Effect of Mold Material on Heat Treatment Deformation
Heat treatment is a critical process in manufacturing that involves heating and cooling materials, particularly metals and alloys, to alter their physical and mechanical properties without changing their shapes. The choice of mold material plays a crucial role in heat treatment, as it can significantly impact the deformation of the treated parts. This article explores the relationship between mold material and heat treatment deformation, delving into the underlying principles, material properties, and practical implications.
Overview of Heat Treatment Processes
Heat treatment encompasses several processes, including annealing, quenching, tempering, and carburizing. Each of these processes aims to achieve specific material characteristics:
- Annealing: A process of heating the material to a specific temperature and then slowly cooling it to remove internal stresses, increase ductility, and improve machinability.
- Quenching: Rapid cooling of a material, typically in water or oil, to harden it. Quenching can induce significant thermal stresses and deformation.
- Tempering: Heating a quenched material to a temperature below its critical point and then cooling it, which reduces brittleness while maintaining hardness.
- Carburizing: A heat treatment process where carbon is diffused into the surface of a steel part to improve its hardness and wear resistance.
Each of these processes involves thermal cycles that can lead to expansion and contraction, potentially causing deformation. The mold material used during these processes can influence the extent and nature of this deformation.
Properties of Mold Materials
Mold materials for heat treatment must possess specific properties to withstand high temperatures and thermal cycling. Key properties include:
- Thermal Conductivity: The ability of a material to conduct heat. High thermal conductivity allows for uniform heating and cooling, reducing thermal gradients and associated stresses.
- Thermal Expansion: The degree to which a material expands when heated. Materials with similar thermal expansion coefficients to the treated part can minimize differential expansion and contraction.
- Thermal Shock Resistance: The ability to withstand rapid temperature changes without cracking or degrading.
- Mechanical Strength: The ability to maintain structural integrity at elevated temperatures and under thermal cycling.
- Chemical Stability: Resistance to oxidation and other chemical reactions at high temperatures.
Common mold materials include graphite, ceramic, and various high-temperature alloys, each offering a unique combination of these properties.
Graphite Molds
Graphite is a widely used mold material in heat treatment due to its excellent thermal properties and chemical stability. Its high thermal conductivity and low thermal expansion make it ideal for applications requiring uniform heating and cooling. Graphite molds are often used in processes such as vacuum brazing, where they provide good dimensional stability and minimize deformation.
Advantages
- High Thermal Conductivity: Ensures uniform temperature distribution, reducing thermal gradients and associated deformation.
- Low Thermal Expansion: Minimizes differential expansion and contraction, reducing the risk of warping and distortion.
- Chemical Stability: Resistant to most chemicals and oxidation at high temperatures.
Disadvantages
- Mechanical Strength: Lower than some metal alloys, which can limit its use in applications requiring high mechanical load-bearing capacity.
- Cost: High-quality graphite can be expensive, particularly for large or complex molds.
Ceramic Molds
Ceramic molds, including materials such as alumina and zirconia, are used in heat treatment processes requiring excellent thermal shock resistance and chemical stability. These molds are particularly suitable for high-temperature applications, such as investment casting and superalloy processing.
Advantages
- Thermal Shock Resistance: Can withstand rapid temperature changes without cracking.
- Chemical Stability: Highly resistant to oxidation and other chemical reactions at high temperatures.
- High-Temperature Capability: Suitable for extremely high-temperature applications.
Disadvantages
- Thermal Conductivity: Lower than metals and graphite, which can lead to non-uniform heating and cooling.
- Brittleness: Susceptible to cracking under mechanical stress or impact.
Metal Alloy Molds
High-temperature metal alloys, such as tool steels and nickel-based superalloys, are also used as mold materials. These alloys offer a balance of thermal and mechanical properties, making them suitable for demanding heat treatment processes.
Advantages
- Mechanical Strength: High load-bearing capacity, suitable for large mold parts or complex molds.
- Thermal Conductivity: Moderate thermal conductivity, better than ceramics but lower than graphite.
- Durability: Long service life due to high mechanical strength and resistance to thermal cycling.
Disadvantages
- Cost: High-performance alloys can be expensive.
- Thermal Expansion: Higher thermal expansion coefficients compared to ceramics and graphite, which can increase the risk of deformation.
