch design and controlling the drawing process parameters.
Quality Control in Brass Deep Drawing
Quality control is a critical aspect of the deep drawing process, ensuring that the final product meets the required specifications. Several inspection techniques are used to assess the quality of deep-drawn brass parts, including:
-
Visual Inspection: Checking for surface defects such as scratches, wrinkles, and tears.
-
Dimensional Inspection: Ensuring that the part's dimensions meet the specified tolerances using tools such as calipers and coordinate measuring machines (CMMs).
-
Testing: Mechanical testing, such as tensile and hardness testing, can be performed to verify that the material's properties meet the required standards.
Various standards and certifications may apply to deep-drawn brass products, depending on the industry and application. Adherence to these standards is crucial for ensuring product quality and safety.
Applications of Deep Drawn Brass Products
Deep-drawn brass products are used in a wide range of industries due to their excellent mechanical properties and corrosion resistance. Some common applications include:
-
Electrical Components: Brass is widely used in electrical connectors, terminals, and other components due to its excellent conductivity and resistance to corrosion.
-
Automotive Industry: Deep-drawn brass parts are used in automotive components such as radiators, fuel system components, and decorative trim.
-
Ammunition Casings: Brass is the material of choice for ammunition casings due to its malleability, corrosion resistance, and ability to withstand the high pressures generated during firing.
-
Plumbing and HVAC: Brass fittings, valves, and other components used in plumbing and HVAC systems are often deep-drawn to achieve the desired shapes and sizes.
Environmental and Economic Considerations
The deep drawing process for brass is generally considered to be environmentally friendly, particularly when compared to other metal forming processes. Brass is highly recyclable, and scrap material generated during the deep drawing process can be reused, reducing waste and conserving resources.
From an economic perspective, deep drawing is a cost-effective method for producing large quantities of high-quality brass parts with consistent dimensions and properties. The ability to produce complex shapes in a single operation also reduces the need for additional machining and finishing processes, further lowering production costs.
Innovations in Deep Drawing Technology
Advancements in deep drawing technology have focused on improving the efficiency and precision of the process. Some recent innovations include:
-
Advanced Materials: The development of new brass alloys with improved properties, such as higher strength and better corrosion resistance, has expanded the range of applications for deep-drawn brass products.
-
Coatings and Surface Treatments: The use of advanced coatings and surface treatments on dies and punches has improved tool life and reduced friction during the drawing process, leading to better-quality parts and lower production costs.
-
Automation and Process Control: The integration of automation and advanced process control systems in deep drawing presses has improved the consistency and accuracy of the process, reducing the occurrence of defects and improving overall productivity.
Conclusion
Deep drawing is a highly efficient and versatile process for manufacturing complex brass components. The combination of brass's excellent mechanical properties, corrosion resistance, and workability makes it an ideal material for deep drawing. While the process presents certain challenges, such as wrinkling and tearing, careful control of the process parameters, material selection, and tool design can mitigate these issues. The resulting deep-drawn brass products are widely used across various industries, from automotive and electrical to plumbing and HVAC, offering a cost-effective and environmentally friendly solution for producing high-quality components.
Reprint Statement: If there are no special instructions, all articles on this site are original. Please indicate the source for reprinting:https://www.cncmachiningptj.com/,thanks!
3, 4 and 5-axis precision CNC machining services for aluminum machining, beryllium, carbon steel, magnesium, titanium machining, Inconel, platinum, superalloy, acetal, polycarbonate, fiberglass, graphite and wood. Capable of machining parts up to 98 in. turning dia. and +/-0.001 in. straightness tolerance. Processes include milling, turning, drilling, boring, threading, tapping, forming, knurling, counterboring, countersinking, reaming and laser cutting. Secondary services such as assembly, centerless grinding, heat treating, plating and welding. Prototype and low to high volume production offered with maximum 50,000 units. Suitable for fluid power, pneumatics, hydraulics and valve applications. Serves the aerospace, aircraft, military, medical and defense industries.PTJ will strategize with you to provide the most cost-effective services to help you reach your target,Welcome to Contact us ( sales@pintejin.com ) directly for your new project.
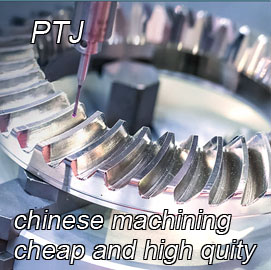
- 5 Axis Machining
- Cnc Milling
- Cnc Turning
- Machining Industries
- Machining Process
- Surface Treatment
- Metal Machining
- Plastic Machining
- Powder Metallurgy Mold
- Die Casting
- Parts Gallery
- Auto Metal Parts
- Machinery Parts
- LED Heatsink
- Building Parts
- Mobile Parts
- Medical Parts
- Electronic Parts
- Tailored Machining
- Bicycle Parts
- Aluminum Machining
- Titanium Machining
- Stainless Steel Machining
- Copper Machining
- Brass Machining
- Super Alloy Machining
- Peek Machining
- UHMW Machining
- Unilate Machining
- PA6 Machining
- PPS Machining
- Teflon Machining
- Inconel Machining
- Tool Steel Machining
- More Material