Five Major Thin-Walled Parts Forming Processes
Thin-walled parts are integral components in a myriad of industries, including automotive, aerospace, electronics, and consumer goods. These components, characterized by their minimal wall thickness relative to their overall dimensions, offer a blend of lightweight characteristics and structural integrity. The fabrication of thin-walled parts involves sophisticated forming processes that ensure precision, durability, and functionality. This article delves into five major forming processes—Deep Drawing, Hydroforming, Metal Spinning, Roll Forming, and Superplastic Forming—elucidating their principles, applications, advantages, and limitations.
Deep Drawing
Definition and Basic Principles
Deep drawing is a forming process in which a flat sheet metal blank is radially drawn into a forming die by the mechanical action of a punch. It is distinguished from other metal forming processes by the material flow characteristics and the significant depth-to-diameter ratio achieved in the drawn part.
Equipment and Materials Used
The deep drawing process requires specific equipment, including hydraulic or mechanical presses, punches, and dies. The choice of material is critical, with common choices being aluminum, brass, copper, and steel, each selected based on the required mechanical properties and end-use applications.
Process Steps
- Blanking: The initial step involves cutting the raw sheet metal into a blank, typically performed using a blanking die.
- Drawing: The blank is placed over a die cavity and pressed into shape by a punch, creating a deep recess.
- Ironing: The walls of the part may be thinned and smoothed through ironing rings to ensure uniform thickness.
- Trimming: Excess material is trimmed to achieve the final dimensions.
Advantages and Limitations
Deep drawing offers several advantages, such as the ability to produce complex shapes with high strength and smooth finishes. However, it has limitations, including the risk of tearing, wrinkling, and the necessity for precise control of material properties and process parameters.
Applications and Case Studies
Deep drawing is widely used in manufacturing automotive components, beverage cans, kitchen sinks, and various containers. For instance, the production of fuel tanks in the automotive industry showcases the efficiency and precision of deep drawing in creating large, complex parts.
Recent Advancements and Future Trends
Recent advancements in deep drawing include the development of servo-controlled presses, which provide enhanced control over the drawing process, and the use of simulation software to optimize tool design and material flow. Future trends point towards greater automation and the integration of real-time monitoring systems to ensure quality and efficiency.
Hydroforming
Definition and Basic Principles
Hydroforming is a versatile forming process that uses a high-pressure hydraulic fluid to shape metal sheets or tubes into desired forms. This method is particularly advantageous for creating complex geometries with uniform material distribution.
Types of Hydroforming
- Sheet Hydroforming: Involves placing a sheet over a die and using hydraulic fluid to press it into shape.
- Tube Hydroforming: A tube is placed inside a die and pressurized from the inside, causing it to conform to the die’s shape.
Equipment and Materials Used
Hydroforming requires specialized equipment, including high-pressure pumps, hydraulic presses, and precision dies. Materials such as aluminum, brass, stainless steel, and high-strength alloys are commonly used due to their excellent formability and strength.
Process Steps
- Preparation: The metal blank or tube is prepared and placed in the hydroforming die.
- Forming: High-pressure hydraulic fluid is applied, which molds the material into the desired shape.
- Finishing: Post-forming processes such as trimming, heat treatment, or surface finishing may be applied to meet final specifications.
Advantages and Limitations
Hydroforming offers numerous advantages, including the ability to form complex shapes in a single operation, reduced material waste, and improved mechanical properties due to work hardening. However, the high initial cost of equipment and the complexity of the process can be seen as limitations.
Applications and Case Studies
This process is widely utilized in the automotive and aerospace industries for manufacturing lightweight, high-strength components such as engine cradles, exhaust components, and structural members. For example, the use of hydroformed components in automotive chassis design has led to significant weight reductions and performance improvements.
Recent Advancements and Future Trends
Recent advancements in hydroforming include the development of more efficient hydraulic systems, the use of advanced materials, and the integration of computer-aided design and manufacturing technologies. Future trends are likely to focus on further automation and the exploration of hybrid forming techniques to enhance efficiency and reduce costs.
Metal Spinning
Definition and Basic Principles
Metal spinning, also known as spin forming or spinning, is a metalworking process by which a disc or tube of metal is rotated at high speed and formed into an axially symmetric part using a roller or other forming tool.
