How Hot Dip Galvanizing Protects Steel?
Hot dip galvanizing is a widely used process for protecting steel from corrosion. It involves the coating of steel with a layer of zinc by immersing the metal in a bath of molten zinc. This method has been utilized for over a century due to its effectiveness, durability, and cost-efficiency. This article provides an extensive overview of the hot dip galvanizing process, its benefits, applications, and the science behind how it protects steel from corrosion.
History of Galvanizing
Early Developments
The concept of galvanizing dates back to the 18th century. Luigi Galvani's experiments with animal tissues and electrical currents in the late 1700s led to the term "galvanizing." However, the modern method of hot dip galvanizing was developed much later.
Industrial Revolution and Beyond
During the Industrial Revolution, the need for corrosion-resistant materials became critical. The first patent for a method of coating iron with zinc was issued to Stanislas Sorel in France in 1837. This process laid the foundation for modern galvanizing techniques. Over the years, improvements in technology and the understanding of metallurgy have refined the process, making it more efficient and effective.
The Hot Dip Galvanizing Process
Pre-treatment
The pre-treatment phase is crucial for ensuring the quality of the galvanized coating. It typically involves several steps:
-
Cleaning: The steel surface must be thoroughly cleaned to remove all impurities, such as dirt, oil, and mill scale. This is usually done through a combination of degreasing, pickling, and rinsing.
-
Pickling: In this step, the steel is immersed in a solution of hydrochloric or sulfuric acid to remove rust and scale. This step is essential for creating a clean surface that allows for proper zinc adhesion.
-
Fluxing: After pickling, the steel is dipped in a flux solution (typically a mixture of zinc chloride and ammonium chloride) to prevent oxidation before galvanizing. This ensures that the steel surface remains clean and ready for the zinc coating.
Galvanizing
Once the steel has been properly cleaned and fluxed, it is immersed in a bath of molten zinc at temperatures around 450°C (842°F). The steel is left in the bath until it reaches the same temperature as the molten zinc, allowing for the formation of a metallurgical bond between the zinc and the steel.
Cooling and Inspection
After the steel is removed from the zinc bath, it is cooled, usually in a quench tank. The cooling process solidifies the zinc coating. The galvanized steel is then inspected for quality, ensuring that the coating is uniform and free of defects.
Mechanisms of Corrosion Protection
Barrier Protection
The zinc coating acts as a physical barrier that prevents corrosive substances from reaching the steel surface. This barrier protection is effective in preventing rust and corrosion as long as the zinc coating remains intact.
Cathodic Protection
One of the unique properties of zinc is its ability to provide cathodic protection. Zinc is more electronegative than steel, meaning it will corrode in preference to the steel. When the zinc coating is damaged, exposing the underlying steel, the zinc will continue to protect the steel by corroding itself. This sacrificial action prevents the steel from rusting.
Formation of Protective Layers
When exposed to the atmosphere, the zinc coating reacts with oxygen and moisture to form zinc oxide, which further reacts with carbon dioxide to form zinc carbonate. This layer of zinc carbonate is relatively insoluble and adheres well to the zinc coating, providing an additional layer of protection against corrosion.
Benefits of Hot Dip Galvanizing
Long-Lasting Protection
Hot dip galvanizing provides long-lasting protection for steel structures. The life expectancy of galvanized steel can exceed 50 years in rural environments and 20 to 25 years in severe urban and coastal environments.
Cost-Effectiveness
Although the initial cost of galvanizing can be higher than other coating methods, the long-term savings in maintenance and replacement costs make it highly cost-effective. The minimal maintenance requirements further enhance its economic advantages.
Complete Coverage
The galvanizing process ensures complete coverage of the steel, including edges, corners, and intricate details that are often difficult to protect with other coating methods. This comprehensive coverage is essential for ensuring the longevity and durability of the steel.
Environmental Benefits
Galvanized steel is highly recyclable, and the galvanizing process itself has minimal environmental impact. The zinc used in the process can be reclaimed and reused, making it an environmentally friendly option.
Robustness and Durability
The metallurgical bond formed between the zinc and steel during the galvanizing process creates a coating that is tightly adhered to the steel. This bond enhances the durability of the coating, making it resistant to mechanical damage during handling, transport, and installation.
Applications of Hot Dip Galvanizing
Construction
Galvanized steel is extensively used in the construction industry for structural elements such as beams, columns, and reinforcing bars. Its corrosion resistance ensures the longevity and safety of buildings and infrastructure.
Automotive Industry
In the automotive industry, galvanized steel is used for body panels, frames, and other components. The corrosion resistance provided by galvanizing helps extend the life of vehicles and reduces maintenance costs.
Agriculture
Agricultural equipment and structures, such as fencing, silos, and irrigation systems, benefit from hot dip galvanizing. The harsh conditions in agricultural environments make corrosion protection essential for maintaining functionality and reducing maintenance.
Utilities and Energy
Galvanized steel is used in the utilities and energy sectors for transmission towers, poles, and substations. The durability and low maintenance requirements of galvanized steel make it ideal for these applications.
