The development and trend of vacuum induction melting technology
With the rapid development of modern industrial technology, people's requirements for the use of mechanical parts are getting higher and higher, and the more severe use environment puts forward higher requirements for the high temperature resistance, wear resistance, fatigue resistance and other properties of metal materials.
For some specific metals or alloy materials, whether it is early stage R&D test or later stage mass production and put into use, research or obtain high-performance metal alloy materials require the support of metal smelting equipment, surface heat treatment equipment, etc. Among the many special heating or smelting methods, induction heating technology is used to smelt and prepare metal materials or to sinter and heat treat materials in a certain process, which has played a vital role.
This article introduces the development process of vacuum induction smelting technology and the application of induction smelting technology in different occasions. According to the structure of different vacuum induction furnace types, compare their advantages and disadvantages. Looking forward to the future development direction of vacuum induction furnaces, expounds its development trend. The development and progress of vacuum induction furnaces are mainly reflected in the gradual improvement of the overall structure of the equipment, the increasingly obvious trend of modularization and the more intelligent control system.
1. Vacuum induction melting technology
1.1 Principle
__kindeditor_temp_url__Induction heating technology usually refers to a technology that uses the principle of electromagnetic induction to obtain induction current for materials with better magnetic sensitivity to achieve the purpose of heating under vacuum conditions. The electric current passes through the electromagnetic coil surrounding the metal material at a certain frequency. The changing electric current generates an induced magnetic field, which causes an induced current in the metal and generates a large amount of heat to heat the material. When the heat is relatively low, it can be used in vacuum induction heat treatment and other processes. When the heat is high, the heat generated is enough to melt the metal and be used to prepare metal or alloy materials.
1.2, application
1.2.1, vacuum induction melting
Vacuum induction melting technology is currently the most efficient, fastest, low-consumption, energy-saving and environmentally friendly induction heating technology for heating metal materials. This technology is mainly implemented in induction melting furnaces and other equipment and has a wide range of applications. The solid metal raw materials are placed in a crucible wrapped by a coil. When the current flows through the induction coil, an induced electromotive force is generated and an eddy current is generated inside the metal charge. When the current heat is greater than the rate of heat dissipation of the metal charge, the heat accumulates more and more When reaching a certain level, the metal melts from a solid state to a liquid state to achieve the purpose of smelting metals. In this process, since the whole process takes place in a vacuum environment, it is beneficial to remove the gas impurities inside the metal, and the obtained metal alloy material is more pure. At the same time, during the smelting process, through the control of the vacuum environment and induction heating, the smelting temperature can be adjusted and the alloy metal can be supplemented in time to achieve the purpose of refining. During the melting process, due to the characteristics of the induction melting technology, the liquid metal material inside the crucible can be stirred automatically due to the interaction of electromagnetic force to make the composition more uniform. This is also a major advantage of the induction melting technology.
Compared with traditional smelting, vacuum induction smelting has great advantages because of energy saving, environmental protection, good working environment for workers, and low labor intensity. Using induction melting technology, the final alloy material is less impurity and the proportion of the alloy added is more suitable, which can better meet the requirements of the process for the properties of the material.
Vacuum induction smelting technology has been used on a large scale, from induction furnaces of several kilograms for experimental research to large-scale induction furnaces with a capacity of tens of tons for actual production. Because of its simple operation technology, the melting process is easy to control and the melting temperature is fast. , The smelted metal has the advantages of uniform composition, and has great application prospects, and has been rapidly developed in recent years.
1.2.2, vacuum induction sintering
Vacuum sintering refers to the sintering of metal, alloy or metal compound powder into metal products and metal blanks at a temperature below the melting point in an environment with a vacuum degree of (10-10-3Pa). Sintering under vacuum conditions, there is no reaction between metal and gas, and no influence of adsorbed gas. Not only does the densification effect is good, but it can also play a role of purification and reduction, reducing the sintering temperature, and the ratio of sintering at room temperature can be reduced by 100℃~150℃ , Save energy consumption, improve the life of the sintering furnace and obtain high-quality products.
