CNC Machining ABS Plastic 101:A Beginner’s guide
Acrylonitrile Butadiene Styrene (ABS) is a common thermoplastic polymer renowned for its toughness, impact resistance, and ease of machining. ABS is extensively used in the manufacturing industry, especially in applications requiring robust mechanical properties and moderate heat resistance. CNC (Computer Numerical Control) machining is a preferred method for shaping and forming ABS plastic into desired components due to its precision, repeatability, and versatility. This article delves into the considerations, common issues, and troubleshooting techniques associated with CNC machining of ABS plastic.
Characteristics of ABS Plastic
Mechanical Properties
ABS plastic combines three distinct monomers: acrylonitrile, butadiene, and styrene. Each contributes to the material's overall characteristics:
- Acrylonitrile: Enhances chemical resistance and thermal stability.
- Butadiene: Provides toughness and impact resistance.
- Styrene: Offers rigidity and ease of processing.
Physical Properties
ABS has several key physical properties:
- Density: Approximately 1.04 g/cm³.
- Glass Transition Temperature: Around 105°C.
- Thermal Conductivity: 0.17 W/(m·K).
Advantages
- Impact Resistance: High toughness makes ABS suitable for applications subjected to physical stress.
- Machinability: ABS is easy to cut, drill, and machine.
- Surface Finish: Offers good surface finish quality post-machining.
- Adhesion: Can be easily bonded using adhesives.
- Recyclability: ABS is recyclable, contributing to environmental sustainability.
Disadvantages
- Heat Sensitivity: Prone to deformation under high temperatures.
- Chemical Sensitivity: Can be affected by certain solvents.
- UV Sensitivity: Susceptible to degradation when exposed to UV radiation over extended periods.
CNC Machining Considerations
Tool Selection
Choosing the appropriate tools for ABS CNC machining is crucial. The following are important considerations:
- Tool Material: Carbide tools are preferred due to their hardness and wear resistance.
- Tool Geometry: Sharp tools with positive rake angles reduce cutting forces and minimize heat generation.
- Coatings: Tools with coatings such as TiN (Titanium Nitride) can extend tool life and improve performance.
Machining Parameters
Optimizing machining parameters is essential to achieve the desired finish and dimensional accuracy. Key parameters include:
- Spindle Speed: Typically ranges between 1,000 to 5,000 RPM, depending on the tool size and material thickness.
- Feed Rate: Should be adjusted to balance between speed and surface finish, often ranging from 0.1 to 0.5 mm/revolution.
- Depth of Cut: Light cuts (0.5 to 2 mm) are recommended to prevent excessive heat buildup and material deformation.
- Coolant: Using a suitable coolant can help manage heat and improve surface finish.
Workholding
Effective workholding is essential for precision machining. Considerations include:
- Fixtures: Custom fixtures may be necessary to secure irregularly shaped ABS parts.
- Vacuum Tables: Useful for holding flat and thin parts securely.
- Clamping Force: Must be balanced to avoid deformation of the material.
Environment
The machining environment plays a role in the quality of the final product:
- Temperature Control: Maintaining a stable temperature prevents thermal expansion and contraction.
- Cleanliness: Removing chips and debris prevents re-machining and surface scratches.
Common Issues in CNC Machining ABS Plastic
Material Deformation
ABS can deform due to excessive heat generated during machining. This is often caused by:
- High Spindle Speeds: Generating too much frictional heat.
- Large Depth of Cut: Increasing the load on the tool and the material.
- Insufficient Coolant: Leading to inadequate heat dissipation.
Poor Surface Finish
Surface finish quality can be affected by:
- Tool Wear: Dull tools cause rough surfaces.
- Incorrect Feed Rates: Too high or too low feed rates can lead to poor finish.
- Vibration: Insufficient rigidity in the setup can cause chatter marks.
Dimensional Inaccuracy
Factors leading to dimensional inaccuracy include:
- Tool Deflection: High cutting forces can cause tool bending.
- Thermal Expansion: Heat buildup can expand the material during machining.
- Inconsistent Workholding: Improperly secured parts can shift during machining.
Tool Wear
ABS can cause rapid tool wear due to its abrasive fillers. This is exacerbated by:
- High Cutting Speeds: Increasing tool wear rate.
- Inadequate Cooling: Leading to higher tool temperatures and wear.
Chip Management
ABS produces long, stringy chips that can:
- Clog Tool Paths: Leading to re-machining and surface damage.
- Accumulate: Creating fire hazards or interfering with machine operation.
Troubleshooting Techniques
Managing Heat
- Optimize Cutting Parameters: Adjust spindle speed, feed rate, and depth of cut to reduce heat generation.
