Surface Finishing Technology of Magnesium Alloys
Magnesium alloys, known for their remarkable properties such as low density, high specific strength, and excellent machinability, are becoming increasingly popular in various high-performance applications. Despite these advantages, magnesium alloys are highly reactive, making them prone to corrosion when exposed to environmental elements. This susceptibility necessitates the use of effective surface finishing technologies to enhance the durability, aesthetics, and functionality of magnesium components. This article delves into the various surface finishing techniques used for magnesium alloys, exploring their mechanisms, benefits, and industrial applications.
Surface finishing is a crucial process in the manufacturing of magnesium alloy components, aimed at improving their surface properties and extending their service life. The main goals of surface finishing include enhancing corrosion resistance, improving wear resistance, providing aesthetic appeal, and preparing surfaces for subsequent coating or painting. The selection of a suitable surface finishing technique depends on the specific application requirements, environmental conditions, and the desired performance characteristics.
History and Development
Early Uses and Limitations of Magnesium Alloys
The utilization of magnesium dates back to the early 19th century when it was first isolated and identified as a distinct element. Early applications of magnesium and its alloys were limited due to the metal's high reactivity and susceptibility to corrosion. Despite these challenges, magnesium alloys found use in military and aerospace applications during the early 20th century, primarily due to their lightweight nature, which offered significant advantages in reducing the weight of aircraft and military equipment.
Evolution of Surface Finishing Techniques
The development of surface finishing techniques for magnesium alloys has been driven by the need to overcome their inherent limitations, particularly their tendency to corrode. Early methods focused on basic mechanical and chemical treatments to prepare surfaces for further coating applications. As technology advanced, more sophisticated techniques such as anodizing, electroplating, and conversion coatings were developed to provide better protection and enhanced surface properties.
Modern Advancements and Industrial Adoption
In recent decades, significant advancements have been made in surface finishing technologies for magnesium alloys. The introduction of environmentally friendly and high-performance coatings, along with the development of novel surface treatment processes, has expanded the use of magnesium alloys in various industries. Today, magnesium alloys are extensively used in the automotive, aerospace, electronics, and biomedical sectors, where their lightweight and high-strength properties are highly valued.
Properties of Magnesium Alloys
Chemical Composition
Magnesium alloys are typically composed of magnesium as the base metal, with various alloying elements added to improve their properties. Common alloying elements include aluminum, zinc, manganese, silicon, and rare earth metals. These alloying elements influence the mechanical, physical, and corrosion properties of the magnesium alloys, allowing for the development of materials tailored to specific applications.
Physical and Mechanical Properties
Magnesium alloys are known for their low density, which is approximately two-thirds that of aluminum and one-quarter that of steel. This characteristic makes magnesium alloys ideal for applications where weight reduction is critical. Additionally, magnesium alloys exhibit high specific strength, good castability, and excellent machinability. However, they also possess lower ductility and toughness compared to other engineering materials, which can limit their use in certain applications.
Corrosion Behavior and Challenges
One of the primary challenges associated with magnesium alloys is their susceptibility to corrosion. Magnesium is highly reactive and readily forms magnesium hydroxide when exposed to moisture, leading to rapid degradation of the material. The presence of alloying elements can influence the corrosion behavior, either enhancing or reducing the corrosion resistance. As a result, effective surface finishing techniques are essential to protect magnesium alloys from corrosive environments and extend their service life.
Surface Preparation
Cleaning and Degreasing
Surface preparation is a critical step in the surface finishing process, as it ensures that the substrate is clean and free of contaminants that could affect the adhesion and performance of subsequent coatings. Cleaning and degreasing involve the removal of oils, greases, dirt, and other surface impurities. Various methods, including alkaline cleaning, solvent cleaning, and ultrasonic cleaning, can be employed depending on the nature and extent of the contamination.
