5 Essential Technology Skills of CNC Machining Centers You Should Master
2023-09-15
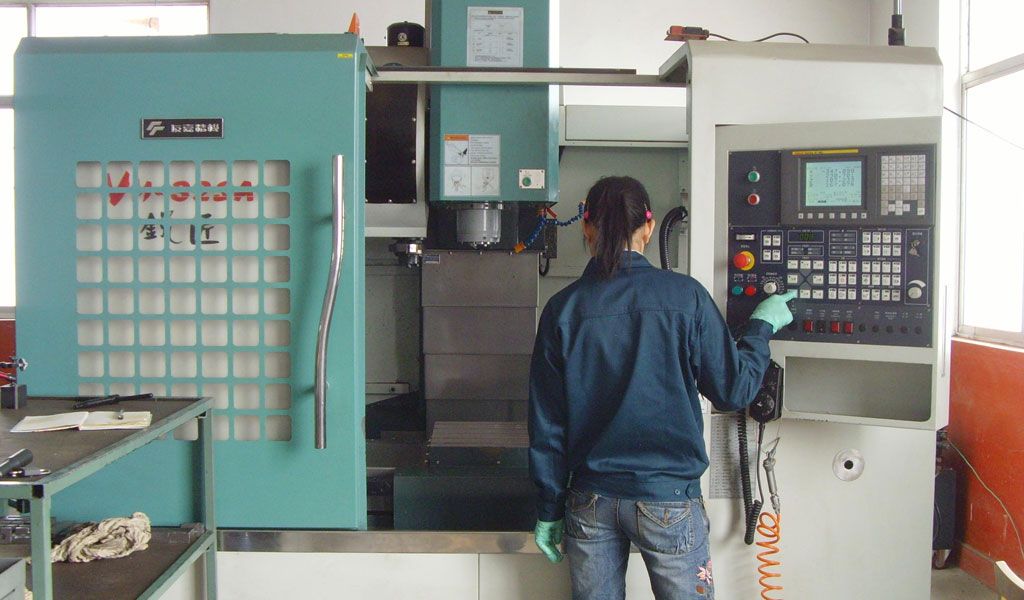
CNC Programming Proficiency
CNC programming is the foundation of operating a machining center effectively. It involves creating a set of instructions that guide the CNC machine in producing a desired part. To become proficient in CNC programming, you need to understand the following:- a. G-code and M-code fundamentals: Learn the basics of G-codes (geometric codes) and M-codes (miscellaneous function codes) used to control CNC machines. Understand how to write, edit, and troubleshoot these codes to achieve precise machining operations.
- b. CAD/CAM software utilization: Familiarize yourself with Computer-Aided Design (CAD) software for creating 3D models and Computer-Aided Manufacturing (CAM) software for generating toolpaths and G-code from these models. Explore popular software options like AutoCAD, SolidWorks, and Mastercam.
- c. Toolpath generation: Master the art of creating efficient and optimized toolpaths that minimize cycle times, reduce tool wear, and produce high-quality parts. Explore different strategies for 2D and 3D machining, including contouring, pocketing, and adaptive toolpaths.
- d. Simulation and verification: Understand the importance of simulating and verifying your CNC programs using software tools. Learn how to detect and rectify errors before they result in costly mistakes on the machine.
Machine Setup and Maintenance
Proper machine setup and maintenance are crucial for ensuring the longevity of CNC machining centers and achieving consistent, accurate results. Key topics to explore in this area include:- a. Machine calibration: Learn how to calibrate the machine's axes and tools to maintain precision throughout the contract cnc machining process.
- b. Tool selection and management: Understand how to choose the right cutting tools for specific materials and applications. Explore tool-changing procedures and tool life management.
- c. Workholding techniques: Discover various workholding methods, such as clamps, vises, and fixtures, and how to select the most suitable option for your job.
- d. Lubrication and cooling systems: Familiarize yourself with the importance of proper lubrication and cooling to prevent overheating and tool wear. Learn how to maintain these systems for optimal performance.
