Zinc Die Casting vs. Zinc CNC Machining
Zinc is a versatile material widely used in manufacturing due to its excellent mechanical properties, including high strength, durability, and resistance to corrosion. Among the various manufacturing techniques employed to shape zinc into functional components, Zinc Die Casting and Zinc CNC Machining are two prominent methods. These processes cater to different industrial requirements and are chosen based on factors such as production volume, part complexity, material properties, and cost-effectiveness.
This article provides an in-depth comparison between Zinc Die Casting and Zinc CNC Machining, exploring their methodologies, advantages, limitations, and applications. Understanding these processes' nuances helps manufacturers and engineers select the most suitable method for their specific needs.
Historical Background
Zinc Die Casting
Zinc die casting has a long history dating back to the early 20th century. Initially developed to meet the demands of mass production, die casting became a popular method for producing intricate metal components with high precision and consistency. The process involves injecting molten zinc into a mold cavity under high pressure, allowing for rapid production of complex shapes with minimal post-processing.
The advent of modern die casting machines and the development of zinc alloys further enhanced the efficiency and quality of die-cast products. The automotive, electronics, and consumer goods industries are among the sectors that extensively use zinc die casting.
Zinc CNC Machining
Computer Numerical Control (CNC) Machining emerged later, in the mid-20th century, as a technological advancement over traditional machining methods. CNC machining uses computer-controlled tools to remove material from a solid block, or "workpiece," to create precise parts. The process is highly versatile, allowing for the production of both simple and complex geometries with tight tolerances.
While CNC machining can work with a variety of materials, zinc's machinability makes it a suitable candidate for this process. CNC machining is particularly valued for producing small to medium-sized production runs, prototypes, and customized components.
Technical Overview
Zinc Die Casting
Process Description: Zinc die casting involves injecting molten zinc alloy into a steel mold, known as a die, under high pressure. The mold cavity is designed to shape the molten metal into the desired form. Once the metal solidifies, the die opens, and the casting is ejected. The process can be repeated rapidly, making it ideal for high-volume production.
Key Elements:
- Die: The mold, typically made of hardened tool steel, is composed of two halves (the "fixed die" and the "moving die") that form the cavity.
- Molten Zinc Alloy: Common zinc alloys used in die casting include Zamak alloys (Zamak 3, Zamak 5, etc.), which are known for their excellent fluidity, strength, and ease of casting.
- Injection System: The molten zinc is injected into the die at pressures ranging from 1,500 to 25,000 psi, ensuring that the metal fills the mold cavity completely and replicates the mold's intricate details.
Advantages:
- High Production Rate: Zinc die casting is highly efficient, with cycle times often measured in seconds, making it suitable for mass production.
- Complex Geometries: The process can produce parts with complex shapes, thin walls, and fine details.
- Surface Finish: Die-cast parts typically have smooth surfaces, reducing the need for additional finishing.
- Material Efficiency: The process generates minimal waste, as excess metal can often be recycled and reused.
Limitations:
- Initial Cost: The cost of creating dies can be high, making the process less economical for low-volume production.
- Part Size Limitation: The size of the part is limited by the capacity of the die casting machine.
- Porosity: The high-pressure injection can cause porosity in the casting, which may affect the mechanical properties and require secondary operations to address.
Zinc CNC Machining
Process Description: Zinc CNC machining involves using computer-controlled tools to precisely remove material from a solid block (or workpiece) to achieve the desired shape. The process typically begins with a digital design, often created using Computer-Aided Design (CAD) software. The CAD model is then translated into machine code that controls the movement and operation of the machining tools.
Key Elements:
- Workpiece: The initial block of zinc from which material is removed.
- CNC Machine: The machine uses various tools (e.g., drills, lathes, mills) to cut, drill, or grind the workpiece into the desired form.
- Toolpath: The path followed by the cutting tools, which is precisely controlled by the CNC software to achieve the required dimensions and surface finish.
Advantages:
- Precision: CNC machining offers high precision and can achieve tight tolerances, making it ideal for components requiring exact dimensions.