Mechanical Treatments: Grinding, Polishing, and Blasting
Mechanical treatments such as grinding, polishing, and blasting are commonly used to prepare the surface of magnesium alloys. Grinding involves the use of abrasive materials to remove surface irregularities and achieve a smooth finish. Polishing further refines the surface, producing a mirror-like appearance and improving the adhesion of subsequent coatings. Blasting, which involves the use of abrasive particles propelled at high velocities, is effective in removing oxides and other surface contaminants.
Chemical Treatments: Etching and Pickling
Chemical treatments such as etching and pickling are used to remove surface oxides and contaminants from magnesium alloys. Etching involves the use of acidic or alkaline solutions to dissolve surface oxides and produce a clean, active surface. Pickling, a specific type of etching, typically employs acid solutions to remove scale, rust, and other impurities. These treatments are essential for enhancing the adhesion of subsequent coatings and ensuring uniform coverage.
Conversion Coatings
Chromate Conversion Coatings
Chromate conversion coatings are widely used for protecting magnesium alloys due to their excellent corrosion resistance and self-healing properties. The process involves the application of a chromate solution to the magnesium surface, resulting in the formation of a protective, adherent film. However, due to environmental and health concerns associated with hexavalent chromium, the use of chromate conversion coatings is being phased out in favor of more environmentally friendly alternatives.
Mechanism
The formation of chromate conversion coatings involves the chemical reaction between the chromate solution and the magnesium surface. This reaction produces a mixed oxide-chromate layer that adheres strongly to the substrate and provides excellent corrosion protection. The self-healing nature of chromate coatings is attributed to the release of chromate ions, which can migrate to damaged areas and re-form the protective layer.
Process Details
The chromate conversion coating process typically involves several steps, including cleaning, rinsing, chromate application, and drying. The cleaning step ensures the removal of contaminants, while rinsing eliminates any residual cleaning agents. The chromate solution is then applied to the magnesium surface, either by immersion, spraying, or brushing, followed by drying to complete the coating process.
Environmental and Safety Considerations
The use of hexavalent chromium in chromate conversion coatings poses significant environmental and health risks, leading to stringent regulations and restrictions on its use. As a result, there is a growing emphasis on developing alternative conversion coatings that provide similar performance without the associated hazards. Non-chromate conversion coatings, discussed in the next section, are among the most promising alternatives.
Non-chromate Conversion Coatings
Non-chromate conversion coatings are being developed to replace traditional chromate coatings, offering improved environmental and safety profiles while maintaining effective corrosion protection. Common non-chromate conversion coatings include phosphate, permanganate, and rare earth-based coatings.
Phosphate Coatings
Phosphate conversion coatings involve the application of phosphate solutions to the magnesium surface, resulting in the formation of a protective phosphate layer. These coatings provide good corrosion resistance and serve as an excellent base for subsequent painting or coating applications. Phosphate coatings are commonly used in the automotive industry for corrosion protection and as a primer layer.
Permanganate Coatings
Permanganate conversion coatings utilize permanganate solutions to form a protective layer on the magnesium surface. These coatings offer good corrosion resistance and are environmentally friendly compared to chromate coatings. The permanganate conversion process typically involves cleaning, permanganate application, and drying steps, similar to other conversion coating processes.
Rare Earth-based Coatings
Rare earth-based conversion coatings use solutions containing rare earth elements such as cerium, lanthanum, or yttrium to form protective layers on magnesium alloys. These coatings have shown promising corrosion resistance and are considered environmentally friendly alternatives to chromate coatings. The development and optimization of rare earth-based coatings are ongoing, with a focus on enhancing their performance and cost-effectiveness.
Anodizing
Anodizing is an electrochemical process that converts the surface of magnesium alloys into a durable, corrosion-resistant oxide layer. This process not only enhances corrosion resistance but also improves wear resistance and provides an aesthetically pleasing finish. Various anodizing methods are used for magnesium alloys, each offering unique benefits and characteristics.
