Failure Forms of Aluminum Die Casting Molds and Material Selection
Aluminum die casting is a versatile and widely used manufacturing process that involves forcing molten aluminum into a mold cavity under high pressure. This method is employed to produce complex and precise metal parts, offering benefits such as excellent dimensional accuracy, high production rates, and the ability to create intricate shapes with smooth surfaces. However, the quality and durability of the molds used in die casting play a crucial role in determining the efficiency and overall success of the process.
Die casting molds, also known as dies, are subjected to extreme conditions, including high temperatures, intense pressures, and rapid cooling cycles. These conditions can lead to various forms of failure, which can significantly impact the productivity, quality, and cost-effectiveness of the die casting operation. Understanding the different failure forms of aluminum die casting molds and the appropriate material selection is essential for improving mold performance and longevity.
This article aims to provide a comprehensive overview of the failure forms of aluminum die casting molds and discuss the factors influencing material selection. By examining the causes, examples, and mitigation strategies for each failure form, as well as exploring the properties and benefits of different mold materials, this article will serve as a valuable resource for professionals in the die casting industry.
Failure Forms of Aluminum Die Casting Molds
Introduction to Failure Forms
Aluminum die casting molds can experience various types of failures due to the demanding operating conditions they endure. These failures can be categorized into several main forms, each with distinct causes and characteristics. Understanding these failure forms is crucial for diagnosing problems, implementing preventive measures, and selecting appropriate materials to enhance mold performance and longevity.
Thermal Fatigue Cracking
Causes
Thermal fatigue cracking, also known as heat checking, is one of the most common failure forms in aluminum die casting molds. It occurs due to the cyclic thermal stresses induced by the repeated heating and cooling of the mold during the casting process. When molten aluminum is injected into the mold cavity, the surface of the mold experiences a rapid temperature rise, followed by a rapid cooling cycle when the casting solidifies and is ejected. This continuous thermal cycling causes the mold material to expand and contract repeatedly, leading to the initiation and propagation of cracks on the mold surface.
Examples
An example of thermal fatigue cracking can be seen in the formation of fine, network-like cracks on the surface of the mold cavity. These cracks typically start as small fissures and gradually expand over time with each casting cycle. If left unchecked, thermal fatigue cracks can deepen and spread, eventually compromising the structural integrity of the mold and leading to premature failure.
Mitigation
To mitigate thermal fatigue cracking, several strategies can be employed:
- Material Selection: Choosing mold materials with high thermal conductivity and low coefficients of thermal expansion can help reduce thermal stresses. Materials such as H13 tool steel are commonly used for their excellent thermal fatigue resistance.
- Surface Treatments: Applying surface treatments like nitriding or PVD (Physical Vapor Deposition) coatings can enhance the surface hardness and reduce the initiation of cracks.
- Optimized Cooling: Implementing effective cooling systems within the mold design can help control the temperature fluctuations and reduce thermal stresses.
- Regular Maintenance: Periodic inspection and maintenance of molds can help detect early signs of thermal fatigue cracking and allow for timely repairs or replacements.
Erosion
Causes
Erosion is a failure form that occurs due to the abrasive action of the molten aluminum against the mold surface. During the injection process, the high-velocity flow of molten metal can cause mechanical wear and material removal from the mold surface. This phenomenon is particularly prevalent in areas with complex geometries or sharp corners, where the molten aluminum flow is turbulent and concentrated.
Examples
Erosion can manifest as localized material loss and surface roughening in the mold cavity. Over time, the eroded areas can lead to dimensional inaccuracies in the cast parts, affecting their quality and requiring frequent mold repairs or replacements.
Mitigation
To mitigate erosion, the following measures can be implemented:
- Material Selection: Using erosion-resistant materials such as high-hardness tool steels or surface-hardened alloys can improve the mold's resistance to abrasive wear.
- Surface Coatings: Applying protective coatings, such as ceramic or diamond-like carbon (DLC) coatings, can enhance the mold's surface hardness and reduce erosion.
