Types of Powder Coating Materials
Powder coating is a type of coating that is applied as a free-flowing, dry powder. Unlike conventional liquid paint, which is delivered via an evaporating solvent, powder coating is typically applied electrostatically and then cured under heat or with ultraviolet light. The powder may be a thermoplastic or a thermoset polymer. It is usually used to create a hard finish that is tougher than conventional paint. Powder coating is mainly used for coating of metals, such as household appliances, aluminum extrusions, drum hardware, and automobile and bicycle parts. Newer technologies allow other materials, such as MDF (medium-density fibreboard), to be powder coated using different methods. This article explores the various types of powder coating materials, their applications, benefits, and limitations.
History of Powder Coating
The process of powder coating was introduced in the 1940s and has evolved significantly over the decades. The development of thermosetting resins in the 1960s marked a significant milestone in the industry, leading to the broader adoption of powder coating for various applications. Since then, advancements in formulation, application technology, and curing methods have expanded the use of powder coatings across numerous industries.
Types of Powder Coating Materials
Powder coatings can be broadly classified into two categories: thermoplastic and thermoset. Each type has distinct characteristics and applications.
Thermoplastic Powder Coatings
Thermoplastic powder coatings do not undergo any chemical change when heated; instead, they melt and flow to form the coating. When cooled, they solidify into a durable, non-reactive layer. The primary types of thermoplastic powder coatings include:
Polyvinyl Chloride (PVC)
PVC powder coatings are known for their excellent chemical resistance, flexibility, and toughness. They are commonly used for coating wire goods, dishwasher baskets, and tool handles. PVC coatings offer good adhesion to metals and are resistant to water, acids, and alkalis. However, they may not be suitable for high-temperature applications due to their relatively low melting point.
Nylon
Nylon powder coatings are valued for their superior impact resistance, flexibility, and abrasion resistance. They are often used in applications requiring durable finishes, such as automotive parts, kitchen utensils, and outdoor furniture. Nylon coatings provide excellent protection against chemicals, solvents, and wear, but they can be more expensive compared to other types of powder coatings.
Polyester
Polyester thermoplastic powder coatings are widely used due to their excellent weatherability, UV resistance, and mechanical properties. They are commonly applied in outdoor applications, such as architectural components, fencing, and playground equipment. Polyester coatings are known for their durability and resistance to chipping, fading, and cracking.
Polyethylene
Polyethylene powder coatings offer good chemical resistance, low friction, and excellent electrical insulation properties. They are often used in applications where these properties are critical, such as coating wire and cable, pipe coatings, and automotive parts. Polyethylene coatings are relatively low-cost and provide a smooth, durable finish.
Thermoset Powder Coatings
Thermoset powder coatings undergo a chemical reaction during the curing process, forming a cross-linked polymer structure. This reaction makes the coating more resistant to heat and chemicals compared to thermoplastic coatings. The primary types of thermoset powder coatings include:
Epoxy
Epoxy powder coatings are known for their excellent adhesion, chemical resistance, and mechanical properties. They are commonly used in applications requiring robust protection, such as automotive parts, electrical components, and industrial equipment. Epoxy coatings provide superior corrosion resistance and are ideal for indoor applications, but they may degrade under prolonged UV exposure, making them less suitable for outdoor use.
Polyester
Polyester thermoset powder coatings are widely used for their excellent weatherability, UV resistance, and mechanical properties. They are suitable for both indoor and outdoor applications, including automotive parts, appliances, and furniture. Polyester coatings offer good flexibility, impact resistance, and color retention, making them a popular choice for various industries.
Epoxy-Polyester Hybrids
Epoxy-polyester hybrid powder coatings combine the advantages of both epoxy and polyester resins. They offer good adhesion, flexibility, and chemical resistance, along with improved UV stability compared to pure epoxy coatings. Hybrid coatings are commonly used in applications requiring a balance of properties, such as office furniture, lighting fixtures, and automotive components.
Acrylic
Acrylic powder coatings are known for their excellent clarity, gloss, and color retention. They are often used in applications requiring aesthetic appeal, such as automotive parts, consumer electronics, and decorative items. Acrylic coatings provide good UV resistance and weatherability, but they may not offer the same level of chemical resistance and mechanical properties as epoxy or polyester coatings.
Polyurethane
Polyurethane powder coatings are valued for their superior abrasion resistance, flexibility, and chemical resistance. They are commonly used in demanding applications, such as automotive parts, industrial equipment, and outdoor furniture. Polyurethane coatings provide excellent protection against weathering, chipping, and impact, making them suitable for both indoor and outdoor use.
Advantages of Powder Coating
Powder coating offers several advantages over conventional liquid coatings:
Environmental Benefits
- Low Emissions: Powder coating processes produce little to no volatile organic compounds (VOCs), reducing environmental impact and health risks.
- Waste Reduction: Overspray from powder coating can be collected and reused, minimizing waste and improving material efficiency.
- Energy Efficiency: Curing powder coatings generally require less energy compared to drying liquid paints, contributing to energy savings.
Performance Benefits
- Durability: Powder coatings provide a tough, durable finish that is resistant to chipping, scratching, and fading.
- Chemical Resistance: Many powder coatings offer excellent resistance to chemicals, solvents, and corrosion.
- Aesthetic Quality: Powder coatings can achieve high-quality finishes with a wide range of colors, textures, and gloss levels.
Application Benefits
- Ease of Application: Powder coating processes are relatively easy to automate, leading to consistent, high-quality finishes.