Comparative Analysis of Mold Materials
The choice of mold material significantly impacts the deformation behavior of heat-treated parts. Comparative analysis based on key properties reveals insights into their suitability for various applications:
-
Thermal Conductivity:
- Graphite > Metal Alloys > Ceramics
-
Thermal Expansion:
- Ceramics < Graphite < Metal Alloys
-
Thermal Shock Resistance:
- Ceramics > Graphite > Metal Alloys
-
Mechanical Strength:
- Metal Alloys > Ceramics > Graphite
-
Chemical Stability:
- Ceramics > Graphite > Metal Alloys
Practical Implications and Case Studies
Case Study 1: Heat Treatment of Aerospace Components
Aerospace components often require precise heat treatment to achieve specific mechanical properties while maintaining tight dimensional tolerances. In this case, the choice of mold material is crucial to minimizing deformation. Graphite molds are commonly used due to their low thermal expansion and high thermal conductivity, which ensure uniform heating and cooling. This minimizes thermal gradients and associated stresses, reducing the risk of deformation.
Case Study 2: Tool Steel Quenching
In the quenching of tool steels, rapid cooling can induce significant thermal stresses and deformation. Using metal alloy molds with similar thermal expansion properties to the tool steel can help minimize differential expansion and contraction. Additionally, the high mechanical strength of metal alloy molds ensures they can withstand the mechanical stresses involved in quenching.
Case Study 3: Investment Casting of Superalloys
Investment casting of superalloys involves high-temperature processing, where ceramic molds are often used due to their excellent thermal shock resistance and chemical stability. The low thermal expansion of ceramics minimizes deformation during cooling, ensuring the dimensional accuracy of the cast parts.
Future Directions and Research
The development of advanced mold materials with tailored properties continues to be an area of active research. Emerging materials, such as advanced ceramics and composite materials, offer the potential for improved performance in heat treatment applications. Additionally, the integration of computational modeling and simulation tools can aid in the design of molds that minimize deformation, optimizing the heat treatment process.
Conclusion
The choice of mold material plays a pivotal role in the heat treatment of materials, influencing the extent and nature of deformation. Graphite, ceramics, and metal alloys each offer unique properties that make them suitable for specific applications. Understanding the interplay between mold material properties and heat treatment processes is essential for optimizing performance and achieving desired material characteristics. Ongoing research and development in this field promise to further enhance the efficiency and precision of heat treatment processes in the future.
Reprint Statement: If there are no special instructions, all articles on this site are original. Please indicate the source for reprinting:https://www.cncmachiningptj.com/,thanks!
3, 4 and 5-axis precision CNC machining services for aluminum machining, beryllium, carbon steel, magnesium, titanium machining, Inconel, platinum, superalloy, acetal, polycarbonate, fiberglass, graphite and wood. Capable of machining parts up to 98 in. turning dia. and +/-0.001 in. straightness tolerance. Processes include milling, turning, drilling, boring, threading, tapping, forming, knurling, counterboring, countersinking, reaming and laser cutting. Secondary services such as assembly, centerless grinding, heat treating, plating and welding. Prototype and low to high volume production offered with maximum 50,000 units. Suitable for fluid power, pneumatics, hydraulics and valve applications. Serves the aerospace, aircraft, military, medical and defense industries.PTJ will strategize with you to provide the most cost-effective services to help you reach your target,Welcome to Contact us ( sales@pintejin.com ) directly for your new project.
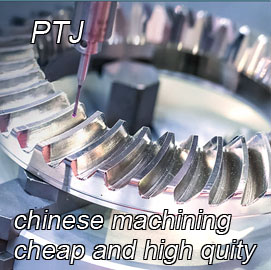
- 5 Axis Machining
- Cnc Milling
- Cnc Turning
- Machining Industries
- Machining Process
- Surface Treatment
- Metal Machining
- Plastic Machining
- Powder Metallurgy Mold
- Die Casting
- Parts Gallery
- Auto Metal Parts
- Machinery Parts
- LED Heatsink
- Building Parts
- Mobile Parts
- Medical Parts
- Electronic Parts
- Tailored Machining
- Bicycle Parts
- Aluminum Machining
- Titanium Machining
- Stainless Steel Machining
- Copper Machining
- Brass Machining
- Super Alloy Machining
- Peek Machining
- UHMW Machining
- Unilate Machining
- PA6 Machining
- PPS Machining
- Teflon Machining
- Inconel Machining
- Tool Steel Machining
- More Material