Sulfuric Acid Anodizing
Sulfuric acid anodizing is one of the most common methods for anodizing magnesium alloys. The process involves immersing the magnesium component in a sulfuric acid electrolyte and applying an electric current. This results in the formation of a thick, hard oxide layer on the surface, providing excellent corrosion and wear resistance. The anodized layer can be further sealed to enhance its protective properties.
Dow 17 Process
The Dow 17 process is a proprietary anodizing method developed by Dow Chemical Company specifically for magnesium alloys. This process involves the use of a proprietary electrolyte solution and specific operating conditions to produce a thick, durable oxide layer. The Dow 17 process is known for its excellent corrosion resistance and has been widely adopted in the aerospace industry for magnesium parts and components.
Micro-arc Oxidation (Plasma Electrolytic Oxidation)
Micro-arc oxidation (MAO), also known as plasma electrolytic oxidation (PEO), is an advanced anodizing technique that produces thick, hard oxide coatings on magnesium alloys. The process involves applying a high voltage to the magnesium component in an electrolyte solution, creating micro-discharges on the surface. These discharges result in the formation of a dense, ceramic-like oxide layer with superior wear and corrosion resistance. MAO coatings are particularly suitable for applications requiring high durability and performance.
Sealing Methods and Benefits
Sealing is an important step in the anodizing process, aimed at closing the pores in the anodized layer and enhancing its protective properties. Common sealing methods include hot water sealing, where the anodized component is immersed in hot water to hydrate and close the pores, and cold sealing, which involves the use of sealing agents such as nickel acetate. Sealing improves the corrosion resistance and longevity of anodized coatings, making them more effective in harsh environments.
Electroplating
Electroplating is a widely used surface finishing technique that involves the deposition of a metallic coating on the surface of magnesium alloys through electrochemical processes. Electroplating provides enhanced corrosion resistance, improved wear resistance, and decorative finishes. The process typically involves several steps, including pre-treatment, activation, plating, and post-treatment.
Pre-treatment and Activation
Proper surface preparation is essential for successful electroplating on magnesium alloys. Pre-treatment steps, such as cleaning, degreasing, and etching, are necessary to remove contaminants and activate the magnesium surface for plating. Activation often involves the use of acidic or alkaline solutions to create a clean, reactive surface that promotes the adhesion of the electroplated layer.
Electroplating Processes
Various electroplating processes can be used for magnesium alloys, depending on the desired coating properties and application requirements. Common electroplating processes include nickel plating, copper plating, and other metallic coatings.
Nickel Plating
Nickel plating is one of the most commonly used electroplating processes for magnesium alloys. It provides excellent corrosion resistance, wear resistance, and an attractive appearance. The process involves the deposition of a nickel layer on the magnesium surface, typically followed by a passivation step to enhance the protective properties. Nickel-plated magnesium components are widely used in the automotive and electronics industries.
Copper Plating
Copper plating is another widely used electroplating process for magnesium alloys. Copper coatings offer good corrosion resistance, electrical conductivity, and solderability. The process involves the deposition of a copper layer on the magnesium surface, followed by further finishing steps such as nickel or tin plating, depending on the application requirements. Copper-plated magnesium components are commonly used in electrical and electronic applications.
Other Metallic Coatings
In addition to nickel and copper plating, other metallic coatings such as zinc, tin, and silver can be applied to magnesium alloys through electroplating. Each coating provides specific benefits, such as enhanced corrosion resistance, improved electrical conductivity, and aesthetic appeal. The selection of the appropriate metallic coating depends on the specific application requirements and environmental conditions.
Post-treatment and Finishing
Post-treatment steps are often necessary to further enhance the properties of electroplated coatings. Common post-treatment processes include passivation, chromate conversion coating, and sealing. These treatments improve the corrosion resistance, adhesion, and overall performance of the electroplated layer. Additionally, mechanical finishing processes such as polishing and buffing can be employed to achieve the desired surface finish and appearance.
