Aluminum Die Casting vs. Aluminum Forging
Aluminum has become a cornerstone material in various industries, from automotive to aerospace, due to its unique combination of properties such as low density, high strength-to-weight ratio, and excellent corrosion resistance. The methods used to shape aluminum into the desired components significantly impact the final product's performance, cost, and environmental footprint. Among these methods, die casting and forging are two prominent techniques with distinct advantages and challenges.
Aluminum die casting involves forcing molten aluminum into a mold cavity under high pressure, allowing for the creation of complex shapes with tight tolerances. In contrast, aluminum forging is a process where aluminum is deformed under high pressure, typically at high temperatures, to achieve the desired shape. Each process is suited for different applications and presents unique benefits, making the choice between them a critical decision in the manufacturing process.
This article delves into the intricacies of both aluminum die casting and forging, providing a comprehensive comparison that highlights the technical, economic, and environmental considerations involved in each process. Understanding these differences is crucial for manufacturers aiming to optimize their production processes and achieve the best possible outcome for their specific needs.
Historical Context
Aluminum's history in manufacturing is closely tied to its discovery and subsequent commercialization in the 19th century. The development of die casting can be traced back to the mid-1800s when it was first used to produce type for printing presses. As the automotive industry grew in the early 20th century, die casting became increasingly popular for producing lightweight, high-volume components.
Forging, on the other hand, is one of the oldest metalworking processes, dating back thousands of years. The transition from iron and steel to aluminum forging began in the early 20th century, driven by the aerospace industry's demand for strong yet lightweight materials. The evolution of aluminum forging has been marked by continuous advancements in material science and process technologies, allowing for the production of increasingly complex and high-performance components.
Technical Overview of Aluminum Die Casting
Aluminum die casting is a highly efficient manufacturing process that involves injecting molten aluminum into a steel mold, known as a die, under high pressure. This process allows for the rapid production of components with intricate geometries, smooth surfaces, and tight tolerances. There are two primary types of die casting: high-pressure die casting (HPDC) and low-pressure die casting (LPDC).
High-Pressure Die Casting is the most common form of die casting, where molten aluminum is injected into the die at pressures ranging from 1,500 to 25,000 psi. The high pressure ensures that the molten aluminum fills even the most complex cavities within the die, resulting in highly detailed and precise components. This method is ideal for mass production, offering excellent repeatability and efficiency.
Low-Pressure Die Casting involves filling the mold at a lower pressure, typically around 15 psi, allowing for better control over the flow of the molten aluminum. This process is particularly suited for producing large and complex parts with fewer porosity issues than high-pressure die casting.
The aluminum alloys commonly used in die casting include Al-Si (Aluminum-Silicon) alloys, which offer good fluidity, corrosion resistance, and mechanical properties. The equipment required for die casting includes a die casting machine, dies, and a furnace for melting the aluminum.
Die casting is widely used in the automotive, aerospace, and consumer electronics industries, where high production volumes, precision, and surface finish are critical. The main advantages of die casting include its ability to produce complex shapes with minimal post-processing, high production efficiency, and excellent surface finish. However, the process also has some disadvantages, such as high initial tooling costs, potential porosity issues, and limitations on the mechanical properties of the cast parts.
Technical Overview of Aluminum Forging
Aluminum forging is a process in which aluminum is shaped by deforming it under high pressure, typically at elevated temperatures. The forging process can be classified into several types, including open die forging, closed die forging, cold forging, and hot forging.
Open Die Forging involves placing the aluminum between two flat or contoured dies and applying pressure to deform the material into the desired shape. This method is typically used for large and simple shapes, such as bars, shafts, and rings.
Closed Die Forging uses a pair of dies with the negative shape of the part to be produced. The aluminum is placed in the die cavity, and pressure is applied to shape it according to the die's contours. This method is suitable for producing complex and high-precision parts, such as gears, connecting rods, and crankshafts.
Cold Forging is performed at or near room temperature, resulting in high strength and excellent surface finish. However, the process is limited to simpler shapes and requires higher forces.
Hot Forging is conducted at elevated temperatures, making the aluminum more malleable and allowing for the production of more complex shapes. The hot forging process is widely used in the aerospace and automotive industries for critical structural components.
Aluminum alloys used in forging are typically those that offer a good balance of strength, ductility, and resistance to fatigue, such as 7075, 6061, and 2024 alloys. The equipment required for forging includes forging presses, hammers, and dies.
Forging offers several advantages, including superior mechanical properties, high strength, and durability. The process is also versatile, allowing for the production of a wide range of sizes and shapes. However, forging has its disadvantages, such as higher production costs, longer production times, and limitations in producing complex shapes compared to die casting.