- Flow Optimization: Designing the mold with smooth and streamlined flow paths can minimize turbulence and reduce the abrasive impact of the molten aluminum.
- Maintenance and Repair: Regularly inspecting and repairing eroded areas can help maintain mold performance and extend its service life.
Corrosion
Causes
Corrosion is a chemical degradation process that occurs when the mold material reacts with the molten aluminum or the surrounding environment. The high temperatures and reactive nature of molten aluminum can lead to the formation of aluminum oxides or other corrosive compounds on the mold surface. Additionally, exposure to moisture or other contaminants can accelerate the corrosion process.
Examples
Corrosion can appear as pitting, discoloration, or the formation of oxide layers on the mold surface. These corrosive effects can degrade the surface finish of the mold cavity, leading to casting defects and reduced mold life.
Mitigation
To mitigate corrosion, the following strategies can be employed:
- Material Selection: Choosing corrosion-resistant materials, such as stainless steels or nickel-based alloys, can help reduce the susceptibility to chemical reactions.
- Protective Coatings: Applying anti-corrosion coatings, such as chromium or nickel plating, can create a barrier between the mold material and the corrosive environment.
- Environmental Control: Implementing proper environmental controls, such as reducing humidity levels and minimizing exposure to corrosive agents, can help mitigate corrosion.
- Regular Maintenance: Periodic cleaning and maintenance of molds can prevent the buildup of corrosive compounds and extend the mold's service life.
Soldering
Causes
Soldering, also known as sticking, occurs when molten aluminum adheres to the mold surface and solidifies, forming a bond between the casting and the mold. This can happen due to several factors, including high temperatures, inadequate mold coatings, or improper mold lubrication. Soldering can lead to difficulties in ejecting the cast part and can damage the mold surface during part removal.
Examples
Soldering can manifest as localized bonding of the cast part to the mold surface, making it challenging to release the part without causing damage. This can result in surface defects on the cast part and increased wear on the mold.
Mitigation
To mitigate soldering, the following measures can be implemented:
- Mold Coatings: Applying mold coatings with anti-soldering properties, such as ceramic or boron nitride coatings, can prevent the molten aluminum from adhering to the mold surface.
- Proper Lubrication: Using appropriate mold lubricants can create a barrier between the molten aluminum and the mold surface, reducing the likelihood of soldering.
- Temperature Control: Maintaining optimal mold temperatures can prevent excessive heating that can promote soldering.
- Ejection System Design: Designing an effective ejection system can facilitate smooth part removal and reduce the risk of soldering-related damage.
Mechanical Fatigue
Causes
Mechanical fatigue occurs due to the repeated application of mechanical stresses during the die casting process. The cyclic loading and unloading of the mold, coupled with the high pressures involved, can lead to the initiation and propagation of fatigue cracks. Mechanical fatigue is often exacerbated by stress concentrations, such as sharp corners or notches, in the mold design.
Examples
Mechanical fatigue can manifest as the formation of cracks or fractures in the mold, particularly in areas subjected to high mechanical stresses. These cracks can compromise the structural integrity of the mold, leading to premature failure and requiring mold repairs or replacements.
Mitigation
To mitigate mechanical fatigue, the following measures can be implemented:
- Material Selection: Choosing materials with high fatigue resistance, such as tool steels with excellent toughness and strength, can improve the mold's ability to withstand cyclic loading.
- Design Optimization: Implementing design features that minimize stress concentrations, such as rounded corners and smooth transitions, can reduce the likelihood of fatigue crack initiation.
- Surface Treatments: Applying surface treatments, such as shot peening or nitriding, can enhance the surface hardness and fatigue resistance of the mold.
- Regular Inspection: Conducting regular inspections to detect early signs of fatigue cracks and performing timely repairs can prevent further propagation and extend the mold's service life.
Distortion and Warping
Causes
Distortion and warping can occur due to uneven thermal expansion and contraction during the die casting process. The rapid heating and cooling cycles can induce thermal stresses in the mold, leading to dimensional changes and deformation. Additionally, improper mold design or inadequate cooling systems can exacerbate these issues.
