High-Speed Milling vs. Electrical Discharge Machining (EDM)
High-speed milling and Electrical Discharge Machining (EDM) are two of the most prominent machining processes used in modern manufacturing. Both techniques are integral to the production of high-precision components, each offering unique advantages and specific applications. This article delves into the fundamental principles, advantages, limitations, and applications of high-speed milling and EDM, comparing these two machining processes in various contexts.
High-Speed Milling
High-speed milling (HSM) refers to a machining process that involves the rapid movement of the cutting tool and workpiece. This process is characterized by high cutting speeds, feed rates, and spindle speeds, typically exceeding those used in conventional milling. HSM is widely used in the aerospace, automotive, and mold and die industries due to its efficiency and ability to produce high-quality surface finishes.
Principles of High-Speed Milling
The primary principles of HSM involve the use of high spindle speeds (often exceeding 20,000 RPM), high feed rates, and shallow depth of cut. The process minimizes the cutting force on the tool and workpiece, reducing the heat generation and improving tool life. Advanced machine tool designs, including high-rigidity structures, precision spindles, and sophisticated control systems, are essential for achieving the desired performance in HSM.
Advantages of High-Speed Milling
- Increased Productivity: HSM significantly reduces machining time by allowing higher material removal rates.
- Improved Surface Finish: The high cutting speeds and reduced cutting forces result in superior surface finishes, often eliminating the need for additional finishing operations.
- Enhanced Accuracy: HSM minimizes thermal deformation and vibration, leading to better dimensional accuracy and precision.
- Extended Tool Life: Lower cutting forces and reduced heat generation prolong tool life, reducing the frequency of tool changes and downtime.
- Versatility: HSM is suitable for a wide range of materials, including hard metals, composites, and alloys.
Limitations of High-Speed Milling
- High Initial Investment: The advanced machinery and tooling required for HSM can be expensive.
- Complex Programming: The precision and speed of HSM demand sophisticated CAM programming and skilled operators.
- Tool Wear: Despite the extended tool life, high speeds and feed rates can still lead to significant tool wear, especially with harder materials.
Applications of High-Speed Milling
- Aerospace: Production of complex components with tight tolerances and high surface quality.
- Automotive: Manufacturing of engine parts, molds, and dies.
- Mold and Die Making: Creation of intricate molds with excellent surface finishes.
- Medical Devices: Fabrication of precision components for medical instruments and implants.
Electrical Discharge Machining (EDM)
Electrical Discharge Machining (EDM) is a non-traditional machining process that uses electrical discharges (sparks) to erode material from the workpiece. This process is particularly effective for machining hard materials and complex geometries that are difficult to machine using conventional methods. EDM is extensively used in the aerospace, automotive, and tool and die industries.
Principles of EDM
EDM operates on the principle of spark erosion, where an electrical discharge occurs between the electrode (tool) and the workpiece, both submerged in a dielectric fluid. The discharge generates intense heat, melting and vaporizing a small volume of the workpiece material. The dielectric fluid cools the area and flushes away the eroded particles. There are two main types of EDM: sinker EDM and wire EDM.
- Sinker EDM: Utilizes a shaped electrode that is gradually sunk into the workpiece to produce the desired cavity.
- Wire EDM: Uses a thin, continuously fed wire as the electrode to cut intricate shapes and profiles.
Advantages of EDM
- Machining Hard Materials: EDM can easily machine hard materials like hardened steels, titanium, and carbide that are challenging to cut with traditional methods.
- Complex Geometries: The process excels at producing intricate shapes, fine details, and sharp corners.
- No Mechanical Force: Since there is no physical contact between the tool and workpiece, EDM is suitable for delicate and fragile components.
- High Precision: EDM can achieve high levels of precision and surface finish.
- Versatility: Applicable to a wide range of conductive materials, regardless of hardness.
Limitations of EDM
- Slow Material Removal Rates: EDM is generally slower than conventional machining processes, making it less suitable for high-volume production.
- Electrode Wear: The electrode undergoes wear during the process, necessitating frequent replacements or redressing.
- Dielectric Fluid Maintenance: Proper maintenance and handling of the dielectric fluid are crucial to ensure consistent performance and quality.
- Limited to Conductive Materials: Only conductive materials can be machined using EDM.
Applications of EDM
- Tool and Die Making: Precision machining of dies, molds, and punches.
- Aerospace: Manufacturing of high-precision components with complex geometries.