- Coverage Efficiency: Powder coatings can achieve thicker coatings in a single application compared to liquid paints, improving efficiency and coverage.
- Adhesion: Powder coatings typically offer superior adhesion to a variety of substrates, including metals and plastics.
Limitations of Powder Coating
While powder coating offers numerous benefits, it also has some limitations:
Substrate Limitations
- Heat Sensitivity: Some substrates, such as certain plastics and composites, may not withstand the high temperatures required for curing powder coatings.
- Conductivity: Powder coatings are typically applied electrostatically, requiring substrates to be electrically conductive. Non-conductive materials may require special pre-treatments.
Finish Limitations
- Color Matching: Achieving precise color matches can be challenging with powder coatings, particularly for small batches or custom colors.
- Surface Smoothness: Achieving extremely smooth finishes can be more difficult with powder coatings compared to liquid paints.
Equipment Costs
- Initial Investment: The equipment required for powder coating, such as spray guns, curing ovens, and recovery systems, can represent a significant initial investment.
Applications of Powder Coating Materials
Powder coating is used across a wide range of industries and applications due to its versatility and durability:
Automotive Industry
- Exterior Parts: Powder coatings are used for wheels, bumpers, and trim components, providing durability and aesthetic appeal.
- Interior Parts: Applications include seat frames, door handles, and other interior components requiring robust finishes.
Architectural and Construction
- Building Components: Powder coatings are applied to aluminum extrusions, window frames, and cladding for enhanced weather resistance and aesthetics.
- Furniture: Both indoor and outdoor furniture benefit from the durability and color options provided by powder coatings.
Industrial Equipment
- Machinery: Powder coatings protect machinery and equipment from corrosion, chemicals, and wear.
- Tools: Hand tools and industrial tools are coated for improved grip, durability, and resistance to environmental factors.
Consumer Goods
- Appliances: Household appliances, such as refrigerators, washing machines, and ovens, use powder coatings for protection and aesthetics.
- Sporting Goods: Bicycles, gym equipment, and other sporting goods are powder coated for durability and visual appeal.
Electrical Components
- Enclosures: Electrical enclosures and control panels are coated to protect against environmental factors and provide insulation.
- Hardware: Powder coatings are used for connectors, brackets, and other hardware requiring robust finishes.
Future Trends in Powder Coating Materials
The powder coating industry continues to evolve, driven by advancements in materials, technologies, and environmental considerations. Some emerging trends include:
Low-Cure Powder Coatings
Developments in low-cure powder coatings enable applications on heat-sensitive substrates and reduce energy consumption during curing.
High-Performance Coatings
Advances in resin formulations and additives are leading to powder coatings with enhanced performance characteristics, such as improved UV stability, higher chemical resistance, and increased flexibility.
Sustainable Solutions
The industry is focusing on sustainable practices, including the development of bio-based resins, recycling technologies, and reducing the environmental footprint of powder coating processes.
Digitalization and Automation
The integration of digital technologies and automation in powder coating processes is improving efficiency, consistency, and quality control.
Conclusion
Powder coating materials offer a versatile, durable, and environmentally friendly alternative to conventional liquid coatings. With a wide range of types, including thermoplastic and thermoset powders, powder coatings can meet the diverse needs of various industries and applications. While there are some limitations to consider, the advantages in terms of performance, environmental impact, and application efficiency make powder coatings an attractive choice for many manufacturers and consumers. As the industry continues to innovate and evolve, powder coating materials are poised to play an increasingly important role in modern manufacturing and surface finishing.
Reprint Statement: If there are no special instructions, all articles on this site are original. Please indicate the source for reprinting:https://www.cncmachiningptj.com/,thanks!
3, 4 and 5-axis precision CNC machining services for aluminum machining, beryllium, carbon steel, magnesium, titanium machining, Inconel, platinum, superalloy, acetal, polycarbonate, fiberglass, graphite and wood. Capable of machining parts up to 98 in. turning dia. and +/-0.001 in. straightness tolerance. Processes include milling, turning, drilling, boring, threading, tapping, forming, knurling, counterboring, countersinking, reaming and laser cutting. Secondary services such as assembly, centerless grinding, heat treating, plating and welding. Prototype and low to high volume production offered with maximum 50,000 units. Suitable for fluid power, pneumatics, hydraulics and valve applications. Serves the aerospace, aircraft, military, medical and defense industries.PTJ will strategize with you to provide the most cost-effective services to help you reach your target,Welcome to Contact us ( sales@pintejin.com ) directly for your new project.
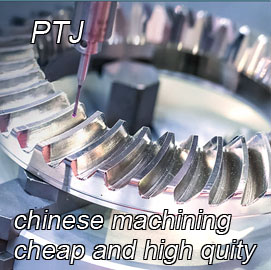
- 5 Axis Machining
- Cnc Milling
- Cnc Turning
- Machining Industries
- Machining Process
- Surface Treatment
- Metal Machining
- Plastic Machining
- Powder Metallurgy Mold
- Die Casting
- Parts Gallery
- Auto Metal Parts
- Machinery Parts
- LED Heatsink
- Building Parts
- Mobile Parts
- Medical Parts
- Electronic Parts
- Tailored Machining
- Bicycle Parts
- Aluminum Machining
- Titanium Machining
- Stainless Steel Machining
- Copper Machining
- Brass Machining
- Super Alloy Machining
- Peek Machining
- UHMW Machining
- Unilate Machining
- PA6 Machining
- PPS Machining
- Teflon Machining
- Inconel Machining
- Tool Steel Machining
- More Material