Examples
Distortion and warping can manifest as dimensional inaccuracies in the mold cavity, leading to defects in the cast parts. These deformations can affect the overall quality and precision of the die cast components.
Mitigation
To mitigate distortion and warping, the following measures can be implemented:
- Material Selection: Using materials with low coefficients of thermal expansion and high thermal stability can help reduce the susceptibility to distortion and warping.
- Cooling System Design: Implementing an efficient and uniform cooling system within the mold can help control temperature gradients and minimize thermal stresses.
- Stress Relieving: Conducting stress-relieving heat treatments on the mold material can help reduce residual stresses and improve dimensional stability.
- Design Considerations: Incorporating design features that account for thermal expansion and contraction can help minimize distortion and warping.
Surface Defects
Causes
Surface defects in aluminum die casting molds can arise from various factors, including improper mold maintenance, inadequate surface treatments, and suboptimal casting parameters. These defects can negatively impact the surface finish and quality of the cast parts.
Examples
Surface defects can appear as roughness, pitting, or irregularities on the mold cavity surface. These imperfections can transfer to the cast parts, leading to cosmetic and functional issues.
Mitigation
To mitigate surface defects, the following measures can be implemented:
- Surface Treatments: Applying surface treatments such as polishing, coating, or texturing can enhance the surface finish and reduce the occurrence of defects.
- Regular Maintenance: Conducting regular maintenance and cleaning of the mold can prevent the buildup of contaminants and debris that can cause surface defects.
- Optimized Casting Parameters: Adjusting casting parameters, such as injection speed and temperature, can help achieve a smooth and defect-free surface.
- Quality Control: Implementing stringent quality control measures during mold manufacturing and maintenance can ensure a high-quality mold surface.
General Wear
Causes
General wear is a gradual degradation process that occurs due to the repetitive use of the mold in the die casting process. Factors such as high pressures, abrasive materials, and frequent thermal cycling contribute to the overall wear and tear of the mold.
Examples
General wear can manifest as surface roughening, dimensional changes, and loss of detail in the mold cavity. Over time, this wear can affect the quality and precision of the cast parts, requiring mold refurbishment or replacement.
Mitigation
To mitigate general wear, the following measures can be implemented:
- Material Selection: Choosing durable and wear-resistant materials, such as high-hardness tool steels, can improve the mold's longevity and resistance to wear.
- Surface Coatings: Applying wear-resistant coatings, such as titanium nitride or chromium carbide, can enhance the mold's surface hardness and reduce wear.
- Regular Maintenance: Implementing a routine maintenance schedule, including inspection, cleaning, and lubrication, can help extend the mold's service life.
- Design Optimization: Designing the mold with features that distribute wear evenly and reduce stress concentrations can help minimize general wear.
Material Selection for Aluminum Die Casting Molds
Overview of Material Requirements
Selecting the appropriate material for aluminum die casting molds is crucial for ensuring mold performance, durability, and cost-effectiveness. The chosen material must withstand the demanding conditions of the die casting process, including high temperatures, mechanical stresses, and corrosive environments. Key material requirements for die casting molds include:
- Thermal Conductivity: High thermal conductivity is essential for efficient heat transfer and rapid cooling of the mold.
- Thermal Stability: The material should exhibit low thermal expansion and good dimensional stability under varying temperatures.
- Mechanical Strength: High mechanical strength and toughness are necessary to withstand the high pressures and cyclic loading during the casting process.
- Wear Resistance: The material should resist abrasive wear and erosion caused by the molten aluminum flow.
- Corrosion Resistance: Resistance to chemical reactions with molten aluminum and environmental factors is important for preventing corrosion.
- Machinability: The material should be easy to machine and fabricate into complex mold shapes.
- Cost-Effectiveness: The material should offer a balance between performance and cost, considering the overall economics of the die casting process.
