Sheet metal machining process
According to the difference in the structure of sheet metal parts, the production process can be different, but the total does not exceed the following many levels.
1. Cutting: There are various ways of cutting, the most important are the following methods
①. Hydraulic shearing machine: It uses hydraulic shearing machine to cut simple strips. It is important to prepare fully processed mold shells for blanking and forming. The cost is low, and the precision is less than 0.2, but only processing without holes and arcs. Strip or block surface layer.
②. Stamping machine tool: It uses the stamping machine tool to form various shapes of materials by cold punching the flat parts after the parts are developed on the plate in one or more steps. Its advantages are that the construction time is shorter, the efficiency is high, the high precision, and the cost is low. It can be produced in large quantities, but it needs to be designed with a model.
③. NC CNC lathe blanking. When NC blanking, the NC lathe processing program flow should be written at the beginning. Use the CNC lathe to program the mobile phone software, and make the expanded drawing sister to the NC digital drawing machining center can distinguish the program flow, let it be based on This kind of program flow is one step at a time to cold-punch the various shapes of flat parts on the flat plate, but its structure is affected by the structure of the CNC tool, the cost is low, and the precision is less than 0.15.
④. Laser laser cutting is the use of fiber line fiber laser cutting method to cut the structure of the flat plate on a large flat plate. The laser laser program flow is required to be written like NC cutting. It can download all kinds of complex patterns. The cost of flat parts increases, and the precision is less than 0.1.
⑤. Numerical control sawing machine: mainly use aluminum profiles, galvanized square steel, rectangular steel, and round sliding rods, with low cost and low precision.
1. Planer: countersinking, tapping, punching, opening
The counterbore angle is generally 120°C, used for pulling rivets, and 90°C used for countersunk bolts, tapping the outer diameter bottom hole of the external thread.
2. Negative side:
also called hole extraction and hole turning, which is to draw a slightly larger hole on a smaller base hole, and then tap the teeth. It is important to use thinner sheet metal processing to improve its tensile strength and imperial system. The number of turns of the threaded coil to avoid slipping teeth. It is generally used for the thinner plate thickness and the normal shallow reverse side of the hole. Most of the thickness does not change. When the thickness is allowed to become loose by 30-40%, the result can be better than everything. The aspect ratio of the reverse side is 40-60%. When the thickness is 50%, a large reverse side aspect ratio can be obtained. When the thickness of the board is very large, such as 2.0, 2.5 and other thicknesses, You can tap the teeth immediately.
3. Punching machine tool:
It is a processing and production process that uses mold shell forming. Generally, punching machine tools include automatic punching machine, arc, blanking, punching convex hull (projection), punching and tearing, punching, forming and other processing methods. Its processing must have relative mold shells to carry out the operation process, such as automatic punching machine blanking mold, convex mold, tearing mold, punching mold, forming mold, etc., the operation process is important to pay attention to position and specificity.
4. Pressure riveting:
As far as the company is concerned, pressure riveting is important including pressure riveting nuts, screws, and non-dismounting. It is based on the four-column hydraulic pressure riveting machine or punching machine to carry out the operation process and riveting it to the sheet metal parts. There is also a riveting method, which requires attention to specificity.
5. Sheet metal bending;
sheet metal bending is to fold 2D flat parts into 3D parts. Its processing must be carried out with a folding bed and corresponding bending molds. It also has a certain sheet metal bending sequence. The specification is to bend first without interference for the next cut, and then bend after interference.
Link to this article: Sheet metal machining process
Reprint Statement: If there are no special instructions, all articles on this site are original. Please indicate the source for reprinting:https://www.cncmachiningptj.com
PTJ® is a customized manufacturer that provides a full range of copper bars, brass parts and copper parts. Common manufacturing processes include blanking, embossing, coppersmithing, wire edm services, etching, forming and bending, upsetting, hot forging and pressing, perforating and punching, thread rolling and knurling, shearing, multi spindle machining, extrusion and metal forging and stamping. Applications include bus bars, electrical conductors, coaxial cables, waveguides, transistor components, microwave tubes, blank mold tubes, and powder metallurgy extrusion tanks.
Tell us a little about your project’s budget and expected delivery time. We will strategize with you to provide the most cost-effective services to help you reach your target,You are welcome to contact us directly ( sales@pintejin.com ) .
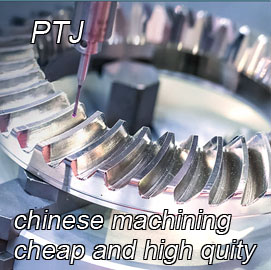
- 5 Axis Machining
- Cnc Milling
- Cnc Turning
- Machining Industries
- Machining Process
- Surface Treatment
- Metal Machining
- Plastic Machining
- Powder Metallurgy Mold
- Die Casting
- Parts Gallery
- Auto Metal Parts
- Machinery Parts
- LED Heatsink
- Building Parts
- Mobile Parts
- Medical Parts
- Electronic Parts
- Tailored Machining
- Bicycle Parts
- Aluminum Machining
- Titanium Machining
- Stainless Steel Machining
- Copper Machining
- Brass Machining
- Super Alloy Machining
- Peek Machining
- UHMW Machining
- Unilate Machining
- PA6 Machining
- PPS Machining
- Teflon Machining
- Inconel Machining
- Tool Steel Machining
- More Material