Different Aspects in Wire EDM vs. Laser Cutting
Wire Electrical Discharge Machining (Wire EDM) and Laser Cutting are two advanced manufacturing technologies widely utilized for precision machining and cutting of materials. Both techniques offer unique advantages and are employed in various industrial applications, from aerospace to medical device manufacturing. Understanding the different aspects of Wire EDM and Laser Cutting is crucial for selecting the appropriate method based on specific requirements. This article provides an in-depth comparison of Wire EDM and Laser Cutting, examining their principles, capabilities, advantages, limitations, and typical applications.
Principles of Operation
Wire EDM
Wire Electrical Discharge Machining (Wire EDM) is a non-traditional machining process that uses electrical discharges (sparks) to erode material. The fundamental principle of Wire EDM involves using a thin, electrically conductive wire as an electrode. This wire is typically made of brass, copper, or tungsten and is continuously fed through the material being cut.
The workpiece is submerged in a dielectric fluid, usually deionized water, which acts as an insulator and coolant. When a voltage is applied between the wire and the workpiece, an electric field is created. As the wire approaches the workpiece, the dielectric fluid ionizes, creating a plasma channel. This ionized path allows current to flow, generating sparks that erode the material. The eroded material is then flushed away by the dielectric fluid.
Laser Cutting
Laser cutting is a thermal cutting process that utilizes a high-powered laser beam to melt, burn, or vaporize material. The laser beam is generated by a laser source, such as a CO2, fiber, or Nd
A coaxial gas, typically oxygen, nitrogen, or air, is used to assist the cutting process by blowing away molten material and debris from the cutting zone. This results in a clean and precise cut. The laser cutting process can be performed in various modes, including continuous wave (CW) or pulsed mode, depending on the material and cutting requirements.
Material Compatibility
Wire EDM
Wire EDM is suitable for cutting electrically conductive materials, including metals such as steel, aluminum, titanium, copper, and their alloys. It can also be used to machine exotic materials like tungsten, carbide, and certain conductive ceramics. However, non-conductive materials like plastics, glass, and ceramics cannot be processed using Wire EDM.
One of the significant advantages of Wire EDM is its ability to machine hard and tough materials that are difficult to cut using conventional methods. It can achieve high precision and excellent surface finishes, making it ideal for applications requiring tight tolerances and intricate geometries.
Laser Cutting
Laser cutting is versatile in terms of material compatibility. It can cut a wide range of materials, including metals (steel, stainless steel, aluminum, brass, copper), non-metals (plastics, wood, paper, rubber), and composites. Different types of lasers are used depending on the material being cut. For instance, CO2 lasers are commonly used for cutting non-metals, while fiber lasers are preferred for cutting metals due to their high absorption rate in metals.
Laser cutting is particularly advantageous for non-metallic materials and thin metals, as it can achieve high cutting speeds and intricate shapes. However, the cutting quality and speed can vary depending on the material properties, thickness, and laser parameters.
Cutting Speed and Efficiency
Wire EDM
Wire EDM is known for its precision rather than speed. The cutting speed of Wire EDM is relatively slow compared to traditional machining processes and laser cutting. The cutting rate depends on several factors, including the material type, thickness, and desired surface finish. For thick and hard materials, the cutting process can be time-consuming.
Despite its slower cutting speed, Wire EDM excels in producing intricate and complex shapes with high accuracy. It is often used for applications where precision and surface finish are critical, such as aerospace components, medical devices, and molds.
Laser Cutting
Laser cutting is renowned for its high cutting speed and efficiency, especially when processing thin materials. The cutting speed depends on the laser power, material type, and thickness. Fiber lasers, in particular, offer high cutting speeds for metals, making them suitable for industrial applications requiring rapid production rates.
For thin sheets and non-metals, laser cutting can achieve cutting speeds that are orders of magnitude faster than Wire EDM. This makes laser cutting a preferred choice for industries like automotive, electronics, and signage, where high throughput and efficiency are essential.