Steel Alloys
Types of Steel Used
Steel alloys are commonly used for aluminum die casting molds due to their excellent mechanical properties, thermal stability, and cost-effectiveness. The most widely used steel alloys include:
- H13 Tool Steel: Known for its high hardness, toughness, and thermal fatigue resistance, H13 tool steel is a popular choice for die casting molds. It offers excellent wear resistance and can withstand high temperatures without losing its strength.
- P20 Tool Steel: P20 tool steel is a versatile alloy with good machinability and toughness. It is often used for molds requiring moderate strength and wear resistance.
- 420 Stainless Steel: This stainless steel alloy offers excellent corrosion resistance and good mechanical properties. It is suitable for molds exposed to corrosive environments.
- A2 Tool Steel: A2 tool steel provides a good balance of toughness, wear resistance, and machinability. It is used for molds requiring high dimensional stability and precision.
Properties and Benefits
Steel alloys offer several properties and benefits for aluminum die casting molds:
- High Hardness and Strength: Steel alloys provide excellent hardness and strength, enabling the mold to withstand high pressures and mechanical stresses.
- Thermal Stability: Steel alloys exhibit good thermal stability, minimizing distortion and warping during the casting process.
- Wear Resistance: The high hardness and toughness of steel alloys enhance their resistance to abrasive wear and erosion.
- Corrosion Resistance: Certain steel alloys, such as stainless steel, offer good corrosion resistance, protecting the mold from chemical reactions with molten aluminum.
- Cost-Effectiveness: Steel alloys are relatively cost-effective compared to other high-performance materials, making them a practical choice for die casting molds.
Examples of Applications
Steel alloys are used in various applications within the die casting industry:
- Automotive Components: H13 tool steel molds are commonly used for casting engine blocks, transmission cases, and other critical automotive components.
- Consumer Electronics: Steel molds are used for producing housings and structural components for consumer electronic devices.
- Aerospace Parts: P20 tool steel molds are used for casting lightweight and high-precision aerospace components.
Copper Alloys
Types of Copper Alloys Used
Copper alloys are utilized in die casting molds for their excellent thermal conductivity and corrosion resistance. The most commonly used copper alloys include:
- Beryllium Copper: This alloy combines high strength with excellent thermal conductivity and corrosion resistance. It is used in applications requiring superior heat dissipation and precision.
- Bronze Alloys: Various bronze alloys, such as aluminum bronze and silicon bronze, offer good mechanical properties and wear resistance, making them suitable for specific mold components.
Properties and Benefits
Copper alloys provide several properties and benefits for die casting molds:
- High Thermal Conductivity: Copper alloys offer exceptional thermal conductivity, enabling rapid heat transfer and efficient cooling of the mold.
- Corrosion Resistance: Copper alloys exhibit excellent resistance to corrosion, preventing chemical reactions with molten aluminum and extending mold life.
- Machinability: Copper alloys are relatively easy to machine, allowing for the fabrication of complex mold shapes with high precision.
- Wear Resistance: Certain copper alloys, such as beryllium copper, offer good wear resistance, enhancing the mold's durability.
Examples of Applications
Copper alloys are used in various applications within the die casting industry:
- Cooling Inserts: Beryllium copper inserts are used in die casting molds to improve heat dissipation and reduce cycle times.
- Core Pins: Copper alloy core pins are employed in molds requiring precise cooling and dimensional stability.
- Ejector Sleeves: Copper alloy ejector sleeves provide improved wear resistance and corrosion protection in high-stress mold components.
Nickel Alloys
Types of Nickel Alloys Used
Nickel alloys are employed in die casting molds for their excellent mechanical properties, thermal stability, and corrosion resistance. The most commonly used nickel alloys include:
- Inconel: Inconel alloys, such as Inconel 718 and Inconel 625, offer high strength, excellent thermal stability, and resistance to oxidation and corrosion. They are used in molds subjected to extreme temperatures and harsh environments.
- Monel: Monel alloys, such as Monel 400, provide good mechanical properties, corrosion resistance, and thermal conductivity. They are suitable for specific mold components requiring these characteristics.