Electroless Plating
Electroless plating, also known as chemical or auto-catalytic plating, is a surface finishing technique that involves the deposition of a metallic coating on the surface of magnesium alloys without the use of an external electrical current. The process relies on chemical reactions to achieve uniform and adherent coatings, offering several advantages over traditional electroplating methods.
Fundamentals of Electroless Plating
The electroless plating process involves the reduction of metal ions in a solution onto the magnesium surface through a chemical reaction. This reaction is typically catalyzed by the presence of a reducing agent and the surface of the magnesium alloy. The result is a uniform, adherent metallic coating that provides excellent corrosion and wear resistance.
Common Electroless Coatings
Electroless plating is commonly used to deposit nickel, copper, and composite coatings on magnesium alloys. Each type of coating offers unique benefits and is suited to specific applications.
Nickel
Electroless nickel plating is widely used for magnesium alloys due to its excellent corrosion resistance, hardness, and wear resistance. The process involves the deposition of a nickel-phosphorus or nickel-boron alloy on the magnesium surface. Electroless nickel coatings are commonly used in the automotive, aerospace, and electronics industries for components requiring high durability and performance.
Copper
Electroless copper plating provides good electrical conductivity, solderability, and corrosion resistance. The process involves the deposition of a copper layer on the magnesium surface through chemical reduction. Electroless copper coatings are commonly used in electronic and electrical applications where conductivity and reliability are critical.
Composite Coatings
Electroless composite coatings involve the incorporation of fine particles, such as ceramics or polymers, into the metallic matrix during the plating process. These composite coatings offer enhanced properties, such as improved wear resistance, lubricity, and corrosion resistance. Electroless composite coatings are used in a variety of industries, including automotive, aerospace, and industrial machinery.
Organic Coatings
Organic coatings, such as paints, primers, and powder coatings, are commonly used for protecting and enhancing the appearance of magnesium alloys. These coatings provide a barrier against environmental elements, improving corrosion resistance and aesthetics. The application of organic coatings involves several steps, including surface preparation, coating application, and curing.
Paints and Primers
Paints and primers are widely used for coating magnesium alloys, providing a protective barrier and an attractive finish. Primers are typically applied as an initial layer to improve adhesion and corrosion resistance, followed by the application of topcoat paints. Various types of paints, including solvent-based, water-based, and high-performance coatings, can be used depending on the application requirements.
Powder Coatings
Powder coatings are a popular choice for coating magnesium alloys due to their durability, environmental friendliness, and excellent finish. The process involves the application of a dry powder to the magnesium surface, followed by curing in an oven to form a hard, protective layer. Powder coatings provide excellent corrosion resistance, impact resistance, and aesthetic appeal, making them suitable for a wide range of applications.
Application Techniques and Curing
The application of organic coatings can be carried out using various techniques, including spraying, dipping, brushing, and electrostatic deposition. The choice of application method depends on the size, shape, and complexity of the magnesium component. Curing is a critical step in the coating process, involving the use of heat or UV light to cross-link and harden the coating material. Proper curing ensures the durability and performance of the organic coating.
Hybrid Coatings
Hybrid coatings involve the combination of multiple surface finishing techniques to achieve synergistic effects and improved performance. These coatings leverage the benefits of different processes, such as anodizing, electroplating, and organic coatings, to provide enhanced corrosion resistance, wear resistance, and aesthetic appeal.
Combining Multiple Techniques
The combination of different surface finishing techniques allows for the creation of hybrid coatings that offer superior properties compared to single-process coatings. For example, anodizing followed by organic coating can provide excellent corrosion resistance and a durable finish. Similarly, electroplating with a topcoat of powder coating can enhance both the appearance and protective properties of magnesium components.
Synergistic Effects and Improved Performance
Hybrid coatings take advantage of the synergistic effects of multiple surface finishing techniques, resulting in improved performance and extended service life of magnesium components. By combining the strengths of different processes, hybrid coatings can address specific challenges and meet the demanding requirements of various applications.
