Advantages and Disadvantages of 3D Printing Technology to Make Molds
3D printing, also known as additive manufacturing, has revolutionized various sectors of manufacturing, including the production of molds. Molds are essential in manufacturing processes like injection molding, casting, and thermoforming. Traditionally, molds are crafted from metal or other durable materials using subtractive manufacturing techniques, such as CNC machining. However, the advent of 3D printing technology has introduced new possibilities and challenges in mold making. This article explores the advantages and disadvantages of using 3D printing technology to make molds, providing a comprehensive overview of its impact on the manufacturing industry.
Advantages of 3D Printing Technology in Mold Making
1. Cost-Effectiveness
One of the most significant advantages of using 3D printing for mold making is cost-effectiveness. Traditional mold-making processes, especially CNC machining, can be expensive due to the high cost of materials, labor, and machinery. 3D printing reduces these costs by using less material and requiring less manual labor. The initial investment in a 3D printer may be high, but it can be offset by the savings in production costs over time.
2. Speed and Efficiency
3D printing significantly reduces the time required to produce molds. Traditional mold-making methods can take weeks or even months, from design to final product. In contrast, 3D printing can produce molds in a matter of hours or days, depending on the complexity and size. This speed is particularly advantageous for prototyping and short production runs, allowing manufacturers to quickly test and iterate designs.
3. Design Flexibility
3D printing offers unparalleled design flexibility. Traditional manufacturing techniques often have limitations in terms of geometry and complexity. 3D printing can produce intricate and complex shapes that would be difficult or impossible to achieve with conventional methods. This flexibility allows for more innovative designs and can lead to improved product performance and functionality.
4. Customization and Personalization
3D printing enables easy customization and personalization of molds. This is particularly beneficial in industries such as healthcare, where custom molds can be used to produce patient-specific implants or prosthetics. The ability to quickly and affordably produce customized molds opens up new possibilities for tailored solutions in various applications.
5. Reduction of Material Waste
Traditional subtractive manufacturing processes generate a significant amount of material waste, as excess material is removed to create the desired shape. In contrast, 3D printing is an additive process, building the mold layer by layer with minimal waste. This reduction in material waste not only lowers costs but also has environmental benefits.
6. Tool-less Production
3D printing eliminates the need for specialized tools and equipment traditionally required for mold making. This tool-less production simplifies the manufacturing process and reduces the time and cost associated with tool changes and maintenance. Additionally, it allows for the production of molds on-demand without the need for extensive setup and preparation.
7. Enhanced Prototyping
The ability to quickly produce prototypes is a major advantage of 3D printing in mold making. Manufacturers can rapidly create and test multiple iterations of a mold design, making adjustments as needed before committing to full-scale production. This iterative process enhances product development, reduces the risk of design flaws, and ultimately leads to better end products.
Disadvantages of 3D Printing Technology in Mold Making
1. Material Limitations
Despite the advances in 3D printing materials, there are still limitations compared to traditional mold-making materials like steel and aluminum. 3D printed mold may not have the same durability, strength, or heat resistance as their traditional counterparts. This can limit their use in high-volume production or applications requiring extreme conditions.
2. Surface Finish Quality
The surface finish of 3D printed molds may not be as smooth or precise as those produced by traditional methods. Post-processing steps such as sanding, polishing, or coating may be required to achieve the desired surface quality. These additional steps can add time and cost to the production process, potentially offsetting some of the efficiency gains of 3D printing.
3. Size Constraints
The size of the molds that can be produced using 3D printing is often limited by the build volume of the printer. Large molds may need to be printed in multiple pieces and then assembled, which can introduce challenges in terms of alignment, bonding, and structural integrity. This limitation can restrict the use of 3D printing for very large or complex mold designs.
4. Cost of High-Performance Materials
While 3D printing can be cost-effective for many applications, the cost of high-performance materials suitable for mold making can be prohibitive. Materials that offer high strength, heat resistance, or other specialized properties tend to be more expensive than standard 3D printing materials. This can limit the economic benefits of 3D printing for certain applications.
5. Technological Limitations
Despite significant advancements, 3D printing technology still faces some limitations in terms of precision, accuracy, and repeatability. Variations in printer performance, material quality, and environmental conditions can impact the consistency of the final product. For critical applications requiring high precision and reliability, these technological limitations can be a significant drawback.
6. Post-Processing Requirements
Many 3D printed molds require post-processing to achieve the desired properties and finish. This can include heat treatment, surface finishing, and assembly of printed components. These additional steps can increase the time and cost of production, potentially reducing the overall efficiency gains from using SLM 3D printing.
7. Intellectual Property Concerns
The ease of creating and sharing digital designs in 3D printing raises concerns about intellectual property (IP) protection. Unauthorized reproduction and distribution of mold designs can be difficult to control, leading to potential IP infringement issues. Manufacturers need to implement robust measures to protect their designs and maintain competitive advantage.
Case Studies and Applications
Automotive Industry
In the automotive industry, 3D printing is used to produce prototype molds for testing new components and designs. This allows for rapid iteration and validation of parts before committing to mass production. For example, car manufacturers have used 3D printed molds to create prototype parts for engines, interiors, and body components, significantly reducing development time and cost.
