The Types of Laser Cutting Gases in Sheet Metal Fabrication
Laser cutting is a widely utilized technology in the field of sheet metal fabrication, owing to its precision, speed, and versatility. Central to the effectiveness of laser cutting are the gases used during the process. These gases, known as laser cutting gases, play crucial roles in the cutting mechanism, influencing the quality, efficiency, and type of cuts achievable. This article explores the various types of laser cutting gases, their roles, and their applications in sheet metal fabrication.
Introduction to Laser Cutting
Laser cutting is a thermal-based material processing method that employs a high-powered laser beam to cut, engrave, or mark materials. The process involves focusing a laser beam onto a material, which absorbs the light and converts it into heat, causing localized melting, burning, or vaporization. The process is controlled by a computer, allowing for high precision and complex designs.
The core components of a laser cutting system include the laser source, optics (such as lenses and mirrors), and a motion control system. However, the choice of assist gas, often referred to as laser cutting gas, is equally critical to the process.
The Role of Laser Cutting Gases
Laser cutting gases serve multiple purposes in the cutting process:
-
Assisting in Material Removal: The primary function of cutting gases is to aid in the removal of molten material from the cutting kerf (the gap made by the cutting process). This ensures a cleaner cut and prevents re-solidification of the molten material, which can affect the quality of the cut edge.
-
Cooling the Workpiece and Cutting Area: Gases can help dissipate heat from the cutting zone, preventing overheating and potential damage to the workpiece.
-
Protecting the Optics: Gases can protect the laser optics from contamination by debris and vapors generated during cutting, thereby extending the lifespan of the optics and maintaining cutting quality.
-
Enhancing the Cutting Process: Different gases can influence the cutting process by reacting chemically with the material being cut. This can either improve the cutting speed or the quality of the cut surface.
Types of Laser Cutting Gases
The choice of laser cutting gas depends on several factors, including the type of material being cut, the thickness of the material, and the desired quality of the cut. The main types of laser cutting gases used in sheet metal fabrication are:
1. Oxygen (O₂)
Oxygen is commonly used in laser cutting, especially for cutting carbon steel. The primary advantages of using oxygen include:
- Exothermic Reaction: When oxygen is used as the assist gas, it reacts with the metal to form metal oxides, which release additional heat. This exothermic reaction increases the cutting speed, making oxygen an excellent choice for cutting thick carbon steel.
- Improved Piercing Performance: Oxygen helps in piercing thicker materials more efficiently.
However, using oxygen can lead to the formation of oxide layers on the cut edge, which may require post-processing to remove, especially if painting or coating is required.
2. Nitrogen (N₂)
Nitrogen is another widely used laser cutting gas, particularly for cutting stainless steel, aluminum, and other non-ferrous metals. The benefits of using nitrogen include:
- Non-Reactiveness: Nitrogen is an inert gas and does not react with the molten metal. This results in clean, oxide-free edges, which are essential for applications where the appearance of the cut edge is critical.
- High-Quality Cuts: Nitrogen helps achieve high-quality cuts with smooth edges, reducing the need for additional finishing processes.
The primary drawback of using nitrogen is the slower cutting speed compared to oxygen, especially for thicker materials.
3. Argon (Ar)
Argon is an inert gas used in laser cutting, particularly for materials like titanium and copper. Its main advantages are:
- Inert Atmosphere: Argon creates an inert atmosphere around the cutting area, preventing oxidation and ensuring high-quality, clean cuts.
- Protection of Sensitive Materials: Argon is beneficial for cutting materials that are highly reactive or prone to oxidation, such as titanium.
However, the use of argon is generally more expensive compared to nitrogen and oxygen, which can increase operational costs.
4. Compressed Air
Compressed air is an economical alternative to pure gases like nitrogen and oxygen. It is often used for cutting thinner sheets of metal and non-metals. The advantages of using compressed air include:
- Cost-Effectiveness: Compressed air is cheaper and readily available compared to other gases, making it a cost-effective option for certain applications.
- Adequate Quality for Non-Critical Applications: For applications where the highest quality cut is not essential, compressed air can provide acceptable results.
However, the quality of the cut edge may not be as high as with pure gases, and the cutting speed can be slower.
5. Helium (He)
Helium is less commonly used in laser cutting but has specific applications where its properties are advantageous. The benefits of helium include:
- High Thermal Conductivity: Helium's high thermal conductivity helps in dissipating heat efficiently, making it suitable for cutting materials that are prone to heat damage.
- Inert Atmosphere: Like argon, helium provides an inert atmosphere, preventing oxidation and ensuring clean cuts.
The primary disadvantages of helium are its high cost and limited availability, making it a less common choice in laser cutting applications.
Selection of Laser Cutting Gases
The selection of the appropriate laser cutting gas depends on several factors:
- Material Type: Different materials require different gases for optimal cutting performance. For example, oxygen is preferred for carbon steel, while nitrogen is better for stainless steel and aluminum.
- Material Thickness: The thickness of the material affects the choice of gas. Thicker materials benefit from the exothermic reaction of oxygen, while thinner materials can be cut effectively with nitrogen or compressed air.
- Desired Cut Quality: The required quality of the cut edge influences the gas selection. For high-quality, oxide-free edges, nitrogen or argon are preferred.