Testing and Characterization
Testing and characterization of surface finishes on magnesium alloys are essential to ensure their performance, durability, and compliance with industry standards. Various tests and analytical techniques are used to evaluate the adhesion, corrosion resistance, wear resistance, and microstructural properties of the coatings.
Adhesion Tests
Adhesion tests are performed to assess the bond strength between the coating and the magnesium substrate. Common adhesion testing methods include pull-off tests, scratch tests, and tape tests. These tests provide valuable information on the coating's ability to withstand mechanical stresses and environmental conditions.
Corrosion Resistance Evaluation
Corrosion resistance is a critical property of surface finishes for magnesium alloys. Various corrosion testing methods, such as salt spray testing, electrochemical testing, and immersion testing, are used to evaluate the coating's ability to protect the substrate from corrosive environments. These tests help determine the long-term performance and reliability of the coatings.
Wear Resistance Tests
Wear resistance is an important property for surface finishes used in applications involving friction and mechanical wear. Wear resistance tests, such as abrasion testing, pin-on-disk testing, and wear track analysis, are conducted to evaluate the coating's ability to withstand wear and maintain its protective properties. These tests provide insights into the durability and performance of the coatings under different operating conditions.
Microstructural Analysis
Microstructural analysis involves the examination of the coating's structure, composition, and morphology using techniques such as scanning electron microscopy (SEM), energy-dispersive X-ray spectroscopy (EDS), and X-ray diffraction (XRD). This analysis provides detailed information on the coating's uniformity, thickness, and composition, helping to optimize the surface finishing processes and improve the performance of the coatings.
Industrial Applications
Automotive Industry
Magnesium alloys are extensively used in the automotive industry for components such as engine blocks, transmission cases, and body panels. Surface finishing techniques play a crucial role in enhancing the corrosion resistance, wear resistance, and aesthetics of these components. Anodizing, electroplating, and organic coatings are commonly used to protect and improve the performance of magnesium alloy automotive parts.
Aerospace Sector
The aerospace sector relies on magnesium alloys for various structural and non-structural components due to their lightweight and high-strength properties. Surface finishing techniques, such as anodizing, chromate conversion coatings, and hybrid coatings, are essential for ensuring the corrosion resistance and durability of magnesium components used in aerospace applications. These coatings help extend the service life and reliability of critical aerospace parts.
Electronics and Consumer Goods
Magnesium alloys are used in the electronics and consumer goods industries for components such as laptop casings, mobile phone frames, and electronic housings. Surface finishing techniques, including electroless plating, powder coatings, and organic coatings, are employed to provide corrosion resistance, wear resistance, and an attractive appearance. These coatings help protect electronic components and enhance the overall quality and aesthetics of consumer goods.
Biomedical Applications
Magnesium alloys are gaining attention in the biomedical field for applications such as biodegradable implants, orthopedic devices, and medical instruments. Surface finishing techniques play a vital role in enhancing the biocompatibility, corrosion resistance, and mechanical properties of magnesium biomedical components. Anodizing, electroless plating, and hybrid coatings are commonly used to improve the performance and safety of magnesium-based medical devices.
Environmental and Safety Considerations
Regulations and Standards
The use of surface finishing techniques for magnesium alloys is subject to various regulations and standards aimed at ensuring environmental protection and safety. These regulations govern the use of hazardous chemicals, waste management, and the environmental impact of surface finishing processes. Compliance with these regulations is essential for sustainable and responsible surface finishing practices.
Eco-friendly Alternatives
The development of eco-friendly surface finishing techniques is a priority in the industry, driven by the need to reduce environmental impact and comply with regulations. Alternatives to traditional chromate conversion coatings, such as non-chromate conversion coatings and environmentally friendly anodizing processes, are being developed and adopted. These alternatives offer effective corrosion protection while minimizing health and environmental risks.
