Cost-Effective Tolerance and Surface Finish Strategies in CNC Machining
Computer Numerical Control (CNC) machining is a versatile manufacturing process widely used across industries for its precision and efficiency in creating intricate parts and components from various materials. Key to the success of CNC machining are tolerance and surface finish considerations, which directly impact both the functionality and aesthetic appeal of the final product.
Tolerance refers to the permissible limit or variation in a physical dimension of a part. In CNC machining, achieving precise tolerances is crucial for ensuring parts fit together correctly and perform their intended functions reliably. Factors influencing tolerance include the machining process, material properties, tooling capabilities, and design specifications.
What Factors Affect CNC Machining Tolerances?
Several factors influence CNC machining tolerances, which are critical for ensuring parts meet design specifications and functional requirements. Understanding these factors helps manufacturers optimize their machining processes for accuracy and reliability:
-
Machine Capability: The precision and capabilities of the CNC machine itself play a significant role. Factors such as spindle runout, axis positioning accuracy, and thermal stability of the machine affect its ability to achieve tight tolerances.
-
Tooling Selection and Condition: The choice of cutting tools, tool geometry, and their sharpness directly impact dimensional accuracy. Worn or improperly selected tools can introduce variations in dimensions and surface finish.
-
Material Properties: Different materials behave differently during machining. Factors such as hardness, elasticity, thermal expansion, and machinability influence how well a material holds tight tolerances.
-
Cutting Parameters: Machining parameters such as cutting speed, feed rate, depth of cut, and coolant usage affect dimensional accuracy. Optimal parameter selection balances material removal rates with maintaining desired tolerances.
-
Fixturing and Workholding: Properly designed fixtures and clamping mechanisms are crucial for minimizing part movement and vibration during machining. Secure fixturing ensures consistent part positioning relative to the cutting tools.
-
Environmental Factors: Temperature variations, humidity levels, and ambient vibrations in the machining environment can affect machine stability and, consequently, tolerance control.
-
Design Considerations: The complexity and geometry of the part design influence achievable tolerances. Sharp corners, deep cavities, thin walls, and complex features may require special tooling or machining techniques to maintain accuracy.
-
Operator Skill and Experience: Operator proficiency in programming, setup, and monitoring the machining process plays a significant role. Skilled operators can identify issues early, adjust parameters effectively, and ensure consistent quality.
-
Quality Control and Inspection: Robust inspection procedures and measurement tools are essential for verifying part dimensions throughout the machining process. Regular checks help identify deviations promptly, enabling corrective actions.
-
Post-Processing and Finishing: Processes such as deburring, polishing, and surface treatments can influence final dimensions and surface quality. Careful planning of these steps ensures they enhance, rather than detract from, dimensional accuracy.
By addressing these factors systematically, manufacturers can optimize CNC machining processes to achieve tighter tolerances, reduce scrap and rework, and ultimately deliver high-quality parts that meet customer expectations.
What Are the Cost Implications of Tighter Tolerances in CNC Machining?
Tighter tolerances in CNC machining can significantly impact production costs due to several factors that increase complexity and operational requirements. Here are the main cost implications:
-
Increased Machining Time: Achieving tighter tolerances often requires slower cutting speeds, finer tool feeds, and more frequent tool changes to maintain precision. This extended machining time directly increases labor costs and machine utilization expenses.
-
Specialized Tooling and Equipment: To meet tighter tolerances, manufacturers may need to invest in higher precision tools, cutting inserts, and specialized measuring instruments. These tools are generally more expensive upfront and may require frequent calibration and maintenance, adding to operational costs.
-
Material Costs: Certain materials that offer superior dimensional stability and machinability required for tight tolerances can be more expensive. Additionally, stricter material handling and storage protocols may be necessary to prevent dimensional changes due to environmental factors.
-
Increased Scrap and Rework: Tighter tolerances leave less room for error. As a result, any deviations from specified dimensions during machining may lead to increased scrap rates or the need for costly rework to salvage parts that do not meet requirements.
-
Quality Control Expenses: Ensuring parts meet tight tolerances demands more rigorous inspection and quality control measures. This includes more frequent inspections using precision measurement tools, as well as the implementation of statistical process control (SPC) methods to monitor and adjust machining processes.
-
Design and Engineering Costs: Achieving tighter tolerances often necessitates more detailed design work and engineering analysis upfront. Design revisions and prototyping may be required to optimize part geometry and manufacturing processes, adding to development costs.
-
Operational Efficiency Impact: Striving for tighter tolerances can sometimes reduce overall production throughput. This could be due to increased setup times, more frequent machine adjustments, and the need for specialized operator training, all of which can affect efficiency and capacity utilization.
-
Supply Chain Considerations: Suppliers capable of consistently meeting tight tolerance requirements may charge higher prices for their expertise and reliability. Additionally, tighter tolerances may increase lead times as more careful planning and coordination with suppliers are necessary.