Accuracy and Precision
Wire EDM
Wire EDM is celebrated for its exceptional accuracy and precision. It can achieve tight tolerances, typically in the range of ±0.001 to ±0.005 inches, and produce intricate geometries with sharp corners and fine details. The process is highly controlled, and the use of a continuously fed wire ensures consistent cutting performance.
The absence of mechanical forces during cutting eliminates issues like tool wear and deflection, resulting in highly accurate and repeatable cuts. This makes Wire EDM ideal for applications requiring complex shapes, precision tooling, and micro-machining.
Laser Cutting
Laser cutting also offers high precision, but the achievable tolerances depend on factors such as the material type, thickness, and laser parameters. Modern laser cutting systems can achieve tolerances in the range of ±0.002 to ±0.005 inches for thin materials. However, the precision may decrease for thicker materials due to the increased heat-affected zone and potential for material distortion.
Laser cutting is well-suited for applications requiring intricate shapes and fine details, especially in thin materials. It is widely used in industries like electronics, jewelry, and decorative arts, where precision and intricate designs are essential.
Surface Finish and Quality
Wire EDM
Wire EDM is known for producing excellent surface finishes, often eliminating the need for secondary finishing operations. The surface finish quality is influenced by factors such as the type of wire used, cutting speed, and the dielectric fluid. Typical surface finishes achieved with Wire EDM range from 16 to 32 microinches Ra (Roughness Average).
The absence of mechanical forces and tool wear during the EDM process contributes to the superior surface finish. Additionally, Wire EDM can produce sharp corners and fine details, making it suitable for applications requiring high surface quality and intricate features.
Laser Cutting
Laser cutting also produces high-quality surface finishes, particularly in thin materials. The quality of the cut surface depends on factors such as laser power, cutting speed, and assist gas. Laser-cut edges are typically smooth and require minimal post-processing.
However, the surface finish quality can vary based on the material properties and thickness. Thicker materials may exhibit a rougher edge due to the increased heat input and potential for material melting. For applications where surface finish is critical, laser cutting parameters can be optimized to achieve the desired quality.
Kerf Width and Material Loss
Wire EDM
The kerf width in Wire EDM is relatively narrow, typically ranging from 0.004 to 0.012 inches, depending on the wire diameter and cutting conditions. This narrow kerf width minimizes material loss and allows for precise cutting of intricate shapes with minimal waste.
Wire EDM's ability to produce narrow kerfs is advantageous for applications where material conservation is essential, such as in the aerospace and medical industries. The precise control over the cutting path also ensures minimal deviation from the desired geometry.
Laser Cutting
The kerf width in laser cutting varies depending on the material thickness, laser power, and focal length. For thin materials, the kerf width can be as narrow as 0.002 to 0.006 inches, while for thicker materials, it can range from 0.010 to 0.020 inches or more.
Laser cutting's relatively narrow kerf width is beneficial for applications requiring intricate shapes and fine details. However, the material loss due to the kerf width can be higher for thicker materials compared to Wire EDM. Optimizing the laser parameters can help minimize material loss and achieve precise cuts.
Heat-Affected Zone (HAZ)
Wire EDM
One of the significant advantages of Wire EDM is the minimal heat-affected zone (HAZ) it produces. Since the material removal is achieved through electrical discharges rather than thermal energy, the heat input is localized and controlled. This results in a small HAZ, reducing the risk of thermal distortion, material hardening, and microstructural changes.
The minimal HAZ in Wire EDM makes it suitable for applications requiring tight tolerances and high surface integrity. It is particularly beneficial for machining materials sensitive to heat, such as certain alloys and hardened steels.
Laser Cutting
Parts laser cutting, being a thermal process, generates a heat-affected zone (HAZ) around the cut edge. The size of the HAZ depends on factors such as laser power, cutting speed, and material properties. For thin materials, the HAZ is typically small and has minimal impact on the overall cut quality.