Types of Metal Spinning
- Manual Spinning: Traditional form where the operator manually shapes the metal.
- CNC Spinning: Computer Numerical Control (CNC) machines automate the process, allowing for greater precision and repeatability.
- Shear Spinning: A variation where the metal is thinned and stretched during the spinning process.
Equipment and Materials Used
The process involves a lathe or spinning machine, forming tools, and sometimes a mandrel to support the workpiece. Common materials include aluminum, brass, copper, stainless steel, and titanium, chosen for their malleability and strength.
Process Steps
- Preparation: The metal blank is cut and positioned on the spinning machine.
- Spinning: The blank is rotated at high speed while a forming tool presses it against a mandrel to achieve the desired shape.
- Finishing: Additional operations such as trimming, polishing, or heat treatment may be performed to finalize the part.
Advantages and Limitations
Metal spinning allows for the production of seamless, strong, and lightweight components with minimal waste. The process is flexible and cost-effective for small to medium production runs. However, it can be labor-intensive, especially in manual spinning, and may be limited by the complexity of shapes that can be produced.
Applications and Case Studies
Metal spinning is used in producing parts such as lighting fixtures, cookware, musical instruments, and aerospace components. For instance, the creation of nose cones for rockets and missiles demonstrates the capability of metal spinning to produce high-precision, thin-walled parts.
Recent Advancements and Future Trends
Advancements in metal CNC spinning include the use of CNC technology for greater precision and automation, as well as the development of new forming tools and techniques to expand the range of producible shapes. Future trends may involve the integration of real-time monitoring and control systems to enhance process efficiency and quality.
Roll Forming
Definition and Basic Principles
Roll forming is a continuous bending process in which a long strip of sheet metal is passed through a series of rollers to achieve the desired cross-sectional profile. This process is highly efficient for producing long lengths of complex profiles.
Equipment and Materials Used
The roll forming process requires a series of roll stands, each containing a pair of rollers that incrementally shape the metal strip. Materials commonly used include steel, aluminum, and high-strength alloys, selected based on the required mechanical properties and application.
Process Steps
- Roll Stands: The strip is fed through a series of roll stands, each progressively shaping the metal.
- Forming: The metal strip is continuously bent into the desired profile.
- Cutting: The formed profile is cut to the required length using flying cut-off machines.
Advantages and Limitations
Roll forming is highly efficient, capable of producing complex profiles with high dimensional accuracy and consistency. It is suitable for high-volume production with minimal material waste. However, the initial cost of roll forming equipment and tooling can be high, and the process may be less flexible for small production runs or complex shapes.
Applications and Case Studies
Roll forming is extensively used in the construction, automotive, and appliance industries to produce components such as roof panels, structural beams, and window frames. For example, the production of automotive door beams showcases the ability of roll forming to create strong, lightweight parts with precise geometries.
Recent Advancements and Future Trends
Recent advancements in roll forming include the development of more sophisticated roll designs, the use of high-strength materials, and the integration of computer-aided engineering tools to optimize the process. Future trends are likely to focus on further automation, the use of advanced materials, and the exploration of hybrid forming processes to enhance efficiency and flexibility.
Superplastic Forming
Definition and Basic Principles
Superplastic forming is a manufacturing process that leverages the superplasticity of certain materials, allowing them to be stretched into complex shapes at elevated temperatures without tearing. This process is particularly useful for creating intricate, lightweight components with excellent dimensional accuracy.
Equipment and Materials Used
The process involves specialized forming presses capable of maintaining high temperatures and precise pressure control. Common materials used include titanium alloys, aluminum alloys, and some advanced ceramics, chosen for their superplastic properties.
Process Steps
- Heating: The material is heated to a temperature where it exhibits superplastic behavior.
- Forming: The material is slowly formed into the desired shape using a die, with precise control over pressure and temperature.
- Cooling: The formed part is cooled down to retain its shape and properties.
Advantages and Limitations
Superplastic forming enables the production of complex geometries with fine details and minimal residual stresses. It also allows for significant weight reductions in the final parts. However, the process can be slow and energy-intensive due to the high temperatures required, and it may be limited by the availability of suitable materials.