Properties and Benefits
Nickel alloys offer several properties and benefits for die casting molds:
- High Strength and Toughness: Nickel alloys provide excellent mechanical strength and toughness, enabling the mold to withstand high pressures and mechanical stresses.
- Thermal Stability: Nickel alloys exhibit good thermal stability, minimizing distortion and warping during the casting process.
- Corrosion Resistance: Nickel alloys offer excellent resistance to corrosion, protecting the mold from chemical reactions with molten aluminum and harsh environments.
- Oxidation Resistance: Certain nickel alloys, such as Inconel, provide superior resistance to oxidation at high temperatures, extending mold life.
Examples of Applications
Nickel alloys are used in various applications within the die casting industry:
- High-Temperature Molds: Inconel molds are used for casting components subjected to extreme temperatures, such as turbine blades and aerospace parts.
- Corrosive Environments: Monel molds are employed in applications exposed to corrosive environments, such as chemical processing equipment.
- Precision Components: Nickel alloy molds are used for producing high-precision and intricate components requiring superior mechanical properties.
Other Materials
Composite Materials
Composite materials, consisting of a combination of different materials, are gaining traction in the die casting industry due to their unique properties. Examples of composite materials used in die casting molds include:
- Ceramic Matrix Composites (CMCs): CMCs offer high-temperature stability, excellent wear resistance, and low thermal expansion. They are used in applications requiring extreme thermal and mechanical performance.
- Metal Matrix Composites (MMCs): MMCs combine metals with ceramic or other reinforcements, providing enhanced wear resistance, thermal stability, and mechanical strength.
Experimental Materials
Researchers and manufacturers are continuously exploring new materials and coatings to improve the performance and longevity of die casting molds. Some experimental materials being investigated include:
- Advanced Coatings: Development of new coatings with superior wear resistance, anti-soldering properties, and thermal stability.
- Additive Manufacturing: Utilization of additive manufacturing techniques to create molds with complex geometries and tailored material properties.
- Nano-Enhanced Materials: Incorporation of nanomaterials to enhance the mechanical, thermal, and wear properties of mold materials.
Comparative Analysis of Materials
Performance Under Different Conditions
The performance of die casting mold materials varies under different operating conditions. Factors such as temperature, pressure, and exposure to corrosive environments influence the material's behavior and longevity. A comparative analysis of materials based on their performance under different conditions includes:
- Thermal Conductivity: Copper alloys exhibit the highest thermal conductivity, followed by nickel alloys and steel alloys. This property is crucial for efficient heat dissipation and cooling of the mold.
- Thermal Stability: Nickel alloys, such as Inconel, offer superior thermal stability, making them suitable for high-temperature applications. Steel alloys like H13 also provide good thermal stability.
- Mechanical Strength: Steel alloys, particularly H13 and P20, offer high mechanical strength and toughness, making them ideal for molds subjected to high pressures and mechanical stresses.
- Wear Resistance: Steel alloys and certain copper alloys, such as beryllium copper, exhibit excellent wear resistance, enhancing the mold's durability.
- Corrosion Resistance: Nickel alloys, such as CNC Machining Inconel and Monel, provide the best corrosion resistance, followed by stainless steel and copper alloys.
Cost-Effectiveness
The cost-effectiveness of die casting mold materials depends on several factors, including material cost, machining and fabrication costs, and mold longevity. A comparative analysis of materials based on cost-effectiveness includes:
- Steel Alloys: Steel alloys, such as H13 and P20, are relatively cost-effective and offer a good balance between performance and cost. They are widely used in the die casting industry.
- Copper Alloys: Copper alloys, such as beryllium copper, are more expensive than steel alloys but offer superior thermal conductivity and wear resistance. They are used in specific applications requiring these properties.
- Nickel Alloys: Nickel alloys, such as Inconel and Monel, are more expensive than steel and copper alloys. However, their exceptional performance in high-temperature and corrosive environments justifies their cost in certain applications.
- Composite Materials: Composite materials, such as CMCs and MMCs, can be costly due to their specialized properties and manufacturing processes. They are used in applications requiring extreme performance.