- e. Routine maintenance tasks: Develop a maintenance schedule for cleaning, inspection, and preventive maintenance of your CNC machining center. Learn how to identify and address common issues promptly.
CNC Machine Control
To operate a CNC machining center effectively, you must have a deep understanding of its control system. Key topics to explore in this section include:- a. Machine interfaces: Learn how to navigate and operate the machine's control panel, including the keyboard, monitor, and manual controls.
- b. Axis control: Understand how to move and position the machine's axes accurately using both manual and automated methods.
- c. Program loading and execution: Master the process of loading CNC programs, setting work offsets, and executing machining operations safely.
- d. Emergency procedures: Familiarize yourself with emergency stop procedures and safety protocols to protect both the machine and its operators.
CNC Machining Strategies
Efficient machining strategies are essential for optimizing productivity and achieving high-quality parts. Explore the following topics related to CNC machining strategies:- a. Cutting speeds and feeds: Learn how to calculate and adjust cutting speeds and feeds for different materials, tool types, and cutting conditions.
- b. Toolpath optimization: Understand how to optimize toolpaths for improved chip evacuation, reduced tool wear, and minimized cycle times.
- c. High-speed machining (HSM): Explore advanced techniques like HSM, which enables high speed machining with higher accuracy and surface finish.
- d. Multi-axis machining: Familiarize yourself with multi-axis machining capabilities and techniques, including 4-axis and 5-axis machining, to expand your machining capabilities.
Automation and Industry 4.0 Integration
The future of CNC machining centers lies in automation and integration with Industry 4.0 technologies. Stay ahead of the curve by learning about:- a. CNC automation: Explore the use of automation technologies like robotic loading/unloading, pallet changers, and conveyor systems to enhance productivity and reduce labor costs.
- b. Internet of Things (IoT) and data analytics: Understand how IoT sensors and data analytics can provide real-time monitoring of machine performance and predictive maintenance insights.
- c. CNC networking: Learn about networking CNC machines to enable data exchange, remote monitoring, and centralized control.
- d. Cybersecurity: Stay informed about cybersecurity best practices to protect CNC machines and data from potential threats.
Conclusion
In today's fast-evolving manufacturing landscape, mastering the technology skills associated with CNC machining centers is essential for career growth and staying competitive. By developing proficiency in CNC programming, machine setup and maintenance, CNC machine control, machining strategies, and automation, you can unlock the full potential of these powerful machines and contribute to the future of precision manufacturing. Whether you're a novice CNC enthusiast or an experienced machinist, continuous learning and adaptation to emerging technologies will ensure that you remain at the forefront of CNC machining advancements. Embrace the opportunities presented by Industry 4.0 and the ongoing innovations in CNC technology to propel your career and contribute to the exciting developments in modern manufacturing.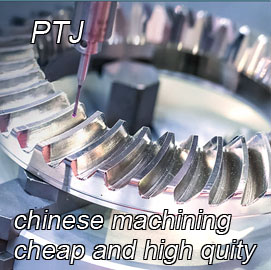
Our Services
- 5 Axis Machining
- Cnc Milling
- Cnc Turning
- Machining Industries
- Machining Process
- Surface Treatment
- Metal Machining
- Plastic Machining
- Powder Metallurgy Mold
- Die Casting
- Parts Gallery
Case Studies
- Auto Metal Parts
- Machinery Parts
- LED Heatsink
- Building Parts
- Mobile Parts
- Medical Parts
- Electronic Parts
- Tailored Machining
- Bicycle Parts
Material List
- Aluminum Machining
- Titanium Machining
- Stainless Steel Machining
- Copper Machining
- Brass Machining
- Super Alloy Machining
- Peek Machining
- UHMW Machining
- Unilate Machining
- PA6 Machining
- PPS Machining
- Teflon Machining
- Inconel Machining
- Tool Steel Machining
- More Material
Parts Gallery