From Molten Metal to Precision Parts: Exploring the Magnesium Die Casting Process
Magnesium die casting is a manufacturing process that produces complex, high-precision parts using molten magnesium. Known for its light weight, excellent strength-to-weight ratio, and superior machinability, magnesium has become a crucial material in various industries, including automotive, aerospace, electronics, and consumer goods. This article delves into the intricacies of the magnesium die casting and magnesium cnc machining process, exploring its history, materials, methods, advantages, challenges, and applications.
Historical Overview
Early Developments
The use of magnesium in casting dates back to the early 20th century. The initial foray into magnesium casting began with the development of lightweight alloys for military applications during World War I. However, the widespread adoption of magnesium die casting emerged post-World War II, driven by the need for lighter materials in automotive and aerospace sectors.
Evolution of Techniques
The evolution of die casting techniques significantly influenced the utilization of magnesium. Initially, gravity casting was the predominant method, but advancements in technology led to the development of pressure die casting, which offered superior precision and efficiency. The introduction of hot chamber die casting further revolutionized the industry, allowing for faster production cycles and enhanced control over the casting process.
Materials and Properties
Magnesium Alloys
Magnesium alloys are primarily composed of magnesium, with varying amounts of other elements such as aluminum, zinc, manganese, silicon, and rare earth metals. The choice of alloy depends on the specific requirements of the application. Common magnesium alloys used in die casting include AZ91D, AM60, and AM50. These alloys offer a balance of strength, ductility, and corrosion resistance.
Properties of Magnesium
Magnesium boasts several desirable properties that make it an ideal material for die casting. It is the lightest structural metal, with a density approximately two-thirds that of aluminum and one-fourth that of steel. Magnesium also exhibits excellent castability, allowing for the production of complex shapes with thin walls. Additionally, it has good machinability, high thermal conductivity, and excellent electromagnetic shielding properties.
The Die Casting Process
Overview
Magnesium die casting involves injecting molten magnesium into a mold cavity under high pressure. The magnesiumm de casting and magnesium cnc machining process can be broadly classified into two main types: hot chamber die casting and cold chamber die casting. Each method has its advantages and is suited for different applications.
Hot Chamber Die Casting
Hot chamber die casting, also known as gooseneck casting, is the preferred method for casting magnesium due to its relatively low melting point. In this process, the molten magnesium is kept in a reservoir, and a plunger mechanism injects the metal into the die cavity. The key components of a hot chamber die casting machine include the gooseneck, plunger, die, and cooling system.
-
Melting and Holding Furnace: The magnesium alloy is melted in a furnace and maintained at a specific temperature in a holding furnace. The molten metal is transferred to the gooseneck.
-
Injection: The plunger forces the molten metal through the gooseneck into the die cavity at high pressure, typically ranging from 7,000 to 15,000 psi (48 to 103 MPa).
-
Solidification: The molten metal rapidly solidifies upon contact with the cooler surfaces of the die, forming the desired shape.
-
Ejection and Cooling: Once the part solidifies, the die opens, and ejector pins push the casting out. The part is then cooled, and any excess material, such as flash, is removed.
Cold Chamber Die Casting
Cold chamber die casting is used for metals with higher melting points, such as aluminum and copper. In this process, the molten metal is poured into a cold chamber, and a piston forces it into the die cavity. While less common for magnesium, cold chamber die casting is sometimes used for specific applications.
-
Melting and Holding Furnace: Similar to hot chamber casting, the magnesium alloy is melted and maintained in a holding furnace.
-
Pouring: The molten metal is manually ladled or poured into the shot sleeve of the cold chamber machine.
-
Injection: A hydraulic piston pushes the metal from the shot sleeve into the die cavity at high pressure.
-
Solidification: The metal solidifies quickly upon contact with the die surfaces.
-
Ejection and Cooling: The die opens, ejector pins release the part, and it undergoes cooling and finishing processes.
Advantages of Magnesium Die Casting
Lightweight
One of the primary advantages of magnesium die casting is the significant weight reduction it offers compared to other metals. This attribute is especially crucial in industries like automotive and aerospace, where reducing weight directly impacts fuel efficiency and performance.
High Strength-to-Weight Ratio
Magnesium alloys possess a high strength-to-weight ratio, making them suitable for applications that require robust yet lightweight components. This characteristic is particularly valuable in the production of structural parts and components subject to mechanical stress.
Excellent Machinability
Magnesium alloys are known for their exceptional machinability, allowing for precise and efficient post-casting operations such as drilling, milling, and threading. This property contributes to cost-effective manufacturing and shorter production cycles.
Superior Electromagnetic Shielding
Magnesium alloys exhibit excellent electromagnetic shielding properties, making them ideal for electronic enclosures and components. This capability is increasingly important in modern electronics, where electromagnetic interference can affect performance and reliability.
Good Thermal Conductivity
The high thermal conductivity of magnesium alloys enables efficient heat dissipation, making them suitable for applications requiring thermal management, such as heat sinks and electronic housings.
Challenges and Solutions
Corrosion Resistance
While magnesium alloys offer many benefits, they are susceptible to corrosion, especially in environments with high humidity or exposure to salts. To mitigate this issue, protective coatings such as anodizing, conversion coatings, and paint are applied to enhance corrosion resistance.
