Aluminum-Based Castings in the Automotive Sector
Aluminum-based castings have become a pivotal component in the automotive sector, driven by the need for lightweight, high-performance, and fuel-efficient vehicles. The versatility of aluminum, combined with advancements in casting technologies, has revolutionized automotive manufacturing. This comprehensive article delves into the history, types, processes, applications, advantages, and future trends of aluminum-based castings in the automotive industry.
History of Aluminum in the Automotive Sector
The use of aluminum in the automotive sector dates back to the late 19th and early 20th centuries. Early automotive pioneers recognized the potential of aluminum due to its favorable properties such as low density and high strength-to-weight ratio. In 1899, the first car with an aluminum body was produced by the French carmaker, Renault. However, it wasn't until the mid-20th century that aluminum began to gain significant traction in automotive manufacturing.
Mid-20th Century Developments
During World War II, the demand for lightweight and durable materials surged, leading to increased use of aluminum in military vehicles. Post-war, the automotive industry adopted these advancements, integrating aluminum in various components to enhance performance and fuel efficiency. By the 1970s and 1980s, with growing concerns over fuel economy and emissions, aluminum's role in automotive manufacturing became more pronounced.
Modern Era and Technological Advancements
In recent decades, the automotive sector has witnessed a surge in the use of aluminum due to advancements in casting technologies, materials science, and manufacturing processes. The rise of electric vehicles (EVs) and stringent environmental regulations have further accelerated the adoption of aluminum-based castings. Today, aluminum is a cornerstone material in the production of modern, high-performance automobiles.
Types of Aluminum-Based Castings
Sand Casting
Sand casting is one of the oldest and most versatile methods for producing aluminum-based components. It involves creating a mold from sand and pouring molten aluminum into the cavity. Sand casting is suitable for producing large and complex parts with high dimensional accuracy.
Die Casting
Die casting is a highly efficient process that involves injecting molten aluminum into a steel mold under high pressure. This method is ideal for producing high-volume, intricate components with excellent surface finish and dimensional accuracy. There are two main types of die casting: hot chamber and cold chamber, each suitable for different aluminum alloys and component requirements.
Permanent Mold Casting
Permanent mold casting, also known as gravity die casting, involves pouring molten aluminum into a reusable metal mold. This process is advantageous for producing medium to high-volume parts with consistent quality and mechanical properties. Permanent mold casting is commonly used for manufacturing engine blocks, cylinder heads, and other critical components.
Investment Casting
Investment casting, or lost-wax casting, is a precision casting process used to produce intricate and detailed aluminum components. The process involves creating a wax pattern, coating it with a ceramic shell, and then melting the wax to create a mold. Molten aluminum is then poured into the mold to form the final component. Investment casting is ideal for producing small, complex parts with tight tolerances.
Squeeze Casting
Squeeze casting combines the advantages of casting and forging to produce high-strength aluminum components. In this process, molten aluminum is poured into a preheated mold and then subjected to high pressure, solidifying the metal and improving its mechanical properties. Squeeze casting is used for producing structural and safety-critical components in the automotive sector.
Manufacturing Processes
Alloy Selection
The selection of aluminum alloys is a critical step in the casting process, as it determines the mechanical properties, machinability, and corrosion resistance of the final component. Commonly used aluminum alloys in automotive castings include A356, A380, and 6061. Each alloy offers unique properties tailored to specific applications.
Mold Design and Fabrication
Mold design is a crucial aspect of the casting process, influencing the quality, dimensional accuracy, and performance of the final component. Advanced computer-aided design (CAD) software is used to create precise mold geometries, ensuring optimal material flow and solidification. The fabrication of molds involves machining and assembling various mold components, including cores and cavities.
Melting and Pouring
The melting of aluminum alloys is carried out in furnaces, such as electric induction furnaces, crucible furnaces, or reverberatory furnaces. The molten aluminum is then transferred to the mold using ladles or automated pouring systems. Temperature control and degassing techniques are employed to ensure the purity and quality of the molten aluminum.
Solidification and Cooling
The solidification and cooling of aluminum castings are critical steps that determine the microstructure and mechanical properties of the final component. Controlled cooling rates and solidification parameters are employed to minimize defects such as porosity and shrinkage. In some cases, post-casting heat treatments are applied to enhance the material properties.
