Rapid Prototyping Methods for Indirect Manufacturing Molds
Rapid prototyping (RP) has revolutionized the manufacturing industry by allowing for the quick fabrication of physical models using three-dimensional computer-aided design (CAD) data. This process has significantly reduced the time and cost associated with the development and testing of new products. One of the critical applications of rapid prototyping is in the creation of molds for indirect manufacturing processes. This article delves into the various rapid prototyping methods employed to produce molds for indirect manufacturing, their benefits, limitations, and impact on the manufacturing industry.
Historical Context and Evolution
Early Developments in Rapid Prototyping
The concept of rapid prototyping began to take shape in the late 20th century, primarily in the 1980s, with the advent of technologies such as stereolithography (SLA). These early developments laid the groundwork for more advanced methods and applications, including the production of molds for indirect manufacturing. Initially, RP was used primarily for creating prototypes to visualize and test product designs. However, the potential for creating complex geometries and accurate models quickly led to its adoption in mold making.
Evolution to Indirect Manufacturing Molds
The transition from using rapid prototyping for simple model creation to producing molds for indirect manufacturing marked a significant milestone. Traditional mold-making processes are time-consuming and expensive, involving several stages of manual labor and machining. The integration of RP in mold-making processes provided a faster, cost-effective alternative that could produce complex mold geometries with high precision. This evolution has been driven by advancements in materials, software, and hardware technologies, which have collectively enhanced the capabilities and applications of rapid prototyping.
Rapid Prototyping Technologies for Mold Making
Several rapid prototyping technologies have been adapted for mold making, each with its unique advantages and limitations. The following sections provide a detailed overview of these technologies.
Stereolithography (SLA)
Stereolithography (SLA) is one of the earliest and most widely used rapid prototyping technologies. It uses a laser to cure liquid photopolymer resin layer by layer, building up the mold's structure.
Advantages:
- High accuracy and resolution, suitable for creating intricate mold details.
- Smooth surface finish, reducing the need for extensive post-processing.
Limitations:
- Limited material options, primarily restricted to photopolymers.
- The mechanical properties of the molds may not be suitable for high-stress applications.
Applications:
- Prototyping complex mold designs for injection molding.
- Creating master patterns for silicone rubber molding.
Selective Laser Sintering (SLS)
Selective Laser Sintering (SLS) uses a laser to sinter powdered material, binding it together to form a solid structure. This technology can utilize a variety of materials, including plastics, metals, and ceramics.
Advantages:
- Versatile material options, allowing for functional testing of molds.
- Good mechanical properties suitable for producing durable molds.
Limitations:
- Surface finish may require post-processing to achieve desired smoothness.
- Potential for dimensional inaccuracies due to shrinkage and warping.
Applications:
- Producing functional prototypes and short-run production molds.
- Creating molds for casting applications, including metal casting.
Fused Deposition Modeling (FDM)
Fused Deposition Modeling (FDM) involves extruding thermoplastic material layer by layer to build the mold. This technology is known for its ease of use and wide availability.
Advantages:
- Cost-effective and accessible, with a wide range of thermoplastic materials.
- Suitable for rapid iterations and functional testing.
Limitations:
- Lower resolution compared to SLA and SLS, leading to rougher surface finishes.
- Limited to thermoplastic materials, which may not be suitable for high-temperature applications.
Applications:
- Creating quick and cost-effective prototypes of molds.
- Producing molds for low-volume production and testing.
Digital Light Processing (DLP)
Digital Light Processing (DLP) is similar to SLA but uses a digital light projector to cure the photopolymer resin. This technology offers high speed and accuracy.
Advantages:
- High resolution and fast build times.
- Excellent surface finish and detail accuracy.
Limitations:
- Limited to photopolymer materials, which may have restricted mechanical properties.
- Requires careful handling and post-processing to ensure mold integrity.
Applications:
- Producing high-precision molds for detailed components.
- Creating master patterns for casting and silicone molding.