- Cost Considerations: The cost of the gas and the overall operational cost are important factors. Compressed air is the most economical option, while argon and helium are more expensive.
- Cutting Speed: The desired cutting speed can also affect the choice of gas. Oxygen provides higher cutting speeds due to its exothermic reaction, while nitrogen offers slower speeds but better edge quality.
Applications in Sheet Metal Fabrication
Laser cutting gases find applications in various industries and processes within sheet metal fabrication:
Automotive Industry
In the automotive industry, laser cutting is used for manufacturing components such as body panels, frames, and intricate parts. Nitrogen is commonly used to achieve high-quality cuts and smooth edges, which are crucial for assembly and painting processes.
Aerospace Industry
The aerospace industry requires precision and high-quality cuts for components like turbine blades, structural parts, and airframes. Argon and nitrogen are often used to ensure clean, oxidation-free cuts, particularly for materials like titanium and aluminum.
Electronics Industry
In the electronics industry, laser cutting is used for producing intricate components and enclosures for electronic devices. Nitrogen and compressed air are used to achieve fine cuts and smooth edges, essential for the assembly of electronic components.
Medical Device Manufacturing
Laser cutting is employed in the manufacturing of medical devices, including surgical instruments and implants. High-quality cuts with minimal thermal damage are essential, making nitrogen and argon the preferred gases for cutting stainless steel and titanium.
Metal Fabrication and Welding
In general metal fabrication and welding, laser cutting is used for producing parts and components for various industries. The choice of gas depends on the material and the required cut quality. Oxygen is often used for cutting carbon steel, while nitrogen and argon are used for stainless steel and aluminum.
Advances in Laser Cutting Gas Technology
The field of laser cutting gases is continuously evolving, with advancements aimed at improving efficiency, quality, and cost-effectiveness. Some of the recent developments include:
Gas Mixtures
Innovative gas mixtures are being developed to combine the benefits of different gases. For example, a mixture of nitrogen and oxygen can provide a balance between cutting speed and edge quality, making it suitable for specific applications.
High-Pressure Gas Delivery Systems
High-pressure gas delivery systems are being used to enhance the cutting performance, especially for thicker materials. These systems ensure a consistent and high-flow rate of gas, improving the efficiency of the cutting process.
Automation and Control Systems
Advanced automation and control systems are being integrated into laser cutting machines to optimize gas usage. These systems adjust the gas flow and pressure in real-time based on the cutting parameters, material type, and thickness, ensuring optimal performance.
Environmentally Friendly Gases
Research is being conducted to identify and develop environmentally friendly laser cutting gases. The goal is to reduce the environmental impact of laser cutting processes while maintaining or improving cutting performance.
Conclusion
Laser cutting gases play a pivotal role in the efficiency, quality, and versatility of laser cutting processes in sheet metal fabrication. The choice of gas depends on several factors, including the material type, thickness, desired cut quality, and cost considerations. Oxygen, nitrogen, argon, compressed air, and helium are the primary gases used, each offering distinct advantages and applications. As technology advances, the development of innovative gas mixtures, high-pressure delivery systems, and automation solutions will continue to enhance the capabilities of laser cutting in various industries. Understanding the properties and applications of different laser cutting gases is essential for optimizing the performance and outcomes of laser cutting processes in sheet metal fabrication.
Reprint Statement: If there are no special instructions, all articles on this site are original. Please indicate the source for reprinting:https://www.cncmachiningptj.com/,thanks!
3, 4 and 5-axis precision CNC machining services for aluminum machining, beryllium, carbon steel, magnesium, titanium machining, Inconel, platinum, superalloy, acetal, polycarbonate, fiberglass, graphite and wood. Capable of machining parts up to 98 in. turning dia. and +/-0.001 in. straightness tolerance. Processes include milling, turning, drilling, boring, threading, tapping, forming, knurling, counterboring, countersinking, reaming and laser cutting. Secondary services such as assembly, centerless grinding, heat treating, plating and welding. Prototype and low to high volume production offered with maximum 50,000 units. Suitable for fluid power, pneumatics, hydraulics and valve applications. Serves the aerospace, aircraft, military, medical and defense industries.PTJ will strategize with you to provide the most cost-effective services to help you reach your target,Welcome to Contact us ( sales@pintejin.com ) directly for your new project.
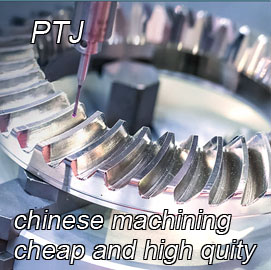
- 5 Axis Machining
- Cnc Milling
- Cnc Turning
- Machining Industries
- Machining Process
- Surface Treatment
- Metal Machining
- Plastic Machining
- Powder Metallurgy Mold
- Die Casting
- Parts Gallery
- Auto Metal Parts
- Machinery Parts
- LED Heatsink
- Building Parts
- Mobile Parts
- Medical Parts
- Electronic Parts
- Tailored Machining
- Bicycle Parts
- Aluminum Machining
- Titanium Machining
- Stainless Steel Machining
- Copper Machining
- Brass Machining
- Super Alloy Machining
- Peek Machining
- UHMW Machining
- Unilate Machining
- PA6 Machining
- PPS Machining
- Teflon Machining
- Inconel Machining
- Tool Steel Machining
- More Material