The Molding Method Of Industrial Ceramic Machining
Mechanical accessories made of modern industrial ceramics are widely used in military ceramics, textile ceramics, electronic and electrical ceramics, etc. So do you know how industrial ceramics are formed? What are the methods? Pintejin Ceramics will tell you.
There are many types of industrial ceramics, classified according to raw materials, they are divided into the following series:
- --- Oxide ceramics: mainly alumina ceramics, zirconia ceramics, mullite ceramics, etc.;
- --- Carbide ceramics: mainly silicon carbide ceramics, titanium carbide ceramics, boron carbide ceramics, etc.;
In industrial ceramic processing machinery, in addition to some milling machines, grinders and CNC precision engraving machines, grinding machines are also its important ceramic processing machinery, which can achieve high-precision ceramic processing.
Grinding: At present, most industrial ceramics processing mainly adopts grinding. Due to the high hardness of 99 alumina ceramic materials, diamond (natural and artificial) materials are usually used for grinding wheels, while B4C materials are mainly used for grinding.
Research shows that in the grinding process of 99 alumina industrial ceramics, industrial ceramic materials mainly include brittle removal methods such as grain removal, brittle fracture, material exfoliation, and grain boundary microfracture.
The main forming methods of industrial ceramics:
- --- Dry pressing molding: There are two types of presses for dry pressing molding technology, hydraulic and mechanical, which can be semi-automatic or fully automatic. When the pressure is particularly high, it is 200Mpa. The output can reach 15 to 50 pieces per minute. Due to the uniform stroke pressure of the hydraulic press, the height of the pressed parts is different when the powder filling is different. However, the pressure applied by the mechanical press varies with the amount of powder filling, which may easily lead to differences in dimensional shrinkage after sintering, affecting product quality. Therefore, the uniform distribution of powder particles during dry pressing is very important for mold filling.
- --- Grouting molding method: grouting molding adopts plaster mold, which is low in cost and easy to form parts with large size and complex shape. The key to grouting is the preparation of the material. Usually water is used as the solvent medium, and then debonding agent and binder are added. After a long time of grinding, the air is exhausted, and then poured into the plaster mold. Due to the adsorption of water by the capillary of the plaster mold, the slurry solidifies in the mold. When hollow grouting, when the mold wall absorbs the slurry to the required thickness, the excess slurry needs to be poured out. In order to reduce the shrinkage of the green body, a high-concentration slurry should be used as much as possible.
- --- Sintering and molding method: The technical method of densifying granular industrial ceramic bodies and forming solid materials is called sintering. Sintering is a method of removing the voids between the particles in the body, removing a small amount of gas and impurities, and making the particles grow and combine with each other to form a new substance.
Pintejin ceramic company provides ceramic machining services to engineers, product developers, designers, and more through our in-housing capabilities. Our highly qualified ISO9001:2015 and ITAF 16949 machine shops can make any custom design, simple or complex. We offer rapid ceramic prototypes, small-batch machining, and high-volume production, with all orders serviced by Pintejin from end to end. We accept technical drawings and have support teams to ensure you get your machined parts or mold at quality and on time.
our machining ceramic website:https://machiningceramic.com/
3, 4 and 5-axis precision CNC machining services for aluminum machining, beryllium, carbon steel, magnesium, titanium machining, Inconel, platinum, superalloy, acetal, polycarbonate, fiberglass, graphite and wood. Capable of machining parts up to 98 in. turning dia. and +/-0.001 in. straightness tolerance. Processes include milling, turning, drilling, boring, threading, tapping, forming, knurling, counterboring, countersinking, reaming and laser cutting. Secondary services such as assembly, centerless grinding, heat treating, plating and welding. Prototype and low to high volume production offered with maximum 50,000 units. Suitable for fluid power, pneumatics, hydraulics and valve applications. Serves the aerospace, aircraft, military, medical and defense industries.PTJ will strategize with you to provide the most cost-effective services to help you reach your target,Welcome to Contact us ( sales@pintejin.com ) directly for your new project.
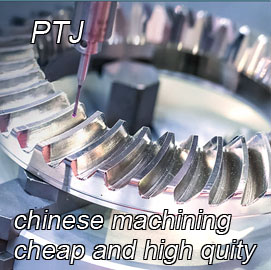
- 5 Axis Machining
- Cnc Milling
- Cnc Turning
- Machining Industries
- Machining Process
- Surface Treatment
- Metal Machining
- Plastic Machining
- Powder Metallurgy Mold
- Die Casting
- Parts Gallery
- Auto Metal Parts
- Machinery Parts
- LED Heatsink
- Building Parts
- Mobile Parts
- Medical Parts
- Electronic Parts
- Tailored Machining
- Bicycle Parts
- Aluminum Machining
- Titanium Machining
- Stainless Steel Machining
- Copper Machining
- Brass Machining
- Super Alloy Machining
- Peek Machining
- UHMW Machining
- Unilate Machining
- PA6 Machining
- PPS Machining
- Teflon Machining
- Inconel Machining
- Tool Steel Machining
- More Material