- Medical Devices: Production of intricate surgical instruments and implants.
- Automotive: Fabrication of high-precision engine components and intricate parts.
Comparative Analysis
Material Removal Rate (MRR)
- High-Speed Milling: Generally offers higher MRR due to high cutting speeds and feed rates. Suitable for roughing operations and bulk material removal.
- EDM: Lower MRR, making it less suitable for high-volume material removal but ideal for finishing operations and precision machining.
Surface Finish and Accuracy
- High-Speed Milling: Achieves excellent surface finishes and high dimensional accuracy, particularly beneficial for finishing operations.
- EDM: Capable of producing superior surface finishes and precise details, especially for complex geometries and fine features.
Tool Wear and Maintenance
- High-Speed Milling: Tool wear is a concern, but advances in tooling materials and coatings have mitigated this issue. Requires regular tool changes and maintenance.
- EDM: Electrode wear is a significant factor, necessitating frequent replacement or redressing. Dielectric fluid maintenance is also crucial.
Flexibility and Versatility
- High-Speed Milling: Versatile across a wide range of materials, including metals, composites, and alloys. Suitable for various operations, from roughing to finishing.
- EDM: Highly versatile for machining hard and conductive materials, capable of producing complex shapes and fine details. Limited to conductive materials only.
Cost and Investment
- High-Speed Milling: High initial investment in machinery and tooling. Operational costs can be offset by increased productivity and efficiency.
- EDM: Generally involves lower initial investment compared to HSM. Operational costs include electrode wear and dielectric fluid maintenance.
Application Suitability
- High-Speed Milling: Ideal for industries requiring high productivity, excellent surface finishes, and precision, such as aerospace, automotive, and mold and die making.
- EDM: Best suited for applications requiring high precision, intricate geometries, and machining of hard materials, such as tool and die making, aerospace, and medical devices.
Conclusion
High-speed milling and Electrical Discharge Machining are both vital machining processes, each with unique strengths and limitations. High-speed milling excels in productivity, surface finish, and versatility across various materials and applications. In contrast, EDM stands out for its ability to machine hard materials, produce complex geometries, and achieve high precision.
Choosing between high-speed milling and EDM depends on several factors, including the material to be machined, the complexity of the geometry, required precision, and production volume. In many cases, manufacturers employ both processes complementarily to leverage their respective advantages, thereby optimizing the production of high-precision components in various industries.
Reprint Statement: If there are no special instructions, all articles on this site are original. Please indicate the source for reprinting:https://www.cncmachiningptj.com/,thanks!
3, 4 and 5-axis precision CNC machining services for aluminum machining, beryllium, carbon steel, magnesium, titanium machining, Inconel, platinum, superalloy, acetal, polycarbonate, fiberglass, graphite and wood. Capable of machining parts up to 98 in. turning dia. and +/-0.001 in. straightness tolerance. Processes include milling, turning, drilling, boring, threading, tapping, forming, knurling, counterboring, countersinking, reaming and laser cutting. Secondary services such as assembly, centerless grinding, heat treating, plating and welding. Prototype and low to high volume production offered with maximum 50,000 units. Suitable for fluid power, pneumatics, hydraulics and valve applications. Serves the aerospace, aircraft, military, medical and defense industries.PTJ will strategize with you to provide the most cost-effective services to help you reach your target,Welcome to Contact us ( sales@pintejin.com ) directly for your new project.
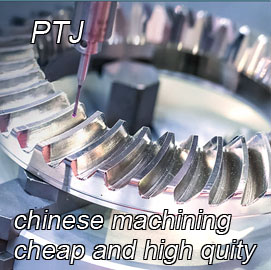
- 5 Axis Machining
- Cnc Milling
- Cnc Turning
- Machining Industries
- Machining Process
- Surface Treatment
- Metal Machining
- Plastic Machining
- Powder Metallurgy Mold
- Die Casting
- Parts Gallery
- Auto Metal Parts
- Machinery Parts
- LED Heatsink
- Building Parts
- Mobile Parts
- Medical Parts
- Electronic Parts
- Tailored Machining
- Bicycle Parts
- Aluminum Machining
- Titanium Machining
- Stainless Steel Machining
- Copper Machining
- Brass Machining
- Super Alloy Machining
- Peek Machining
- UHMW Machining
- Unilate Machining
- PA6 Machining
- PPS Machining
- Teflon Machining
- Inconel Machining
- Tool Steel Machining
- More Material