CNC Milling and Its Role in Cost Savings in Manufacturing
Computer Numerical Control (CNC) milling is a manufacturing process in which pre-programmed computer software dictates the movement of factory tools and machinery. The process can be used to control a range of complex machinery, from grinders and lathes to mills and routers. This technology has revolutionized the manufacturing industry, particularly in terms of cost savings and efficiency. This article explores the various ways in which CNC milling contributes to cost savings in manufacturing.
Historical Context
CNC technology emerged in the late 1940s and early 1950s. It was initially developed as a means to automate the control of machine tools through the use of early computers and punch cards. The advent of CNC milling allowed for unprecedented precision and repeatability, which laid the foundation for modern manufacturing techniques. Over the decades, advancements in software, hardware, and materials have significantly enhanced the capabilities and cost-effectiveness of CNC milling.
Precision and Accuracy
One of the primary benefits of CNC milling is its ability to produce parts with high precision and accuracy. This level of control reduces material waste and ensures that parts fit together perfectly, minimizing the need for costly rework or adjustments. Precision in manufacturing is critical in industries such as aerospace, automotive, and medical devices, where even minor deviations can lead to significant issues.
Reduced Material Waste
CNC milling minimizes material waste through precise cutting and shaping. Traditional manufacturing methods often result in significant waste due to human error or less accurate machinery. By optimizing material usage, manufacturers can reduce the costs associated with raw materials. Additionally, the reduction in waste contributes to more sustainable manufacturing practices, which can further enhance cost savings through waste management efficiencies.
Enhanced Repeatability
CNC milling ensures that each part produced is identical to the last. This repeatability is crucial in mass production, where consistent quality is essential. By maintaining uniformity, manufacturers can avoid the costs associated with quality control issues, product recalls, and customer dissatisfaction. The ability to produce identical parts with minimal variation also simplifies the assembly process, reducing labor costs and increasing overall production efficiency.
Labor Cost Reduction
CNC milling significantly reduces the need for manual labor. Once a CNC machine is programmed, it can operate with minimal human intervention, performing complex tasks that would otherwise require skilled labor. This automation not only lowers labor costs but also mitigates the risk of human error, further enhancing the efficiency and reliability of the manufacturing process.
Automation and Productivity
The automation provided by CNC milling machines allows for continuous operation, often 24/7, without the need for rest breaks or shift changes. This maximizes production output and minimizes downtime, leading to higher productivity and lower per-unit costs. Additionally, CNC machines can be programmed to perform multiple operations sequentially, further streamlining the manufacturing process.
Skilled Labor Optimization
While CNC milling reduces the need for manual labor, it does not eliminate the need for skilled workers entirely. Skilled machinists are still required to program and maintain CNC machines. However, their roles shift from manual operation to oversight and optimization, allowing them to focus on higher-level tasks. This optimization of skilled labor leads to more efficient use of human resources and can result in significant cost savings.
Flexibility and Customization
CNC milling offers unparalleled flexibility in manufacturing. The technology allows for rapid prototyping and easy adjustments to design specifications without the need for extensive retooling. This adaptability is particularly valuable in industries where custom parts or small production runs are common.
Rapid Prototyping
The ability to quickly produce prototypes accelerates the product development cycle. Designers can test and refine their concepts more rapidly, reducing the time to market. Faster development cycles lead to cost savings by shortening the duration of R&D projects and enabling companies to respond more swiftly to market demands.
Customization and Short Runs
CNC milling is highly adaptable to custom orders and short production runs. Traditional manufacturing methods often require significant setup and tooling costs, making them less cost-effective for small quantities. In contrast, CNC machines can be quickly reprogrammed for different tasks, allowing manufacturers to fulfill custom orders without incurring high setup costs. This flexibility makes CNC milling an ideal solution for industries that require bespoke parts or frequent design changes.
Quality Control and Consistency
Quality control is a critical aspect of manufacturing, and CNC milling enhances quality assurance through its precision and consistency. By reducing variability and ensuring that each part meets exact specifications, CNC milling minimizes defects and reduces the costs associated with quality control failures.
In-Process Monitoring
Many CNC machines are equipped with advanced monitoring systems that provide real-time feedback on the manufacturing process. This in-process monitoring allows for immediate detection and correction of deviations, reducing the likelihood of defects and rework. By maintaining tight control over the production process, manufacturers can achieve higher quality standards and reduce associated costs.
Consistent Quality
The consistent quality produced by CNC milling machines leads to higher customer satisfaction and lower warranty costs. Products that meet or exceed quality expectations are less likely to be returned or require costly repairs. Consistent quality also enhances a company’s reputation, potentially leading to increased sales and market share.
Inventory Management
CNC milling contributes to more efficient inventory management through just-in-time (JIT) manufacturing. JIT reduces the need for large inventories by producing parts as they are needed. This approach minimizes storage costs and reduces the financial risks associated with holding large quantities of stock.