For some materials, it is necessary to realize the bonding between particles through the transfer of atoms through heating, and the induction sintering technology plays a heating role in this process. The advantage of vacuum induction sintering is that it helps to reduce harmful substances (water vapor, oxygen, nitrogen and other impurities) in the atmosphere under vacuum conditions, and avoid a series of reactions such as decarburization, nitriding, carburizing, reduction, and oxidation. During the process, the amount of gas in the pores is reduced, and the chemical reaction of gas molecules is reduced. At the same time, the oxide film on the surface of the material is removed before the material appears in the liquid phase, so that the material is more densely bonded when the material is melted and bonded, and its wear resistance is improved. strength. In addition, vacuum induction sintering also has a certain effect on reducing product costs.
Because the gas content is relatively low in a vacuum environment, the convection and conduction of heat can be ignored. The heat is mainly transferred from the heating component to the surface of the material in the form of radiation. The selection is based on the specific sintering temperature and the physical and chemical properties of the material. Appropriate heating components are also very important. Compared with vacuum resistance heating, induction sintering adopts intermediate frequency power heating, which avoids the high-temperature insulation problem of vacuum furnaces that use resistance heating to a certain extent.
At present, induction sintering technology is mainly used in the fields of steel and metallurgy. In addition, on special ceramic materials, induction sintering enhances the bonding of solid particles, helps crystal grains grow, compresses voids, and then increases density to form dense polycrystalline sintered bodies. Induction sintering technology is also being more widely used in the research of new materials.
1.2.3, vacuum induction heat treatment
At present, there should be more induction heat treatment technology mainly concentrated in induction hardening technology. Put the workpiece into the inductor (coil), when an alternating current of a certain frequency is passed through the inductor, an alternating magnetic field will be generated around it. The electromagnetic induction of the alternating magnetic field produces a closed eddy current in the workpiece. Due to the skin effect, that is, the distribution of the induced current on the cross-section of the workpiece is very uneven, the current density on the surface of the workpiece is very high and gradually decreases inward.
The electric energy of the high-density current on the surface of the workpiece is converted into heat energy, which increases the temperature of the surface, that is, realizes surface heating. The higher the current frequency, the greater the current density difference between the surface and the interior of the workpiece, and the thinner the heating layer. After the temperature of the heating layer exceeds the critical point temperature of the steel, it is rapidly cooled to achieve surface quenching. It can be known from the principle of induction heating that the penetration depth of the current can be appropriately changed by adjusting the frequency of the current through the induction coil. The adjustable depth is also a major advantage of induction heat treatment. However, induction hardening technology is not suitable for complicated mechanical workpieces due to its poor adaptability. Although the surface layer of the quenched workpiece has a larger compressive internal stress, the fatigue fracture resistance is higher. But it is only suitable for assembly line production of simple workpieces.
At present, the application of induction hardening technology is mainly used in the surface quenching of crankshafts and camshafts in the automotive industry. Although these parts have a simple structure, but the working environment is harsh, they have a certain degree of wear resistance, bending resistance, and resistance to the performance of the parts. Fatigue requirements, through induction hardening to improve their wear resistance and fatigue resistance is also the most reasonable method to meet the performance requirements. It is widely used in the surface treatment of some parts in the automotive industry.
2. Vacuum induction melting equipment
Vacuum induction smelting equipment uses induction smelting technology to realize the principle in actual use through the matching of mechanical structure. The equipment usually uses the principle of electromagnetic induction to put the induction coil and the material into a closed cavity, and extract the gas in the container through a vacuum pumping system, and then use the power supply to pass the current through the induction coil to generate an induced electromotive force and be inside the material A vortex is formed, and when the heat generation reaches a certain level, the material starts to melt. During the melting process, a series of operations such as power control, temperature measurement, vacuum measurement, and supplementary feeding are realized through other supporting components on the equipment, and finally the liquid metal is poured into the mold through the crucible inversion to form a metal ingot. Smelt. The main structure of vacuum induction melting equipment includes the following parts:
In addition to the above components, the vacuum melting furnace should also be equipped with a power supply, a control system, and a cooling system to provide energy input for the equipment to melt the material, and provide a certain amount of cooling in key parts to prevent the system from overheating and resulting in structural life reduction or damage. For induction smelting equipment with specific process requirements, there are related auxiliary components, such as transmission trolley, furnace door opening and closing, centrifugal casting pan, observation window, etc. For equipment with more impurities, it should also be equipped with a gas filter system, etc. . It can be seen that, in addition to the necessary components, a complete set of induction melting equipment can also realize different functions by adding other components according to specific process requirements, and provide convenient conditions and implementation methods for metal preparation.
