Metal Powder Approved for 3D Printing in Formula 1
The realm of Formula 1 (F1) racing has consistently been at the forefront of technological innovation. Among the many advancements, the use of metal powder for 3D printing, also known as additive manufacturing (AM), represents a significant leap forward. This technology has revolutionized how components are designed, manufactured, and integrated into the highly competitive world of F1 racing. This article delves into the intricacies of metal powder 3D printing in Formula 1, examining its development, applications, benefits, and future prospects.
Historical Context of 3D Printing in Formula 1
Early Adoption of 3D Printing
3D printing technology first emerged in the 1980s, but it wasn't until the late 1990s and early 2000s that it began to make inroads into various industries, including automotive and aerospace. Formula 1 teams, always on the lookout for cutting-edge technology, soon recognized the potential of 3D printing. Initial applications focused on rapid prototyping, allowing teams to create scale models and test parts quickly and cost-effectively.
Transition to Metal 3D Printing
While early 3D printing efforts in F1 primarily used plastics and resins, the transition to metal 3D printing marked a pivotal shift. Metal 3D printing, or metal additive manufacturing, enables the production of functional, high-strength components suitable for use in critical areas of an F1 car. This transition was driven by advancements in metal powder technology and 3D printing techniques, which allowed for the creation of parts that could withstand the extreme conditions of F1 racing.
Metal Powder Technology
Types of Metal Powders
The metal powders used in 3D printing for Formula 1 are meticulously engineered to meet specific performance criteria. Commonly used metal powders include:
- Titanium Alloys: Known for their excellent strength-to-weight ratio and corrosion resistance, titanium alloys such as Ti-6Al-4V are widely used in F1.
- Aluminum Alloys: Aluminum alloys, including AlSi10Mg, offer lightweight properties and good mechanical strength, making them ideal for various structural components.
- Nickel Alloys: Inconel 718 and other nickel-based superalloys are used for parts that must endure high temperatures and stresses, such as exhaust components and turbocharger parts.
- Stainless Steel: Stainless steel powders like 316L provide excellent mechanical properties and corrosion resistance, suitable for various engine and structural parts.
Powder Production Methods
The quality and consistency of metal powders are critical to the success of 3D printed parts. Common methods for producing metal powders include:
- Atomization: This process involves melting the metal and then dispersing it into fine droplets using a high-pressure gas or liquid. The droplets solidify into spherical powder particles.
- Mechanical Alloying: This method mixes and fuses different metal powders through mechanical processes, creating alloy powders with desired properties.
- Electrolysis: Electrolysis can produce high-purity metal powders by depositing metal onto a cathode from a solution of metal ions.
Quality Control
Ensuring the quality of metal powders is paramount. Quality control measures include:
- Particle Size Distribution: Consistent particle size distribution is crucial for achieving uniform layer deposition during the printing process.
- Purity: Impurities can weaken the final part, so high-purity powders are essential.
- Morphology: The shape and surface characteristics of powder particles affect flowability and packing density, impacting the quality of the printed part.
3D Printing Processes in Formula 1
Selective Laser Melting (SLM)
Selective Laser Melting (SLM) is one of the most common 3D printing techniques used in Formula 1. It involves spreading a thin layer of metal powder onto a build platform and selectively melting it using a high-powered laser. This process is repeated layer by layer until the entire part is built. SLM offers high precision and is capable of producing complex geometries with excellent mechanical properties.
Electron Beam Melting (EBM)
Electron Beam Melting (EBM) is another technique used in F1, similar to SLM but utilizing an electron beam instead of a laser to melt the powder. EBM operates in a vacuum environment, which is beneficial for processing reactive materials like titanium. It also allows for faster build rates and is suitable for larger parts.
Direct Metal Laser Sintering (DMLS)
Direct Metal Laser Sintering (DMLS) is akin to SLM but typically used for a wider range of metal powders. DMLS involves sintering the powder particles together rather than fully melting them. This technique is advantageous for producing parts with intricate internal structures and fine details.
