Is Powder Coating Better Than Liquid Paint?
Powder coating and liquid paint are two prominent methods used for applying finishes to surfaces, particularly metals. Both techniques serve the primary purpose of protecting and beautifying the surface they cover. While liquid paint has been around for centuries and is widely recognized, powder coating has gained substantial popularity in recent decades due to its distinct advantages. This article delves into the comparative aspects of powder coating and liquid paint, evaluating their benefits, drawbacks, applications, environmental impact, and future trends.
Historical Background
Evolution of Liquid Paint
Liquid paint has a long history dating back thousands of years. Early humans used natural pigments mixed with water or other binders to create rudimentary paints for decorating caves and pottery. The development of synthetic paints in the 20th century revolutionized the industry, offering improved durability, color range, and application methods.
Emergence of Powder Coating
Powder coating is a more recent innovation, emerging in the mid-20th century. Initially developed in the late 1940s and early 1950s, it was first used in industrial applications. The technique gained widespread acceptance in the 1970s due to advancements in technology and growing environmental concerns about the solvents used in liquid paints.
Application Process
Liquid Paint Application
Liquid paint can be applied using various methods, including brushes, rollers, and spray guns. The process generally involves the following steps:
- Surface Preparation: Cleaning and preparing the surface to ensure proper adhesion of the paint.
- Priming: Applying a primer to enhance adhesion and provide a uniform base for the topcoat.
- Painting: Applying one or more coats of liquid paint.
- Drying/Curing: Allowing the paint to dry and cure, which can take varying amounts of time depending on the type of paint and environmental conditions.
Powder Coating Application
Powder coating is applied as a dry powder and requires specialized equipment and procedures:
- Surface Preparation: Similar to liquid paint, the surface must be thoroughly cleaned and prepared.
- Application: Using an electrostatic gun, the powder is sprayed onto the surface. The electrostatic charge helps the powder adhere uniformly.
- Curing: The coated object is placed in an oven where the powder melts and flows, forming a continuous, durable finish.
Advantages and Disadvantages
Advantages of Powder Coating
- Durability: Powder coatings are highly durable and resistant to chipping, scratching, and fading.
- Environmental Impact: Powder coating is more environmentally friendly as it emits fewer volatile organic compounds (VOCs) compared to liquid paint.
- Efficiency: Overspray can be collected and reused, reducing waste.
- Finish Quality: Provides a uniform, high-quality finish with a variety of textures and colors.
Disadvantages of Powder Coating
- Initial Cost: The setup and equipment for powder coating can be more expensive than for liquid paint.
- Complexity: Requires specialized equipment and expertise.
- Limitations on Coating Thickness: Achieving very thin or very thick coatings can be challenging.
Advantages of Liquid Paint
- Versatility: Suitable for a wide range of surfaces and complex geometries.
- Lower Initial Cost: Generally, the initial investment is lower than for powder coating.
- Repairability: Easier to touch up or repair than powder-coated surfaces.
Disadvantages of Liquid Paint
- Durability: Generally less durable than powder coating, prone to chipping and scratching.
- Environmental Impact: Higher levels of VOC emissions and hazardous waste.
- Drying Time: Longer drying and curing times compared to powder coating.
Environmental Considerations
VOC Emissions
Liquid paints typically contain solvents that emit VOCs, which can contribute to air pollution and health issues. Powder coatings, being solvent-free, have significantly lower VOC emissions.
Waste Management
Powder coating overspray can be collected and reused, minimizing waste. Liquid paint overspray is often wasted and can pose disposal challenges.
Energy Consumption
Powder coating requires curing in an oven, which consumes energy. However, advancements in curing technologies are reducing energy requirements. Liquid paints also require energy for drying and curing, particularly in industrial applications.
Applications
Automotive Industry
Both liquid paint and powder coating are extensively used in the automotive industry. Powder coating is preferred for parts that require high durability and resistance to corrosion, such as wheels and underbody components. Liquid paint is often used for exterior body panels due to its superior finish quality and ease of application on complex shapes.
Architectural and Construction
In architectural and construction applications, powder coating is favored for its durability and weather resistance. It is commonly used for aluminum window frames, fencing, and metal roofing. Liquid paint is used for both interior and exterior applications, providing aesthetic versatility and ease of maintenance.