2.1. Vacuum induction melting furnace
Vacuum induction smelting furnace is a smelting equipment that first melts metal by induction heating under vacuum, and then pours liquid metal into a mold to obtain a metal ingot. The development of vacuum induction furnaces began around 1920 and was mainly used to smelt nickel-chromium alloys. Until World War II promoted the advancement of vacuum technology, the vacuum induction melting furnace was truly developed. During this period, due to the demand for alloy materials, vacuum induction melting furnaces continued to develop into large-scale, from the initial several tons to dozens of tons of ultra-large induction furnace. In order to adapt to mass production, in addition to the change in equipment capacity, the structure of the induction furnace has also evolved from a cycle furnace with a cycle as a unit to a continuous or semi-continuous vacuum induction melting for charging, mold preparation, smelting, and pouring operations. Continuous operation without stopping the furnace saves the charging time and the waiting time for the ingot to cool. The continuous production increases the efficiency and also increases the alloy output. Better meet the needs of actual production. Compared with foreign countries, the early vacuum induction furnaces in my country have relatively small capacity, mainly under 2 tons. Large-scale smelting furnaces still rely on imports from abroad. With the development of recent decades, my country can also develop large-scale vacuum induction smelting by itself. Furnace, the maximum smelting reaches more than ten tons. VIM vacuum induction melting furnace developed earlier, with simple structure, convenient use and low maintenance cost, and has been widely used in actual production.
The basic form of a vacuum induction melting furnace. Metal materials are added to the melting crucible through a rotatable turret. The other side is aligned with the crucible, and the temperature measurement is realized by inserting the thermocouple down into the molten metal. The smelted metal is driven by the turning mechanism and poured into the forming mold to realize the smelting of the metal. The entire process is simple and convenient to operate. Each smelting requires one or two workers to complete. During the smelting process, real-time temperature monitoring and adjustment of material composition can be achieved, and the final metal material is more in line with the process requirements.
2.2. Vacuum induction membrane gas furnace
For certain materials, it is not required to complete the pouring in a vacuum chamber in the process, only heat preservation and degassing in a vacuum environment are required. On the basis of the VIM furnace, the vacuum induction membrane gas furnace of the VID degassing furnace is gradually developed.
The main feature of vacuum induction degassing furnace is compact structure and small furnace volume. A smaller volume is more conducive to rapid gas extraction and a better vacuum. Compared with conventional degassing furnaces, the equipment has relatively small volume, low temperature loss, better flexibility and economy, and is suitable for liquid or solid feeding. The VID furnace can be used for the smelting and degassing of special steel and non-ferrous metals, and it needs to be poured into the mold under the conditions of an atmospheric environment or a protective atmosphere. The entire smelting process can realize the removal of impurities such as decarburization and refining of materials, dehydrogenation, deoxidation, and desulfurization, which is conducive to precise adjustment of chemical composition to meet process requirements.
Under a certain vacuum condition or protective atmosphere, the metal material is gradually melted by the heating of the induction degassing furnace, and the internal gas can be removed in this process. If an appropriate reaction gas is added in the process, it will combine with the carbon element inside the metal to generate gaseous carbides to be removed from the furnace, achieving the purpose of decarburization and refining. In the pouring process, a certain protective atmosphere needs to be introduced to ensure that the metal material that has been degassed is isolated from the gas in the atmosphere, and finally the degassing and refining of the metal material is completed.
2.3. Vacuum induction degassing pouring furnace
The vacuum induction degassing pouring furnace is developed on the basis of the first two smelting technologies. In 1988, Leybold-Heraeus, the predecessor of the German ALD company, manufactured the first VIDP furnace. The technical core of this furnace type is a compact vacuum melting chamber integrated with the induction coil crucible. It is only a little larger than the induction coil and only contains the induction coil and the crucible. Cables, water-cooling pipelines and hydraulic turnover mechanism are all installed outside the melting chamber. The advantage is to protect cables and water-cooled pipelines from damage caused by molten steel splashing and periodic changes in temperature and pressure. Due to the convenience of disassembly and facilitating the replacement of the crucible, the VIDP furnace shell is equipped with three furnace bodies. A preparation crucible furnace lining shortens the production cycle and improves production efficiency.