Flammability
Magnesium is highly flammable, particularly in its molten state. Stringent safety measures and equipment designs are implemented to minimize the risk of ignition. This includes proper ventilation, controlled atmospheres, and the use of fire-resistant materials.
Dimensional Stability
Maintaining dimensional stability during the cooling and solidification process can be challenging due to magnesium's high shrinkage rate. Precision die design, controlled cooling rates, and the use of advanced simulation software help achieve accurate and consistent dimensions.
Applications of Magnesium Die Casting
Automotive Industry
Magnesium die casting plays a vital role in the automotive industry, where reducing vehicle weight is essential for improving fuel efficiency and performance. Common applications include engine components, transmission housings, steering wheels, and dashboard frames. The light weight of magnesium helps lower the overall vehicle weight, contributing to reduced emissions and better fuel economy.
Aerospace Industry
In the aerospace sector, magnesium die casting is used to manufacture components that require high strength, lightweight, and excellent thermal conductivity. Examples include aircraft engine housings, landing gear components, and interior cabin parts. The reduction in weight provided by magnesium alloys enhances aircraft performance and fuel efficiency.
Electronics and Consumer Goods
Magnesium die casting is increasingly utilized in the electronics industry for producing lightweight, durable, and electromagnetically shielded enclosures for laptops, smartphones, tablets, and other electronic devices. Additionally, magnesium alloys are used in the manufacture of various consumer goods, such as camera bodies, power tools, and sporting equipment, where their light weight and strength are advantageous.
Future Trends and Innovations
Advanced Alloys
Research and development efforts continue to focus on creating advanced magnesium alloys with improved properties, such as increased strength, enhanced corrosion resistance, and better formability. These innovations aim to expand the range of applications for magnesium die casting and overcome existing limitations.
Additive Manufacturing Integration
The integration of additive manufacturing (3D printing) with die casting processes is an emerging trend. This hybrid approach combines the design flexibility of 3D printing with the high-volume production capabilities of die casting, enabling the creation of complex geometries and customized components.
Sustainability and Recycling
As sustainability becomes a growing concern, the magnesium die casting industry is exploring ways to reduce its environmental footprint. Efforts include improving energy efficiency in casting processes, developing more sustainable alloys, and enhancing recycling methods to minimize waste and promote the circular economy.
Conclusion
Magnesium die casting is a versatile and efficient manufacturing process that has revolutionized various industries by providing lightweight, high-strength, and precisely engineered components. Despite challenges such as corrosion and flammability, ongoing advancements in materials and technology continue to expand the potential of magnesium die casting. As industries strive for lighter, more efficient, and sustainable solutions, magnesium die casting will undoubtedly play a pivotal role in shaping the future of manufacturing.
References
- Davis, J.R. (1993). ASM Specialty Handbook: Magnesium and Magnesium Alloys. ASM International.
- Luo, A.A. (2004). "Magnesium casting technology for structural applications." Journal of Magnesium and Alloys, 2(1), 2-14.
- Mordike, B.L., & Ebert, T. (2001). "Magnesium properties—applications—potential." Materials Science and Engineering: A, 302(1), 37-45.
- Polmear, I.J. (2006). Light Alloys: Metallurgy of the Light Metals. Elsevier.
- Schaffer, P., Dahle, A.K., & StJohn, D.H. (2006). "The role of alloying and grain refinement in the development of magnesium alloys for automotive applications." Materials Science Forum, 519-521, 49-54.
Reprint Statement: If there are no special instructions, all articles on this site are original. Please indicate the source for reprinting:https://www.cncmachiningptj.com/,thanks!
3, 4 and 5-axis precision CNC machining services for aluminum machining, beryllium, carbon steel, magnesium, titanium machining, Inconel, platinum, superalloy, acetal, polycarbonate, fiberglass, graphite and wood. Capable of machining parts up to 98 in. turning dia. and +/-0.001 in. straightness tolerance. Processes include milling, turning, drilling, boring, threading, tapping, forming, knurling, counterboring, countersinking, reaming and laser cutting. Secondary services such as assembly, centerless grinding, heat treating, plating and welding. Prototype and low to high volume production offered with maximum 50,000 units. Suitable for fluid power, pneumatics, hydraulics and valve applications. Serves the aerospace, aircraft, military, medical and defense industries.PTJ will strategize with you to provide the most cost-effective services to help you reach your target,Welcome to Contact us ( sales@pintejin.com ) directly for your new project.
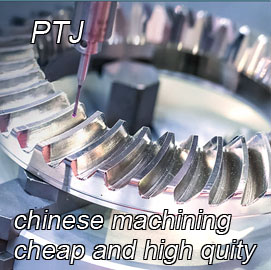
- 5 Axis Machining
- Cnc Milling
- Cnc Turning
- Machining Industries
- Machining Process
- Surface Treatment
- Metal Machining
- Plastic Machining
- Powder Metallurgy Mold
- Die Casting
- Parts Gallery
- Auto Metal Parts
- Machinery Parts
- LED Heatsink
- Building Parts
- Mobile Parts
- Medical Parts
- Electronic Parts
- Tailored Machining
- Bicycle Parts
- Aluminum Machining
- Titanium Machining
- Stainless Steel Machining
- Copper Machining
- Brass Machining
- Super Alloy Machining
- Peek Machining
- UHMW Machining
- Unilate Machining
- PA6 Machining
- PPS Machining
- Teflon Machining
- Inconel Machining
- Tool Steel Machining
- More Material