Aerospace Industry
The aerospace industry benefits from the ability to produce lightweight and complex molds using 3D printing. This is particularly important for creating molds for composite materials used in aircraft components. The ability to produce intricate shapes and structures enhances the performance and efficiency of aerospace parts while reducing manufacturing time and material waste.
Healthcare and Medical Devices
3D printing is revolutionizing the healthcare sector by enabling the production of custom molds for medical devices and implants. Custom molds can be created based on patient-specific data, leading to better-fitting and more effective medical solutions. For instance, dental laboratories use 3D printing to create molds for dental crowns, bridges, and orthodontic devices tailored to individual patients.
Consumer Goods
The consumer goods industry uses 3D printing to create molds for a wide range of products, from household items to electronics. The ability to quickly produce and test prototype molds accelerates product development and allows for more innovative designs. For example, companies have used 3D printed molds to create custom phone cases, kitchen utensils, and wearable technology components.
Jewelry and Fashion
In the jewelry and fashion industries, 3D printing is used to create molds for intricate and unique designs. Jewelry designers can produce custom molds for casting precious metals, allowing for personalized and complex pieces that would be difficult to achieve with traditional methods. Similarly, fashion designers use 3D printed molds to create accessories and embellishments for garments.
Future Trends and Developments
Advancements in Materials
Ongoing research and development in 3D printing materials are expected to address many of the current limitations. New materials with improved strength, durability, and heat resistance are being developed, which will expand the range of applications for 3D printed molds. Additionally, multi-material printing technology is advancing, allowing for the creation of molds with complex material properties.
Integration with Traditional Manufacturing
The integration of 3D printing with traditional manufacturing methods is becoming more common. Hybrid manufacturing approaches combine the strengths of both techniques, using 3D printing for complex and customized parts while leveraging traditional methods for high-volume production. This integration can optimize production processes, reduce costs, and improve overall efficiency.
Improved Precision and Accuracy
As 3D printing technology continues to evolve, improvements in precision and accuracy are expected. Enhanced printer capabilities, better control software, and advanced calibration techniques will contribute to more reliable and consistent results. These advancements will make 3D printing a more viable option for applications requiring high precision and repeatability.
Sustainable Manufacturing
Sustainability is a growing concern in the manufacturing industry, and 3D printing has the potential to contribute to more sustainable practices. The reduction of material waste, energy-efficient production processes, and the ability to produce on-demand are all factors that can lead to a smaller environmental footprint. Continued advancements in sustainable materials and practices will further enhance the environmental benefits of 3D printing.
Digital Supply Chain
The adoption of digital supply chains is expected to accelerate with the growth of 3D printing. Digital design files can be easily shared and transmitted, allowing for decentralized production and reducing the need for physical inventory. This digital approach can improve supply chain flexibility, reduce lead times, and enhance responsiveness to market demands.
Conclusion
3D printing technology has introduced significant advantages in the field of mold making, offering cost savings, speed, design flexibility, and customization opportunities. However, it also presents challenges such as material limitations, surface finish quality, and size constraints. Despite these drawbacks, the continued advancements in 3D printing technology and materials are likely to address many of these issues, making it an increasingly viable option for a wide range of applications.
The impact of 3D printing on mold making is evident across various industries, from automotive and aerospace to healthcare and consumer goods. As the technology continues to evolve, it is expected to play an even more prominent role in the manufacturing landscape, driving innovation, efficiency, and sustainability in mold production.
Reprint Statement: If there are no special instructions, all articles on this site are original. Please indicate the source for reprinting:https://www.cncmachiningptj.com/,thanks!
3, 4 and 5-axis precision CNC machining services for aluminum machining, beryllium, carbon steel, magnesium, titanium machining, Inconel, platinum, superalloy, acetal, polycarbonate, fiberglass, graphite and wood. Capable of machining parts up to 98 in. turning dia. and +/-0.001 in. straightness tolerance. Processes include milling, turning, drilling, boring, threading, tapping, forming, knurling, counterboring, countersinking, reaming and laser cutting. Secondary services such as assembly, centerless grinding, heat treating, plating and welding. Prototype and low to high volume production offered with maximum 50,000 units. Suitable for fluid power, pneumatics, hydraulics and valve applications. Serves the aerospace, aircraft, military, medical and defense industries.PTJ will strategize with you to provide the most cost-effective services to help you reach your target,Welcome to Contact us ( sales@pintejin.com ) directly for your new project.
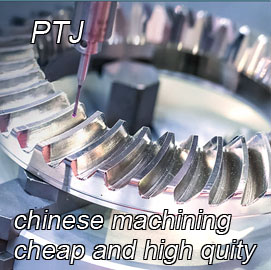
- 5 Axis Machining
- Cnc Milling
- Cnc Turning
- Machining Industries
- Machining Process
- Surface Treatment
- Metal Machining
- Plastic Machining
- Powder Metallurgy Mold
- Die Casting
- Parts Gallery
- Auto Metal Parts
- Machinery Parts
- LED Heatsink
- Building Parts
- Mobile Parts
- Medical Parts
- Electronic Parts
- Tailored Machining
- Bicycle Parts
- Aluminum Machining
- Titanium Machining
- Stainless Steel Machining
- Copper Machining
- Brass Machining
- Super Alloy Machining
- Peek Machining
- UHMW Machining
- Unilate Machining
- PA6 Machining
- PPS Machining
- Teflon Machining
- Inconel Machining
- Tool Steel Machining
- More Material