Relationship Between the Geometric Angle of Twist Drill and Grinding Accuracy
A twist drill is a fundamental tool in machining processes, primarily used for creating cylindrical holes. The efficiency, performance, and longevity of a twist drill are significantly influenced by its geometric design and the accuracy of its grinding process. This article delves into the intricate relationship between the geometric angle of a twist drill and grinding accuracy, exploring how these factors interplay to affect drilling performance, tool life, and overall manufacturing quality.
Geometric Angles of Twist Drill
Point Angle
The point angle, formed at the drill tip, is a critical parameter that influences the cutting action. Commonly, point angles range from 118° to 135° for general-purpose drills. A sharper point angle reduces the thrust force and is suitable for softer materials, while a blunter angle is better for harder materials.
Helix Angle
The helix angle, or the angle of the spiral flutes, affects chip removal and cutting efficiency. Typical helix angles range from 15° to 30°. A higher helix angle improves chip evacuation and is ideal for soft, ductile materials, whereas a lower angle is better for hard and brittle materials.
Lip Relief Angle
The lip relief angle, which is the angle between the leading edge of the cutting lip and the surface behind it, influences cutting efficiency and tool strength. An optimal lip relief angle minimizes friction and wear, enhancing tool life and performance.
Grinding Accuracy
Definition and Importance
Grinding accuracy refers to the precision with which the drill geometry is created during the grinding process. Accurate grinding ensures that the geometric angles are within specified tolerances, directly impacting the drill's performance and durability.
Factors Affecting Grinding Accuracy
- Machine Precision: The accuracy of the grinding machine itself is paramount. High-precision machines can produce consistent and accurate drill geometries.
- Wheel Selection: The type of grinding wheel used affects the grinding process. Proper selection of wheel material and grain size is crucial for achieving desired accuracy.
- Operator Skill: The skill and experience of the operator play a significant role in grinding accuracy. Skilled operators can make fine adjustments to ensure precision.
- Setup and Alignment: Proper setup and alignment of the drill in the grinding machine are essential for accurate results. Misalignment can lead to errors in geometric angles.
Relationship Between Geometric Angles and Grinding Accuracy
Impact on Cutting Performance
The geometric angles of a twist drill, when ground accurately, ensure optimal cutting performance. Inaccurate grinding can lead to deviations in these angles, resulting in poor cutting efficiency, increased wear, and reduced tool life.
- Point Angle: Inaccurate grinding of the point angle can cause uneven cutting forces, leading to poor hole quality and potential drill breakage.
- Helix Angle: Deviations in the helix angle affect chip evacuation. Improper grinding can cause chip clogging, increasing the risk of drill failure.
- Lip Relief Angle: Incorrect lip relief angle grinding results in increased friction and wear, reducing the drill's cutting efficiency and lifespan.
Tool Life and Durability
Accurate grinding extends tool life by ensuring that the geometric angles are optimized for the material being drilled. Inaccurate grinding can lead to premature tool wear and failure.
- Wear Resistance: Properly ground angles reduce wear by minimizing friction and heat generation during drilling.
- Strength and Stability: Accurate grinding maintains the structural integrity of the drill, preventing breakage and deformation.
Surface Finish and Hole Quality
The quality of the drilled hole is directly related to the accuracy of the drill geometry. Inaccurate grinding can lead to poor surface finish, dimensional inaccuracies, and defects in the drilled hole.
- Surface Finish: Accurate geometric angles produce a smooth surface finish by ensuring consistent cutting action.
- Dimensional Accuracy: Properly ground drills maintain tight tolerances, ensuring the drilled hole meets the required specifications.
Methods to Enhance Grinding Accuracy
Advanced Grinding Techniques
- CNC Grinding: Computer Numerical Control (CNC) grinding machines offer high precision and repeatability, ensuring accurate drill geometry.
- Laser-Assisted Grinding: Laser technology can be used to enhance the accuracy of the grinding process by providing precise control over material removal.
Quality Control Measures
- Inspection and Measurement: Regular inspection and measurement of drill geometry using advanced metrology tools ensure that the grinding process remains within specified tolerances.
- Process Optimization: Continuous monitoring and optimization of the grinding process parameters help maintain grinding accuracy.
Training and Skill Development
- Operator Training: Regular training programs for operators enhance their skills and understanding of the grinding process, leading to better accuracy.
- Skill Development: Encouraging skill development through workshops and hands-on training improves overall grinding accuracy.
Conclusion
The geometric angle of a twist drill and the accuracy of its grinding are intricately linked, with a direct impact on drilling performance, tool life, and hole quality. Ensuring accurate grinding of the geometric angles enhances cutting efficiency, reduces wear, and improves the overall quality of the drilling process. Advances in grinding technology and continuous skill development are crucial for maintaining high grinding accuracy and optimizing drill performance.
Reprint Statement: If there are no special instructions, all articles on this site are original. Please indicate the source for reprinting:https://www.cncmachiningptj.com/,thanks!
3, 4 and 5-axis precision CNC machining services for aluminum machining, beryllium, carbon steel, magnesium, titanium machining, Inconel, platinum, superalloy, acetal, polycarbonate, fiberglass, graphite and wood. Capable of machining parts up to 98 in. turning dia. and +/-0.001 in. straightness tolerance. Processes include milling, turning, drilling, boring, threading, tapping, forming, knurling, counterboring, countersinking, reaming and laser cutting. Secondary services such as assembly, centerless grinding, heat treating, plating and welding. Prototype and low to high volume production offered with maximum 50,000 units. Suitable for fluid power, pneumatics, hydraulics and valve applications. Serves the aerospace, aircraft, military, medical and defense industries.PTJ will strategize with you to provide the most cost-effective services to help you reach your target,Welcome to Contact us ( sales@pintejin.com ) directly for your new project.
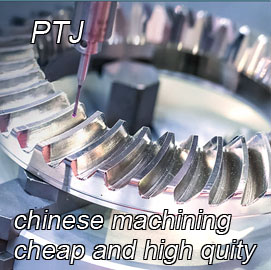
- 5 Axis Machining
- Cnc Milling
- Cnc Turning
- Machining Industries
- Machining Process
- Surface Treatment
- Metal Machining
- Plastic Machining
- Powder Metallurgy Mold
- Die Casting
- Parts Gallery
- Auto Metal Parts
- Machinery Parts
- LED Heatsink
- Building Parts
- Mobile Parts
- Medical Parts
- Electronic Parts
- Tailored Machining
- Bicycle Parts
- Aluminum Machining
- Titanium Machining
- Stainless Steel Machining
- Copper Machining
- Brass Machining
- Super Alloy Machining
- Peek Machining
- UHMW Machining
- Unilate Machining
- PA6 Machining
- PPS Machining
- Teflon Machining
- Inconel Machining
- Tool Steel Machining
- More Material