Multi-Jet Fusion (MJF)
Multi-Jet Fusion (MJF) is an advanced technology developed by HP that uses a combination of material and fusing agents to create parts layer by layer. This method offers high speed and detail.
Advantages:
- Fast production times and high-quality surface finish.
- Good mechanical properties suitable for functional testing.
Limitations:
- Limited material options, primarily thermoplastics.
- Higher initial setup cost compared to other RP methods.
Applications:
- Producing detailed and functional molds for a variety of applications.
- Creating short-run production molds with high accuracy.
Electron Beam Melting (EBM)
Electron Beam Melting (EBM) is a type of additive manufacturing that uses an electron beam to melt and fuse metal powder layer by layer. This technology is primarily used for creating metal molds.
Advantages:
- Capable of producing molds from high-performance metal alloys.
- Good mechanical properties and durability for demanding applications.
Limitations:
- High cost and complexity of the equipment and process.
- Limited to specific metal powders and requires significant post-processing.
Applications:
- Producing metal molds for high-temperature and high-stress applications.
- Creating molds for metal casting and injection molding.
Comparative Analysis of Rapid Prototyping Methods
Each rapid prototyping method has its unique set of strengths and weaknesses, making them suitable for different applications in mold making. The following comparative analysis highlights these differences to guide the selection of the appropriate technology.
Material Properties
- SLA and DLP: Best for high-detail, low-stress applications due to the limited mechanical properties of photopolymers.
- SLS and MJF: Offer a good balance between detail and mechanical properties, suitable for functional testing and short-run production.
- FDM: Best for low-cost, rapid iterations with moderate mechanical properties.
- EBM: Ideal for high-performance metal molds, providing excellent mechanical properties but at a higher cost.
Surface Finish and Detail
- SLA and DLP: Provide the best surface finish and detail accuracy, reducing the need for post-processing.
- SLS and MJF: Good detail but may require post-processing for smooth finishes.
- FDM: Rougher surface finish, often requiring significant post-processing.
- EBM: Good detail for metal parts, but surface finish may require machining.
Production Speed
- DLP and MJF: Generally offer the fastest production times.
- SLA and SLS: Moderate production speeds, depending on part complexity.
- FDM: Slower production times due to the layer-by-layer extrusion process.
- EBM: Slowest production speed due to the complexity of the electron beam melting process.
Cost Considerations
- FDM: Most cost-effective for initial prototyping and low-volume production.
- SLA and SLS: Moderate cost, balancing detail and material properties.
- DLP: Higher initial cost but efficient for detailed, small parts.
- MJF: High initial setup cost but efficient for medium to large production runs.
- EBM: Highest cost due to the complexity and material requirements.
Applications in Indirect Manufacturing
Rapid prototyping methods are extensively used in various indirect manufacturing processes, including injection molding, metal casting, and silicone rubber molding. The following sections explore these applications in detail.
Injection Molding
Injection molding is a widely used manufacturing process for producing plastic parts by injecting molten material into a mold. Rapid prototyping methods are used to create both prototype and production molds.
Applications:
- Prototype Molds: Used for testing and validating part designs before mass production.
- Bridge Molds: Intermediate molds used to produce parts while production molds are being manufactured.
- Production Molds: In some cases, RP methods can produce durable molds for low-volume production runs.
Benefits:
- Reduces lead time and cost compared to traditional mold-making methods.
- Allows for quick iterations and design modifications.
Metal Casting
Metal casting involves pouring molten metal into a mold to create parts. Rapid prototyping methods are used to create patterns and molds for various metal casting processes, including sand casting and investment casting.
Applications:
- Patterns for Sand Casting: RP methods can produce complex patterns for sand molds.
- Investment Casting Patterns: Wax or plastic patterns created using RP methods for investment casting.
- Direct Metal Molds: EBM and other metal RP methods can produce molds directly.
Benefits:
- Enables the production of complex geometries not possible with traditional methods.
- Reduces the time and cost associated with creating patterns and molds.
