How To Reduce The Cost Of Manufacturing During CNC Lathing
2023-09-26
In the world of precision machining, CNC (Computer Numerical Control) lathing is a fundamental process that plays a crucial role in the production of various components. However, the cost of manufacturing using CNC lathing can be a significant concern for many businesses. In this comprehensive guide, we will explore various strategies and techniques to reduce the cost of manufacturing during CNC lathing.
Understanding CNC Lathing
Before we delve into cost reduction strategies, let's begin by understanding the basics of CNC lathing. CNC lathing is a subtractive manufacturing process that involves the removal of material from a workpiece to create a desired shape or part. It is widely used in industries such as aerospace, automotive, and medical devices, among others, due to its precision and versatility. The primary components of a CNC lathe include the workpiece, the cutting tool, and the CNC controller. The CNC controller interprets a computer-generated design file (usually in CAD/CAM software) and guides the cutting tool to remove material from the workpiece with precision and accuracy.Challenges in CNC Lathing Cost Reduction
Reducing the cost of manufacturing in CNC lathing can be a complex task, as it involves optimizing various aspects of the process. Some of the key challenges include:- Material Costs: The choice of material for the workpiece can significantly impact manufacturing costs. High-quality and exotic materials can be expensive, so selecting the right material is crucial.
- Tooling Costs: CNC lathing requires specialized cutting tools, and tool wear and replacement can add to production expenses.
- Labor Costs: Skilled operators are required to program and operate CNC lathes, and their wages contribute to manufacturing costs.
- Energy Consumption: CNC lathes consume energy for both machining and cooling systems, which can be a substantial cost factor.
- Waste Management: Material wastage due to inefficient cutting or programming can increase costs and harm sustainability efforts.
- Downtime: Unplanned downtime, maintenance, and tool changes can disrupt production schedules and increase overall costs.
- Quality Control: Ensuring the quality of machined parts is essential, as defective parts can lead to costly rework or scrap.
Material Selection and Optimization
The choice of material significantly affects manufacturing costs. Consider the following strategies:- a. Material Selection: Evaluate the application and requirements of the part to select the most cost-effective material that meets performance criteria.
- b. Material Optimization: Minimize waste by using optimal stock sizes and shapes to reduce material costs and machining time.
Tooling Strategies
Optimizing tooling is crucial for cost reduction. Here's how:- a. Tool Selection: Choose the right cnc cutting tools based on material and machining requirements to enhance tool life and reduce replacement costs.
- b. Tool Life Management: Implement tool life monitoring systems to replace tools only when necessary, reducing downtime and tooling expenses.
- c. Cutting Speed and Feed Rates: Optimize cutting speeds and feed rates for efficiency without compromising quality to minimize tool wear.
Labor Efficiency
Maximize the efficiency of your workforce:- a. Training: Invest in operator training programs to enhance skills, reduce errors, and improve productivity.
- b. Programming Efficiency: Optimize CNC programs to minimize cycle times and reduce operator intervention.
Energy Management
Reduce energy consumption in CNC lathing:- a. Efficient Machines: Invest in energy-efficient CNC lathes and cooling systems to lower electricity costs.
- b. Off-Peak Production: Schedule heavy machining during off-peak hours when energy rates are lower.
Waste Reduction
Minimize material waste and enhance sustainability:- a. CAD/CAM Software: Utilize advanced software to optimize toolpaths, reducing material wastage.
- b. Recycling: Implement recycling programs for materials and cutting fluids to reduce waste disposal costs.
Downtime Management
Minimize unplanned downtime:- a. Preventive Maintenance: Implement regular maintenance schedules to prevent breakdowns and maintain machine efficiency.
- b. Spare Parts Inventory: Maintain a well-stocked inventory of critical spare parts to reduce waiting time for replacements.
Quality Control
Ensure high-quality parts from the start:- a. In-Process Inspection: Implement real-time quality checks to identify issues early and avoid costly rework.
- b. Statistical Process Control (SPC): Use SPC techniques to monitor and control the machining process for consistent quality.
Automation and Robotics
Integrate automation into CNC lathing processes:- a. Robotic Loading: Use robots for material handling and tool changes to reduce labor costs and improve efficiency.
- b. Lights-Out Machining: Explore lights-out machining options to extend production hours without increasing labor costs.
Supply Chain Optimization
Streamline your supply chain for cost savings:- a. Vendor Relationships: Develop strong relationships with material and tooling suppliers to negotiate favorable terms and pricing.
- b. Just-in-Time (JIT): Implement JIT inventory management to reduce carrying costs and minimize waste.
Continuous Improvement
Foster a culture of continuous improvement:- a. Lean Manufacturing: Implement lean principles to eliminate waste, improve processes, and reduce costs systematically.
- b. Kaizen Events: Conduct Kaizen events to involve employees in identifying and implementing cost-saving improvements.
Conclusion
Reducing the cost of manufacturing during CNC lathing is a multifaceted endeavor that requires a holistic approach. By carefully considering material selection, tooling strategies, labor efficiency, energy management, waste reduction, downtime management, quality control, automation, supply chain optimization, and continuous improvement, businesses can significantly lower production costs while maintaining or even improving product quality. Implementing these strategies requires a commitment to ongoing evaluation and adaptation, but the long-term benefits in terms of cost savings and competitiveness are well worth the effort.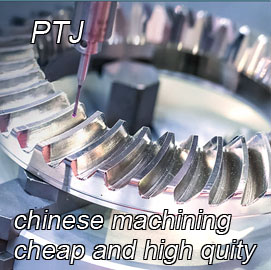
Our Services
- 5 Axis Machining
- Cnc Milling
- Cnc Turning
- Machining Industries
- Machining Process
- Surface Treatment
- Metal Machining
- Plastic Machining
- Powder Metallurgy Mold
- Die Casting
- Parts Gallery
Case Studies
- Auto Metal Parts
- Machinery Parts
- LED Heatsink
- Building Parts
- Mobile Parts
- Medical Parts
- Electronic Parts
- Tailored Machining
- Bicycle Parts
Material List
- Aluminum Machining
- Titanium Machining
- Stainless Steel Machining
- Copper Machining
- Brass Machining
- Super Alloy Machining
- Peek Machining
- UHMW Machining
- Unilate Machining
- PA6 Machining
- PPS Machining
- Teflon Machining
- Inconel Machining
- Tool Steel Machining
- More Material
Parts Gallery