The furnace cover is supported on the furnace frame and two hydraulic cylinder columns by vacuum sealed bearings. When pouring, two hydraulic cylinders top the furnace cover on the side, and the furnace cover drives the melting chamber to tilt around the vacuum bearing. In the inclined pouring state, there is no relative movement between the melting chamber and the induction coil crucible. The runner is an important part of the VIDP furnace. Because the design of the VIDP furnace isolates the melting chamber from the ingot chamber, the molten steel must pass through the vacuum runner into the ingot chamber. The ingot chamber is open and closed with a square oblique side. It is composed of two parts. The fixed part is adjacent to the runner chamber, and the movable part moves horizontally along the ground track to complete the opening and closing of the ingot chamber. In some equipment, the movable part is designed to be 30 degrees, open left and right upwards, which is convenient for loading and unloading ingot molds and daily maintenance and repair of cranes. At the beginning of smelting, the furnace body is lifted by the hydraulic mechanism below, joined with the upper structure furnace cover of the furnace, and locked with a special mechanism. The upper end of the furnace cover is connected with the feeding chamber through a vacuum valve.
Since only the smelting part is enclosed in the vacuum chamber and poured out through the diversion groove, the furnace structure is compact, the melting chamber is smaller, and the vacuum can be controlled better and faster. Compared with the traditional induction melting furnace, it has the characteristics of short evacuation time and low leakage rate. The ideal pressure control can be achieved by equipping the PLC logic control system. At the same time, the electromagnetic stirring system can stably stir the molten pool, and the added elements will be uniformly dissolved in the molten pool from top to bottom, keeping the temperature close to constant. When pouring money, the runner is heated by the external heating system to reduce the initial pouring blockage of the pouring port and the runner thermal cracking. By adding filter baffle and other measures, it can alleviate the impact of molten steel and improve metal purity. Due to the small volume of the VIDP furnace, vacuum leak detection and repair are easier, and the cleaning time in the furnace is shorter. In addition, the temperature in the furnace can be measured with a small, easy-to-replace thermocouple.
2.4, induction water-cooled crucible
The water-cooled crucible electromagnetic induction vacuum levitation smelting method is a smelting method that has developed rapidly in recent years. It is mainly used to prepare high melting point, high purity and extremely active metal or non-metal materials. By cutting the copper crucible into equal parts of the copper petal structure, and water cooling is passed through each petal block, this structure enhances the electromagnetic thrust, so that the molten metal is squeezed in the middle to form a hump and break away from the crucible wall. The metal is placed in an alternating electromagnetic field. The device concentrates the capacity in the volume space inside the crucible, and then forms a strong eddy current on the surface of the charge. On the one hand, it releases Joule heat to melt the charge, and on the other hand, it forms Lorentz force to melt The body suspends and produces strong stirring. The added alloy elements can be quickly and evenly mixed in the melt, making the chemical composition more uniform and the temperature conduction more balanced. Due to the effect of magnetic levitation, the melt is out of contact with the inner wall of the crucible, which prevents the crucible from polluting the melt. At the same time, it reduces heat conduction and enhances heat radiation, which reduces the heat dissipation of the molten metal and reaches a higher temperature. For the added metal charge, it can be melted and kept warm according to the required time and set temperature, and the charge does not need to be processed in advance. Water-cooled crucible smelting can reach the level of electron beam smelting in terms of removing metal inclusions and degassing refining, while the evaporation loss is smaller, and the energy consumption is lower, and the production efficiency is improved. Due to the non-contact heating characteristics of induction heating, the impact on the melt is smaller, and it has a good effect on the preparation of higher purity or extremely active metals. Due to the complex structure of the equipment, it is still difficult to realize maglev smelting for large-capacity equipment. At this stage, there is no large-capacity water-cooled copper crucible smelting equipment. The current water-cooled crucible equipment is only used for experimental research on small-volume metal smelting.
3. The future development trend of induction melting equipment
With the development of vacuum induction heating technology, furnace types are constantly changing in order to achieve different functions. From a simple smelting or heating structure, it has gradually developed into a complex structure that can realize different functions and is more conducive to production. For more complex technological processes in the future, how to achieve precise process control, measure and extract relevant information, and reduce labor costs as much as possible is the development direction of induction melting equipment.