Longevity and Maintenance Requirements
The longevity and maintenance requirements of die casting mold materials vary based on their properties and operating conditions. A comparative analysis of materials based on longevity and maintenance includes:
- Steel Alloys: Steel alloys, such as H13 and P20, offer good longevity and require regular maintenance, including surface treatments and inspections, to prevent wear and thermal fatigue.
- Copper Alloys: Copper alloys, such as beryllium copper, provide excellent thermal conductivity and wear resistance, reducing maintenance requirements and extending mold life.
- Nickel Alloys: Nickel alloys, such as Inconel, offer superior thermal stability and corrosion resistance, resulting in longer mold life and reduced maintenance.
- Composite Materials: Composite materials, such as CMCs and MMCs, provide excellent wear resistance and thermal stability, reducing maintenance needs and extending mold life.
Environmental Impact
The environmental impact of die casting mold materials depends on factors such as material extraction, manufacturing processes, and recyclability. A comparative analysis of materials based on environmental impact includes:
- Steel Alloys: Steel alloys have a moderate environmental impact, with significant energy consumption during extraction and manufacturing. However, they are widely recyclable, reducing their overall impact.
- Copper Alloys: Copper alloys also have a moderate environmental impact, with energy-intensive extraction and processing. They are recyclable, but beryllium copper requires careful handling due to its toxicity.
- Nickel Alloys: Nickel alloys have a higher environmental impact due to energy-intensive extraction and processing. However, their long service life and recyclability mitigate some of this impact.
- Composite Materials: Composite materials can have a significant environmental impact due to complex manufacturing processes and limited recyclability. However, their superior performance and extended mold life can offset some of this impact.
Case Studies and Practical Applications
Real-World Examples of Mold Failures
Examining real-world examples of mold failures provides valuable insights into the causes and consequences of different failure forms. Case studies highlight common issues and the effectiveness of mitigation strategies.
- Thermal Fatigue Cracking: A die casting facility experienced frequent thermal fatigue cracking in their molds, leading to premature failures and increased downtime. By switching to H13 tool steel molds with improved thermal fatigue resistance and implementing optimized cooling systems, the facility significantly reduced the occurrence of cracks and extended mold life.
- Erosion: An automotive manufacturer faced erosion issues in their die casting molds, resulting in dimensional inaccuracies and increased maintenance costs. By applying wear-resistant coatings and redesigning the mold with smoother flow paths, the manufacturer reduced erosion and improved the quality of their cast parts.
- Corrosion: A die casting company producing components for a corrosive environment encountered corrosion-related mold failures. By switching to stainless steel molds with anti-corrosion coatings and implementing better environmental controls, the company enhanced mold durability and reduced maintenance needs.
Successful Implementations of Material Selections
Real-world examples of successful material selections demonstrate the benefits of choosing the right materials for die casting molds. Case studies highlight the impact on mold performance, longevity, and cost-effectiveness.
- Steel Alloys in Automotive Components: An automotive manufacturer used H13 tool steel molds for casting engine blocks and transmission cases. The high hardness, toughness, and thermal stability of H13 tool steel provided excellent mold performance, reduced downtime, and improved part quality.
- Copper Alloys in Cooling Inserts: A die casting company utilized beryllium copper inserts in their molds to enhance heat dissipation and reduce cycle times. The superior thermal conductivity of beryllium copper improved cooling efficiency, resulting in faster production and reduced mold wear.
- Nickel Alloys in High-Temperature Molds: An aerospace component manufacturer employed Inconel molds for casting turbine blades subjected to extreme temperatures. The high strength, thermal stability, and oxidation resistance of Inconel ensured the molds' durability and precision, improving the quality and reliability of the cast parts.
Future Trends and Innovations
Advances in Materials Science
Ongoing research and development in materials science are driving innovations in die casting mold materials. Advances include:
- Nanostructured Materials: The development of nanostructured materials with enhanced mechanical, thermal, and wear properties holds promise for improving mold performance and longevity.