- Use Coolant: Employ coolant or mist to dissipate heat effectively.
- Sharp Tools: Ensure tools are sharp to minimize friction and heat.
Enhancing Surface Finish
- Tool Maintenance: Regularly inspect and replace worn tools.
- Appropriate Feed Rates: Adjust feed rates to balance between speed and surface finish quality.
- Vibration Control: Improve machine rigidity and use dampening techniques.
Improving Dimensional Accuracy
- Toolpath Optimization: Use CAM software to optimize tool paths and minimize tool deflection.
- Thermal Management: Maintain a stable machining environment and use coolants.
- Secure Workholding: Ensure parts are firmly and accurately held during machining.
Extending Tool Life
- Proper Tool Selection: Use carbide tools with appropriate coatings.
- Controlled Cutting Conditions: Maintain moderate cutting speeds and feed rates.
- Regular Maintenance: Schedule regular tool inspections and replacements.
Effective Chip Management
- Chip Breakers: Use tools with chip breakers to manage chip size.
- High-Pressure Coolant: Utilize high-pressure coolant to clear chips from the cutting area.
- Vacuum Systems: Employ vacuum systems to remove chips from the workspace.
Case Studies
Case Study 1: Optimizing Spindle Speed and Feed Rate
A manufacturing company experienced material deformation and poor surface finish when machining ABS parts. By conducting a series of tests, they optimized the spindle speed to 3,500 RPM and the feed rate to 0.3 mm/revolution. This adjustment reduced heat generation and improved surface finish quality significantly.
Case Study 2: Implementing Effective Workholding Solutions
An aerospace component manufacturer faced issues with dimensional accuracy due to part movement during machining. They designed custom fixtures tailored to their part geometry, ensuring secure and stable workholding. This solution enhanced dimensional accuracy and reduced rework.
Case Study 3: Enhancing Tool Life with Coated Tools
A precision engineering firm observed rapid tool wear while machining ABS. Switching to carbide tools with TiN coating extended tool life by 50%, reduced tool replacement frequency, and maintained consistent surface finish quality.
Conclusion
CNC machining of ABS plastic offers numerous advantages, including high precision and repeatability. However, it presents unique challenges such as heat sensitivity, chip management, and tool wear. By understanding the material properties, selecting appropriate tools, optimizing machining parameters, and employing effective workholding and cooling strategies, manufacturers can mitigate these issues and achieve high-quality machined ABS parts. Continuous improvement and adaptation of best practices are essential for optimizing the CNC machining process for ABS plastic.
Reprint Statement: If there are no special instructions, all articles on this site are original. Please indicate the source for reprinting:https://www.cncmachiningptj.com/,thanks!
3, 4 and 5-axis precision CNC machining services for aluminum machining, beryllium, carbon steel, magnesium, titanium machining, Inconel, platinum, superalloy, acetal, polycarbonate, fiberglass, graphite and wood. Capable of machining parts up to 98 in. turning dia. and +/-0.001 in. straightness tolerance. Processes include milling, turning, drilling, boring, threading, tapping, forming, knurling, counterboring, countersinking, reaming and laser cutting. Secondary services such as assembly, centerless grinding, heat treating, plating and welding. Prototype and low to high volume production offered with maximum 50,000 units. Suitable for fluid power, pneumatics, hydraulics and valve applications. Serves the aerospace, aircraft, military, medical and defense industries.PTJ will strategize with you to provide the most cost-effective services to help you reach your target,Welcome to Contact us ( sales@pintejin.com ) directly for your new project.
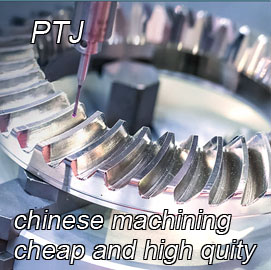
- 5 Axis Machining
- Cnc Milling
- Cnc Turning
- Machining Industries
- Machining Process
- Surface Treatment
- Metal Machining
- Plastic Machining
- Powder Metallurgy Mold
- Die Casting
- Parts Gallery
- Auto Metal Parts
- Machinery Parts
- LED Heatsink
- Building Parts
- Mobile Parts
- Medical Parts
- Electronic Parts
- Tailored Machining
- Bicycle Parts
- Aluminum Machining
- Titanium Machining
- Stainless Steel Machining
- Copper Machining
- Brass Machining
- Super Alloy Machining
- Peek Machining
- UHMW Machining
- Unilate Machining
- PA6 Machining
- PPS Machining
- Teflon Machining
- Inconel Machining
- Tool Steel Machining
- More Material