Choosing Steel for Your CNC Machining Project
CNC (Computer Numerical Control) machining has revolutionized manufacturing processes by providing precise, repeatable, and efficient means of shaping materials into intricate components. Among the various materials used in CNC machining, steel stands out due to its exceptional mechanical properties, versatility, and widespread availability. Choosing the right type of steel for a CNC machining project is critical to ensuring optimal performance, durability, and cost-effectiveness. This article explores the different types of steel commonly used in CNC machining, their properties, and the factors to consider when selecting the perfect match for a specific application.
Properties of Steel
Composition and Microstructure
Steel is an alloy primarily composed of iron and carbon, with the carbon content typically ranging from 0.02% to 2.1% by weight. The addition of carbon significantly enhances the strength and hardness of iron. Other elements such as manganese, chromium, nickel, and molybdenum are often added to steel to impart specific properties such as improved corrosion resistance, toughness, and machinability. The microstructure of steel, which includes phases such as ferrite, austenite, martensite, and pearlite, plays a crucial role in determining its mechanical properties.
Mechanical Properties
The mechanical properties of steel are influenced by its composition, heat treatment, and processing history. Key mechanical properties to consider in CNC machining include:
- Hardness: Resistance to deformation and scratching.
- Tensile Strength: The maximum stress that steel can withstand while being stretched or pulled before breaking.
- Yield Strength: The stress at which steel begins to deform plastically.
- Ductility: The ability to deform without breaking.
- Toughness: The ability to absorb energy and resist fracture.
- Machinability: The ease with which steel can be cut, shaped, or finished.
Types of Steel for CNC Machining
Carbon Steel
Carbon steel, with its simple composition primarily of iron and carbon, is widely used in CNC machining due to its cost-effectiveness and mechanical properties. It is classified into three main categories based on its carbon content:
Low Carbon Steel (Mild Steel)
- Carbon Content: Less than 0.3%
- Properties: Good ductility and toughness, easy to machine and weld, relatively low strength.
- Applications: Automotive parts, structural components, machinery.
Medium Carbon Steel
- Carbon Content: 0.3% to 0.6%
- Properties: Balanced strength and ductility, can be heat-treated to improve hardness and strength.
- Applications: Gears, axles, shafts, forging.
High Carbon Steel
- Carbon Content: 0.6% to 1.4%
- Properties: High hardness and strength, less ductile, more difficult to machine.
- Applications: Cutting tools, springs, high-strength wires.
Alloy Steel
Alloy steels contain additional alloying elements such as chromium, nickel, and molybdenum to enhance specific properties like strength, toughness, and corrosion resistance. Common types of alloy steel include:
Low Alloy Steel
- Properties: Improved strength and toughness, good wear resistance, can be heat-treated.
- Applications: Automotive parts, pipelines, pressure vessels.
High Alloy Steel
- Properties: High strength, excellent corrosion resistance, superior heat resistance.
- Applications: Aerospace components, power generation equipment, chemical processing plants.
Stainless Steel
Stainless steel is renowned for its corrosion resistance, which is primarily due to the presence of chromium (at least 10.5% by weight). It is categorized into several types based on its microstructure:
Austenitic Stainless Steel
- Properties: Excellent corrosion resistance, good ductility and toughness, non-magnetic.
- Applications: Food processing equipment, medical devices, marine environments.
Ferritic Stainless Steel
- Properties: Good corrosion resistance, magnetic, lower toughness than austenitic.
- Applications: Automotive exhaust systems, industrial equipment, architectural applications.
Martensitic Stainless Steel
- Properties: High hardness and strength, moderate corrosion resistance, magnetic.
- Applications: Cutlery, surgical instruments, turbine blades.
Duplex Stainless Steel
- Properties: Combines austenitic and ferritic properties, high strength, excellent corrosion resistance.
- Applications: Chemical processing, oil and gas industry, desalination plants.
Tool Steel
Tool steel is designed for use in cutting and shaping tools due to its high hardness, abrasion resistance, and ability to maintain a sharp cutting edge. Common types of tool steel cnc machining material include:
Water-Hardening Tool Steel (W-Series)
- Properties: High hardness, low cost, quenched in water.
- Applications: Hand tools, drills, reamers.
Cold-Work Tool Steel (O-Series, A-Series, D-Series)
- Properties: Good wear resistance, retains hardness at lower temperatures.