Lean Manufacturing
Lean manufacturing principles, which focus on minimizing waste and maximizing efficiency, are closely aligned with the capabilities of CNC milling. By adopting lean practices, manufacturers can streamline their operations, reduce lead times, and lower overall production costs. CNC milling supports lean manufacturing by enabling precise control over production schedules and inventory levels.
Reduced Lead Times
The flexibility and efficiency of CNC milling result in shorter lead times for production. This reduction in lead times allows manufacturers to respond more quickly to customer orders and market changes. Faster turnaround times can enhance customer satisfaction and provide a competitive advantage, leading to increased sales and profitability.
Energy Efficiency
Modern CNC milling machines are designed with energy efficiency in mind. Advanced control systems and energy-saving features reduce power consumption during operation. Energy-efficient machinery lowers utility costs and contributes to more sustainable manufacturing practices.
Advanced Control Systems
CNC machines are equipped with sophisticated control systems that optimize energy usage during operation. These systems adjust power consumption based on the specific requirements of each task, reducing unnecessary energy expenditure. By minimizing energy consumption, manufacturers can lower their utility bills and reduce their environmental footprint.
Sustainable Manufacturing
Energy-efficient CNC milling contributes to sustainable manufacturing practices. Reducing energy consumption not only lowers costs but also supports environmental goals. Sustainable manufacturing practices can enhance a company’s reputation and appeal to environmentally conscious consumers, potentially leading to increased sales and market share.
Maintenance and Downtime
CNC milling machines require regular maintenance to ensure optimal performance. However, their advanced diagnostic and monitoring capabilities make maintenance more predictable and efficient. This predictability reduces unplanned downtime and the associated costs.
Predictive Maintenance
Many modern CNC machines are equipped with predictive maintenance systems that monitor the condition of components and provide early warnings of potential issues. By addressing maintenance needs proactively, manufacturers can prevent unexpected breakdowns and minimize downtime. Predictive maintenance extends the lifespan of machinery and reduces the costs associated with repairs and replacements.
Reduced Downtime
The reliability and durability of CNC milling machines contribute to reduced downtime. High-quality components and robust construction ensure that CNC machines can operate for extended periods without failure. By minimizing downtime, manufacturers can maintain continuous production and avoid the costs associated with production interruptions.
Conclusion
CNC milling has become a cornerstone of modern manufacturing, offering numerous cost-saving benefits. Its precision, accuracy, and repeatability reduce material waste and enhance product quality. Automation and advanced control systems lower labor and energy costs, while flexibility and customization capabilities support efficient production processes. Improved inventory management and predictive maintenance further contribute to cost savings. As CNC technology continues to evolve, its role in cost-effective manufacturing is likely to expand, driving further efficiencies and competitive advantages for manufacturers.
Reprint Statement: If there are no special instructions, all articles on this site are original. Please indicate the source for reprinting:https://www.cncmachiningptj.com/,thanks!
3, 4 and 5-axis precision CNC machining services for aluminum machining, beryllium, carbon steel, magnesium, titanium machining, Inconel, platinum, superalloy, acetal, polycarbonate, fiberglass, graphite and wood. Capable of machining parts up to 98 in. turning dia. and +/-0.001 in. straightness tolerance. Processes include milling, turning, drilling, boring, threading, tapping, forming, knurling, counterboring, countersinking, reaming and laser cutting. Secondary services such as assembly, centerless grinding, heat treating, plating and welding. Prototype and low to high volume production offered with maximum 50,000 units. Suitable for fluid power, pneumatics, hydraulics and valve applications. Serves the aerospace, aircraft, military, medical and defense industries.PTJ will strategize with you to provide the most cost-effective services to help you reach your target,Welcome to Contact us ( sales@pintejin.com ) directly for your new project.
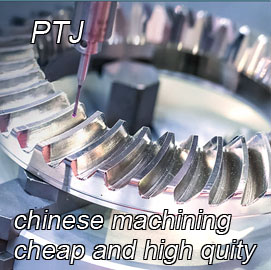
- 5 Axis Machining
- Cnc Milling
- Cnc Turning
- Machining Industries
- Machining Process
- Surface Treatment
- Metal Machining
- Plastic Machining
- Powder Metallurgy Mold
- Die Casting
- Parts Gallery
- Auto Metal Parts
- Machinery Parts
- LED Heatsink
- Building Parts
- Mobile Parts
- Medical Parts
- Electronic Parts
- Tailored Machining
- Bicycle Parts
- Aluminum Machining
- Titanium Machining
- Stainless Steel Machining
- Copper Machining
- Brass Machining
- Super Alloy Machining
- Peek Machining
- UHMW Machining
- Unilate Machining
- PA6 Machining
- PPS Machining
- Teflon Machining
- Inconel Machining
- Tool Steel Machining
- More Material