3.1, modular
In a complete set of equipment, different components are equipped for different usage requirements. Each part of the component performs its own function to achieve its own use purpose. For certain furnace types, adding certain modules to make the equipment more complete, for example, equipped with a complete temperature measurement system helps to observe the changes of the materials in the furnace with temperature, and achieve a more reasonable control of the temperature; equipped with a mass spectrometer to detect the material composition Adjust the time and sequence of adding alloying elements to improve the performance of the alloy in the development stage of the process; equipped with an electron gun and ion gun to solve the problem of melting of some refractory metals, and so on. In the future induction metallurgical equipment, different combinations of different modules to achieve different functions and to meet different process requirements have become an inevitable trend of development, and it is also a combination and reference of different fields. In order to improve the metal smelting process and obtain materials with better performance, modular equipment will have stronger market competitiveness.
3.2. Intelligent control
Compared with traditional smelting, vacuum induction equipment has a great advantage in realizing process control. Due to the development of computer technology, the friendly operation of the man-machine interface, intelligent signal acquisition and reasonable program setting in the equipment can easily achieve the purpose of controlling the smelting process, reduce labor costs, and make the operation more simple and convenient.
In the future development, more intelligent control systems will be added to the vacuum equipment. For the established process, it will be easier for people to precisely control the smelting temperature through the intelligent control system, add alloy materials at a specific time, and complete a series of actions of smelting, heat preservation, and pouring. And all of this will be controlled and recorded by the computer, reducing unnecessary losses caused by human errors. For the repetitive smelting process, it can realize more convenient and intelligent modern control.
3.3. Informatization
Induction smelting equipment will generate a large amount of smelting information during the entire smelting process, the real-time parameter changes of the induction heating power supply, the temperature field of the charge, the crucible, the electromagnetic field generated by the induction coil, the physical properties of the metal melt, and so on. At present, the equipment only realizes simple data collection, and the analysis process is carried out after the data is extracted after the smelting is completed. In the future, the development of informatization, data collection and processing, and the analysis process will inevitably be almost synchronized with the smelting process. Complete data collection for the internally smelted materials of metallurgical equipment, computer processing of data, real-time display of the internal temperature field and electromagnetic field of the equipment under the current situation, and signal transmission, through real-time feedback of different data, convenient for people Real-time observation and adjustment of the smelting process strengthened human intervention and control. In the smelting process, timely adjustments are made to improve the process and improve the alloy performance.
4 Conclusion
With the progress of industry, vacuum induction melting technology has developed tremendously in recent decades with its unique advantages, and it plays an important role in the industrial field. At present, although my country’s vacuum induction smelting technology is still lagging behind foreign countries, it still requires the unremitting efforts of relevant practitioners to improve the market competitiveness of my country’s special smelting equipment and try its best to become the world’s first-class smelting equipment. Forefront.
Link to this article: The development and trend of vacuum induction melting technology
Reprint Statement: If there are no special instructions, all articles on this site are original. Please indicate the source for reprinting:https://www.cncmachiningptj.com
PTJ® is a customized manufacturer that provides a full range of copper bars, brass parts and copper parts. Common manufacturing processes include blanking, embossing, coppersmithing, wire edm services, etching, forming and bending, upsetting, hot forging and pressing, perforating and punching, thread rolling and knurling, shearing, multi spindle machining, extrusion and metal forging and stamping. Applications include bus bars, electrical conductors, coaxial cables, waveguides, transistor components, microwave tubes, blank mold tubes, and powder metallurgy extrusion tanks.
Tell us a little about your project’s budget and expected delivery time. We will strategize with you to provide the most cost-effective services to help you reach your target,You are welcome to contact us directly ( sales@pintejin.com ) .
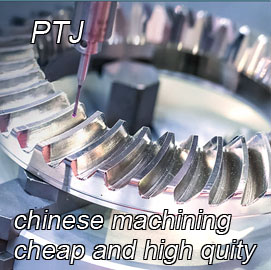
- 5 Axis Machining
- Cnc Milling
- Cnc Turning
- Machining Industries
- Machining Process
- Surface Treatment
- Metal Machining
- Plastic Machining
- Powder Metallurgy Mold
- Die Casting
- Parts Gallery
- Auto Metal Parts
- Machinery Parts
- LED Heatsink
- Building Parts
- Mobile Parts
- Medical Parts
- Electronic Parts
- Tailored Machining
- Bicycle Parts
- Aluminum Machining
- Titanium Machining
- Stainless Steel Machining
- Copper Machining
- Brass Machining
- Super Alloy Machining
- Peek Machining
- UHMW Machining
- Unilate Machining
- PA6 Machining
- PPS Machining
- Teflon Machining
- Inconel Machining
- Tool Steel Machining
- More Material