Silicone Rubber Molding
Silicone rubber molding is used to create flexible, durable parts. Rapid prototyping methods are used to create master patterns and molds for silicone rubber molding.
Applications:
- Master Patterns: High-detail patterns created using SLA or DLP for silicone molding.
- Molds for Prototyping: Creating molds for producing silicone prototypes and short-run production parts.
Benefits:
- High accuracy and detail, essential for producing high-quality silicone parts.
- Cost-effective and quick production of molds compared to traditional methods.
Future Trends and Developments
The field of rapid prototyping and mold making is continuously evolving, driven by advancements in materials, technologies, and software. The following trends are expected to shape the future of this field.
Advanced Materials
The development of new materials with enhanced properties will expand the applications of rapid prototyping in mold making. These materials will offer improved mechanical properties, heat resistance, and durability, making them suitable for more demanding applications.
Hybrid Manufacturing
Combining rapid prototyping with traditional manufacturing methods, such as CNC machining, will create hybrid manufacturing processes that leverage the strengths of both technologies. This approach will enable the production of molds with complex geometries and high precision.
Automation and AI Integration
The integration of automation and artificial intelligence (AI) in rapid prototyping processes will enhance efficiency, accuracy, and customization. AI-driven design optimization and automated production workflows will reduce lead times and improve the quality of molds.
Sustainable Practices
As sustainability becomes a critical consideration in manufacturing, rapid prototyping methods will adopt more eco-friendly practices. This includes the use of recyclable materials, energy-efficient processes, and waste reduction techniques.
Conclusion
Rapid prototyping methods have significantly transformed the production of molds for indirect manufacturing, offering numerous benefits over traditional methods. By enabling faster production times, reduced costs, and greater design flexibility, RP technologies have become indispensable tools in the manufacturing industry. As advancements continue, these methods will further enhance their capabilities, driving innovation and efficiency in mold making and beyond.
Reprint Statement: If there are no special instructions, all articles on this site are original. Please indicate the source for reprinting:https://www.cncmachiningptj.com/,thanks!
3, 4 and 5-axis precision CNC machining services for aluminum machining, beryllium, carbon steel, magnesium, titanium machining, Inconel, platinum, superalloy, acetal, polycarbonate, fiberglass, graphite and wood. Capable of machining parts up to 98 in. turning dia. and +/-0.001 in. straightness tolerance. Processes include milling, turning, drilling, boring, threading, tapping, forming, knurling, counterboring, countersinking, reaming and laser cutting. Secondary services such as assembly, centerless grinding, heat treating, plating and welding. Prototype and low to high volume production offered with maximum 50,000 units. Suitable for fluid power, pneumatics, hydraulics and valve applications. Serves the aerospace, aircraft, military, medical and defense industries.PTJ will strategize with you to provide the most cost-effective services to help you reach your target,Welcome to Contact us ( sales@pintejin.com ) directly for your new project.
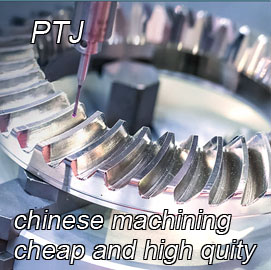
- 5 Axis Machining
- Cnc Milling
- Cnc Turning
- Machining Industries
- Machining Process
- Surface Treatment
- Metal Machining
- Plastic Machining
- Powder Metallurgy Mold
- Die Casting
- Parts Gallery
- Auto Metal Parts
- Machinery Parts
- LED Heatsink
- Building Parts
- Mobile Parts
- Medical Parts
- Electronic Parts
- Tailored Machining
- Bicycle Parts
- Aluminum Machining
- Titanium Machining
- Stainless Steel Machining
- Copper Machining
- Brass Machining
- Super Alloy Machining
- Peek Machining
- UHMW Machining
- Unilate Machining
- PA6 Machining
- PPS Machining
- Teflon Machining
- Inconel Machining
- Tool Steel Machining
- More Material