- Applications: Dies, punches, shears.
Hot-Work Tool Steel (H-Series)
- Properties: Retains hardness and strength at high temperatures, good thermal fatigue resistance.
- Applications: Forging dies, extrusion tools, hot shears.
High-Speed Tool Steel (M-Series, T-Series)
- Properties: Exceptional hardness and wear resistance, retains hardness at high temperatures.
- Applications: Cutting tools, drill bits, end mills.
Factors to Consider in Steel Selection for CNC Machining
Mechanical Requirements
The mechanical requirements of the final component are paramount when choosing the appropriate steel. Considerations include:
- Load-Bearing Capacity: Ensure the steel can withstand the expected loads and stresses.
- Wear Resistance: Select steel with adequate hardness and abrasion resistance for high-wear applications.
- Impact Resistance: Choose steel with sufficient toughness for components subjected to shock or impact loads.
- Fatigue Resistance: Consider steels with good fatigue resistance for cyclic loading conditions.
Machinability
Machinability refers to the ease with which steel can be cut, shaped, and finished using CNC machining. Factors influencing machinability include:
- Hardness: Generally, harder steels are more challenging to machine.
- Tool Wear: Steels that cause rapid tool wear can increase machining costs.
- Surface Finish: The ability to achieve the desired surface finish without excessive tool marks or roughness.
- Chipping and Burr Formation: Some steels are prone to chipping or forming burrs, affecting the quality of the machined part.
Heat Treatment
Heat treatment processes such as annealing, quenching, and tempering can significantly alter the properties of steel. Considerations include:
- Hardness and Strength: Heat treatment can enhance these properties for better performance.
- Dimensional Stability: Ensure the steel maintains its dimensions after heat treatment.
- Machinability Post-Treatment: Some steels become more challenging to machine after heat treatment.
Corrosion Resistance
For applications exposed to corrosive environments, selecting steel with adequate corrosion resistance is essential. Stainless steels, with their chromium content, are often preferred for such applications. Other factors to consider include:
- Environmental Conditions: Exposure to moisture, chemicals, and temperature variations.
- Surface Treatments: Coatings and surface treatments can enhance corrosion resistance.
Cost
The cost of steel and its machining can significantly impact the overall project budget. Factors influencing cost include:
- Material Cost: The base price of the steel alloy.
- Machining Cost: Costs associated with tooling, machine time, and labor.
- Heat Treatment and Surface Finishing Costs: Additional processes required to achieve the desired properties.
Availability
The availability of specific steel grades and forms can influence the selection process. Considerations include:
- Lead Times: Time required to procure the material.
- Form Availability: Availability of steel in required forms such as bars, sheets, or billets.
- Supplier Reliability: Consistent quality and timely delivery from suppliers.
Common Steel Grades for CNC Machining
1018 Carbon Steel
- Composition: Low carbon steel with good balance of strength, ductility, and weldability.
- Properties: Easy to machine, can be case-hardened.
- Applications: Shafts, pins, machinery parts.
1045 Carbon Steel
- Composition: Medium carbon steel with higher strength and hardness than 1018.
- Properties: Good machinability, can be heat-treated.
- Applications: Gears, axles, bolts.
4140 Alloy Steel
- Composition: Chromium-molybdenum alloy steel with excellent strength and toughness.
- Properties: Can be heat-treated to enhance properties, good machinability.
- Applications: Tooling, automotive parts, aerospace components.
4340 Alloy Steel
- Composition: Nickel-chromium-molybdenum alloy steel with high strength and toughness.
- Properties: Excellent impact resistance, can be heat-treated.
- Applications: Heavy-duty shafts, gears, structural components.
303 Stainless Steel
- Composition: Austenitic stainless steel with sulfur for improved machinability.
- Properties: Good corrosion resistance, excellent machinability.
- Applications: Fasteners, fittings, bushings.
304 Stainless Steel
- Composition: Austenitic stainless steel with excellent corrosion resistance.
- Properties: Good machinability, widely used in various industries.
- Applications: Food processing equipment, chemical containers, architectural components.
316 Stainless Steel
- Composition: Austenitic stainless steel with molybdenum for enhanced corrosion resistance.
- Properties: Superior corrosion resistance, good machinability.
- Applications: Marine applications, chemical processing, medical devices.
