Punching Holes in Metal
Punching holes in metal is a fundamental process in the fabrication and manufacturing industries, involving the removal of material to create holes of various shapes and sizes. This process is essential in producing components for numerous applications, including automotive, aerospace, construction, electronics, and household products. The punching process is typically carried out using specialized machinery and tools that apply force to the metal sheet, resulting in the desired hole being cut out with precision and efficiency.
The history of hole punching in metal can be traced back to ancient civilizations, where rudimentary methods of shaping and cutting metal were developed. Over the centuries, advancements in technology and material science have led to the sophisticated techniques and equipment used today. Modern punching methods include mechanical, hydraulic, and CNC-controlled processes, each offering unique advantages depending on the material, hole size, and production volume.
This article provides a comprehensive overview of the punching process, exploring its various techniques, applications, tools, and considerations. It also delves into the technical aspects of punch and die design, the influence of material properties on the punching process, and the latest innovations in punching technology.
1. History of Punching in Metal Fabrication
1.1 Early Methods of Metalwork
The origins of metalworking date back to the Bronze Age, where ancient civilizations developed techniques for shaping and cutting metal for tools, weapons, and decorative items. The earliest forms of metal punching involved manual tools such as chisels and hammers, which were used to create holes in metal sheets or plates.
1.2 Development of Punching Techniques
As metallurgy advanced, so did the methods for working with metal. The invention of the mechanical press in the 19th century revolutionized the punching process, allowing for greater precision and efficiency. The development of hydraulic and pneumatic presses further enhanced the ability to punch holes in thicker and harder materials.
1.3 Modern Punching Methods
With the advent of computer numerical control (CNC) technology in the 20th century, punching processes became more automated and precise. CNC punching machines, equipped with programmable logic controllers (PLCs), enabled manufacturers to produce complex patterns and shapes with high repeatability and accuracy.
2. The Punching Process
2.1 Basic Principles
Punching is a cold-forming process that involves the use of a punch and die set to shear a portion of the metal sheet, creating a hole. The punch is forced through the material by applying a high compressive force, which causes the material to fracture and separate along the contour of the punch.
2.2 Types of Punching
Punching can be categorized into several types based on the shape and size of the hole being created, the method of force application, and the type of punch used.
- Blanking: Blanking involves the removal of a portion of the material to create a part, where the removed piece is the desired product.
- Piercing: Piercing refers to the creation of holes or openings in the material, where the remaining material is the product.
- Nibbling: Nibbling involves the creation of complex shapes by overlapping a series of small, closely spaced holes.
- Notching: Notching is the process of removing material from the edge or corner of a sheet to create specific profiles.
- Lancing: Lancing creates partial cuts in the material, forming tabs or lugs without complete material removal.
2.3 Equipment and Machinery
The equipment used in punching processes can range from simple hand tools to advanced CNC-controlled punching machines. Key components of punching equipment include:
- Punch Presses: The primary machine used for punching, available in mechanical, hydraulic, and pneumatic variants.
- Punch and Die Sets: Tools used to shear the material, with the punch acting as the cutting tool and the die providing support.
- Tooling: Various specialized tools and accessories, such as stripping plates, guide bushings, and alignment fixtures, enhance the precision and efficiency of the punching process.
2.4 Materials and Their Properties
The material being punched plays a crucial role in determining the success and quality of the punching process. Factors such as material thickness, hardness, ductility, and tensile strength influence the choice of punching method and tooling.
- Ferrous Metals: Steel, stainless steel, and other ferrous metals are commonly punched due to their wide usage in industrial applications. Special considerations are required for high-strength alloys.
- Non-Ferrous Metals: Aluminum, copper, and brass are also frequently punched, with adjustments needed for their lower strength and higher ductility.
- Exotic Alloys: Aerospace and medical applications often involve punching exotic alloys, requiring specialized tooling and techniques to prevent cracking or deformation.
3. Punch and Die Design
3.1 Design Considerations
Designing the punch and die is critical to achieving accurate and consistent results in the punching process. Key factors include:
- Clearance: The gap between the punch and die, which must be optimized based on the material thickness and type to minimize burrs and ensure a clean cut.
- Punch Shape: The shape and geometry of the punch determine the final hole's profile, with various shapes such as round, square, rectangular, and custom profiles being used.
- Die Shape: The die's shape complements the punch, and its design influences the ease of material removal and the quality of the cut edge.
3.2 Material Selection for Tools
The selection of materials for punch and die sets is crucial for ensuring tool longevity and performance. Common materials used include tool steels, carbide, and high-speed steel, each offering different levels of hardness, toughness, and wear resistance.
3.3 Tooling Maintenance and Wear
Punch and die tools are subject to wear over time, particularly when punching hard or abrasive materials. Regular maintenance, including sharpening and coating, is essential to extend tool life and maintain punching accuracy.
4. Advanced Punching Techniques
4.1 CNC Punching
CNC punching machines have revolutionized the punching process by automating tool movement and operation. These machines offer high precision, repeatability, and the ability to create complex patterns and shapes with minimal setup time.
4.2 Laser and Plasma-Assisted Punching
Combining traditional punching with laser or plasma cutting technologies allows for greater flexibility in material cutting and shaping. These hybrid processes enable the punching of intricate designs and the cutting of thicker materials with enhanced precision.
4.3 Progressive Die Punching
Progressive die punching involves the use of a series of stations within a single die, each performing a specific operation on the material. This method is highly efficient for mass production, allowing multiple operations such as punching, bending, and forming to be carried out in a single press cycle.
