Briefly describe the current status and development direction of heat treatment technology in the bearing industry
When the bearing material is determined, the heat treatment technology is the key technology to determine the service life of the bearing. In my country's bearing industry, the manufacturing accuracy of bearings has reached the foreign level, but the accuracy of use is far behind foreign countries; the life of the bearings cannot be compared with foreign countries. The market for high-end bearings is basically occupied by foreign bearing factories. The quality of heat treatment of bearing parts directly affects the accuracy and life of the bearing. The heat treatment of bearings in my country started late, but the conventional heat treatment of bearings has developed rapidly in the past ten years, and the heat treatment of bearings with ordinary precision and general life can fully realize mass production.
For a long time, the heat treatment of high carbon chromium bearings adopts martensite quenching + low temperature tempering, and the bainite quenching and tempering process is only used in the fields of railway passenger cars and some rolling mill bearings. Foreign high-carbon chromium bearings are no longer limited to overall quenching, and surface modification is on high-carbon chromium bearings to achieve mass production. Surface modification mainly includes low-temperature ion permeation, carbonitriding, ion nitriding, surface coating, ion implantation, and laser high-energy beam surface heat treatment. Low-temperature seepage can improve the self-lubrication of the bearing and reduce the friction coefficient of the bearing; carbonitriding, ion nitriding, etc. can increase the surface hardness and increase the wear resistance.
The technical progress of the bearing annealing process is mainly reflected in energy saving and temperature uniformity. Waste heat utilization annealing, double-row double-layer energy-saving annealing furnaces have been adopted in batches in the bearing industry. The annealing quality is obviously improved, and the annealing is uniform. At the same time, the energy saving is at least 25% compared with before, and the minimum can reach 110 degrees/t. The annealing power consumption is basically equivalent to that of foreign countries. However, there is still a certain gap between the degree of refinement of the structure after annealing and foreign countries. The refinement and uniformity of carbides have an impact on the service life of the bearing. After bearing forging, the single refinement process and the double refinement process have also been used abroad. There is no industrial batch application in China. There are already companies doing this work. It is estimated that a technological breakthrough will be achieved soon. According to reports, the double refinement process Modification can increase the life of the bearing by more than 1 times. However, the double refinement process is risky, and the key technology of the process has been broken. Industrial practice is advancing, and the double refinement process will also be promoted in high-end bearings in the near future. The double refinement process can not only increase the life of the bearing, but also improve the dimensional stability of the bearing operation. At the same time, it can give full play to material properties and save material resources.
Bainite quenching produces lower bainite structure with better impact toughness. Compared with martensite, bainite has better impact toughness, fracture toughness and dimensional stability, but its hardness is lower than martensite. High-carbon chromium bearing steel bainite quenching has been successfully applied in railway and other industries, and has achieved good benefits.
The carburizing and carbonitriding processes of high-carbon chromium bearing steel are relatively mature abroad, and some domestic manufacturers have stepped into it. Carburizing and carbonitriding high-carbon chromium bearings are mostly used in high-end cars, high-end motorcycles and precision machine tools. These markets are now mostly occupied by foreign countries, and this market has a bright future. The carburizing and carbonitriding processes of high-carbon chromium bearing steel can prolong the service life of the bearing.
Ion implantation technology has been in the bearing surface modification for nearly 20 years. It can improve the friction of the substrate. Wear, corrosion and other chemical properties are a very meaningful new technology for surface modification of materials. There have been industrial practices abroad, and the domestic is still in the laboratory stage.
These surface modification technologies can greatly increase the service life of bearings and are worthy of promotion in domestic bearing heat treatment. At the same time, the surface modification technology of high-carbon chromium bearing steel is of great significance to energy saving and consumption reduction. Exploiting the potential of materials to the limit is the greatest energy saving and consumption reduction; it is the best way to save resources. Heat treatment technology is the best way to maximize the potential of materials.
The precision heat treatment technology of bearings is also developing in a good direction. The precise furnace temperature and controllable cooling medium ensure that the dispersion of the bearing size after quenching is reduced, but the cost is high, which is difficult for ordinary enterprises to achieve. Another type of limited quenching process has been successfully developed in the bearing industry, and the effect of controlling deformation is better. Type-limiting quenching is different from die quenching after carburizing. High-carbon chromium bearing steel is not suitable for die-quenching, and die-quenching is prone to soft spots and unqualified structures; limited-type quenching adopts free quenching in oil above 300℃, 300℃ The following molds are limited to cooling.
In short, the development direction of bearing heat treatment technology is to exert material limits, save material resources, and reduce pollution emissions.
Link to this article:
Reprint Statement: If there are no special instructions, all articles on this site are original. Please indicate the source for reprinting:https://www.cncmachiningptj.com
PTJ® is a customized manufacturer that provides a full range of copper bars, brass parts and copper parts. Common manufacturing processes include blanking, embossing, coppersmithing, wire edm services, etching, forming and bending, upsetting, hot forging and pressing, perforating and punching, thread rolling and knurling, shearing, multi spindle machining, extrusion and metal forging and stamping. Applications include bus bars, electrical conductors, coaxial cables, waveguides, transistor components, microwave tubes, blank mold tubes, and powder metallurgy extrusion tanks.
Tell us a little about your project’s budget and expected delivery time. We will strategize with you to provide the most cost-effective services to help you reach your target,You are welcome to contact us directly ( sales@pintejin.com ) .
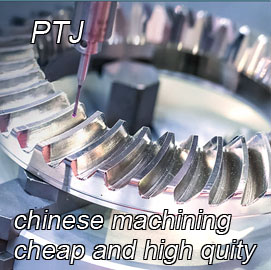
- 5 Axis Machining
- Cnc Milling
- Cnc Turning
- Machining Industries
- Machining Process
- Surface Treatment
- Metal Machining
- Plastic Machining
- Powder Metallurgy Mold
- Die Casting
- Parts Gallery
- Auto Metal Parts
- Machinery Parts
- LED Heatsink
- Building Parts
- Mobile Parts
- Medical Parts
- Electronic Parts
- Tailored Machining
- Bicycle Parts
- Aluminum Machining
- Titanium Machining
- Stainless Steel Machining
- Copper Machining
- Brass Machining
- Super Alloy Machining
- Peek Machining
- UHMW Machining
- Unilate Machining
- PA6 Machining
- PPS Machining
- Teflon Machining
- Inconel Machining
- Tool Steel Machining
- More Material