Applications and Case Studies
Superplastic forming is widely used in the aerospace and automotive industries to produce components such as aircraft fuselage panels, turbine blades, and intricate structural parts. For example, the use of superplastic forming in creating titanium components for aerospace applications highlights the process's capability to produce high-performance, lightweight parts with complex geometries.
Recent Advancements and Future Trends
Advancements in superplastic forming include the development of new superplastic materials, improved heating and pressure control systems, and the integration of simulation tools to optimize process parameters. Future trends may involve the combination of superplastic forming with other advanced manufacturing techniques, such as additive manufacturing, to enhance design flexibility and reduce production times.
Comparison of Processes
Criteria for Selection
The selection of a forming process for thin-walled parts depends on several criteria, including the complexity of the shape, material properties, production volume, cost considerations, and specific application requirements.
Comparative Analysis
- Cost: Roll forming and deep drawing are generally more cost-effective for high-volume production, while superplastic forming and hydroforming may be more suitable for lower volumes or specialized applications.
- Material Utilization: Processes like hydroforming and superplastic forming offer excellent material utilization, with minimal waste.
- Complexity: Superplastic forming and hydroforming can produce more complex shapes compared to deep drawing and roll forming.
- Production Speed: Roll forming and metal spinning offer faster production rates compared to hydroforming and superplastic forming.
Case Studies
Comparative case studies, such as the production of automotive components using deep drawing versus hydroforming, can illustrate the practical considerations and trade-offs involved in selecting a forming process.
Conclusion
Thin-walled parts forming is a critical area of manufacturing that involves various advanced processes to meet the demands of modern industries. Each forming process—Deep Drawing, Hydroforming, Metal Spinning, Roll Forming, and Superplastic Forming—offers unique advantages and challenges, making them suitable for specific applications. As technology advances, these processes continue to evolve, driving improvements in efficiency, precision, and material utilization. The future of thin-walled parts forming is poised for further innovation, integrating new materials, automation, and hybrid techniques to meet the ever-growing needs of diverse industries.
Reprint Statement: If there are no special instructions, all articles on this site are original. Please indicate the source for reprinting:https://www.cncmachiningptj.com/,thanks!
3, 4 and 5-axis precision CNC machining services for aluminum machining, beryllium, carbon steel, magnesium, titanium machining, Inconel, platinum, superalloy, acetal, polycarbonate, fiberglass, graphite and wood. Capable of machining parts up to 98 in. turning dia. and +/-0.001 in. straightness tolerance. Processes include milling, turning, drilling, boring, threading, tapping, forming, knurling, counterboring, countersinking, reaming and laser cutting. Secondary services such as assembly, centerless grinding, heat treating, plating and welding. Prototype and low to high volume production offered with maximum 50,000 units. Suitable for fluid power, pneumatics, hydraulics and valve applications. Serves the aerospace, aircraft, military, medical and defense industries.PTJ will strategize with you to provide the most cost-effective services to help you reach your target,Welcome to Contact us ( sales@pintejin.com ) directly for your new project.
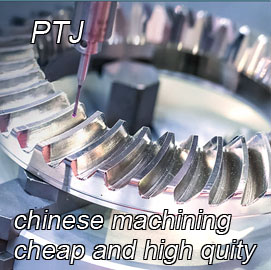
- 5 Axis Machining
- Cnc Milling
- Cnc Turning
- Machining Industries
- Machining Process
- Surface Treatment
- Metal Machining
- Plastic Machining
- Powder Metallurgy Mold
- Die Casting
- Parts Gallery
- Auto Metal Parts
- Machinery Parts
- LED Heatsink
- Building Parts
- Mobile Parts
- Medical Parts
- Electronic Parts
- Tailored Machining
- Bicycle Parts
- Aluminum Machining
- Titanium Machining
- Stainless Steel Machining
- Copper Machining
- Brass Machining
- Super Alloy Machining
- Peek Machining
- UHMW Machining
- Unilate Machining
- PA6 Machining
- PPS Machining
- Teflon Machining
- Inconel Machining
- Tool Steel Machining
- More Material