Exploring the Diversity of Aluminum Grades in Rapid Prototyping: A Comprehensive Guide
Rapid prototyping has revolutionized the product development process, enabling designers and engineers to quickly iterate and refine their designs before moving into full-scale production. Among the myriad of materials available for rapid prototyping, aluminum stands out as a versatile and widely-used option due to its excellent properties such as strength, lightweight, and machinability. However, not all aluminum grades are created equal. In this article, we will delve into the diverse range of aluminum grades utilized in rapid prototyping, exploring their unique characteristics, applications, and advantages.
1. Aluminum Alloys: An Overview
Aluminum alloys are composed primarily of aluminum, with other elements such as copper, zinc, magnesium, and silicon added to enhance specific properties. These alloys are classified based on their chemical composition, with each grade offering distinct advantages for various applications. In rapid prototyping, the choice of aluminum alloy plays a crucial role in determining the performance, cost-effectiveness, and suitability of the final prototype.
2. Common Aluminum Grades in Rapid Prototyping
2.1 6061 Aluminum Alloy
6061 aluminum alloy is one of the most widely used grades in rapid prototyping due to its excellent machinability, weldability, and corrosion resistance. It offers good strength-to-weight ratio, making it ideal for applications requiring structural integrity and durability. Commonly used in aerospace components, automotive parts, and consumer electronics, 6061 aluminum alloy provides versatility and reliability in rapid prototyping projects.
2.2 7075 Aluminum Alloy
Known for its high strength and toughness, 7075 aluminum alloy is favored in rapid prototyping for applications requiring superior performance under extreme conditions. With zinc as its primary alloying element, 7075 offers excellent strength-to-weight ratio, making it suitable for aerospace, defense, and automotive industries. Its exceptional machinability allows for intricate designs and precise prototyping.
2.3 2024 Aluminum Alloy
2024 aluminum alloy is prized for its high strength and fatigue resistance, making it a preferred choice for structural components and aerospace applications. With copper as its primary alloying element, 2024 offers outstanding machinability and dimensional stability, making it well-suited for rapid prototyping projects where precision and reliability are paramount.
2.4 5083 Aluminum Alloy
5083 aluminum alloy is renowned for its exceptional corrosion resistance and weldability, making it suitable for marine and underwater applications. With magnesium as its primary alloying element, 5083 offers good strength and formability, allowing for the creation of complex prototypes with intricate geometries. Its resistance to seawater corrosion makes it an ideal choice for rapid prototyping in naval architecture and offshore industries.
2.5 6063 Aluminum Alloy
6063 aluminum alloy is valued for its excellent extrudability and formability, making it a popular choice for prototyping extruded profiles and shapes. With silicon as its primary alloying element, 6063 offers good surface finish and aesthetics, making it suitable for architectural, automotive, and consumer product applications. Its versatility and ease of fabrication make it a preferred option for rapid prototyping projects requiring complex geometries and precise dimensions.
3. Factors to Consider in Aluminum Grade Selection
When selecting an aluminum grade for rapid prototyping, several factors must be taken into consideration to ensure optimal performance and cost-effectiveness:
- Mechanical properties: Evaluate the strength, hardness, and toughness of the aluminum alloy to meet the specific requirements of the prototype.
- Machinability: Consider the ease of machining and fabrication, as well as the complexity of the design.
- Corrosion resistance: Assess the environmental conditions and exposure to corrosive elements to choose an aluminum grade with adequate corrosion resistance.
- Cost-effectiveness: Balance the performance requirements with the cost of materials and prototyping processes to achieve the desired balance between quality and affordability.
- Industry regulations: Ensure compliance with industry standards and regulations governing the use of aluminum alloys in specific applications, such as aerospace, automotive, and medical devices.
4. Advanced Aluminum Alloys for Rapid Prototyping
In addition to the common aluminum grades mentioned above, rapid prototyping process also leverages advanced aluminum alloys with enhanced properties for specialized applications:
4.1 Aluminum-Lithium Alloys
Aluminum-lithium alloys offer significant weight savings and improved stiffness compared to traditional aluminum alloys, making them ideal for lightweight structures in aerospace and automotive industries. With lithium as a primary alloying element, these alloys exhibit high strength-to-weight ratio and fatigue resistance, enabling the production of lightweight prototypes with superior performance characteristics.
4.2 Aluminum Matrix Composites (AMCs)
Aluminum matrix composites combine aluminum with reinforcing materials such as silicon carbide or alumina to enhance mechanical properties such as strength, stiffness, and wear resistance. These advanced materials are well-suited for rapid prototyping applications requiring superior performance in high-stress environments, such as automotive engine components, sporting goods, and aerospace structures.
5. Conclusion
In conclusion, the diverse range of aluminum grades available for rapid prototyping offers engineers and designers a wealth of options to meet their specific requirements for performance, reliability, and cost-effectiveness. By understanding the unique characteristics and applications of each aluminum alloy, prototyping professionals can make informed decisions to achieve optimal results in their projects. Whether it's the versatility of 6061 alloy, the high strength of 7075 alloy, or the corrosion resistance of 5083 alloy, aluminum grades continue to drive innovation and advancement in rapid prototyping across various industries.
Reprint Statement: If there are no special instructions, all articles on this site are original. Please indicate the source for reprinting:https://www.cncmachiningptj.com/,thanks!
3, 4 and 5-axis precision CNC machining services for aluminum machining, beryllium, carbon steel, magnesium, titanium machining, Inconel, platinum, superalloy, acetal, polycarbonate, fiberglass, graphite and wood. Capable of machining parts up to 98 in. turning dia. and +/-0.001 in. straightness tolerance. Processes include milling, turning, drilling, boring, threading, tapping, forming, knurling, counterboring, countersinking, reaming and laser cutting. Secondary services such as assembly, centerless grinding, heat treating, plating and welding. Prototype and low to high volume production offered with maximum 50,000 units. Suitable for fluid power, pneumatics, hydraulics and valve applications. Serves the aerospace, aircraft, military, medical and defense industries.PTJ will strategize with you to provide the most cost-effective services to help you reach your target,Welcome to Contact us ( sales@pintejin.com ) directly for your new project.
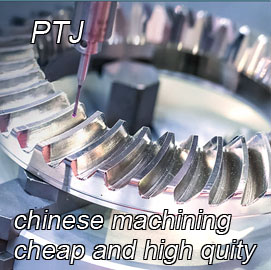
- 5 Axis Machining
- Cnc Milling
- Cnc Turning
- Machining Industries
- Machining Process
- Surface Treatment
- Metal Machining
- Plastic Machining
- Powder Metallurgy Mold
- Die Casting
- Parts Gallery
- Auto Metal Parts
- Machinery Parts
- LED Heatsink
- Building Parts
- Mobile Parts
- Medical Parts
- Electronic Parts
- Tailored Machining
- Bicycle Parts
- Aluminum Machining
- Titanium Machining
- Stainless Steel Machining
- Copper Machining
- Brass Machining
- Super Alloy Machining
- Peek Machining
- UHMW Machining
- Unilate Machining
- PA6 Machining
- PPS Machining
- Teflon Machining
- Inconel Machining
- Tool Steel Machining
- More Material