Binder Jetting
Binder Jetting is a different approach, where a liquid binding agent is selectively deposited onto a powder bed, binding the powder particles together. The part is then cured and sintered in a furnace to achieve its final properties. Binder Jetting allows for the production of parts with complex geometries and can be faster than SLM and EBM.
Applications of 3D Printed Metal Parts in Formula 1
Engine Components
The engine of an F1 car is a highly sophisticated and complex system where 3D printing has found numerous applications. Metal 3D printing allows for the creation of lightweight, high-strength components that can withstand extreme temperatures and pressures. Examples include:
- Turbocharger Housings: 3D printed using nickel alloys, these housings can endure the high temperatures and stresses of turbocharged engines.
- Piston Heads: Titanium alloys are used to produce piston heads that are both lightweight and strong, improving engine performance and efficiency.
- Fuel Nozzles: Complex geometries required for optimal fuel injection can be easily achieved with 3D printing, enhancing combustion efficiency.
Aerodynamic Parts
Aerodynamics play a crucial role in the performance of an F1 car. 3D printing enables the production of intricate aerodynamic components that would be challenging or impossible to create using traditional manufacturing methods. Applications include:
- Winglets and Flaps: These parts can be optimized for aerodynamic performance and printed in lightweight aluminum or titanium alloys.
- Diffusers: Complex internal channels within diffusers can be precisely manufactured to improve airflow and downforce.
- Brake Ducts: Custom brake ducts can be designed and printed to optimize cooling performance for specific race conditions.
Structural Components
Structural integrity is paramount in F1, and 3D printing allows for the creation of robust yet lightweight structural components. Examples include:
- Suspension Components: Titanium and aluminum alloys are used to print suspension parts that offer the necessary strength and durability while reducing weight.
- Chassis Components: 3D printed brackets, mounts, and other chassis components contribute to overall weight reduction and improved performance.
- Steering System Parts: Complex steering system parts can be precisely manufactured to meet the stringent demands of F1 racing.
Customized Parts
The ability to produce customized parts quickly is a significant advantage in F1. Teams can design and print bespoke components tailored to specific requirements or race conditions. This flexibility allows for rapid prototyping and testing of new designs, leading to continuous performance improvements.
Benefits of Metal 3D Printing in Formula 1
Weight Reduction
One of the primary benefits of metal 3D printing in F1 is weight reduction. By optimizing designs and using lightweight materials, 3D printed parts contribute to the overall reduction of the car's weight. This results in improved acceleration, handling, and fuel efficiency.
Design Freedom
3D printing offers unparalleled design freedom, allowing engineers to create complex geometries that would be impossible or impractical with traditional manufacturing methods. This design flexibility enables the production of optimized components that enhance performance and functionality.
Rapid Prototyping and Production
The speed of 3D printing is a significant advantage in the fast-paced world of F1. Teams can rapidly prototype and test new designs, making iterative improvements in a short time frame. Additionally, 3D printing allows for on-demand production of parts, reducing lead times and inventory costs.
Performance Enhancements
By leveraging the capabilities of 3D printing, F1 teams can produce parts with improved mechanical properties and performance characteristics. This includes components with optimized strength-to-weight ratios, enhanced thermal properties, and superior fatigue resistance.
Cost Efficiency
While the initial investment in 3D printing technology can be high, the long-term cost savings are substantial. Reduced material waste, lower tooling costs, and the ability to produce parts on-demand contribute to overall cost efficiency.
Sustainability
3D printing is inherently more sustainable than traditional manufacturing methods, as it generates less waste and requires fewer resources. In an industry increasingly focused on sustainability, this is a notable advantage.
Challenges and Limitations
Material Limitations
Despite the many benefits, there are still limitations in the range of materials that can be effectively used in metal 3D printing. Not all metals possess the necessary properties for 3D printing, and some materials can be challenging to process due to their melting points or reactivity.
Surface Finish and Post-Processing
The surface finish of 3D printed parts can sometimes be rough, requiring additional post-processing to achieve the desired smoothness and precision. This can add time and cost to the production process.
Equipment and Operational Costs
High-end 3D printing equipment and the associated operational costs can be prohibitive. While the technology is becoming more accessible, the initial investment remains a barrier for some teams.