5. Applications of Punching in Metal Fabrication
5.1 Automotive Industry
Punching plays a critical role in the automotive industry, where it is used to produce components such as body panels, brackets, and structural elements. The high volume and precision requirements of automotive manufacturing make punching an ideal process for these applications.
5.2 Aerospace Industry
In the aerospace sector, punching is used to create lightweight and durable components for aircraft and spacecraft. The use of advanced materials such as titanium and composite alloys necessitates specialized punching techniques to achieve the desired results.
5.3 Electronics and Electrical Industries
The electronics and electrical industries rely on punching to create components such as enclosures, connectors, and circuit boards. The miniaturization of electronic devices has driven the development of micro-punching techniques, enabling the production of tiny and precise holes.
5.4 Construction and Architectural Applications
Punching is widely used in the construction industry to produce structural components, such as beams, columns, and brackets. In architectural applications, punching is used to create decorative elements, perforated panels, and custom designs in metal cladding and facades.
6. Challenges and Considerations in Punching
6.1 Material Deformation and Warping
One of the primary challenges in punching is minimizing material deformation and warping, which can occur due to the high forces involved in the process. Techniques such as optimizing clearance, using proper lubrication, and controlling punch speed can help mitigate these issues.
6.2 Burr Formation and Edge Quality
Burrs are unwanted projections of material that form around the edges of the punched hole. Burr formation is influenced by factors such as material type, punch and die condition, and punching speed. Reducing burr formation requires careful control of these variables, along with the use of secondary deburring processes if necessary.
6.3 Tool Wear and Maintenance
Punch and die tools are subject to wear, particularly when punching hard or abrasive materials. Maintaining tool sharpness, using appropriate coatings, and implementing regular maintenance schedules are essential to ensure consistent punching quality and extend tool life.
6.4 Cost and Efficiency Considerations
Balancing cost and efficiency is a key consideration in the punching process. Factors such as tooling costs, machine setup time, material waste, and production volume all influence the overall cost-effectiveness of punching. Optimizing these factors is essential for maximizing profitability in manufacturing operations.
7. Recent Innovations in Punching Technology
7.1 High-Speed Punching
Advancements in machine design and control systems have led to the development of high-speed punching machines capable of achieving faster cycle times and higher throughput. These machines are particularly beneficial for high-volume production environments, where speed and efficiency are critical.
7.2 Servo-Driven Punching Systems
Servo-driven punching systems offer precise control over punch movement and force application, enabling greater accuracy and flexibility in the punching process. These systems are increasingly used in applications that require complex shapes, tight tolerances, and minimal material waste.
7.3 Integration with Industry 4.0
The integration of punching machines with Industry 4.0 technologies, such as IoT, data analytics, and machine learning, is driving the evolution of smart manufacturing. Real-time monitoring, predictive maintenance, and process optimization are becoming increasingly common in punching operations, leading to improved productivity and reduced downtime.
7.4 Eco-Friendly Punching Solutions
Environmental considerations are influencing the development of punching technologies that minimize material waste, energy consumption, and the use of hazardous materials. Innovations such as water-based lubricants, recyclable tooling materials, and energy-efficient machines are contributing to more sustainable punching processes.
Conclusion
Punching holes in metal is a critical process in modern manufacturing, with applications spanning numerous industries. From its historical roots in manual metalworking to the advanced CNC and servo-driven systems of today, punching has evolved into a highly precise and efficient method for creating holes and shapes in metal. As technology continues to advance, the punching process will likely see further innovations, enabling manufacturers to meet the demands of increasingly complex and high-performance products.
Reprint Statement: If there are no special instructions, all articles on this site are original. Please indicate the source for reprinting:https://www.cncmachiningptj.com/,thanks!
3, 4 and 5-axis precision CNC machining services for aluminum machining, beryllium, carbon steel, magnesium, titanium machining, Inconel, platinum, superalloy, acetal, polycarbonate, fiberglass, graphite and wood. Capable of machining parts up to 98 in. turning dia. and +/-0.001 in. straightness tolerance. Processes include milling, turning, drilling, boring, threading, tapping, forming, knurling, counterboring, countersinking, reaming and laser cutting. Secondary services such as assembly, centerless grinding, heat treating, plating and welding. Prototype and low to high volume production offered with maximum 50,000 units. Suitable for fluid power, pneumatics, hydraulics and valve applications. Serves the aerospace, aircraft, military, medical and defense industries.PTJ will strategize with you to provide the most cost-effective services to help you reach your target,Welcome to Contact us ( sales@pintejin.com ) directly for your new project.
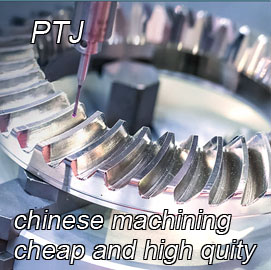
- 5 Axis Machining
- Cnc Milling
- Cnc Turning
- Machining Industries
- Machining Process
- Surface Treatment
- Metal Machining
- Plastic Machining
- Powder Metallurgy Mold
- Die Casting
- Parts Gallery
- Auto Metal Parts
- Machinery Parts
- LED Heatsink
- Building Parts
- Mobile Parts
- Medical Parts
- Electronic Parts
- Tailored Machining
- Bicycle Parts
- Aluminum Machining
- Titanium Machining
- Stainless Steel Machining
- Copper Machining
- Brass Machining
- Super Alloy Machining
- Peek Machining
- UHMW Machining
- Unilate Machining
- PA6 Machining
- PPS Machining
- Teflon Machining
- Inconel Machining
- Tool Steel Machining
- More Material