- Flexibility: The process is versatile and can be used to produce a wide range of parts, from simple to highly complex geometries.
- No Need for Molds: CNC machining does not require molds, making it cost-effective for small production runs and prototypes.
- Material Versatility: CNC machining can work with various materials, including different grades of zinc and zinc alloys.
Limitations:
- Slower Production Rate: CNC machining is generally slower than die casting, especially for high-volume production.
- Material Waste: The subtractive nature of machining results in material waste, as excess material is removed from the workpiece.
- Cost: For large-scale production, the per-unit cost of CNC machining can be higher than that of die casting due to the slower production rate and material waste.
Comparison of Material Properties
Zinc Alloys Used in Die Casting
Zinc die casting typically uses alloys from the Zamak family, which are composed primarily of zinc, with small percentages of aluminum, magnesium, and copper. These alloys are known for their excellent fluidity, making them ideal for the die casting process.
- Zamak 3: The most commonly used zinc alloy in die casting, Zamak 3 offers a good balance of mechanical properties, including strength, ductility, and impact resistance.
- Zamak 5: This alloy has slightly higher copper content than Zamak 3, providing better strength and hardness but slightly lower ductility.
- Zamak 7: Similar to Zamak 3 but with lower magnesium content, Zamak 7 offers better fluidity and is used for more intricate castings.
Zinc Grades for CNC Machining
CNC machining of zinc typically uses high-purity zinc or specific zinc alloys optimized for machining. The choice of material depends on the required mechanical properties, such as strength, hardness, and corrosion resistance.
- High-Purity Zinc: Often used in applications requiring excellent corrosion resistance and machinability.
- Zinc-Aluminum Alloys: Alloys like ZA-12 or ZA-27 are used in applications requiring higher strength and wear resistance.
Production Efficiency and Economic Considerations
Production Volume
- Zinc Die Casting: Best suited for high-volume production due to its rapid cycle times and low per-unit cost at scale. The high initial cost of tooling (dies) is offset by the economies of scale achieved in large production runs.
- Zinc CNC Machining: More economical for low to medium production volumes, especially when the cost of tooling for die casting cannot be justified. CNC machining is also advantageous for producing prototypes or custom components.
Tooling and Setup Costs
- Zinc Die Casting: Involves significant initial costs related to the design and manufacture of the die. However, once the die is created, the marginal cost of producing additional parts is low.
- Zinc CNC Machining: Requires less upfront investment, as no molds or dies are needed. However, the per-unit cost remains higher due to the longer machining time and material waste.
Lead Time
- Zinc Die Casting: After the initial tooling is completed, die casting offers a short lead time for large production runs, as parts can be produced rapidly.
- Zinc CNC Machining: Generally has a longer lead time compared to die casting, especially for complex parts, but offers flexibility in producing small quantities quickly.
Quality Control and Precision
- Zinc Die Casting: The process is highly repeatable, ensuring consistent quality across large production runs. However, issues such as porosity may require additional quality control measures.
- Zinc CNC Machining: Offers exceptional precision and surface finish, making it suitable for applications where tight tolerances and high quality are critical.
Applications
Common Applications of Zinc Die Casting
- Automotive Components: Zinc die casting is widely used in the automotive industry for producing parts such as carburetors, fuel pumps, and structural components.
- Consumer Electronics: The process is employed to manufacture housings and internal components for electronic devices, where complex shapes and high-volume production are required.
- Hardware and Tools: Zinc die casting is used to produce various hardware items, including locks, gears, and handles, due to its strength and durability.
Common Applications of Zinc CNC Machining
- Prototypes and Custom Parts: CNC machining is frequently used to create prototypes and custom parts, allowing for design iterations and testing before mass production.
- Aerospace and Defense: Due to the high precision and quality required, CNC machining is commonly used in the aerospace and defense industries to produce components with tight tolerances.
- Medical Devices: The precision of CNC machining makes it suitable for manufacturing medical devices and instruments that require exact specifications and biocompatibility.
