Tips for You Before Forming a CNC Model
Computer Numerical Control (CNC) machining is a manufacturing process in which pre-programmed computer software dictates the movement of factory tools and machinery. The process is used to control a range of complex machinery, from grinders and lathes to mills and routers. CNC machining allows for three-dimensional cutting tasks to be accomplished in a single set of prompts. This article provides a comprehensive guide to the essential tips and considerations before forming a CNC model.
Introduction to CNC Machining
CNC machining has revolutionized the manufacturing industry, enabling higher precision, efficiency, and flexibility in producing parts and products. The technology has evolved significantly since its inception, with advancements in software, hardware, and techniques. Understanding the basics of CNC machining is crucial before delving into the specifics of forming a CNC model.
Historical Background
CNC machining traces its origins back to the 1940s and 1950s when the first numerical control machines were developed. These early machines used punched tape to control machine operations. With the advent of computers, CNC technology advanced rapidly, leading to the sophisticated systems used today. The evolution of CNC machining has been marked by continuous improvements in accuracy, speed, and capabilities.
Fundamentals of CNC Machining
At its core, CNC machining involves the use of computer-aided design (CAD) and computer-aided manufacturing (CAM) software to create a digital model of the desired part. This model is then converted into a set of instructions (G-code) that control the movements of the CNC machine. The machine removes material from a workpiece to create the final part with high precision.
Planning and Preparation
Proper planning and preparation are critical to the success of any CNC machining project. This phase involves understanding the requirements, selecting appropriate materials, and designing the model.
Understanding Project Requirements
Before starting a CNC machining project, it is essential to have a clear understanding of the project's requirements. This includes the dimensions, tolerances, and surface finish of the final part. Additionally, understanding the functional requirements and operating environment of the part can influence material selection and design considerations.
Material Selection
Choosing the right material is a fundamental aspect of CNC machining. The material should meet the project's mechanical, thermal, and chemical properties. Common materials used in CNC machining include metals (aluminum, steel, titanium), plastics (ABS, polycarbonate, nylon), and composites. Each material has its advantages and limitations, so careful consideration is necessary to ensure optimal performance and cost-effectiveness.
Designing the Model
Designing the model for CNC machining involves creating a detailed CAD drawing of the part. The design should account for the capabilities and limitations of CNC machines, such as minimum feature size, tool access, and machining strategies. Incorporating design for manufacturability (DFM) principles can help streamline the machining process and reduce production costs.
CAD and CAM Software
The selection and use of CAD and CAM software play a pivotal role in CNC machining. These tools enable the creation, simulation, and optimization of the digital model and machining process.
CAD Software
CAD software is used to create the 3D model of the part. Popular CAD software options include SolidWorks, AutoCAD, and Fusion 360. These tools provide a range of features for designing complex geometries, creating detailed drawings, and performing simulations to validate the design.
CAM Software
CAM software translates the CAD model into G-code instructions for the CNC machine. This process involves selecting machining strategies, defining tool paths, and simulating the machining process to identify potential issues. Popular CAM software includes Mastercam, HSMWorks, and Edgecam. Effective use of CAM software can significantly enhance machining efficiency and accuracy.
CNC Machine Setup
Setting up the CNC machine correctly is crucial to achieving the desired results. This phase involves selecting appropriate tools, configuring the machine, and performing necessary calibrations.
Tool Selection
Choosing the right cutting tools is essential for efficient and accurate machining. Factors to consider include the material of the tool, tool geometry, and coating. Common cutting tools used in CNC machining include end mills, drills, and reamers. The selection should align with the material being machined and the desired surface finish.
Machine Configuration
Configuring the CNC machine involves setting up the workpiece, securing it properly, and aligning it with the machine's coordinate system. Ensuring accurate alignment and securing the workpiece can prevent errors and improve machining precision.
Calibration and Testing
Calibrating the CNC machine ensures that it operates within the specified tolerances. This process includes checking and adjusting the machine's axes, verifying tool offsets, and conducting test runs. Regular calibration and maintenance are essential to maintain the machine's performance and accuracy.
Machining Process
The machining process encompasses the actual cutting, milling, drilling, or turning operations performed by the CNC machine. Proper execution of this phase is critical to achieving the desired part quality.
Machining Strategies
Selecting appropriate machining strategies can significantly impact the efficiency and quality of the final part. Common strategies include roughing, finishing, and contouring. Each strategy has its specific purpose and should be chosen based on the part's geometry and material.
Monitoring and Adjustments
Continuous monitoring of the machining process is necessary to identify and address any issues promptly. This includes checking for tool wear, verifying dimensions, and making necessary adjustments to the machine's parameters. Implementing real-time monitoring systems can enhance process control and reduce downtime.