Finishing and Inspection
Once the castings are solidified and cooled, they undergo various finishing operations, including trimming, deburring, and machining. Surface treatments such as shot blasting, anodizing, or painting may be applied to improve aesthetics and corrosion resistance. Non-destructive testing (NDT) methods, such as X-ray inspection and ultrasonic testing, are used to detect internal defects and ensure the quality of the castings.
Applications of Aluminum-Based Castings in Automotives
Engine Components
Aluminum-based castings are extensively used in the production of engine components, including engine blocks, cylinder heads, pistons, and intake manifolds. The lightweight and high thermal conductivity of aluminum contribute to improved engine performance, fuel efficiency, and reduced emissions.
Transmission Systems
Transmission components, such as housings, cases, and gears, benefit from the use of aluminum castings. The high strength-to-weight ratio of aluminum reduces the overall weight of the transmission system, enhancing vehicle performance and fuel economy.
Chassis and Suspension
Aluminum castings are employed in the manufacturing of chassis and suspension components, including control arms, cross members, and subframes. The use of aluminum reduces the weight of the vehicle, improving handling, ride comfort, and overall stability.
Wheels and Brakes
Aluminum castings are widely used in the production of wheels and brake components. Aluminum wheels offer a combination of lightweight, strength, and aesthetic appeal, while aluminum brake calipers and rotors provide excellent heat dissipation and braking performance.
Body Structures
The use of aluminum castings in body structures has increased significantly in recent years. Structural components such as front and rear cradles, door frames, and roof rails benefit from the lightweight and high-strength properties of aluminum, contributing to improved safety and fuel efficiency.
Electric Vehicles
The rise of electric vehicles (EVs) has further accelerated the demand for aluminum-based castings. EV components such as battery housings, motor housings, and structural frames utilize aluminum to enhance energy efficiency, reduce weight, and improve overall performance.
Advantages of Aluminum-Based Castings
Lightweight
The primary advantage of aluminum-based castings is their lightweight nature. Aluminum's low density significantly reduces the weight of automotive components, leading to improved fuel efficiency, reduced emissions, and enhanced vehicle performance.
High Strength-to-Weight Ratio
Aluminum alloys offer a high strength-to-weight ratio, making them ideal for applications requiring both strength and weight reduction. This property is particularly beneficial in structural and safety-critical components.
Corrosion Resistance
Aluminum exhibits excellent corrosion resistance, which is essential for automotive components exposed to harsh environments. The formation of a natural oxide layer on the surface of aluminum provides protection against corrosion and extends the lifespan of the components.
Thermal Conductivity
Aluminum's high thermal conductivity is advantageous for heat dissipation in engine and brake components. This property helps maintain optimal operating temperatures and prevents overheating, improving the overall performance and reliability of the vehicle.
Recyclability
Aluminum is highly recyclable, making it an environmentally friendly choice for automotive manufacturing. The recycling of aluminum requires significantly less energy compared to primary production, reducing the carbon footprint and promoting sustainability.
Design Flexibility
Aluminum-based castings offer excellent design flexibility, allowing for the production of complex and intricate components. Advanced casting techniques and computer-aided design (CAD) software enable the creation of lightweight, high-performance parts with precise geometries.
Cost-Effectiveness
Advancements in casting technologies and the widespread availability of aluminum alloys have made aluminum-based castings a cost-effective solution for automotive manufacturing. The combination of material properties, manufacturing efficiency, and recyclability contributes to overall cost savings.
Challenges and Limitations
Material Costs
Despite the advantages, aluminum can be more expensive than traditional materials like steel. The cost of aluminum alloys and the complexity of the casting processes can impact the overall production costs, particularly for high-volume manufacturing.
Casting Defects
Aluminum casting processes are susceptible to various defects, including porosity, shrinkage, and hot tearing. These defects can affect the quality and performance of the final components, requiring stringent quality control measures and advanced inspection techniques.
Mechanical Properties
While aluminum offers a high strength-to-weight ratio, its mechanical properties can vary depending on the alloy composition and casting process. Ensuring consistent mechanical properties and performance across different components can be challenging.
Machinability
Aluminum castings often require secondary machining operations to achieve the desired dimensions and surface finish. The machinability of aluminum alloys can vary, impacting the efficiency and cost of the manufacturing process.