Waste Management and Recycling
Effective waste management and recycling practices are essential for minimizing the environmental impact of surface finishing processes. Proper disposal and treatment of waste materials, such as spent solutions and sludge, are necessary to prevent contamination and pollution. Recycling of materials, such as aluminum and magnesium, can help reduce resource consumption and promote sustainable manufacturing practices.
Future Trends and Research Directions
Emerging Technologies
Emerging technologies in surface finishing for magnesium alloys are focused on developing advanced coatings and processes that offer superior performance and sustainability. Techniques such as nanocoatings, laser surface modification, and advanced composite coatings are being explored to enhance the properties of magnesium alloys and address specific application requirements.
Nanocoatings and Smart Coatings
Nanocoatings and smart coatings represent a promising area of research in surface finishing for magnesium alloys. Nanocoatings involve the application of nanoscale materials to create thin, uniform coatings with enhanced properties such as corrosion resistance, wear resistance, and self-healing capabilities. Smart coatings, on the other hand, are designed to respond to environmental stimuli, such as changes in temperature or humidity, to provide adaptive protection and functionality.
Industry 4.0 and Surface Finishing
The integration of Industry 4.0 technologies, such as automation, data analytics, and the Internet of Things (IoT), is transforming surface finishing processes for magnesium alloys. Advanced manufacturing techniques, such as additive manufacturing and digital twins, are being utilized to optimize surface finishing processes, improve quality control, and enhance the efficiency and sustainability of production.
Conclusion
Surface finishing technology plays a crucial role in enhancing the performance, durability, and aesthetics of magnesium alloys. Various techniques, including conversion coatings, anodizing, electroplating, electroless plating, and organic coatings, are used to protect and improve the properties of magnesium components. The ongoing development of environmentally friendly and high-performance coatings, along with advancements in testing and characterization methods, is driving the evolution of surface finishing technology. The continued research and innovation in this field are essential for meeting the growing demand for lightweight, high-performance materials in various industries and ensuring the sustainable and responsible use of magnesium alloys.
Reprint Statement: If there are no special instructions, all articles on this site are original. Please indicate the source for reprinting:https://www.cncmachiningptj.com/,thanks!
3, 4 and 5-axis precision CNC machining services for aluminum machining, beryllium, carbon steel, magnesium, titanium machining, Inconel, platinum, superalloy, acetal, polycarbonate, fiberglass, graphite and wood. Capable of machining parts up to 98 in. turning dia. and +/-0.001 in. straightness tolerance. Processes include milling, turning, drilling, boring, threading, tapping, forming, knurling, counterboring, countersinking, reaming and laser cutting. Secondary services such as assembly, centerless grinding, heat treating, plating and welding. Prototype and low to high volume production offered with maximum 50,000 units. Suitable for fluid power, pneumatics, hydraulics and valve applications. Serves the aerospace, aircraft, military, medical and defense industries.PTJ will strategize with you to provide the most cost-effective services to help you reach your target,Welcome to Contact us ( sales@pintejin.com ) directly for your new project.
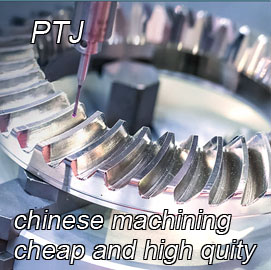
- 5 Axis Machining
- Cnc Milling
- Cnc Turning
- Machining Industries
- Machining Process
- Surface Treatment
- Metal Machining
- Plastic Machining
- Powder Metallurgy Mold
- Die Casting
- Parts Gallery
- Auto Metal Parts
- Machinery Parts
- LED Heatsink
- Building Parts
- Mobile Parts
- Medical Parts
- Electronic Parts
- Tailored Machining
- Bicycle Parts
- Aluminum Machining
- Titanium Machining
- Stainless Steel Machining
- Copper Machining
- Brass Machining
- Super Alloy Machining
- Peek Machining
- UHMW Machining
- Unilate Machining
- PA6 Machining
- PPS Machining
- Teflon Machining
- Inconel Machining
- Tool Steel Machining
- More Material