Quality Control
Quality control measures ensure that the final part meets the specified requirements. This involves inspecting dimensions, surface finish, and other critical features. Using precision measurement tools, such as coordinate measuring machines (CMM), can provide accurate and reliable inspection results.
Post-Machining Considerations
Once the machining process is complete, several post-machining considerations can enhance the part's quality and performance.
Deburring and Finishing
Deburring involves removing sharp edges and burrs from the machined part. This can be done using various methods, such as manual deburring, tumbling, or abrasive blasting. Finishing processes, such as polishing, anodizing, or coating, can further enhance the part's appearance and durability.
Assembly and Testing
For parts that are part of an assembly, ensuring proper fit and function is essential. This may involve conducting assembly tests, checking for proper alignment, and verifying that the part meets functional requirements. Addressing any issues at this stage can prevent costly rework and delays.
Documentation and Traceability
Maintaining detailed documentation of the machining process, including setup parameters, tool selections, and inspection results, is crucial for traceability and quality control. This documentation can be valuable for future reference, troubleshooting, and continuous improvement efforts.
Advanced CNC Techniques
As CNC technology continues to advance, several advanced techniques and technologies have emerged to enhance machining capabilities and efficiency.
5-Axis Machining
5-axis machining involves the simultaneous movement of the CNC machine along five different axes. This enables the production of complex geometries and reduces the need for multiple setups. 5-axis machining is particularly beneficial for aerospace, automotive, and medical applications.
High-Speed Machining
High-speed machining (HSM) focuses on increasing cutting speeds and feed rates while maintaining precision and surface quality. HSM can significantly reduce cycle times and improve productivity. Advanced cutting tools, optimized tool paths, and high-performance machine tools are essential for successful HSM implementation.
Additive Manufacturing Integration
Integrating additive manufacturing (3D printing) with CNC machining can offer unique advantages. This hybrid approach allows for the creation of complex parts with internal features, reducing material waste and enabling innovative design possibilities. Combining additive and subtractive processes can enhance overall manufacturing capabilities.
Conclusion
Forming a CNC model requires careful planning, preparation, and execution. By understanding the fundamentals of CNC machining, selecting appropriate materials, designing effective models, and utilizing advanced techniques, manufacturers can achieve high precision, efficiency, and quality in their CNC machining projects. Continuous learning and adaptation to new technologies and best practices are essential for staying competitive in the evolving field of CNC machining.
Reprint Statement: If there are no special instructions, all articles on this site are original. Please indicate the source for reprinting:https://www.cncmachiningptj.com/,thanks!
3, 4 and 5-axis precision CNC machining services for aluminum machining, beryllium, carbon steel, magnesium, titanium machining, Inconel, platinum, superalloy, acetal, polycarbonate, fiberglass, graphite and wood. Capable of machining parts up to 98 in. turning dia. and +/-0.001 in. straightness tolerance. Processes include milling, turning, drilling, boring, threading, tapping, forming, knurling, counterboring, countersinking, reaming and laser cutting. Secondary services such as assembly, centerless grinding, heat treating, plating and welding. Prototype and low to high volume production offered with maximum 50,000 units. Suitable for fluid power, pneumatics, hydraulics and valve applications. Serves the aerospace, aircraft, military, medical and defense industries.PTJ will strategize with you to provide the most cost-effective services to help you reach your target,Welcome to Contact us ( sales@pintejin.com ) directly for your new project.
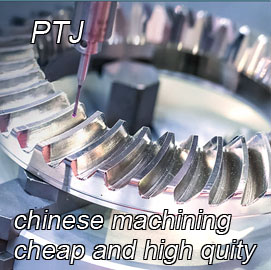
- 5 Axis Machining
- Cnc Milling
- Cnc Turning
- Machining Industries
- Machining Process
- Surface Treatment
- Metal Machining
- Plastic Machining
- Powder Metallurgy Mold
- Die Casting
- Parts Gallery
- Auto Metal Parts
- Machinery Parts
- LED Heatsink
- Building Parts
- Mobile Parts
- Medical Parts
- Electronic Parts
- Tailored Machining
- Bicycle Parts
- Aluminum Machining
- Titanium Machining
- Stainless Steel Machining
- Copper Machining
- Brass Machining
- Super Alloy Machining
- Peek Machining
- UHMW Machining
- Unilate Machining
- PA6 Machining
- PPS Machining
- Teflon Machining
- Inconel Machining
- Tool Steel Machining
- More Material