Joining Techniques
Joining aluminum components, such as welding and adhesive bonding, can present challenges due to the material's thermal conductivity and oxide layer formation. Specialized joining techniques and processes are required to ensure reliable and durable connections.
Future Trends and Innovations
Advanced Alloys
The development of advanced aluminum alloys with enhanced mechanical properties, heat resistance, and corrosion resistance is a key area of research. New alloy compositions and treatments are being explored to meet the evolving demands of the automotive sector.
Additive Manufacturing
Additive manufacturing, or 3D printing, is revolutionizing the production of aluminum-based castings. This technology enables the creation of complex and lightweight components with minimal material waste, offering significant advantages in prototyping and low-volume production.
Lightweighting Initiatives
The automotive industry continues to focus on lightweighting initiatives to improve fuel efficiency and reduce emissions. Aluminum-based castings play a crucial role in achieving these goals, and further advancements in casting technologies are expected to drive lightweighting efforts.
Electric and Autonomous Vehicles
The rise of electric and autonomous vehicles presents new opportunities and challenges for aluminum-based castings. The demand for lightweight, high-performance components in EVs and the integration of advanced sensors and electronics in autonomous vehicles are driving innovation in aluminum casting technologies.
Sustainability and Circular Economy
Sustainability and the circular economy are becoming increasingly important in the automotive sector. The recyclability of aluminum and the development of sustainable manufacturing practices are key trends shaping the future of aluminum-based castings. Efforts to reduce energy consumption, minimize waste, and promote recycling are driving innovation in this field.
Conclusion
Aluminum-based castings have become an integral part of the automotive sector, offering numerous advantages such as lightweight, high strength-to-weight ratio, corrosion resistance, and thermal conductivity. The versatility of aluminum, combined with advancements in casting technologies, has revolutionized automotive manufacturing. Despite challenges such as material costs and casting defects, the future of aluminum-based castings in the automotive industry looks promising, driven by innovations in materials science, manufacturing processes, and sustainability initiatives. As the automotive sector continues to evolve, aluminum-based castings will play a crucial role in shaping the future of high-performance, fuel-efficient, and environmentally friendly vehicles.
Reprint Statement: If there are no special instructions, all articles on this site are original. Please indicate the source for reprinting:https://www.cncmachiningptj.com/,thanks!
3, 4 and 5-axis precision CNC machining services for aluminum machining, beryllium, carbon steel, magnesium, titanium machining, Inconel, platinum, superalloy, acetal, polycarbonate, fiberglass, graphite and wood. Capable of machining parts up to 98 in. turning dia. and +/-0.001 in. straightness tolerance. Processes include milling, turning, drilling, boring, threading, tapping, forming, knurling, counterboring, countersinking, reaming and laser cutting. Secondary services such as assembly, centerless grinding, heat treating, plating and welding. Prototype and low to high volume production offered with maximum 50,000 units. Suitable for fluid power, pneumatics, hydraulics and valve applications. Serves the aerospace, aircraft, military, medical and defense industries.PTJ will strategize with you to provide the most cost-effective services to help you reach your target,Welcome to Contact us ( sales@pintejin.com ) directly for your new project.
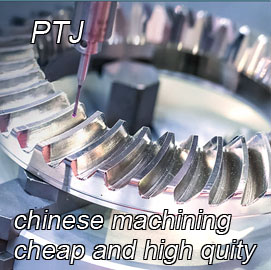
- 5 Axis Machining
- Cnc Milling
- Cnc Turning
- Machining Industries
- Machining Process
- Surface Treatment
- Metal Machining
- Plastic Machining
- Powder Metallurgy Mold
- Die Casting
- Parts Gallery
- Auto Metal Parts
- Machinery Parts
- LED Heatsink
- Building Parts
- Mobile Parts
- Medical Parts
- Electronic Parts
- Tailored Machining
- Bicycle Parts
- Aluminum Machining
- Titanium Machining
- Stainless Steel Machining
- Copper Machining
- Brass Machining
- Super Alloy Machining
- Peek Machining
- UHMW Machining
- Unilate Machining
- PA6 Machining
- PPS Machining
- Teflon Machining
- Inconel Machining
- Tool Steel Machining
- More Material