- High-Entropy Alloys: High-entropy alloys, composed of multiple principal elements, offer unique properties such as high strength, thermal stability, and corrosion resistance, making them potential candidates for die casting molds.
- Functionally Graded Materials: Functionally graded materials, with tailored properties across their volume, can provide optimized performance for specific mold regions, enhancing overall mold efficiency and durability.
Predictive Maintenance Technologies
The integration of predictive maintenance technologies in die casting operations is revolutionizing mold management. Advances include:
- Sensor Integration: Embedding sensors in molds to monitor temperature, pressure, and wear can provide real-time data for predictive maintenance, reducing downtime and extending mold life.
- Data Analytics: Utilizing data analytics and machine learning algorithms to analyze sensor data and predict mold failures, enabling proactive maintenance and minimizing unexpected breakdowns.
- Digital Twin: Creating digital twins of molds to simulate and analyze their performance under different conditions, optimizing maintenance schedules and improving mold design.
Environmental and Sustainability Considerations
The die casting industry is increasingly focusing on environmental and sustainability considerations. Trends and innovations include:
- Recyclable Materials: Developing and using recyclable materials for die casting molds to reduce environmental impact and promote circular economy practices.
- Eco-Friendly Coatings: Researching and implementing eco-friendly coatings with reduced environmental impact, such as water-based and bio-based coatings.
- Sustainable Manufacturing: Adopting sustainable manufacturing practices, including energy-efficient processes, waste reduction, and responsible sourcing of materials, to minimize the industry's carbon footprint.
Conclusion
Selecting the right materials for aluminum die casting molds is crucial for ensuring mold performance, longevity, and cost-effectiveness. This comprehensive guide has explored the various forms of mold failure, material requirements, and properties, as well as practical applications and future trends. By understanding the strengths and weaknesses of different materials and implementing appropriate mitigation strategies, manufacturers can optimize their die casting operations, improve product quality, and enhance sustainability.
Reprint Statement: If there are no special instructions, all articles on this site are original. Please indicate the source for reprinting:https://www.cncmachiningptj.com/,thanks!
3, 4 and 5-axis precision CNC machining services for aluminum machining, beryllium, carbon steel, magnesium, titanium machining, Inconel, platinum, superalloy, acetal, polycarbonate, fiberglass, graphite and wood. Capable of machining parts up to 98 in. turning dia. and +/-0.001 in. straightness tolerance. Processes include milling, turning, drilling, boring, threading, tapping, forming, knurling, counterboring, countersinking, reaming and laser cutting. Secondary services such as assembly, centerless grinding, heat treating, plating and welding. Prototype and low to high volume production offered with maximum 50,000 units. Suitable for fluid power, pneumatics, hydraulics and valve applications. Serves the aerospace, aircraft, military, medical and defense industries.PTJ will strategize with you to provide the most cost-effective services to help you reach your target,Welcome to Contact us ( sales@pintejin.com ) directly for your new project.
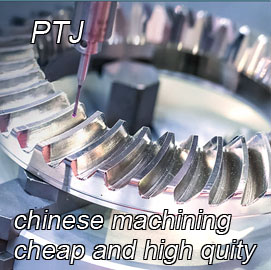
- 5 Axis Machining
- Cnc Milling
- Cnc Turning
- Machining Industries
- Machining Process
- Surface Treatment
- Metal Machining
- Plastic Machining
- Powder Metallurgy Mold
- Die Casting
- Parts Gallery
- Auto Metal Parts
- Machinery Parts
- LED Heatsink
- Building Parts
- Mobile Parts
- Medical Parts
- Electronic Parts
- Tailored Machining
- Bicycle Parts
- Aluminum Machining
- Titanium Machining
- Stainless Steel Machining
- Copper Machining
- Brass Machining
- Super Alloy Machining
- Peek Machining
- UHMW Machining
- Unilate Machining
- PA6 Machining
- PPS Machining
- Teflon Machining
- Inconel Machining
- Tool Steel Machining
- More Material