However, for thicker materials, the HAZ can be more pronounced, leading to potential issues like material distortion, hardening, and microstructural changes. Proper selection of laser parameters and assist gases can help minimize the HAZ and improve the cut quality.
Applications
Wire EDM
Wire EDM is widely used in industries requiring high precision, intricate shapes, and excellent surface finishes. Some common applications of Wire EDM include:
- Aerospace: Machining of turbine blades, fuel injectors, and complex components.
- Medical Devices: Manufacturing of surgical instruments, implants, and micro components.
- Tool and Die Making: Production of molds, dies, and precision tooling.
- Automotive: Machining of engine components, transmission parts, and prototypes.
- Electronics: Production of connectors, semiconductor components, and intricate circuit patterns.
Laser Cutting
Laser cutting is versatile and finds applications across various industries due to its high cutting speed, precision, and material compatibility. Some common applications of laser cutting include:
- Automotive: Cutting of body panels, exhaust systems, and interior components.
- Electronics: Fabrication of printed circuit boards (PCBs), enclosures, and electronic components.
- Signage and Display: Cutting of acrylic, plastics, and metals for signs, displays, and lettering.
- Jewelry: Precision cutting of metals and gemstones for intricate designs.
- Textiles: Cutting of fabrics and leather for fashion and apparel.
- Construction: Cutting of structural components, roofing, and cladding materials.
Cost and Economic Considerations
Wire EDM
The cost of Wire EDM machining depends on factors such as machine setup, material type, cutting speed, and desired surface finish. Wire EDM machines are generally expensive, and the process can be time-consuming, leading to higher operational costs. However, the precision and quality achieved with Wire EDM can offset these costs, especially for high-value applications.
Wire EDM is economically viable for low to medium volume production runs, where precision and intricate shapes are required. It is also suitable for prototyping and custom manufacturing due to its ability to produce complex geometries without the need for specialized tooling.
Laser Cutting
Laser cutting offers cost advantages, especially for high-volume production runs and thin materials. The high cutting speed and efficiency of laser cutting reduce production time and operational costs. Additionally, laser cutting systems have become more affordable and accessible, making them a popular choice for various industries.
The cost-effectiveness of laser cutting is particularly evident in applications requiring rapid production, intricate designs, and minimal post-processing. The ability to cut a wide range of materials also contributes to its economic viability in diverse manufacturing sectors.
Environmental Impact
Wire EDM
Wire EDM generates minimal waste and has a relatively low environmental impact compared to traditional machining processes. The dielectric fluid used in Wire EDM is typically water-based and can be recycled, reducing the environmental footprint. However, the process does generate some waste material in the form of eroded particles and used wire, which must be properly managed and disposed of.
The electrical energy consumption of Wire EDM is a consideration, but advancements in machine technology have led to more energy-efficient systems. Overall, Wire EDM is considered environmentally friendly, especially when proper waste management practices are followed.
Laser Cutting
Laser cutting also has a relatively low environmental impact, particularly when compared to conventional cutting methods. The use of assist gases, such as nitrogen and oxygen, helps achieve clean cuts and minimizes the need for post-processing. The waste material generated during laser cutting is typically limited to the cut-off sections, which can be recycled.
The energy consumption of laser cutting systems is a consideration, but modern lasers are designed to be energy-efficient. Additionally, the high cutting speed and precision of laser cutting reduce material waste, contributing to its environmental benefits.
Future Trends and Developments
Wire EDM
The future of Wire EDM is likely to see advancements in machine technology, software, and automation. Innovations such as multi-axis Wire EDM machines, improved wire materials, and enhanced dielectric fluids will further enhance the capabilities and efficiency of the process. Automation and integration with computer-aided design (CAD) and computer-aided manufacturing (CAM) systems will streamline the machining workflow and reduce setup times.
Research and development efforts are also focused on expanding the material compatibility of Wire EDM, enabling it to machine non-conductive materials through hybrid processes. This will open up new applications and industries for Wire EDM, further solidifying its position in precision manufacturing.
