CNC Turning Affected the Cost of Different Types of Manufactured Goods
CNC turning, a sophisticated method of production involving computer numerical control (CNC) machines, has profoundly transformed the manufacturing landscape. This process employs computerized systems to control machinery, particularly lathes, to produce intricate and precise parts by removing material from a workpiece. The evolution of CNC turning has influenced various sectors, notably in reducing production costs and enhancing efficiency. This article delves into the multifaceted impact of CNC turning on the cost structure of different types of manufactured goods, exploring historical context, technological advancements, economic implications, and industry-specific effects.
Historical Context of CNC Turning
Early Manufacturing Techniques
Prior to the advent of CNC turning, traditional machining methods were predominantly manual. Craftsmen relied on skills honed over years to produce parts with hand-operated tools. While this approach allowed for a high degree of customization, it was time-consuming, labor-intensive, and prone to human error. These limitations resulted in higher production costs and slower turnaround times.
Emergence of CNC Technology
The mid-20th century marked a significant shift with the introduction of numerical control (NC) technology. Early NC machines utilized punched tape to control the movements of machinery. However, the real revolution came with the development of CNC systems, which incorporated digital computing technology. This advancement allowed for greater precision, repeatability, and automation, setting the stage for the widespread adoption of CNC turning.
Technological Advancements in CNC Turning
Precision and Accuracy
CNC turning machines are renowned for their precision. The integration of advanced software and high-resolution encoders enables these machines to achieve tolerances within micrometers. This level of accuracy is crucial for industries requiring exact specifications, such as aerospace and medical device manufacturing. By minimizing deviations and errors, CNC turning reduces the need for rework and scrap, thereby lowering production costs.
Automation and Efficiency
Automation is a hallmark of CNC turning. Once programmed, CNC machines can operate continuously with minimal human intervention. This capability significantly boosts productivity, as machines can run 24/7 without fatigue. Automation also facilitates mass production, allowing manufacturers to scale operations and reduce per-unit costs. The efficiency gained from CNC turning translates to faster turnaround times and improved overall throughput.
Material Utilization
CNC turning optimizes material utilization through precise cutting and shaping techniques. Traditional machining methods often result in significant material waste, especially when producing complex geometries. CNC machines, on the other hand, can maximize the use of raw materials by employing advanced toolpaths and minimizing excess removal. This efficiency not only conserves resources but also reduces material costs.
Integration with Computer-Aided Design (CAD) and Computer-Aided Manufacturing (CAM)
The synergy between CNC turning and CAD/CAM software has revolutionized the manufacturing process. CAD allows engineers to design parts with intricate details, which can be directly translated into CNC machine instructions via CAM software. This seamless integration streamlines the design-to-production workflow, reducing lead times and minimizing the risk of errors. The ability to quickly modify designs and implement changes further enhances cost efficiency.
Economic Implications of CNC Turning
Reduction in Labor Costs
One of the most significant economic impacts of CNC turning is the reduction in labor costs. Traditional machining required skilled machinists to manually operate equipment, perform measurements, and make adjustments. With CNC turning, a single operator can oversee multiple machines, as the programming and operation are largely automated. This shift reduces the reliance on manual labor, leading to cost savings in wages and training.
Increased Production Speed
The speed at which CNC turning machines operate directly influences production costs. High-speed machining capabilities enable faster cycle times, allowing manufacturers to produce more parts in a shorter period. This acceleration in production reduces overhead costs associated with prolonged manufacturing processes. Additionally, the ability to quickly switch between different part designs without extensive setup changes enhances operational flexibility.
Consistency and Quality Control
CNC turning ensures consistent quality across large production runs. The repeatability of CNC machines eliminates variations that can occur with manual machining, resulting in uniform parts that meet stringent quality standards. This consistency reduces the likelihood of defects and rejections, minimizing the costs associated with quality control and product recalls. Moreover, the high-quality output enhances customer satisfaction and strengthens brand reputation.
Customization and Prototyping
CNC turning offers a cost-effective solution for customization and prototyping. The flexibility of CNC programming allows manufacturers to produce small batches or one-off parts without significant retooling expenses. This capability is particularly valuable for industries requiring rapid prototyping and iterative design processes. By facilitating quick adjustments and modifications, CNC turning accelerates product development and reduces time-to-market.
Industry-Specific Effects of CNC Turning
Automotive Industry
In the automotive sector, CNC turning has revolutionized the production of engine components, transmission parts, and other critical elements. The precision and speed of CNC machines enable manufacturers to meet tight tolerances and high-volume demands. By optimizing material usage and reducing scrap, CNC turning contributes to cost savings in raw materials. Additionally, the ability to produce complex geometries enhances the performance and efficiency of automotive parts, driving innovation and competitiveness.
