How to set a safe tool change point for CNC machining center?
The CNC indexing head can provide a lot of convenience for some multi-faceted products. It can process the workpiece at multiple angles at one time, so it can significantly reduce the processing procedures
However, when the workpiece itself (especially when processing the side of the workpiece) is relatively high, or the height of the fixture is relatively high, interference between the tool and the fixture may occur when the tool is changed, which may cause the tool or even the tool change The system is damaged. To prevent this kind of problem, we must pay attention to the following points
1. Placement of workpieces and fixtures on the worktable
Since the disc-type tool magazine is generally installed on the upper left side of the machine tool, the tool change action will also be performed on the left side of the spindle. When changing the tool, the space below the tool arm will be temporarily used, so the workpiece and fixture cannot appear here.
The worktable can be moved left and right. If the workbench is selected as the installation position of the workpiece and fixture, the workpiece and fixture will be on the left side of the spindle no matter how the workbench is moved. This may not be a problem when the height of the workpiece and fixture is relatively low. , But once the workpiece and fixture conflict with the tool change action due to the height relationship, the workpiece and fixture can only be removed at this time, and the debugging can be performed again.
Therefore, it is a good choice to prioritize the use of the space on the right side of the workbench.
2. Selection of tool change point
Due to the restriction of conditions, the action of tool change has to be completed at a specific point, which can be the upper left corner of the workbench first.
3. Consistency of tool change point
We installed the workpiece on the right side of the workbench, and the safe tool change point has been set in the program. However, when the operator grinds or replaces the tool, he may forget the tool change point. Problem, causing damage to the workpiece or tool.
Link to this article: How to set a safe tool change point for CNC machining center?
Reprint Statement: If there are no special instructions, all articles on this site are original. Please indicate the source for reprinting:https://www.cncmachiningptj.com
PTJ® is a customized manufacturer that provides a full range of copper bars, brass parts and copper parts. Common manufacturing processes include blanking, embossing, coppersmithing, wire edm services, etching, forming and bending, upsetting, hot forging and pressing, perforating and punching, thread rolling and knurling, shearing, multi spindle machining, extrusion and metal forging and stamping. Applications include bus bars, electrical conductors, coaxial cables, waveguides, transistor components, microwave tubes, blank mold tubes, and powder metallurgy extrusion tanks.
Tell us a little about your project’s budget and expected delivery time. We will strategize with you to provide the most cost-effective services to help you reach your target,You are welcome to contact us directly ( sales@pintejin.com ) .
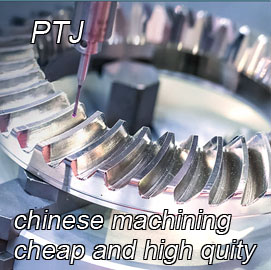
- 5 Axis Machining
- Cnc Milling
- Cnc Turning
- Machining Industries
- Machining Process
- Surface Treatment
- Metal Machining
- Plastic Machining
- Powder Metallurgy Mold
- Die Casting
- Parts Gallery
- Auto Metal Parts
- Machinery Parts
- LED Heatsink
- Building Parts
- Mobile Parts
- Medical Parts
- Electronic Parts
- Tailored Machining
- Bicycle Parts
- Aluminum Machining
- Titanium Machining
- Stainless Steel Machining
- Copper Machining
- Brass Machining
- Super Alloy Machining
- Peek Machining
- UHMW Machining
- Unilate Machining
- PA6 Machining
- PPS Machining
- Teflon Machining
- Inconel Machining
- Tool Steel Machining
- More Material