Environmental Impact
Zinc Die Casting
Zinc die casting is considered relatively environmentally friendly due to the recyclability of zinc alloys. The process generates minimal waste, as excess metal can be remelted and reused. However, the energy consumption associated with melting and injecting the metal can be significant, depending on the scale of production.
Zinc CNC Machining
CNC machining generates more waste material compared to die casting, as the process involves cutting away material from a larger block. However, this waste can often be recycled. The environmental impact of CNC machining also depends on the energy consumption of the machines and the coolant fluids used during the process.
Future Trends and Innovations
Advancements in Die Casting
- Hot Chamber Die Casting: Innovations in hot chamber die casting are improving the efficiency and quality of zinc castings. These advancements include better temperature control, improved mold materials, and automated systems that enhance production speed and consistency.
- Sustainable Practices: The die casting industry is increasingly adopting sustainable practices, such as using recycled materials and optimizing energy consumption to reduce the environmental impact.
Advancements in CNC Machining
- Automation and AI Integration: The integration of artificial intelligence and automation in CNC machining is leading to smarter, more efficient manufacturing processes. These technologies enable real-time monitoring, predictive maintenance, and optimized tool paths, reducing waste and improving precision.
- Hybrid Manufacturing: The combination of CNC machining with additive manufacturing (3D printing) is emerging as a trend, allowing for the production of complex parts that would be difficult or impossible to create with traditional subtractive methods alone.
Conclusion
Zinc Die Casting and Zinc CNC Machining are two distinct manufacturing processes, each with its own set of advantages and limitations. Die casting is well-suited for high-volume production of complex parts with consistent quality, while CNC machining excels in producing precise, customized components with tight tolerances.
The choice between these processes depends on various factors, including production volume, part complexity, material properties, and cost considerations. By understanding the strengths and limitations of each method, manufacturers can make informed decisions that align with their production goals and business objectives.
In the rapidly evolving field of manufacturing, both zinc die casting and CNC machining continue to play critical roles, supported by ongoing innovations that enhance their efficiency, sustainability, and precision.
Reprint Statement: If there are no special instructions, all articles on this site are original. Please indicate the source for reprinting:https://www.cncmachiningptj.com/,thanks!
3, 4 and 5-axis precision CNC machining services for aluminum machining, beryllium, carbon steel, magnesium, titanium machining, Inconel, platinum, superalloy, acetal, polycarbonate, fiberglass, graphite and wood. Capable of machining parts up to 98 in. turning dia. and +/-0.001 in. straightness tolerance. Processes include milling, turning, drilling, boring, threading, tapping, forming, knurling, counterboring, countersinking, reaming and laser cutting. Secondary services such as assembly, centerless grinding, heat treating, plating and welding. Prototype and low to high volume production offered with maximum 50,000 units. Suitable for fluid power, pneumatics, hydraulics and valve applications. Serves the aerospace, aircraft, military, medical and defense industries.PTJ will strategize with you to provide the most cost-effective services to help you reach your target,Welcome to Contact us ( sales@pintejin.com ) directly for your new project.
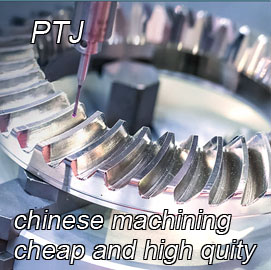
- 5 Axis Machining
- Cnc Milling
- Cnc Turning
- Machining Industries
- Machining Process
- Surface Treatment
- Metal Machining
- Plastic Machining
- Powder Metallurgy Mold
- Die Casting
- Parts Gallery
- Auto Metal Parts
- Machinery Parts
- LED Heatsink
- Building Parts
- Mobile Parts
- Medical Parts
- Electronic Parts
- Tailored Machining
- Bicycle Parts
- Aluminum Machining
- Titanium Machining
- Stainless Steel Machining
- Copper Machining
- Brass Machining
- Super Alloy Machining
- Peek Machining
- UHMW Machining
- Unilate Machining
- PA6 Machining
- PPS Machining
- Teflon Machining
- Inconel Machining
- Tool Steel Machining
- More Material