Aerospace Industry
The aerospace industry demands the highest levels of precision and reliability. CNC turning plays a pivotal role in manufacturing components for aircraft engines, landing gear, and structural elements. The stringent quality requirements necessitate the use of advanced CNC technology to achieve flawless results. CNC turning's ability to handle exotic materials, such as titanium and Inconel, is crucial for aerospace applications. The efficiency and accuracy of CNC turning help reduce production costs while maintaining compliance with rigorous industry standards.
Medical Device Manufacturing
CNC turning is integral to the production of medical devices, including surgical instruments, implants, and diagnostic equipment. The precision and cleanliness of CNC-machined parts are essential for ensuring patient safety and regulatory compliance. CNC turning allows for the creation of intricate designs and micro-scale features required in medical devices. By streamlining production and reducing lead times, CNC turning supports the rapid development and commercialization of innovative medical technologies.
Electronics and Technology
In the electronics and technology sector, CNC turning is employed to manufacture components such as connectors, housings, and heat sinks. The miniaturization trend in electronics demands high-precision machining capabilities, which CNC turning readily provides. The ability to produce complex shapes and fine details is crucial for electronic components. CNC turning's efficiency and accuracy contribute to cost-effective production, enabling the industry to keep pace with rapid technological advancements and market demands.
Industrial Equipment and Machinery
CNC turning is widely used in the production of industrial equipment and machinery parts. Components such as gears, shafts, and bearings require precise machining to ensure optimal performance and durability. CNC turning enhances the reliability and longevity of industrial machinery by producing high-quality, consistent parts. The reduction in maintenance and downtime costs, coupled with efficient production processes, results in overall cost savings for manufacturers and end-users.
Conclusion
CNC turning has undeniably revolutionized the manufacturing industry by significantly affecting the cost structure of various types of manufactured goods. Through technological advancements, increased precision, automation, and integration with CAD/CAM software, CNC turning has reduced labor costs, enhanced production speed, improved material utilization, and ensured consistent quality. These benefits translate into substantial economic advantages across multiple industries, including automotive, aerospace, medical device manufacturing, electronics, and industrial equipment.
The ongoing development and adoption of CNC turning technology continue to shape the future of manufacturing. As CNC machines become more advanced and accessible, their impact on cost reduction and efficiency is expected to grow. By embracing CNC turning, manufacturers can remain competitive in a rapidly evolving market, delivering high-quality products at reduced costs while meeting the demands of modern consumers and industries.
Reprint Statement: If there are no special instructions, all articles on this site are original. Please indicate the source for reprinting:https://www.cncmachiningptj.com/,thanks!
3, 4 and 5-axis precision CNC machining services for aluminum machining, beryllium, carbon steel, magnesium, titanium machining, Inconel, platinum, superalloy, acetal, polycarbonate, fiberglass, graphite and wood. Capable of machining parts up to 98 in. turning dia. and +/-0.001 in. straightness tolerance. Processes include milling, turning, drilling, boring, threading, tapping, forming, knurling, counterboring, countersinking, reaming and laser cutting. Secondary services such as assembly, centerless grinding, heat treating, plating and welding. Prototype and low to high volume production offered with maximum 50,000 units. Suitable for fluid power, pneumatics, hydraulics and valve applications. Serves the aerospace, aircraft, military, medical and defense industries.PTJ will strategize with you to provide the most cost-effective services to help you reach your target,Welcome to Contact us ( sales@pintejin.com ) directly for your new project.
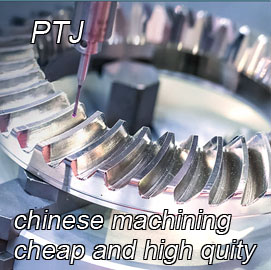
- 5 Axis Machining
- Cnc Milling
- Cnc Turning
- Machining Industries
- Machining Process
- Surface Treatment
- Metal Machining
- Plastic Machining
- Powder Metallurgy Mold
- Die Casting
- Parts Gallery
- Auto Metal Parts
- Machinery Parts
- LED Heatsink
- Building Parts
- Mobile Parts
- Medical Parts
- Electronic Parts
- Tailored Machining
- Bicycle Parts
- Aluminum Machining
- Titanium Machining
- Stainless Steel Machining
- Copper Machining
- Brass Machining
- Super Alloy Machining
- Peek Machining
- UHMW Machining
- Unilate Machining
- PA6 Machining
- PPS Machining
- Teflon Machining
- Inconel Machining
- Tool Steel Machining
- More Material