Comparative Analysis
The choice between aluminum die casting and forging depends on several factors, including the mechanical properties required, design complexity, production efficiency, cost considerations, and application suitability.
Mechanical Properties: Forged aluminum parts generally exhibit superior mechanical properties compared to die-cast parts. Forging results in a more refined grain structure, leading to higher strength, toughness, and fatigue resistance. Die casting, while capable of producing parts with good mechanical properties, may suffer from issues such as porosity, which can compromise strength and integrity.
Design Flexibility: Die casting excels in producing complex shapes with intricate details, such as thin walls, internal cavities, and fine surface textures. Forging, on the other hand, is better suited for simpler shapes, although advances in forging technology have expanded its capabilities in producing more complex geometries.
Production Efficiency: Die casting is highly efficient for large production runs, offering fast cycle times and the ability to produce thousands of parts with minimal variation. Forging is generally slower and more labor-intensive, making it less suitable for high-volume production.
Cost Considerations: Die casting involves significant upfront costs for tooling and equipment, but these costs are amortized over large production volumes, making it cost-effective for mass production. Forging typically has higher per-part costs due to the labor-intensive nature of the process and the need for specialized equipment.
Quality and Consistency: Die-cast parts offer excellent surface finish and dimensional accuracy, but they may suffer from defects such as porosity and shrinkage. Forged parts are known for their superior quality and consistency, with fewer defects and higher reliability.
Environmental Impact: Both die casting and forging have environmental considerations. Die casting is energy-intensive, particularly in melting and injecting the aluminum. Forging also consumes significant energy, especially in hot forging processes. However, both processes generate scrap that can be recycled, contributing to overall sustainability.
Application Suitability: Die casting is widely used in industries where high production volumes, precision, and surface finish are critical, such as automotive and consumer electronics. Forging is preferred for applications requiring high strength, durability, and resistance to fatigue, such as aerospace components and structural parts.
Conclusion
Both aluminum die casting and forging are essential manufacturing processes, each offering unique advantages and challenges. Die casting is ideal for producing complex, high-volume parts with excellent surface finish and dimensional accuracy. In contrast, forging excels in applications where strength, durability, and mechanical performance are paramount.
The choice between the two processes depends on the specific requirements of the application, including the desired mechanical properties, design complexity, production volume, and cost constraints. As technology continues to advance, both die casting and forging will likely see further innovations that enhance their capabilities and expand their applications in various industries.
Reprint Statement: If there are no special instructions, all articles on this site are original. Please indicate the source for reprinting:https://www.cncmachiningptj.com/,thanks!
3, 4 and 5-axis precision CNC machining services for aluminum machining, beryllium, carbon steel, magnesium, titanium machining, Inconel, platinum, superalloy, acetal, polycarbonate, fiberglass, graphite and wood. Capable of machining parts up to 98 in. turning dia. and +/-0.001 in. straightness tolerance. Processes include milling, turning, drilling, boring, threading, tapping, forming, knurling, counterboring, countersinking, reaming and laser cutting. Secondary services such as assembly, centerless grinding, heat treating, plating and welding. Prototype and low to high volume production offered with maximum 50,000 units. Suitable for fluid power, pneumatics, hydraulics and valve applications. Serves the aerospace, aircraft, military, medical and defense industries.PTJ will strategize with you to provide the most cost-effective services to help you reach your target,Welcome to Contact us ( sales@pintejin.com ) directly for your new project.
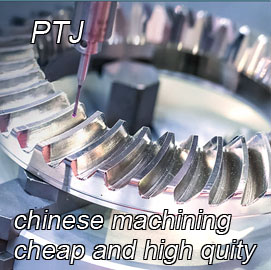
- 5 Axis Machining
- Cnc Milling
- Cnc Turning
- Machining Industries
- Machining Process
- Surface Treatment
- Metal Machining
- Plastic Machining
- Powder Metallurgy Mold
- Die Casting
- Parts Gallery
- Auto Metal Parts
- Machinery Parts
- LED Heatsink
- Building Parts
- Mobile Parts
- Medical Parts
- Electronic Parts
- Tailored Machining
- Bicycle Parts
- Aluminum Machining
- Titanium Machining
- Stainless Steel Machining
- Copper Machining
- Brass Machining
- Super Alloy Machining
- Peek Machining
- UHMW Machining
- Unilate Machining
- PA6 Machining
- PPS Machining
- Teflon Machining
- Inconel Machining
- Tool Steel Machining
- More Material