Despite these cost implications, tighter tolerances are often necessary to meet stringent quality standards, enhance product performance, and satisfy customer requirements in industries such as aerospace, automotive, and medical devices. Balancing these costs with the benefits of improved part quality and reliability is crucial for optimizing CNC machining operations effectively.
How Do Surface Finish Requirements Interact with Tolerance Specifications in CNC Machining?
Surface finish requirements and tolerance specifications in CNC machining are closely intertwined, as both aspects contribute to the overall quality and functionality of machined parts. Here’s how they interact:
-
Functional Relationship: Surface finish and tolerance specifications both influence the functional performance of a part. Tolerances define the permissible limits of dimensional variation, ensuring parts fit together correctly and perform their intended functions. Surface finish, on the other hand, affects properties such as friction, wear resistance, sealing ability, and aesthetic appearance. Balancing these requirements ensures that parts not only fit correctly but also perform optimally in their intended application.
-
Manufacturability Considerations: Achieving tighter tolerances can sometimes require adjustments to machining parameters that impact surface finish. For instance, reducing machining allowances to meet tighter tolerances might result in a rougher surface finish if not compensated properly. Conversely, achieving a superior surface finish might necessitate slower machining speeds or additional finishing operations, affecting dimensional accuracy.
-
Process Optimization: Effective management of both tolerance and surface finish specifications involves optimizing machining processes. This includes selecting appropriate cutting tools, adjusting cutting parameters, and implementing suitable finishing techniques to achieve desired outcomes without compromising either dimensional accuracy or surface quality.
-
Material Influence: Different materials respond differently to machining processes, affecting both tolerance control and surface finish. Some materials may require specific cutting speeds, feeds, or tooling geometries to achieve both tight tolerances and smooth surface finishes. Understanding material properties and their machinability is crucial for balancing these requirements effectively.
-
Quality Control Integration: Inspection and quality control processes play a vital role in ensuring that both tolerance and surface finish requirements are met consistently. Dimensional measurements verify tolerance adherence, while surface roughness measurements assess the quality of surface finishes. Integrated quality control protocols help identify deviations early and enable corrective actions to maintain part integrity.
-
Customer Requirements: Often, customer specifications or industry standards dictate both tolerance limits and surface finish requirements. Manufacturers must align their machining capabilities to these requirements while optimizing processes to achieve cost-effective production without compromising quality.
Achieving the right balance between tolerance specifications and surface finish requirements in CNC machining involves careful planning, process optimization, and robust quality control. Manufacturers must consider the functional needs of the part, material characteristics, and customer expectations to deliver parts that meet both dimensional accuracy and surface quality standards effectively.
Conclusion
In conclusion, effective management of tolerances and surface finishes in CNC machining is essential for achieving high-quality, cost-effective production outcomes. By adopting proactive design strategies, leveraging advanced machining techniques, and implementing rigorous quality control measures, manufacturers can optimize their CNC machining processes to meet both technical requirements and budgetary constraints.
Reprint Statement: If there are no special instructions, all articles on this site are original. Please indicate the source for reprinting:https://www.cncmachiningptj.com/,thanks!
3, 4 and 5-axis precision CNC machining services for aluminum machining, beryllium, carbon steel, magnesium, titanium machining, Inconel, platinum, superalloy, acetal, polycarbonate, fiberglass, graphite and wood. Capable of machining parts up to 98 in. turning dia. and +/-0.001 in. straightness tolerance. Processes include milling, turning, drilling, boring, threading, tapping, forming, knurling, counterboring, countersinking, reaming and laser cutting. Secondary services such as assembly, centerless grinding, heat treating, plating and welding. Prototype and low to high volume production offered with maximum 50,000 units. Suitable for fluid power, pneumatics, hydraulics and valve applications. Serves the aerospace, aircraft, military, medical and defense industries.PTJ will strategize with you to provide the most cost-effective services to help you reach your target,Welcome to Contact us ( sales@pintejin.com ) directly for your new project.
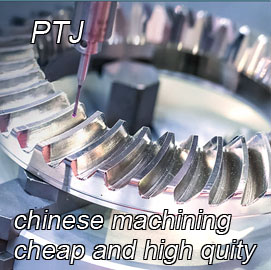
- 5 Axis Machining
- Cnc Milling
- Cnc Turning
- Machining Industries
- Machining Process
- Surface Treatment
- Metal Machining
- Plastic Machining
- Powder Metallurgy Mold
- Die Casting
- Parts Gallery
- Auto Metal Parts
- Machinery Parts
- LED Heatsink
- Building Parts
- Mobile Parts
- Medical Parts
- Electronic Parts
- Tailored Machining
- Bicycle Parts
- Aluminum Machining
- Titanium Machining
- Stainless Steel Machining
- Copper Machining
- Brass Machining
- Super Alloy Machining
- Peek Machining
- UHMW Machining
- Unilate Machining
- PA6 Machining
- PPS Machining
- Teflon Machining
- Inconel Machining
- Tool Steel Machining
- More Material