Marine and Coastal Environments
In marine and coastal environments, where exposure to saltwater and humidity accelerates corrosion, hot dip galvanizing provides essential protection for structures such as piers, docks, and offshore platforms.
Standards and Specifications
Various standards and specifications govern the hot dip galvanizing process to ensure consistency and quality. Some of the key standards include:
- ASTM A123: Standard Specification for Zinc (Hot-Dip Galvanized) Coatings on Iron and Steel Products
- ASTM A153: Standard Specification for Zinc Coating (Hot-Dip) on Iron and Steel Hardware
- ISO 1461: Hot Dip Galvanized Coatings on Fabricated Iron and Steel Articles - Specifications and Test Methods
- BS EN ISO 14713: Protection against Corrosion of Iron and Steel in Structures - Zinc and Aluminium Coatings
Challenges and Limitations
Coating Thickness and Uniformity
Achieving a uniform coating thickness can be challenging, particularly for complex shapes and hollow sections. Variations in coating thickness can affect the overall corrosion resistance and mechanical properties of the galvanized steel.
Hydrogen Embrittlement
High-strength steels can be susceptible to hydrogen embrittlement during the galvanizing process. This phenomenon occurs when hydrogen atoms diffuse into the steel, leading to brittle fracture. Proper process control and pre-treatment can mitigate this risk.
Aesthetic Considerations
While the appearance of galvanized steel is generally acceptable for most industrial applications, it may not meet aesthetic requirements for certain architectural applications. Additional coatings or treatments may be required to achieve the desired finish.
Temperature Sensitivity
The hot dip galvanizing process involves high temperatures, which can affect the mechanical properties of certain types of steel. This is particularly relevant for high-strength, low-alloy steels, where the heat can alter the material's microstructure.
Advances and Innovations
Duplex Systems
Duplex systems combine hot dip galvanizing with additional coating layers, such as paint or powder coatings. This approach enhances corrosion resistance and provides aesthetic benefits. The synergistic effect of the two coatings results in longer service life and reduced maintenance.
Automated Galvanizing Plants
Advancements in automation and robotics have improved the efficiency and consistency of the hot dip galvanizing process. Automated systems ensure precise control of coating thickness and uniformity, reducing the risk of defects.
Nano-Technology
Research into nano-technology has led to the development of advanced coatings that can be applied in conjunction with hot dip galvanizing. These coatings offer enhanced corrosion resistance and additional functionalities, such as self-healing properties and improved adhesion.
Environmental Innovations
Ongoing research and development efforts are focused on making the hot dip galvanizing process more environmentally friendly. Innovations include the use of more sustainable fluxing agents, improvements in zinc recovery and recycling, and the reduction of energy consumption.
Conclusion
Hot dip galvanizing remains one of the most effective methods for protecting steel from corrosion. Its combination of barrier protection, cathodic protection, and the formation of protective layers ensures long-lasting durability and minimal maintenance. Despite certain challenges and limitations, ongoing advancements and innovations continue to enhance the process and expand its applications. From construction and automotive industries to agriculture and marine environments, hot dip galvanizing plays a critical role in ensuring the longevity and sustainability of steel structures worldwide.
Reprint Statement: If there are no special instructions, all articles on this site are original. Please indicate the source for reprinting:https://www.cncmachiningptj.com/,thanks!
3, 4 and 5-axis precision CNC machining services for aluminum machining, beryllium, carbon steel, magnesium, titanium machining, Inconel, platinum, superalloy, acetal, polycarbonate, fiberglass, graphite and wood. Capable of machining parts up to 98 in. turning dia. and +/-0.001 in. straightness tolerance. Processes include milling, turning, drilling, boring, threading, tapping, forming, knurling, counterboring, countersinking, reaming and laser cutting. Secondary services such as assembly, centerless grinding, heat treating, plating and welding. Prototype and low to high volume production offered with maximum 50,000 units. Suitable for fluid power, pneumatics, hydraulics and valve applications. Serves the aerospace, aircraft, military, medical and defense industries.PTJ will strategize with you to provide the most cost-effective services to help you reach your target,Welcome to Contact us ( sales@pintejin.com ) directly for your new project.
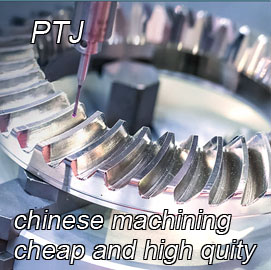
- 5 Axis Machining
- Cnc Milling
- Cnc Turning
- Machining Industries
- Machining Process
- Surface Treatment
- Metal Machining
- Plastic Machining
- Powder Metallurgy Mold
- Die Casting
- Parts Gallery
- Auto Metal Parts
- Machinery Parts
- LED Heatsink
- Building Parts
- Mobile Parts
- Medical Parts
- Electronic Parts
- Tailored Machining
- Bicycle Parts
- Aluminum Machining
- Titanium Machining
- Stainless Steel Machining
- Copper Machining
- Brass Machining
- Super Alloy Machining
- Peek Machining
- UHMW Machining
- Unilate Machining
- PA6 Machining
- PPS Machining
- Teflon Machining
- Inconel Machining
- Tool Steel Machining
- More Material