D2 Tool Steel
- Composition: High-carbon, high-chromium tool steel with excellent wear resistance.
- Properties: High hardness, good dimensional stability.
- Applications: Dies, punches, cutting tools.
H13 Tool Steel
- Composition: Chromium hot-work tool steel with excellent high-temperature strength.
- Properties: Retains hardness at elevated temperatures, good toughness.
- Applications: Forging dies, extrusion tools, hot shears.
Case Studies: Steel Selection for Specific Applications
Automotive Industry
The automotive industry requires materials that can withstand high stresses, wear, and corrosive environments. Steel grades such as 4140 and 4340 are commonly used for components like gears, shafts, and axles due to their excellent strength and toughness. Stainless steels like 304 and 316 are used for exhaust systems and other parts exposed to corrosive conditions.
Aerospace Industry
Aerospace components demand materials with high strength-to-weight ratios, excellent fatigue resistance, and the ability to perform under extreme conditions. 4340 alloy steel is often used for landing gear and structural components due to its superior strength and toughness. Stainless steels like 17-4 PH and 15-5 PH are used for parts requiring high corrosion resistance and strength.
Medical Devices
Medical devices require materials with high corrosion resistance, biocompatibility, and good machinability. Austenitic stainless steels such as 304 and 316 are widely used for surgical instruments, implants, and medical equipment. Tool steels like 420 and 440C are used for cutting tools due to their high hardness and wear resistance.
Oil and Gas Industry
The oil and gas industry demands materials that can withstand harsh environments, high pressures, and corrosive conditions. Duplex stainless steels like 2205 and 2507 are commonly used for pipelines, valves, and offshore equipment due to their excellent corrosion resistance and high strength. Alloy steels like 4140 and 4340 are used for downhole tools and drilling equipment.
Conclusion
Choosing the right type of steel for a CNC machining project involves a comprehensive understanding of the material's properties, the application's requirements, and the machining process. By carefully considering factors such as mechanical requirements, machinability, heat treatment, corrosion resistance, cost, and availability, engineers and manufacturers can select the perfect steel grade that ensures optimal performance, durability, and cost-effectiveness. As technology and materials science continue to advance, the range of available steel alloys will expand, providing even more options for achieving the perfect match for any CNC machining project.
Reprint Statement: If there are no special instructions, all articles on this site are original. Please indicate the source for reprinting:https://www.cncmachiningptj.com/,thanks!
3, 4 and 5-axis precision CNC machining services for aluminum machining, beryllium, carbon steel, magnesium, titanium machining, Inconel, platinum, superalloy, acetal, polycarbonate, fiberglass, graphite and wood. Capable of machining parts up to 98 in. turning dia. and +/-0.001 in. straightness tolerance. Processes include milling, turning, drilling, boring, threading, tapping, forming, knurling, counterboring, countersinking, reaming and laser cutting. Secondary services such as assembly, centerless grinding, heat treating, plating and welding. Prototype and low to high volume production offered with maximum 50,000 units. Suitable for fluid power, pneumatics, hydraulics and valve applications. Serves the aerospace, aircraft, military, medical and defense industries.PTJ will strategize with you to provide the most cost-effective services to help you reach your target,Welcome to Contact us ( sales@pintejin.com ) directly for your new project.
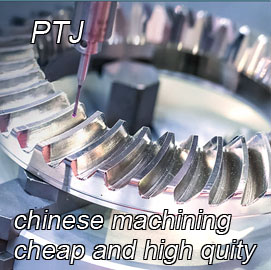
- 5 Axis Machining
- Cnc Milling
- Cnc Turning
- Machining Industries
- Machining Process
- Surface Treatment
- Metal Machining
- Plastic Machining
- Powder Metallurgy Mold
- Die Casting
- Parts Gallery
- Auto Metal Parts
- Machinery Parts
- LED Heatsink
- Building Parts
- Mobile Parts
- Medical Parts
- Electronic Parts
- Tailored Machining
- Bicycle Parts
- Aluminum Machining
- Titanium Machining
- Stainless Steel Machining
- Copper Machining
- Brass Machining
- Super Alloy Machining
- Peek Machining
- UHMW Machining
- Unilate Machining
- PA6 Machining
- PPS Machining
- Teflon Machining
- Inconel Machining
- Tool Steel Machining
- More Material