What technical requirements need to be followed for machining
In terms of mechanical processing skills, only by complying with these skills requirements can the processed products be more standard and reasonable. The detailed skills requirements are as follows
(1) The processed appearance of the parts must not have defects such as scratches and scratches that damage the appearance of the parts.
(2) Remove oxide scale on parts.
(3) Civil servants in the uninjected form shall meet the requirements of GB1184-80, and the agreed error of the uninjected length scale is ±0.5mm.
(4) Casting official belt is symmetrical to the basic standard equipment of blank casting.
(5) Install rolling bearings, and it is agreed to use oil for heating, and the oil temperature should not exceed 100°C.
(6) When installing the hydraulic system, it is agreed to use sealing fillers and sealants, but they should be prevented from entering the system.
(7) The parts and components that enter the installation need to check the conformity certificate of the part.
(8) The parts should be cleaned before installation, and there should be no burrs, flashes, oxide skins, rust, chips, oil stains, colorants, dust, etc.
(9) Before installation, review the main cooperation scale of parts and parts, especially the excess cooperation scale and related accuracy.
(10) During the installation process, the parts must not collide, collide, damage, or rust.
(11) When tightening screws, bolts and nuts, it is forbidden to impact or use improper rotating appliances and wrenches. After tightening, do not damage the screw grooves, nuts and screws, and bolt heads.
(12) The tightening torque required by the rule requires a torque wrench to be selected, and the tightening torque is to be tightened according to the rule.
(13) After bonding, remove the remaining adhesive that flows out.
(14) The semicircular holes of the outer ring of the bearing and the open bearing seat and the bearing cover must not be blocked. The outer ring of the bearing and the semicircular hole of the open bearing seat and the bearing cover have good contact. When inspected by coloring, it is symmetrical to the center line of the bearing seat. 120°, uniform contact with the bearing cover within the range of 90° symmetrical to the center line. When checking with a feeler gauge within the above range, the 0.03mm feeler gauge shall not be inserted into 1/3 of the outer ring width.
(15) After installing the outer ring of the bearing, it should be in uniform contact with the end face of the bearing cap of the positioning end.
(16) After the rolling bearing is installed, it can be rolled flexibly and stably by hand.
(17) The joint surfaces of the upper and lower bearing bushes are in close contact and cannot be seen with a 0.05mm feeler gauge.
(18) When fixing the bearing bush with a positioning pin, make sure that the opening and closing faces and end breads of the socket face and end face of the relevant bearing hole are equal to each other. Hinge and sales shall not be loosened after cancellation.
(19) Alloy bearing linings are forbidden to be used when they are yellow in appearance. The rule is that the nucleation phenomenon is prohibited within the touch angle, and the nucleation area outside the touch angle shall not exceed 10% of the total area of the non-touch area.
(20) The reference end face of the gear (worm gear)** is consistent with the shoulder (or the end face of the positioning sleeve), and cannot be seen with a 0.05mm feeler gauge. Ensure the perpendicularity requirements of the reference end face of the gear and the axis.
(21) Strictly check the sharp corners, burrs and foreign objects remaining during the processing of the parts before assembly and remove them. Ensure that the seal will not be damaged when the seal is installed.
(22) The appearance of castings does not agree with the defects of cold partition, cracks, shrinkage holes, penetrating defects and serious damage.
(23) Castings should be cleaned up, free of burrs and flashes. The exits indicated by non-processing should be smooth with the appearance of the castings.
(24) The casting and marking of the unprocessed appearance of the casting should be clearly identified, and the position and font should meet the pattern requirements.
(25) Castings should be cleaned of exits, thorns, etc. The export residues of non-processed appearance should be smooth and polished to meet the appearance quality requirements.
(26) The molding sand, core sand and core bone on the casting should be removed.
(27) Castings have inclined parts, and their scale official belts should be symmetrically equipped along the inclined plane.
(28) Correct the right and wrong type, boss casting deviation, etc., to achieve a smooth transition and ensure the appearance quality.
(29) The surface of the casting should be smooth, and the gate, burr, sand, etc. should be removed.
(30) Castings do not promise casting defects such as cold barriers, cracks, holes, etc. that will damage the use.
(31) Before spraying, the appearance of all steel products that need to be sprayed needs to be removed from rust, oxide scale, grease, dust, soil, salt, and dirt.
(32) The non-processed appearance of mechanical product castings requires shot peening or roller treatment to meet the requirements of Sa21/2 level of cleanliness.
Link to this article: What technical requirements need to be followed for machining
Reprint Statement: If there are no special instructions, all articles on this site are original. Please indicate the source for reprinting:https://www.cncmachiningptj.com
PTJ® is a custom manufacturer that provides precision machining and straightening shafting for freshwater and seawater marine applications. All are custom metal fabrication and fastener. Manufacturing capabilities include 5 Axis Precision Machining Copper Parts, gear cutting, CNC milling, CNC Lathing, broaching, CNC drilling, hobbing, honing, and internal and external forming. Other services include finishing, sharpening, grinding, filleting, pointed ends, chamfering, straightening and sawing. The radius keyway is cut according to specifications. The shaft system is processed into S.A.E. J755 standard.
Tell us a little about your project’s budget and expected delivery time. We will strategize with you to provide the most cost-effective services to help you reach your target,You are welcome to contact us directly ( sales@pintejin.com ) .
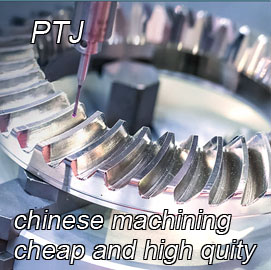
- 5 Axis Machining
- Cnc Milling
- Cnc Turning
- Machining Industries
- Machining Process
- Surface Treatment
- Metal Machining
- Plastic Machining
- Powder Metallurgy Mold
- Die Casting
- Parts Gallery
- Auto Metal Parts
- Machinery Parts
- LED Heatsink
- Building Parts
- Mobile Parts
- Medical Parts
- Electronic Parts
- Tailored Machining
- Bicycle Parts
- Aluminum Machining
- Titanium Machining
- Stainless Steel Machining
- Copper Machining
- Brass Machining
- Super Alloy Machining
- Peek Machining
- UHMW Machining
- Unilate Machining
- PA6 Machining
- PPS Machining
- Teflon Machining
- Inconel Machining
- Tool Steel Machining
- More Material