Standardization and Certification
As with any emerging technology, standardization and certification processes are still evolving for 3D printed parts. Ensuring consistency and reliability across different batches of printed parts is crucial for their widespread adoption in F1.
Intellectual Property Concerns
The ability to quickly replicate complex parts with 3D printing raises concerns about intellectual property protection. Ensuring the security of design data and preventing unauthorized reproduction of proprietary components is a significant challenge.
Future Prospects of Metal 3D Printing in Formula 1
Continued Material Advancements
Ongoing research and development in metal powder technology are expected to yield new materials with enhanced properties suitable for 3D printing. This will expand the range of applications and further improve the performance of 3D printed parts in F1.
Integration with Digital Twins
The concept of digital twins, virtual replicas of physical components, is gaining traction in F1. Integrating 3D printing with digital twins allows for real-time monitoring, testing, and optimization of parts, leading to even greater performance improvements.
Increased Automation
Advancements in automation and robotics will streamline the 3D printing process, reducing labor costs and improving efficiency. This will make the technology more accessible and cost-effective for F1 teams.
Broader Adoption Across Teams
As the benefits of metal 3D printing become increasingly evident, more F1 teams are likely to adopt the technology. This will drive further innovation and competition, leading to continued advancements in 3D printing techniques and applications.
Collaborative Developments
Collaboration between F1 teams, 3D printing companies, and material scientists will accelerate the development of new technologies and materials. These partnerships will drive innovation and ensure that F1 remains at the cutting edge of 3D printing advancements.
Conclusion
Metal powder 3D printing has firmly established itself as a transformative technology in the world of Formula 1 racing. Its ability to produce lightweight, high-strength components with complex geometries has revolutionized the design and manufacturing processes within the sport. While challenges remain, the continued advancement of metal 3D printing technology promises to drive further performance improvements and innovation in F1. As teams continue to explore and harness the potential of this technology, the future of metal powder 3D printing in Formula 1 looks incredibly promising.
Reprint Statement: If there are no special instructions, all articles on this site are original. Please indicate the source for reprinting:https://www.cncmachiningptj.com/,thanks!
3, 4 and 5-axis precision CNC machining services for aluminum machining, beryllium, carbon steel, magnesium, titanium machining, Inconel, platinum, superalloy, acetal, polycarbonate, fiberglass, graphite and wood. Capable of machining parts up to 98 in. turning dia. and +/-0.001 in. straightness tolerance. Processes include milling, turning, drilling, boring, threading, tapping, forming, knurling, counterboring, countersinking, reaming and laser cutting. Secondary services such as assembly, centerless grinding, heat treating, plating and welding. Prototype and low to high volume production offered with maximum 50,000 units. Suitable for fluid power, pneumatics, hydraulics and valve applications. Serves the aerospace, aircraft, military, medical and defense industries.PTJ will strategize with you to provide the most cost-effective services to help you reach your target,Welcome to Contact us ( sales@pintejin.com ) directly for your new project.
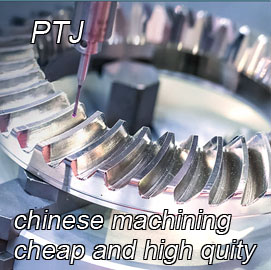
- 5 Axis Machining
- Cnc Milling
- Cnc Turning
- Machining Industries
- Machining Process
- Surface Treatment
- Metal Machining
- Plastic Machining
- Powder Metallurgy Mold
- Die Casting
- Parts Gallery
- Auto Metal Parts
- Machinery Parts
- LED Heatsink
- Building Parts
- Mobile Parts
- Medical Parts
- Electronic Parts
- Tailored Machining
- Bicycle Parts
- Aluminum Machining
- Titanium Machining
- Stainless Steel Machining
- Copper Machining
- Brass Machining
- Super Alloy Machining
- Peek Machining
- UHMW Machining
- Unilate Machining
- PA6 Machining
- PPS Machining
- Teflon Machining
- Inconel Machining
- Tool Steel Machining
- More Material