Laser Cutting
Laser cutting technology is continuously evolving, with advancements in laser sources, beam delivery systems, and cutting strategies. The development of higher-power lasers, such as ultra-short pulse lasers and high-brightness fiber lasers, will enhance cutting capabilities for thicker materials and challenging applications.
Integration of artificial intelligence (AI) and machine learning (ML) in laser cutting systems will enable real-time monitoring and optimization of cutting parameters, improving process efficiency and quality. Additionally, advancements in automation and robotics will further enhance the productivity and flexibility of laser cutting operations.
Sustainability and environmental considerations will also drive innovations in laser cutting, with a focus on reducing energy consumption and optimizing material utilization. The adoption of green manufacturing practices and the use of eco-friendly assist gases will contribute to the overall sustainability of laser cutting processes.
Conclusion
Wire EDM and Laser Cutting are two distinct and powerful manufacturing technologies, each with its unique advantages and applications. Wire EDM excels in precision machining of conductive materials, producing intricate shapes and excellent surface finishes with minimal heat-affected zones. It is ideal for industries requiring high accuracy and complex geometries.
Laser Cutting, on the other hand, offers high cutting speeds, versatility, and the ability to cut a wide range of materials, including non-metals and thin metals. It is well-suited for applications requiring rapid production, intricate designs, and minimal post-processing.
The choice between Wire EDM and Laser Cutting depends on specific requirements, including material type, thickness, precision, and production volume. Understanding the different aspects of these technologies enables manufacturers to make informed decisions and leverage the strengths of each process to achieve optimal results in their applications.
As technology continues to advance, both Wire EDM and Laser Cutting will evolve, offering new possibilities and pushing the boundaries of precision manufacturing. The ongoing research and development efforts will further enhance their capabilities, making them indispensable tools in the ever-changing landscape of modern manufacturing.
Reprint Statement: If there are no special instructions, all articles on this site are original. Please indicate the source for reprinting:https://www.cncmachiningptj.com/,thanks!
3, 4 and 5-axis precision CNC machining services for aluminum machining, beryllium, carbon steel, magnesium, titanium machining, Inconel, platinum, superalloy, acetal, polycarbonate, fiberglass, graphite and wood. Capable of machining parts up to 98 in. turning dia. and +/-0.001 in. straightness tolerance. Processes include milling, turning, drilling, boring, threading, tapping, forming, knurling, counterboring, countersinking, reaming and laser cutting. Secondary services such as assembly, centerless grinding, heat treating, plating and welding. Prototype and low to high volume production offered with maximum 50,000 units. Suitable for fluid power, pneumatics, hydraulics and valve applications. Serves the aerospace, aircraft, military, medical and defense industries.PTJ will strategize with you to provide the most cost-effective services to help you reach your target,Welcome to Contact us ( sales@pintejin.com ) directly for your new project.
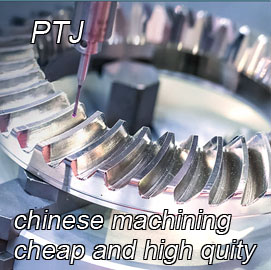
- 5 Axis Machining
- Cnc Milling
- Cnc Turning
- Machining Industries
- Machining Process
- Surface Treatment
- Metal Machining
- Plastic Machining
- Powder Metallurgy Mold
- Die Casting
- Parts Gallery
- Auto Metal Parts
- Machinery Parts
- LED Heatsink
- Building Parts
- Mobile Parts
- Medical Parts
- Electronic Parts
- Tailored Machining
- Bicycle Parts
- Aluminum Machining
- Titanium Machining
- Stainless Steel Machining
- Copper Machining
- Brass Machining
- Super Alloy Machining
- Peek Machining
- UHMW Machining
- Unilate Machining
- PA6 Machining
- PPS Machining
- Teflon Machining
- Inconel Machining
- Tool Steel Machining
- More Material