Consumer Goods
Powder coating is widely used in the manufacturing of consumer goods, including household appliances, furniture, and outdoor equipment, due to its durability and aesthetic appeal. Liquid paint is also used in consumer goods, particularly where intricate designs and color gradients are required.
Technological Advancements
Advancements in Powder Coating
Recent advancements in powder coating technology include low-temperature curing powders, which reduce energy consumption, and the development of powder coatings for heat-sensitive substrates such as plastics and wood. Additionally, innovations in application techniques and materials are expanding the range of possible finishes and textures.
Innovations in Liquid Paint
Liquid paint technology has also seen significant advancements, including the development of high-performance, low-VOC, and waterborne paints. These innovations aim to reduce the environmental impact while maintaining or enhancing the performance and finish quality of traditional solvent-based paints.
Future Trends
Sustainability
The future of both powder coating and liquid paint is likely to be heavily influenced by sustainability considerations. Manufacturers are increasingly adopting environmentally friendly practices, such as reducing VOC emissions, improving energy efficiency, and developing recyclable or biodegradable coatings.
Hybrid Technologies
Hybrid technologies that combine the benefits of powder coating and liquid paint are emerging. For example, liquid primers may be used in conjunction with powder topcoats to provide enhanced adhesion and performance.
Smart Coatings
The development of smart coatings, which can respond to environmental stimuli or provide additional functionalities such as self-healing, anti-microbial properties, or energy efficiency, is an exciting area of research and development in both powder coating and liquid paint industries.
Conclusion
The choice between powder coating and liquid paint depends on various factors, including the specific application, desired finish, environmental considerations, and cost constraints. Powder coating offers superior durability, environmental benefits, and efficiency, making it an excellent choice for many industrial and consumer applications. Liquid paint, with its versatility, ease of application, and lower initial cost, remains a popular option for a wide range of surfaces and applications. Both technologies continue to evolve, driven by advancements in materials science and increasing demand for sustainable and high-performance coatings. As these technologies advance, the distinctions between them may blur, leading to new hybrid solutions that combine the best of both worlds.
Reprint Statement: If there are no special instructions, all articles on this site are original. Please indicate the source for reprinting:https://www.cncmachiningptj.com/,thanks!
3, 4 and 5-axis precision CNC machining services for aluminum machining, beryllium, carbon steel, magnesium, titanium machining, Inconel, platinum, superalloy, acetal, polycarbonate, fiberglass, graphite and wood. Capable of machining parts up to 98 in. turning dia. and +/-0.001 in. straightness tolerance. Processes include milling, turning, drilling, boring, threading, tapping, forming, knurling, counterboring, countersinking, reaming and laser cutting. Secondary services such as assembly, centerless grinding, heat treating, plating and welding. Prototype and low to high volume production offered with maximum 50,000 units. Suitable for fluid power, pneumatics, hydraulics and valve applications. Serves the aerospace, aircraft, military, medical and defense industries.PTJ will strategize with you to provide the most cost-effective services to help you reach your target,Welcome to Contact us ( sales@pintejin.com ) directly for your new project.
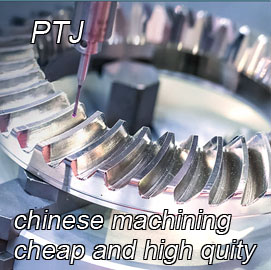
- 5 Axis Machining
- Cnc Milling
- Cnc Turning
- Machining Industries
- Machining Process
- Surface Treatment
- Metal Machining
- Plastic Machining
- Powder Metallurgy Mold
- Die Casting
- Parts Gallery
- Auto Metal Parts
- Machinery Parts
- LED Heatsink
- Building Parts
- Mobile Parts
- Medical Parts
- Electronic Parts
- Tailored Machining
- Bicycle Parts
- Aluminum Machining
- Titanium Machining
- Stainless Steel Machining
- Copper Machining
- Brass Machining
- Super Alloy Machining
- Peek Machining
- UHMW Machining
- Unilate Machining
- PA6 Machining
- PPS Machining
- Teflon Machining
- Inconel Machining
- Tool Steel Machining
- More Material